Battery cell production
Battery cells are manufactured in what are known as ‘gigafactories’. From individual machines to networked production systems, the production steps are optimized to ensure process efficiency. The most stringent requirements relate to the stability of the processes and the quality of the manufactured products. As a result, the sensors used must also meet certain requirements, which are determined by the tracking and tracing of battery cells, the production logistics and the safety and reliability of the machines.
Our sensor solutions guarantee smooth processes and ensure machine safety. Typical areas of application are code reading for traceability, object detection for automation, and access guarding on machines and systems.
Application report: Precise processes for the e-drive
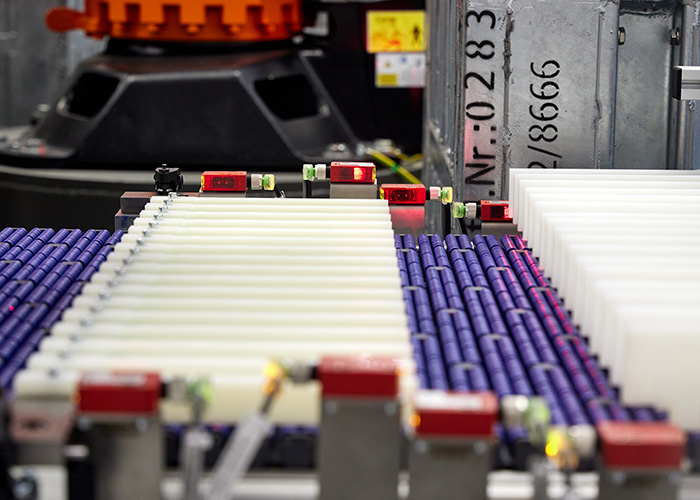
