Overview of services
White paper: Risk assessment – what are the methods?
The European Machinery Directive is being superseded by the German Machinery Ordinance. This requires every machine to undergo a risk analysis before being placed on the market or after being modified. A risk assessment is a significant part of this process. What is the legal basis? What methods are there for conducting a risk assessment? The new white paper has the answers.
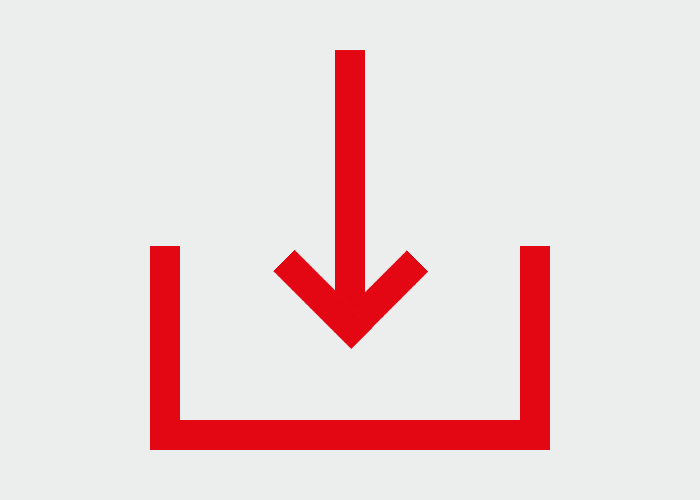
“CE marking of machines” status check
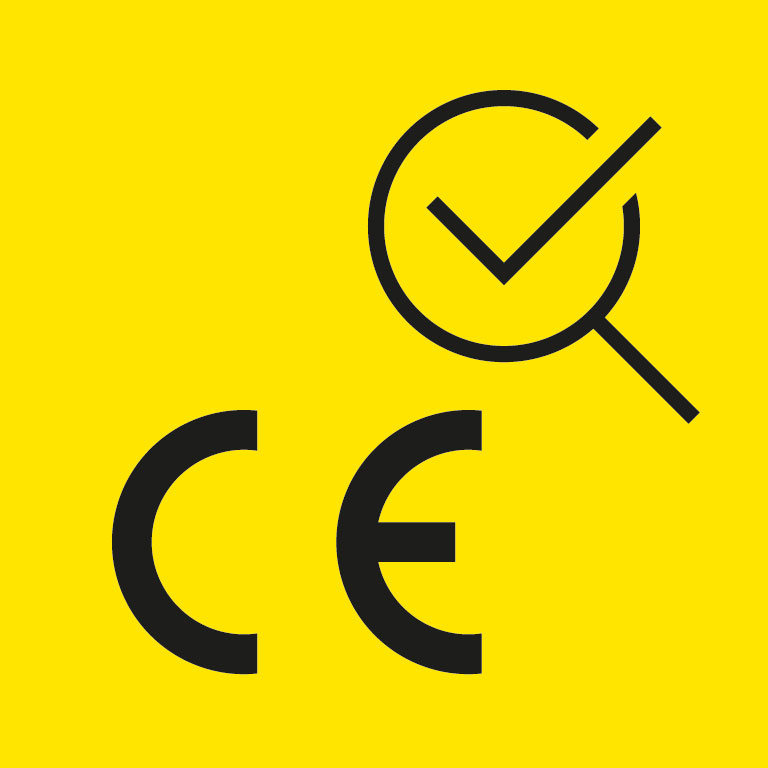
Your requirement
As the manufacturer, you must
- prepare the documentation in accordance with the requirements of the Machinery Directive during the design and after the manufacture of machines
- ensure that the documentation is complete and that the relevant standards are complied with
- confirm the correct procedure by way of the EU declaration of conformity and the CE marking
As the operating company,
- the original operating instructions support you in preparing the risk assessment
Our solution
We check compliance with the requirements of the Machinery Directive for
- the EU Declaration of Conformity/Declaration of Incorporation and CE marking
- the original operating instructions and the safety requirements
- the design of the safe part of the control system based on the relevant EU standards
- the machine documentation
Advantages for you
- Independent check of the completeness and content of the documentation according to the requirements of the machinery directive
- Recommendations for correction in the event of possible deviations
