Wire- and pipe-bending machine
Tube and wire bending machines bend and cut round material. Because these machines process materials of various lengths, the area guarding at the bending head of the machines must be adaptable to different dimensions. Also important is reliable presence control
of the material – regardless of its surface characteristics.
Our easy-to-configure safety laser scanners facilitate fast configuration of different-sized protective fields for this purpose. In addition, they are very resistant to particles that may separate from the material during the machining process. Our optical sensors function largely reflection-independent and therefore reliably detect a wide range of surfaces.
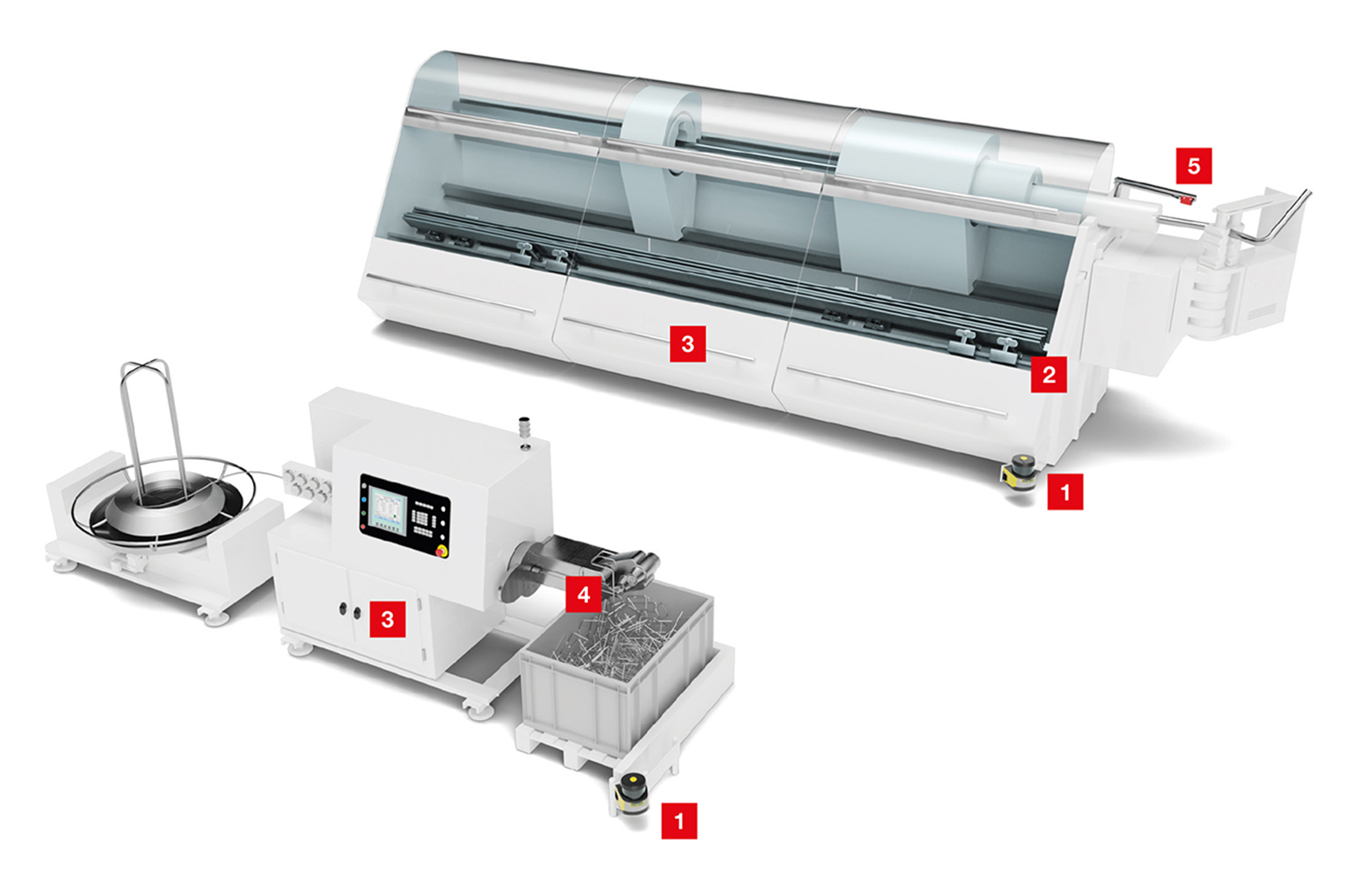