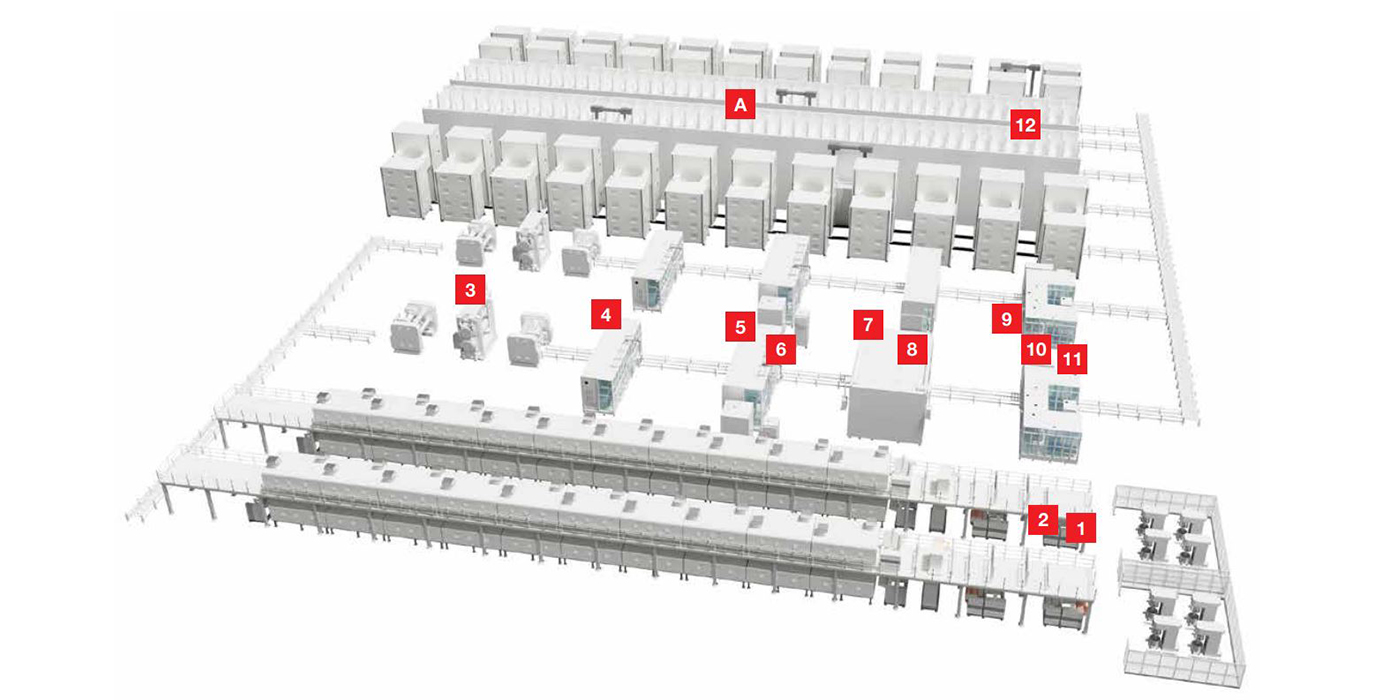
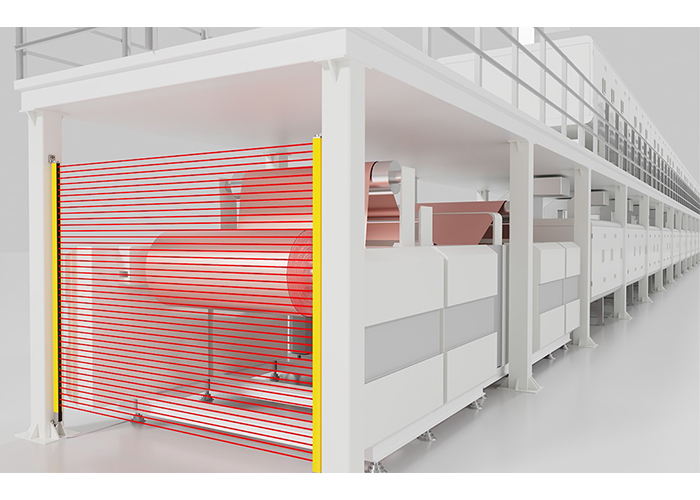
Requirement:
On the coating system, access to the danger zone must be guarded. To ensure that material can enter and exit easily, optoelectronic safety sensors are to be used.
Solution:
The ELC 100 and MLC 500 safety light curtains offer high resolutions for short safety distances, thereby enabling a compact system design. If there is sufficient space, the MLD 500 multiple light beam safety devices are used. These are optionally available with integrated muting function.
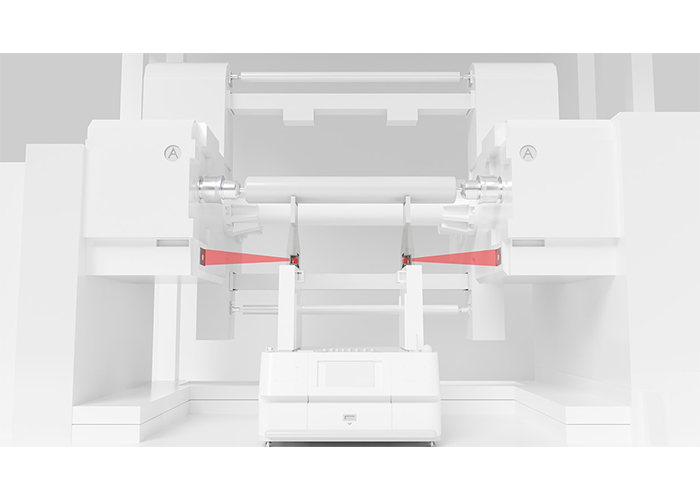
Requirement:
The AGV transports the roll into the transfer station. There, it is pulled in by the coating system. The lifting device of the AGV must be positioned precisely in the y-direction (lifting axis) to ensure reliable transfer.
