Sensor solutions for meat, sausage and cheese packaging
When it comes to the processing and packaging of sausage, cheese or meat, not only the systems but also the installed sensors need to withstand regular intensive cleaning cycles at high pressures and temperatures using aggressive cleaning agents.
Our sensors, which have a special hygienic design, ensure a consistently high product quality in production areas where there is direct contact with the food, for example when detecting the leading edges of cut goods. The sensors of the 53C and 55C series have a high-quality V4A stainless steel housing (AISI 316L). The extremely smooth surfaces can be cleaned very thoroughly and bacterial carry-overs to production systems are avoided. All of the plastic parts used in the sensors have FDA approval. With the highest degree of protection IP 69K as well as ECOLAB and CleanProof+ certification, the robust miniature sensors enable long operating periods in wet zones (wash-down design) and hygienic areas (hygienic design). This ensures reliable and stable processes.
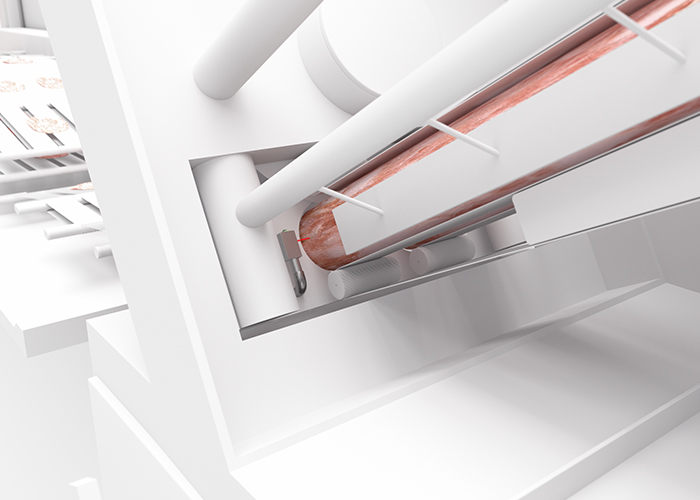
Requirement:
In the food industry, sausage or cheese is delivered in large bars and cut into thin slices in a cutting machine. The product must be reliably detected in the infeed of the machine so that the gripper can uniformly push the material towards the knife and so that all cut slices have the required thickness.
Solution:
The HT53C.S diffuse sensor in hygienic design monitors the product infeed at the cutting machine. A particularly small light spot ensures very good performance, especially with objects with colored structure. Background suppression of the sensor enables reliable color-independent product detection.
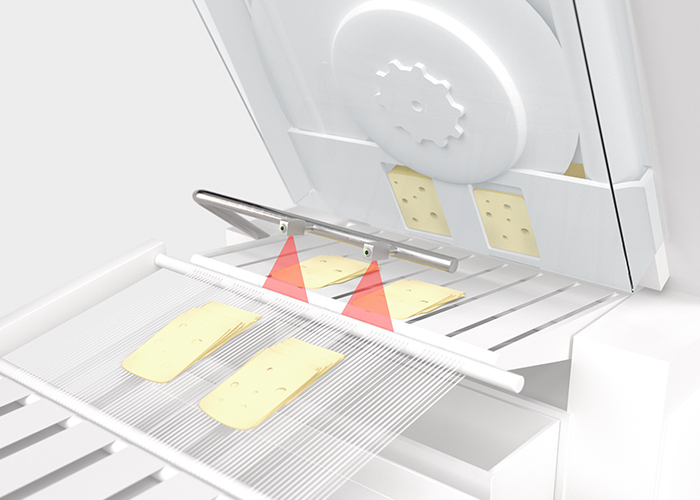
Requirement:
In an industrial cutting machine, cut goods are cut into small stacks and pre-portioned for the subsequent packaging in trays. The challenge for the sensor system is that the front edge of the cut goods must be reliably detected at the same switching point. The sensors are mounted directly above the conveyor belt.