Risk assessment
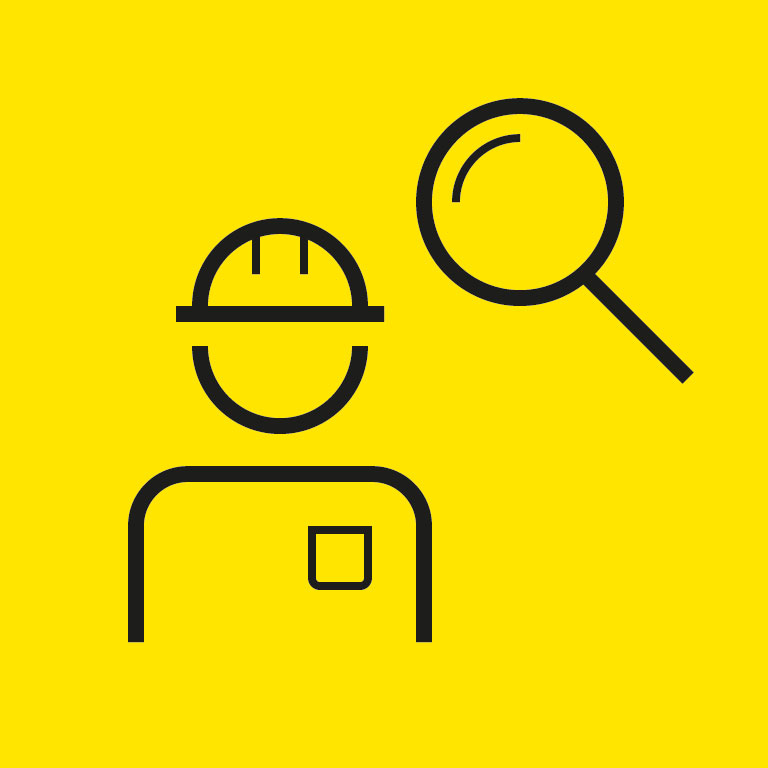
Your requirement
- A risk assessment must be carried out as part of the conformity assessment process for a machine. The legal requirements and the standard machine-specific requirements must be taken into account.
- In the event of a modification or extension to an existing machine, the risk assessment must be adapted
- The assessment and evaluation of hazards and risks is to be performed by an independent person
Our solution
- Analysis of the existing risks
- Assessment of the existing risks and calculation of the risk values using the Leuze risk assessment process HaRMONY (Hazard Rating for Machinery and prOcess iNdustrY)
- Description of the risk-minimizing measures
- Verification of the effectiveness through re-assessment of the risks after applying the risk-reducing measures
Advantages for you
- Benefit from our many years of experience in the preparation of risk assessments
- Tailored solutions: From targeted support to complete implementation
- Detailed description of the risk factors as well as determination of the risk values
- We use the Leuze risk assessment process HaRMONY (Hazard Rating for Machinery and prOcess iNdustrY): This provides you with especially precise risk values
- Assessment of hazards and risks by independent persons
Conformity assessment in accordance with the Machinery Directive
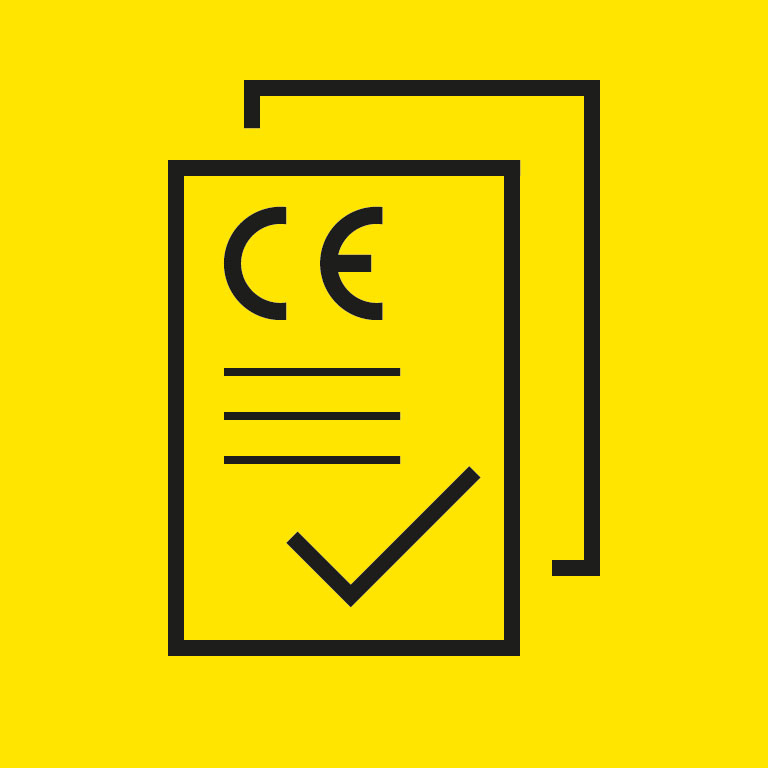
Your requirement
- If a machine is placed on the European market, a conformity assessment must first be performed. The Machinery Directive 2006/42/EC defines the procedure for this.