Solution:
The IPS 200i smart camera determines its position in relation to a marker (hole or reflector) with an accuracy of up to 0.1 mm. The distance can be up to 600 mm. The results are output via an Ethernet TCP/IP, PROFINET or EtherNet/IP interface.
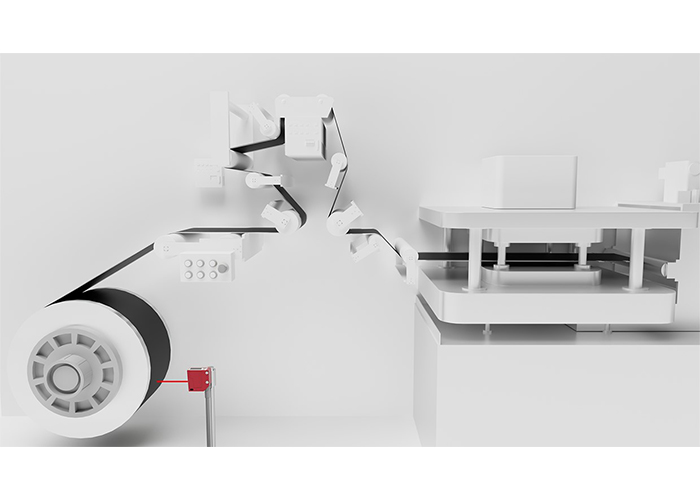
Requirement:
While the film is being wound and unwound, the diameter of the roll must be continuously determined.
Solution:
The ODS 9 optical distance sensors provide exact measurement values even under difficult conditions and set standards in precision and operating comfort. The measurement values can also be read off the integrated display.
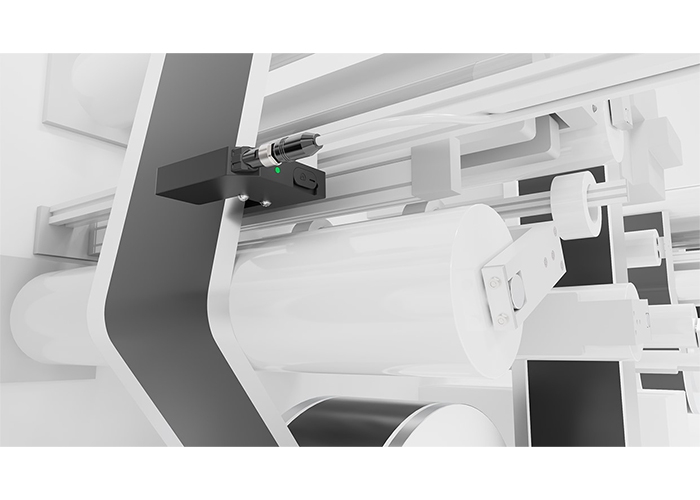
Requirement:
Various process steps in battery cell production require accurate positioning of the electrode film. While the film is being fed into the winding or cutting process, the position of its edge must be determined exactly.
Solution:
The measuring GS 754B CCD fork photoelectric sensor detects the edge of the electrode film with a resolution of up to 0.014 mm and a minimum
reaction time of 2.5 ms. The devices transfer the measurement values to the control via analog means or an RS 232/422 interface.
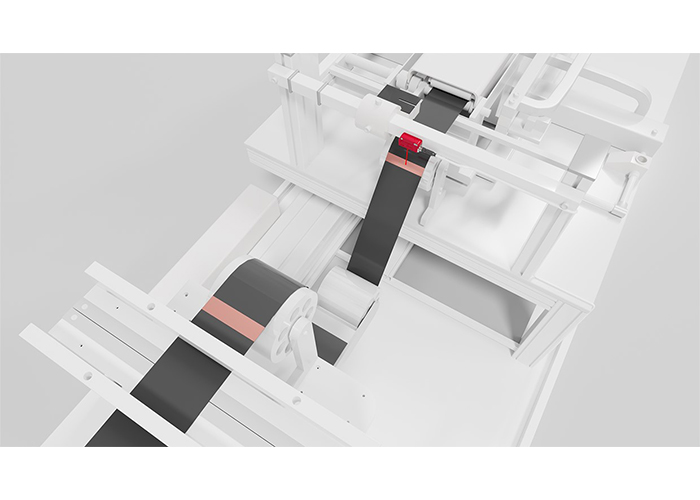
Requirement:
The electrode coating is interrupted periodically. As a result, the copper or aluminum carrier film is visible in these places. The interruptions act as "markings" for the process control – for example, for the cutting process – and are to be detected by sensors.