Solution:
The HT53CL1.X diffuse sensor with background suppression is optimized for the detection of the front edge of products thanks to a long laser light spot. The sensor in hygienic design ensures that cut goods are positioned precisely when loaded into the deep-drawing packaging.
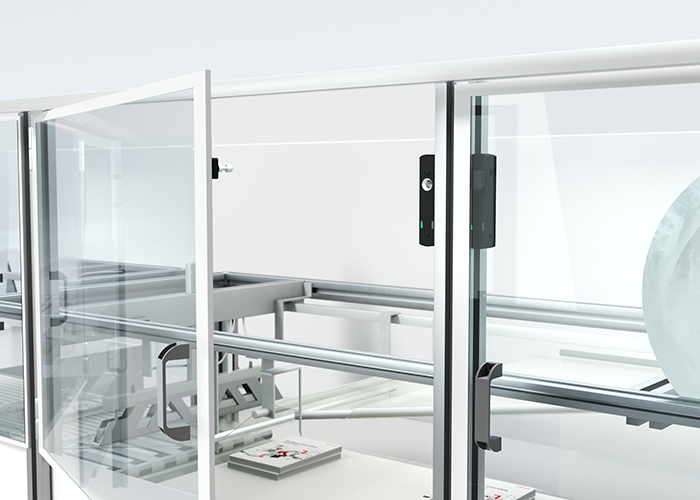
Requirement:
Moving protective devices such as doors and flaps protect the operator from hazards. In the so-called white areas, safety switches with locking device in a hygienic design are required.
Solution:
The L100, L250 and L300 safety switches with locking device keep safety doors locked until access is released by an electric signal. The series includes standard designs, devices with integrated operational controls as well as with RFID‑coded actuators. Technopolymer housings with smooth surfaces are suitable for hygiene-sensitive areas.
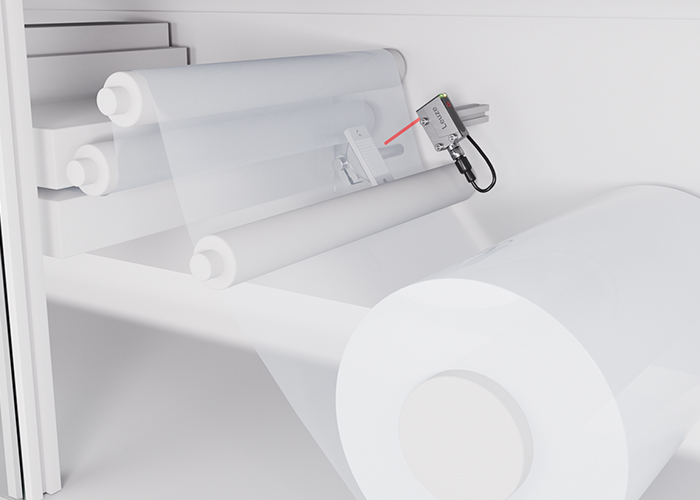
Requirement:
The film infeed must be ensured throughout the complete packaging process. Sensors are used at suitable points to detect the presence of the transparent film as well as film tears or film ends.
Solution:
The PRK 18B retro-reflective photoelectric sensors are suitable for detecting highly transparent films, ideally with an MTKS reflector. Models for the detection of transparent objects include the PRK25C.A and PRK3C.A retro-reflective photoelectric sensors.