- The manufacturer confirms compliance with the requirements of the directive by means of the EU Declaration of Conformity and the CE marking
Our solution
- Tailored support over the entire process for compliance with legal requirements
- Checking the project status to date for content and completeness, e.g. risk assessment, design and documentation
- Proposal for the content of the EU Declaration of Conformity
Advantages for you
- Independent confirmation that the requirements of the Machinery Directive have been met
- Recommendations for correction in the event of possible deviations
Safety concept and design
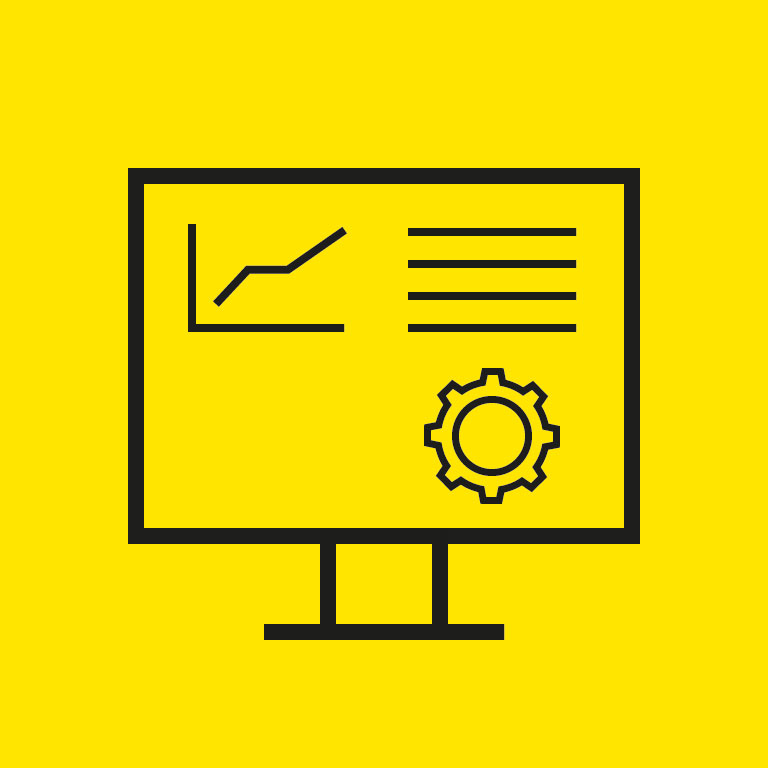
Your requirement
- Creation of a safety concept on the basis of the risk assessment
- The required safety functions must be designed so that an optimum balance between safety, ergonomics and cost effectiveness is achieved while observing the relevant standards and regulations.
- Proper documentation of the safety functions is also important. The validation plan defines the function and error tests that prove the effectiveness of the safety functions during commissioning.