Solution:
The KRT 3B contrast sensor differentiates reliably between the copper/aluminum film and the electrode coating, and thereby detects the markings. The one-button teach function can also be activated from the control. The large operating range of 60 mm ± 20 mm enables the sensors to be flexibly integrated into the machine.
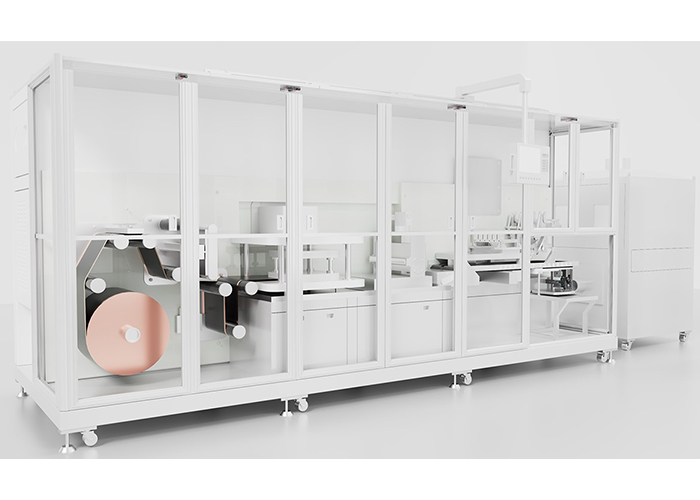
Requirement:
Areas with hazardous movements can be entered via safety doors to allow maintenance. If the movement does not stop immediately after the door is opened, the door is to be guarded by a safety switch with locking device.
Solution:
The robust L series safety switches with locking device keep safety doors securely locked
until access is released by an electric signal. The series includes standard designs and a device with an RFID-coded actuator for optimal protection against tampering.
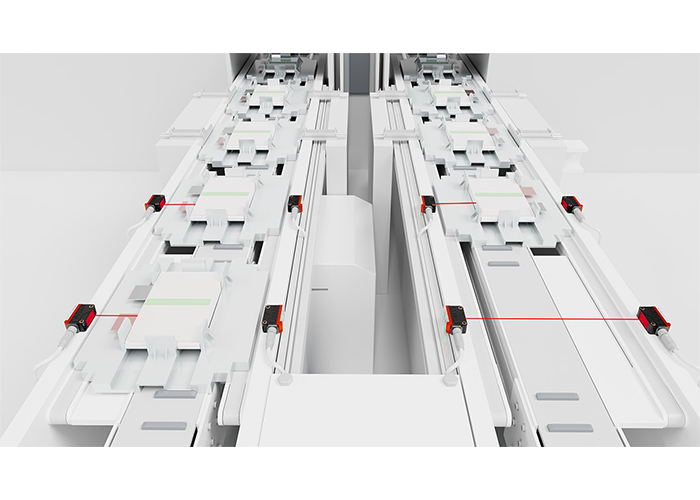
Requirement:
The presence and position of the battery cells on the transport carrier must be checked before the next processing step. To ensure that the system setup is compact, the sensors must not take up much space.
Solution:
The optical sensors of the 5B series require little installation space. Thanks to the optimized beam geometry, the devices are able to detect even flat battery cells reliably, thus ensuring the high availability of the machine.