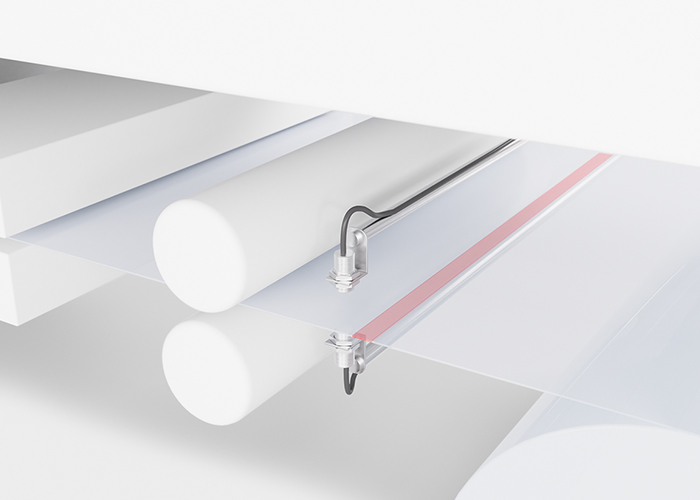
Requirement:
Hard-wearing thermoforming sheets are bonded when changing film rolls. For a fault-free process, this splice must be reliably detected and discharged.
Solution:
Ultrasonic sensors enable material-independent splice detection. The VSU 12 ultrasonic system developed for this application consists of a pair of ultrasonic sensors and an analysis amplifier. The IGSU14E SD ultrasonic fork sensor is an alternative.
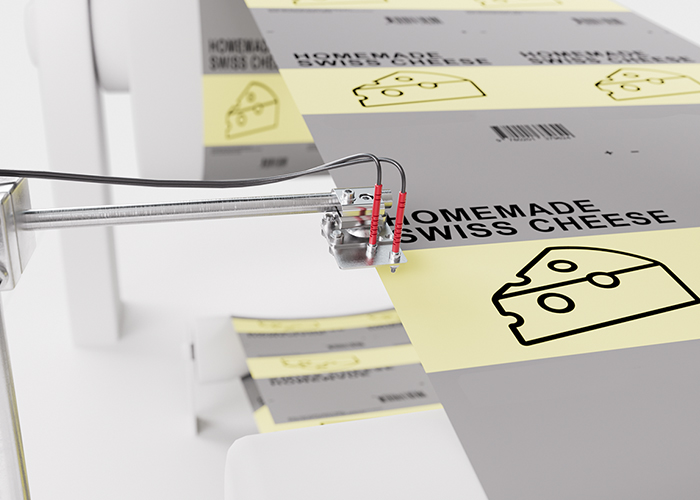
Requirement:
Film webs must be precisely aligned laterally before further processing. Sensors ensure a precise web guide, both for the bottom and top film. Suitable sensor solutions are required in each case for transparent or printed film webs.
Solution:
Different solutions are available for the web guide - with plastic fiber optic cables from the KF series or with switching retro-reflective photoelectric sensors, e.g. PRK 18B, two-point control can be realized. With a GS 754 measuring fork sensor, a high-precision analog web guide is possible.
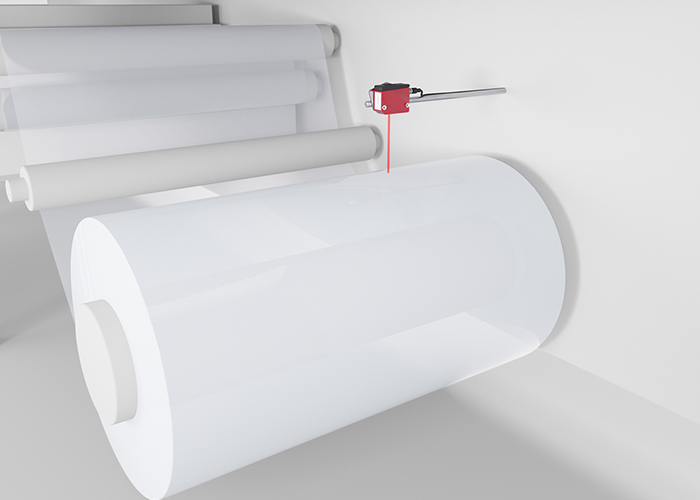
Requirement:
Thermoforming film for trays is provided in large rolls. To ensure uniform unrolling of the film, the axis is motor-driven. A sensor must permanently detect the diameter of the roll.