Our solution
- Design of practical concept proposals
- Selection of suitable components and creation of the connection plan
- Programming the safety-related part of the control system
- Clear and comprehensible documentation of the safety functions
- Creation of the validation plan on the basis of the safety concept
Advantages for you
- Implementation of the control technology measures in safety functions in accordance with the standards’ requirements
- With our extensive industry knowledge and experience in safety technology, you can create optimum safety concepts
- Checking the security concept for completeness
- Review and verification of the safety concept by an independent external inspector (four-eyes principle)
Verification and validation of safety functions
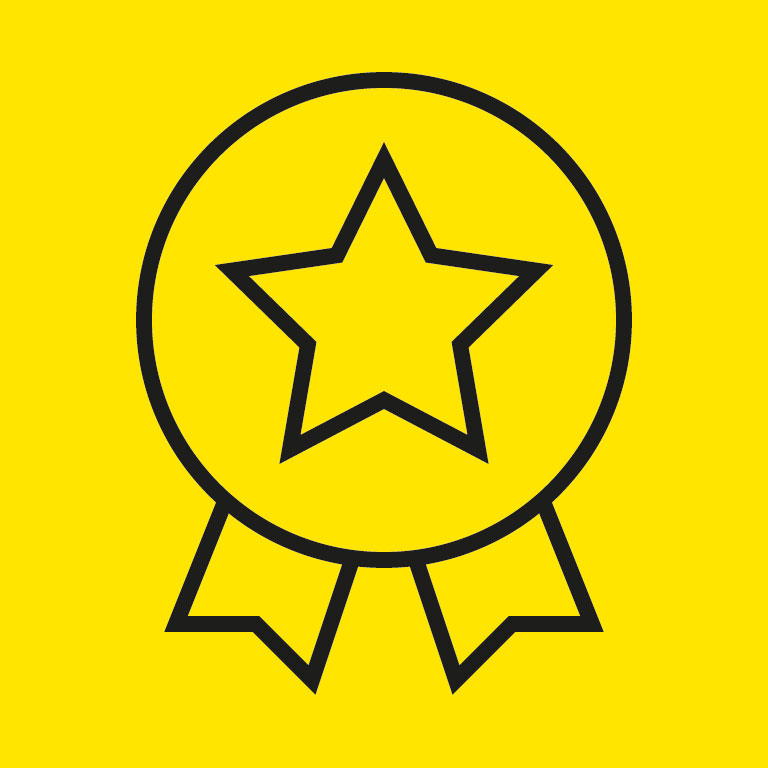
Your requirement
- The error-free implementation of the safety functions on the basis of the safety concept must be checked
- The performance of the safety functions is to be verified through function tests and error simulations
Our solution
- Tailored support during the entire process
- Checking the existing project status for content and completeness
- Planning and execution of individual process steps, e.g., definition of the function tests and creation of the corresponding documentation
Advantages for you
- Correct procedure for the implementation of safety functions is guaranteed
- Efficient implementation of the necessary tasks with support and tips from experienced experts
Start-up support