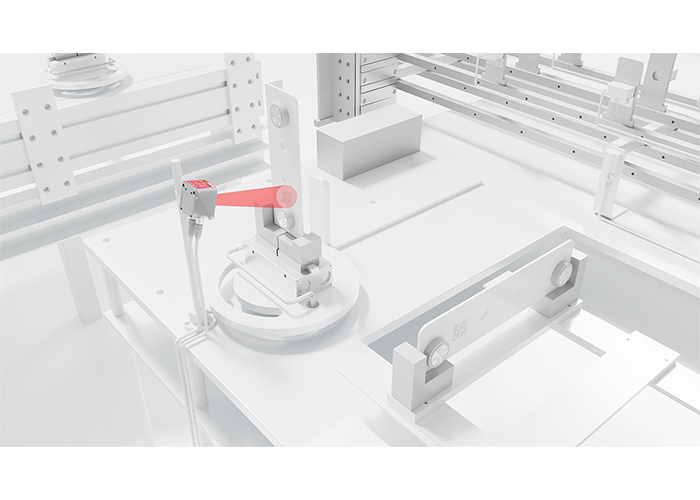
Requirement:
The ‘track & trace’ concept also includes the traceability of each individual battery cell that is in the work system. To make this possible, the laser-etched 2D code (DPM code) on the cover must be read.
Solution:
The DCR 200i 2D-code readers reliably read DPM codes on metallic surfaces – even if the objects are moving quickly. Various optics models are available to adapt the reading range to the application. The devices can be integrated flexibly via PROFINET IO/RT, Ethernet TCP/IP, UDP, RS 232 and RS 422 interfaces.
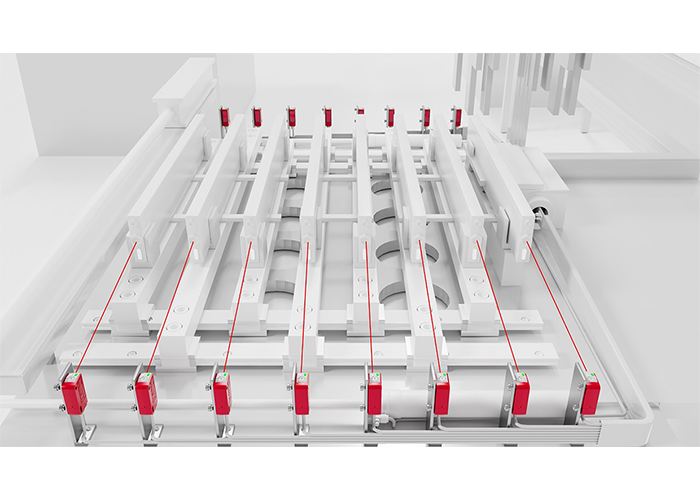
Requirement:
Before the liquid is injected at the filling station, it is necessary to check that the battery cells are in the correct positions. This is also required to ensure
that the battery cells are gripped reliably.
Solution:
The optical sensors of the 3C series use their laser light source to detect the battery cells reliably, even in confined spaces. In addition, thanks to their active ambient light suppression, the sensors are unaffected by direct light from LED hall lighting. This prevents
erroneous switching.