Solution:
The measuring sensors of the ODS9 or ODS96 series send an analog signal in relation to the roll diameter to the control. An alternative for diameter measurement are the DMU318 and DMU418 ultrasonic sensors. Distance sensors are available with different measurement ranges.
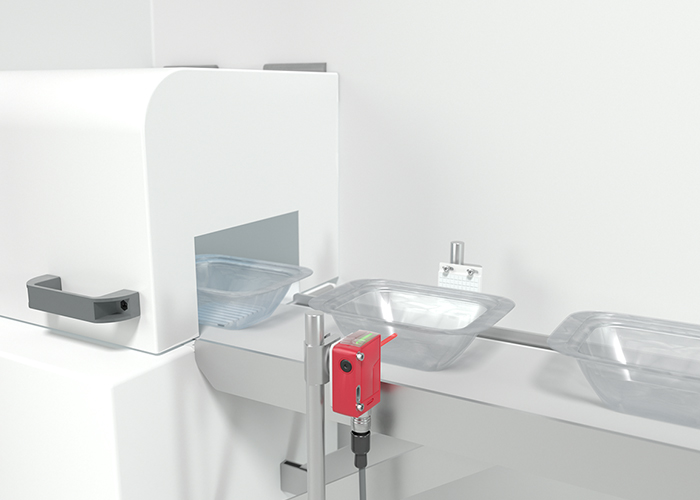
Requirement:
Empty plastic trays that are often transparent must be reliably detected in the feed of a tray sealer. Ideally, retro-reflective photoelectric sensors are used for the detection of transparent objects.
Solution:
The compact retro-reflective photoelectric sensors of the 3C or 25C series in plastic housings and the 55C series in stainless steel housings are designed as autocollimation models for this application. Suitable reflectors with microtriples of type MTKS are available in various dimensions and materials.
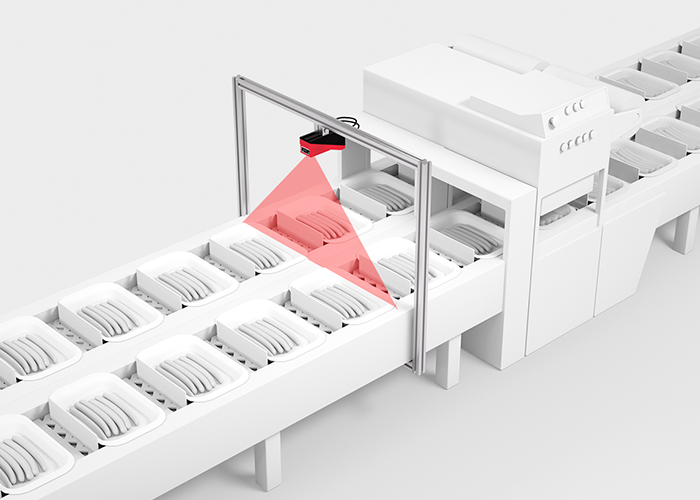
Requirement:
Before the trays are sealed in the sealing machine, it must be checked to determine whether all trays are filled. Unfilled and overfilled containers must be discharged. The control is carried out by sensors mounted above the conveyor.
Solution:
The LRS 36 light section sensor uses a projected laser line to detect the filling status of the individual trays. The sensor provides several switching outputs and process data for the control.

Requirement:
In order to be able to control transport sections between process steps, objects on the conveyor line must be detected. The challenge is that the objects have different shapes and colors or are transparent. Due to their proximity to the food, sensors must meet high hygiene requirements.
Solution:
Retro-reflective photoelectric sensors of the 55C series in stainless steel housings with suitable MTKS.5 stainless steel reflectors as well as diffuse sensors with different light-spot geometries are optimized for detection tasks in the food industry. The housing design of the 53C series in hygienic design is suitable for direct food contact.
