Sensor solutions for cranes
Goods are warehoused or stored temporarily with industrial crane systems. Automatic positioning of the crane makes the production process much more efficient.
Our sensors ensure process reliability and increase the productivity and availability of your system. In addition, they protect people and materials. The connection between the crane and control is established via the DDLS optical data transmission photoelectric sensor. Various sensor systems for position determination enable precise positioning of the crane and control of the gripper. Safety sensors for collision protection avoid possible collisions.
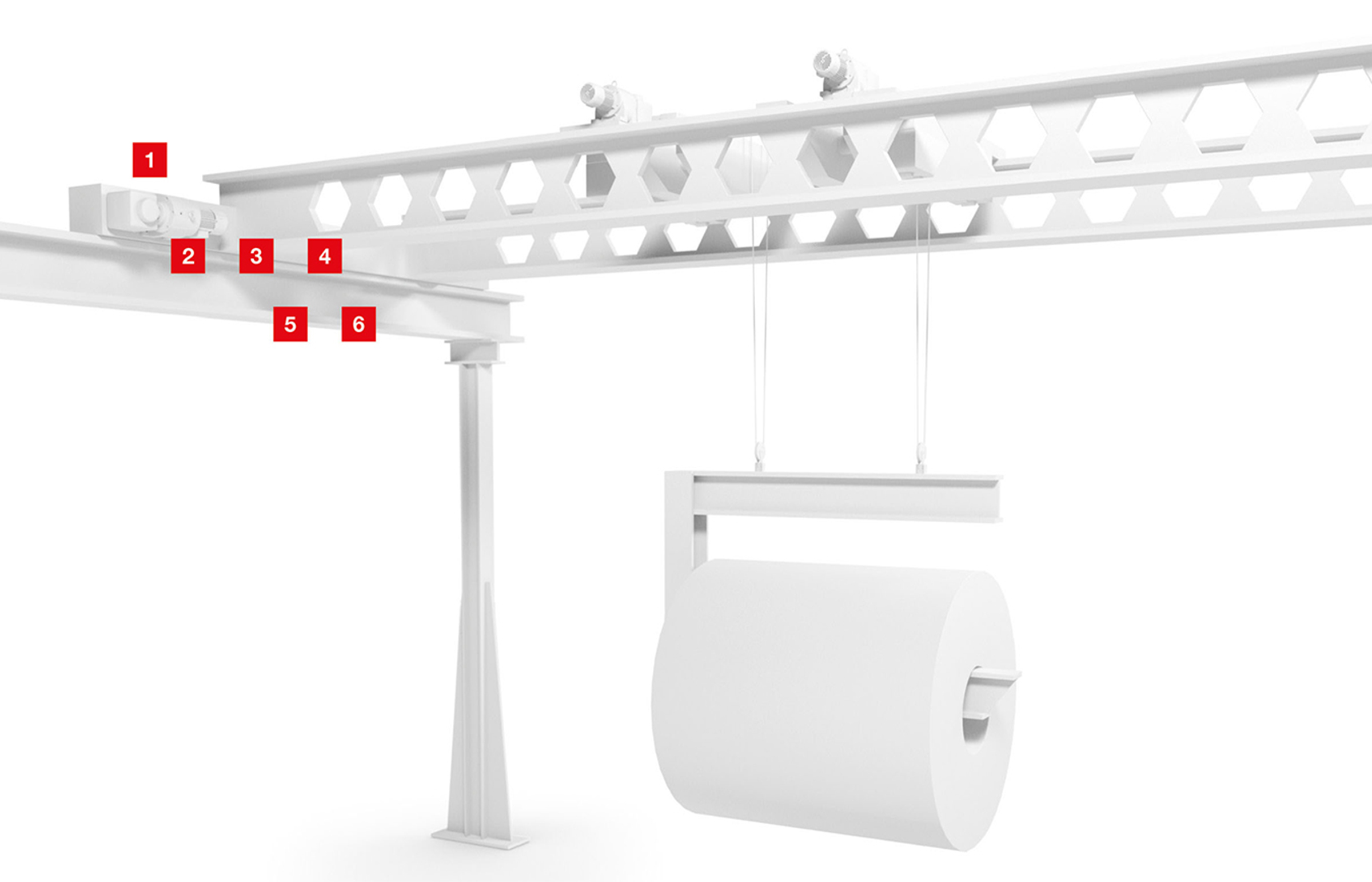