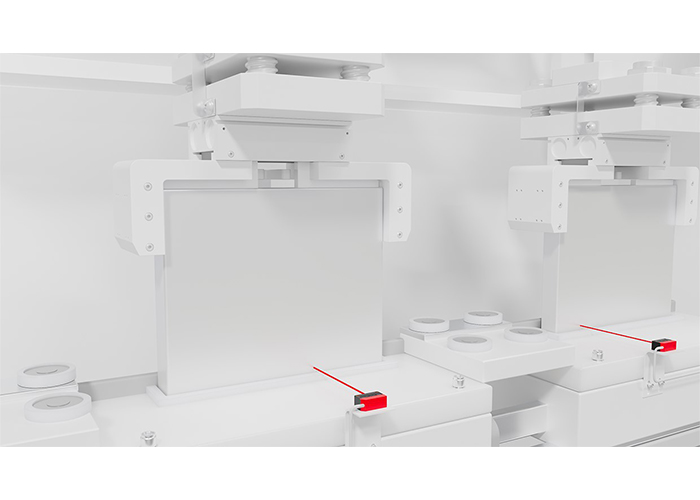
Requirement:
Before they are filled with liquid at the filling station, the presence of the battery cells must be checked. The sensor must reliably detect the reflective aluminum material of the cell cover.
Solution:
The PRK 5B retro-reflective photoelectric sensors detect even reflective objects reliably. The devices have safe switching behavior and can be aligned easily thanks to the homogeneous light spot.
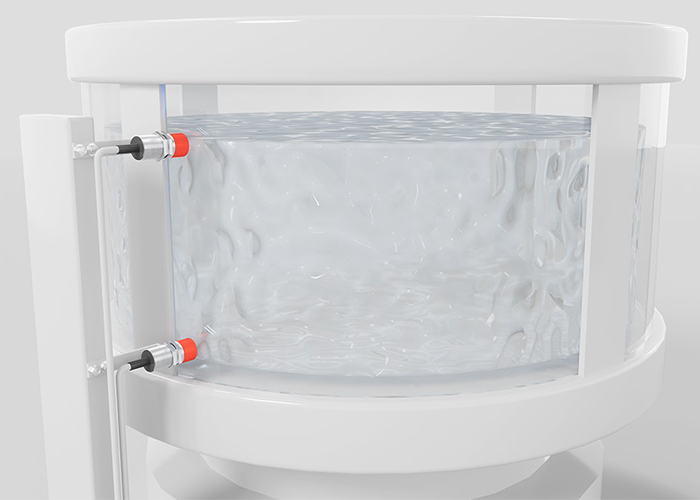
Requirement:
The fill level of the electrolyte in the container must be monitored from outside
the container in a contactless manner.
Solution:
The LCS-1 capacitive sensors detect the fill level in the container,
even with different container wall materials. To ensure easy handling and integration, models with a teach button and IO link are available.
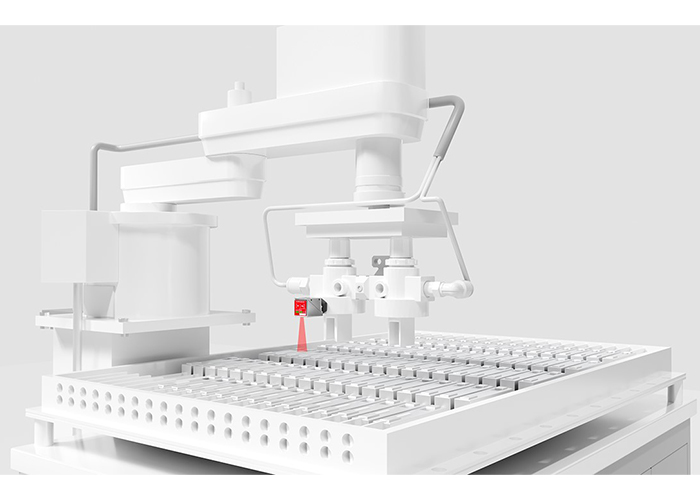
Requirement:
Before the battery cell is placed into storage, it must be coated. The relevant information is coded and printed on the battery cell. Before the cell enters the coating machine, this information (data) must be detected to ensure traceability along the entire process chain.
Solution:
Thanks to their high scanning rate, the DCR 200i 2D-code readers enable the reading of codes on quickly moving objects. To enable adaptation of the reading range, various optics models are available. Diverse interfaces can be used to integrate the devices easily into fieldbuses and commission them quickly with simple configuration tools.