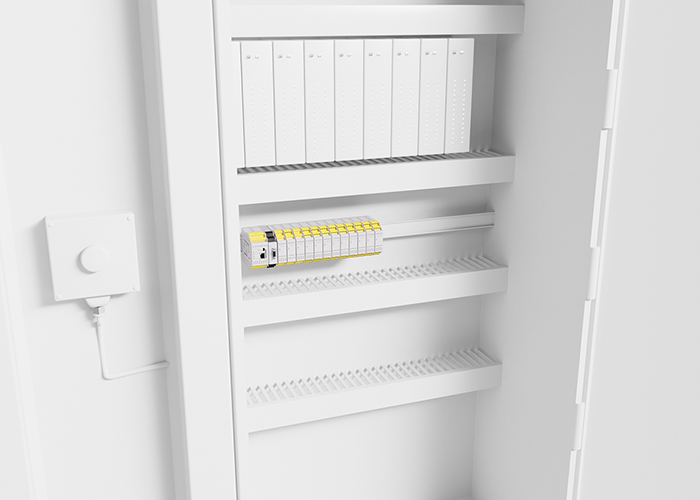
Requirement:
Reliable evaluation units are required for the integration of safety sensors and command devices into the safety circuit of the machine control. Either as safety relays with a fixed function for individual safety sensors or as programmable safety controls with flexible functions for several safety sensors.
Solution:
The MSI SR safety relays offer simple and cost-effective solutions for the integration of individual safety sensors. For more complex safety functions and multiple sensors, the configurable MSI 400 safety controls are used. They are modularly expandable and can be easily adapted to the application.
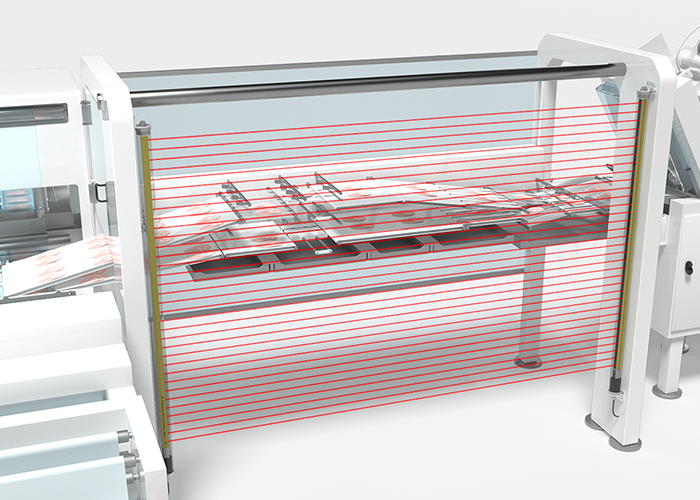
Requirement:
Large machine openings through which access to danger zones is possible must be secured during operation. Safety sensors with a high IP degree of protection are required for use in hygiene-sensitive environments.
Solution:
The MLC 500-IP safety light curtains safeguard points of operation in hygiene-sensitive areas of food processing and have the highest degree of protection IP 69K. For this purpose, the light curtains are mounted in a transparent and encapsulated tube. Different resolutions and protective field lengths offer optimal adaptation to the application.
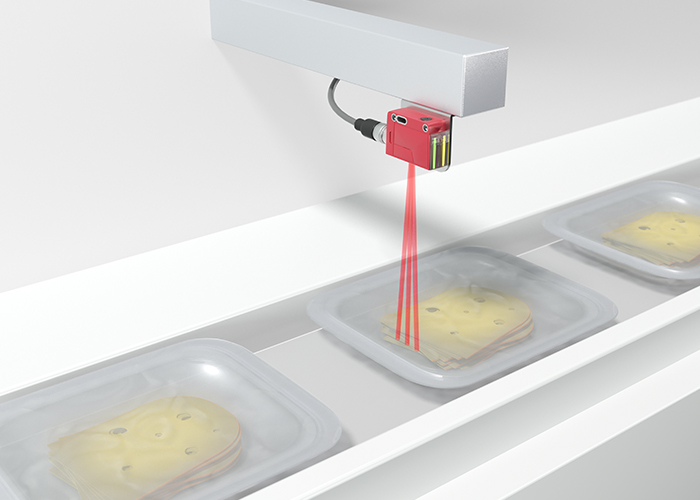
Requirement:
After products have been packaged in thermoformed trays, for example, the front edge must be reliably detected from above, even in single or multiple track systems. Different heights of the trays can pose a challenge for the sensor system used.