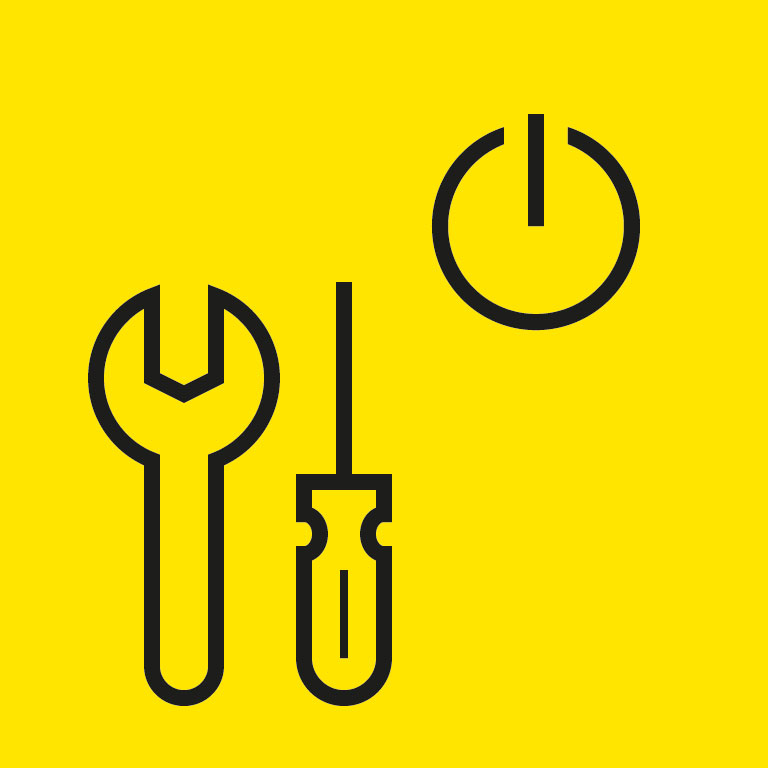
Your requirement
- Fast and safe commissioning
- Optimization of the performance of the devices in the application, e.g., by alignment based on the procedure described in the operating instructions
- If the device is replaced,
- the configuration must be transferred to the new device
- downtime must be minimized
Our solution
- Optimum alignment of optical sensors
- Support during the configuration and parameterization of our devices, e.g., during the selection of the operating mode and the parameterization of protective fields with safety laser scanners
- Configuration adaptation when changing to a newer generation of devices
- Help during troubleshooting
Advantages for you
- Fast and safe commissioning by our service technicians
- Calculable costs
- Minimized downtime in the event of a device replacement
Inspection of protective devices
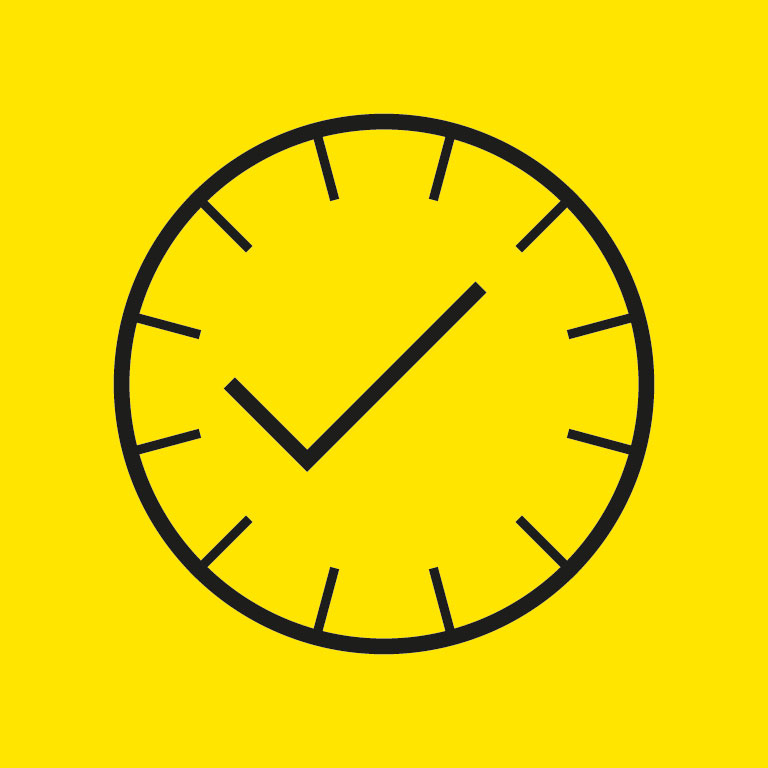
Your requirement
- Safety at work is the employer's responsibility. Through the regular inspection of the protective devices, adherence to safety and quality standards is ensured.
- Inspections minimize undesired machine downtimes as part of the preventive maintenance plan.
- In Germany, the Industrial Safety Ordinance requires machines to be tested prior to initial commissioning and thereafter at regular intervals. A check is also necessary after longer downtimes and after changes to the machine.
- The testing and inspection of protective devices may only be carried out by qualified persons.
