Hydraulic, servo and eccentric presses
Hydraulic, servo and eccentric presses are used for the entire spectrum of metal forming applications. During the forming of sheet metal plates, the operator must be reliably protected from injury in the case of manual operation. Cutting machines or presses can be automated through the use of optional sheet feeders. In this case, the sheet metal plate is unwound from the coil automatically and fed to a cutting machine or press. At the start of the unrolling process, the material must be quickly and unambiguously identified. During the unrolling process, the sheet metal must be inspected for uniform unrolling to ensure precise processing during the subsequent cutting phase.
The safety sensors and controls from Leuze can easily be incorporated in machine processes and process flows, reliably safeguard these processes, and render them tamperproof. Our measuring sensors for loop control and edge control enable smooth process flows when feeding in sheet metal. Our switching sensors reliably detect the end of the coil.
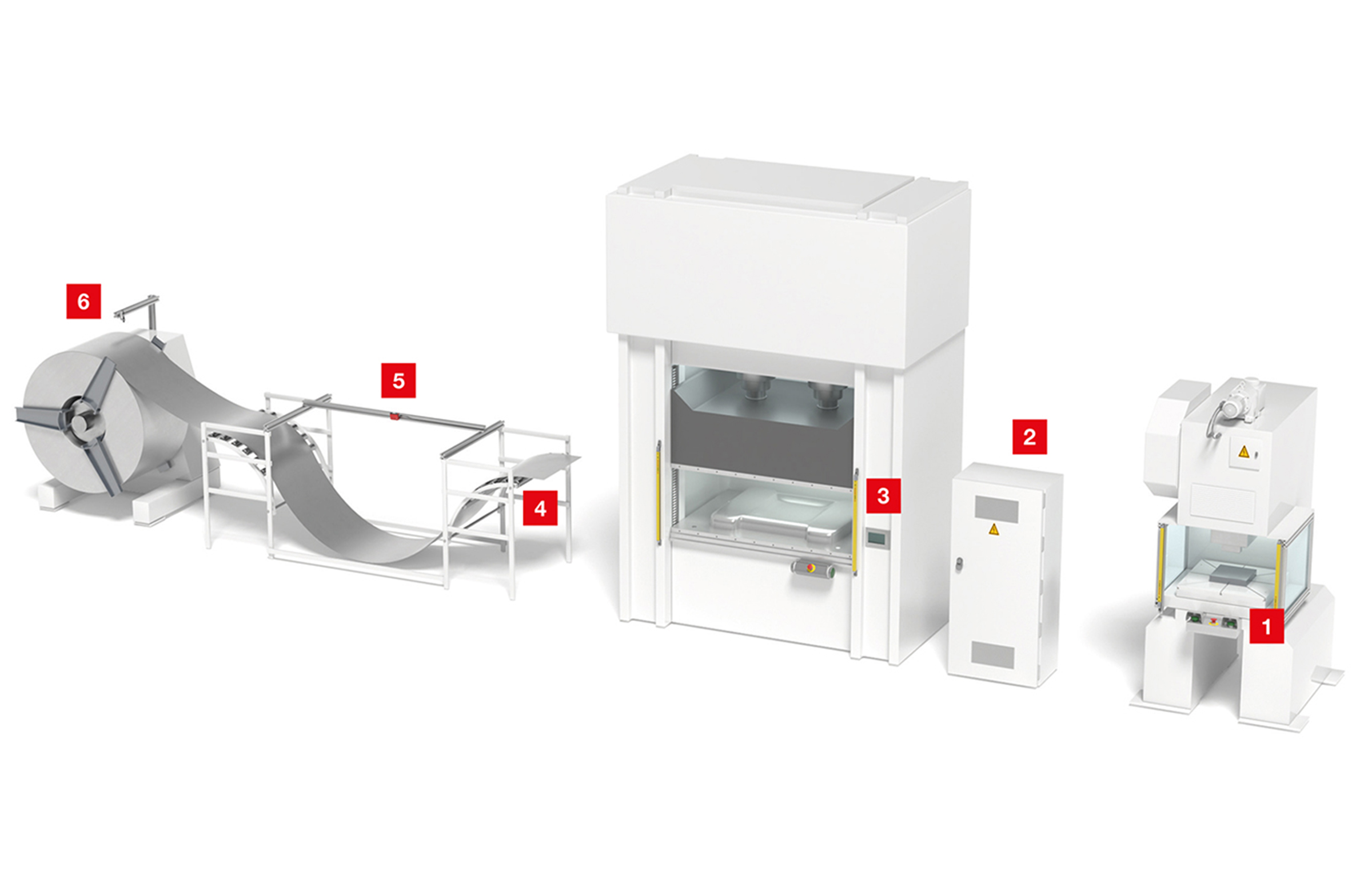