Solution:
The DRT 25C dynamic reference diffuse sensor sets the conveyor belt as a reference and thus allows for reliable detection of the front leading edges of the object on the belt - independent of the colors or heights of the products. Light spots arranged horizontal to the transport direction also detect products with gaps.
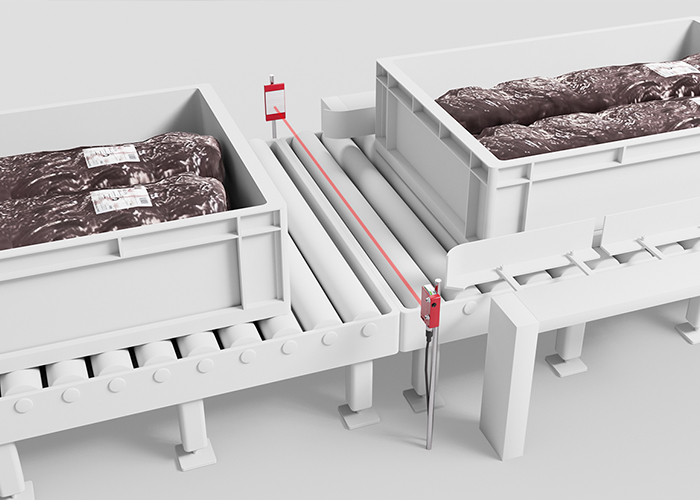
Requirement:
Standardized containers are used in the process steps between meat cutting and further processing. Sensors for detecting these containers must be designed for high hygienic requirements.
Solution:
Retro-reflective photoelectric sensors of the PRK 46C or PRK 25C series can be used for container detection on the transport system. HT 46C and HT 25C diffuse sensors are often also used here. The 46C and 25C series have degree of protection IP 69K and are ECOLAB-certified.
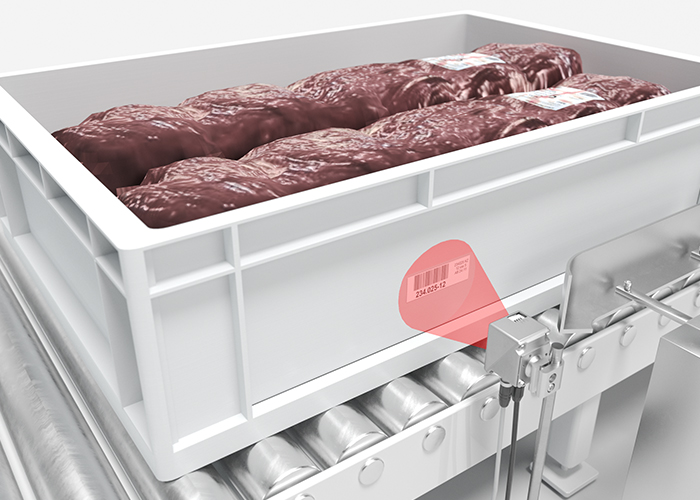
Requirement:
To control the path of the standard containers, the codes attached to the containers must be reliably read. Due to the high requirements of the cleaning agents used and ambient temperatures, sensors must be used that can withstand this environment.
Solution:
The bar codes or Data Matrix codes present on the containers can be read and identified very reliably with the compact, image-based code reader DCR 200i in a stainless steel housing (hygienic design) with a degree of protection IP 69K. The most important Ethernet-based interfaces are available for selection.