Our solution
- Inspection of electro-sensitive protective equipment (ESPE), safety switches and emergency stop equipment
- Testing the condition, functional installation and correct function of the protective device as well as its safe integration in the machine control
- Testing the safety distance to the safeguarding point of operation as stipulated by standards through measurement of the stopping time
- Detailed test log, attachment of the inspection sticker
Advantages for you
- Minimization of accident risks and machine downtime
- Legal security for the operating company through verification of safety and quality standards
- Practical solutions for the rapid elimination of safety deficiencies
- Independent, external assessment by a qualified person in accordance with TRBS 1203
- Clear documentation with our own test database based on more than 20 years of experience
- Inspection of protective devices from all manufacturers
The process on site
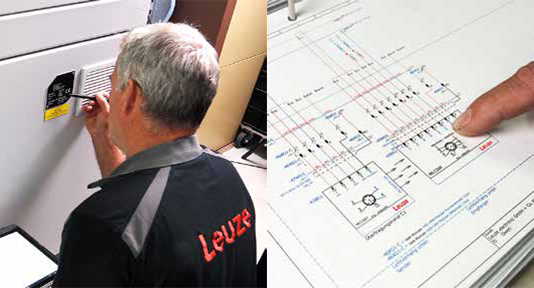
The inspection begins with the recording of data from the machine and protective devices. We then test the safety-related integration of the protective devices and their switching outputs. This work is conducted during operation without affecting the productivity of the machine.
In the next step, we test the function of the protective devices. In the case of optical safety devices, for example, this includes:
- Testing the detection capability and possible reflection bypass. Testing is performed with a test piece suited to the resolution of the device.
- Testing of special functions such as reduced resolution, cycle control, muting and blanking
- Testing function of the start/restart interlock
- Visual check of the device state
We check that the protective device is mounted correctly, and assess the safety distance:
- Can the protective device be bypassed, e.g. by reaching over, under or around or by stepping over?
- Is it possible to crawl under the protective device?
- Measurement of the stopping time for determining the safety distance (if necessary and possible, see next page).
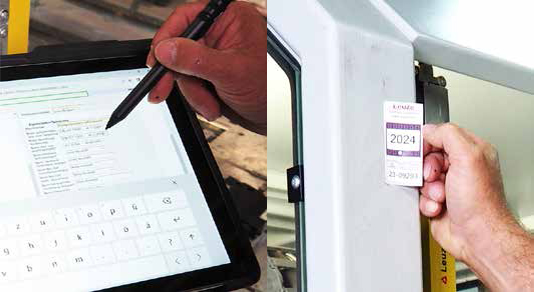
We record all results in the inspection database and use this information to create a clear test log. On completion of the inspection, we attach the inspection stickers to the machine, which also include the inspection number of the test log for easy tracking.
Stopping time measurement
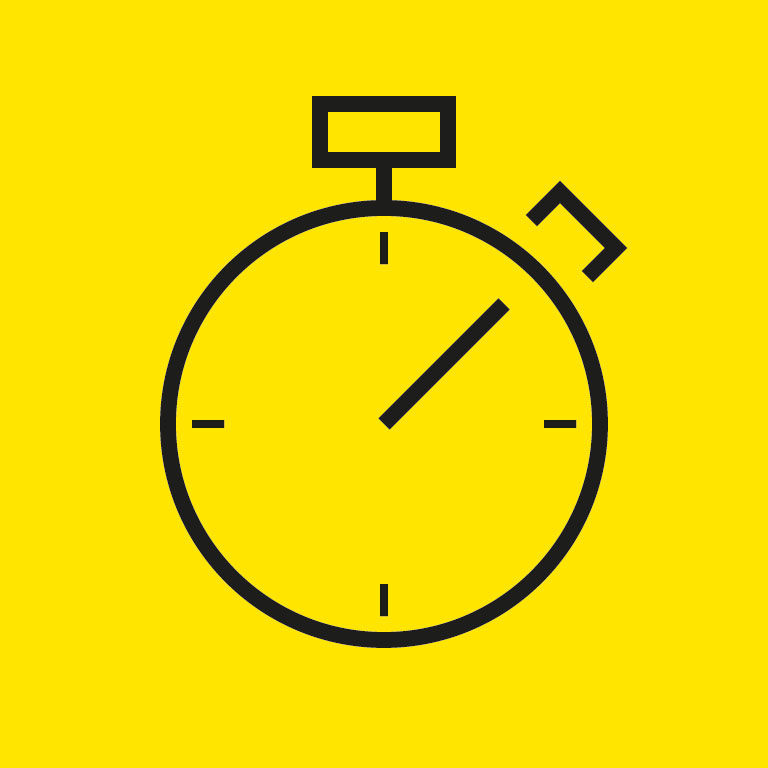
Your requirement
- To calculate the safety distance, the stopping time of the machine must be determined through measurements. This allows the protective device to be positioned correctly, because only a sufficient safety distance between the protective device and the safeguarding point of operation ensures that people are not endangered.
- Wear, e.g., on engine brakes, can extend the stopping time of a machine so much that reliable protection of the operator is no longer ensured by the protective device. Measuring the stopping time allows changes to be identified and necessary measures to be determined. The stopping time measurement is, thus, part of our regular safety inspections.
Our solution
- Physical test of the stopping time for all installed protective devices with calibrated measurement devices
- Assessment of the safety distance based on the measurement results and the requirements in accordance with ISO 13855
- Verifiable and documented test results, optionally with graphic analysis of the braking movement
Your advantage
- Stopping time measurements performed by experts provide a reliable basis for the calculation of the safety distance and the correct positioning of the protective device
- Regular inspections enable early detection of wear, thereby ensuring long-term machine safety
The process on site
Determination of the stopping time with special measurement device
The stopping time is determined with a special measurement device. This measures the time from the interruption of a protective device until the dangerous movement comes to a standstill:
- An actuator (brand name Auto-Hand) is mounted on the protective device – e.g., a safety light curtain – that triggers the protective device
- A rope length sensor detects the movement of the machine. This determines the time until the dangerous movement is stopped.
- The measurement is carried out at maximum movement speed if possible.
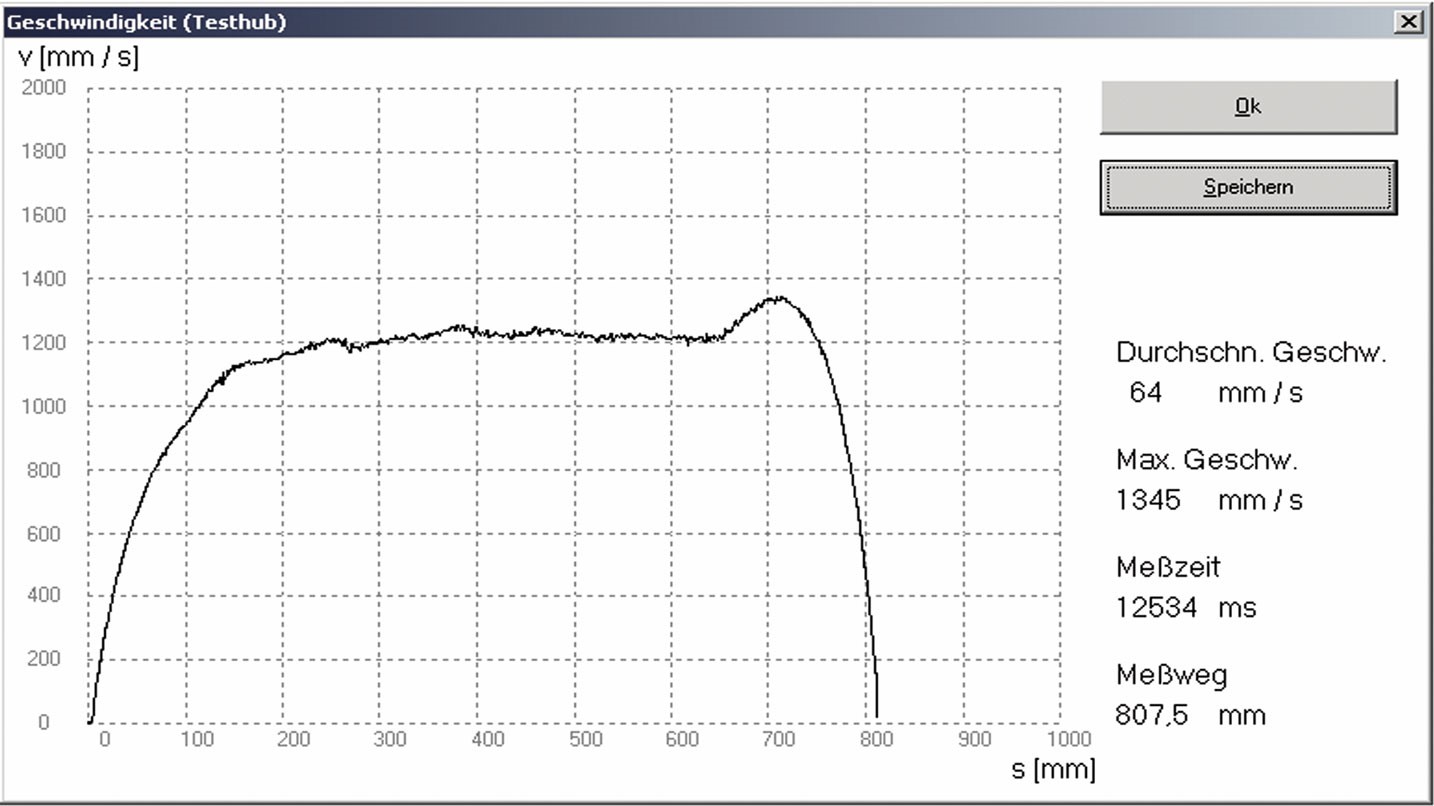
Evaluation of the results
In accordance with the requirements of the ISO 13855 standard, we conduct ten measurements in succession. The largest value from this series of measurements is then documented as the result for the stopping time and used to assess the safety distance.
A graphical analysis of the braking movement is also available if required.
“Safety technology on machines and systems” status check
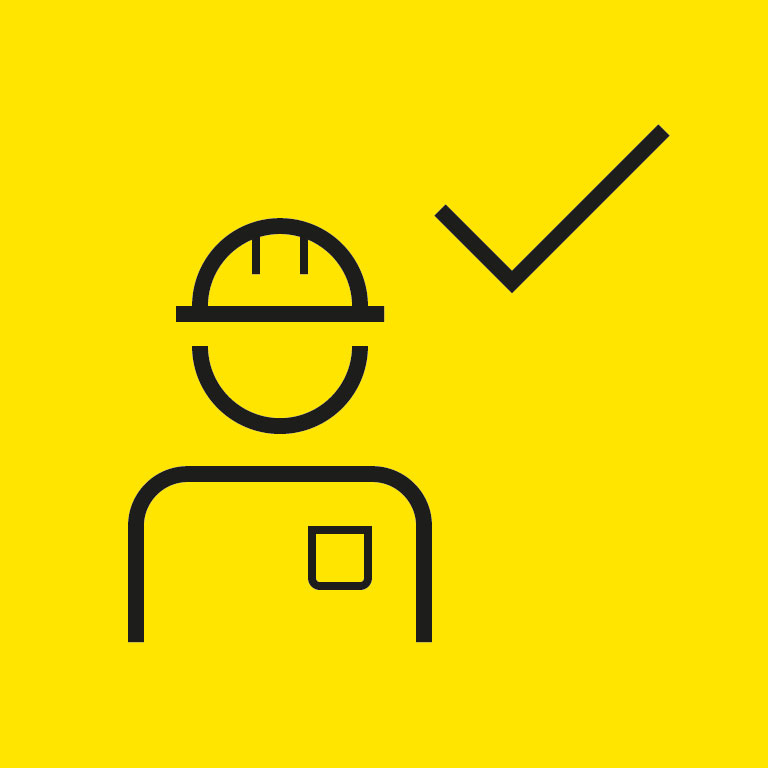
Your requirement
- As an operating company, you are responsible for the safety of your machines. Changes, extensions or wear and tear affect the condition of the machines and the protective devices used over the course of time.
- A “reliable” overview of the condition of the machinery is necessary to identify any need for action with regard to the machines’ safety.
Our solution
- Our experts will professionally identify, describe and assess existing risks for mechanical hazards on your machines and systems
- The current situation is recorded by means of an on-site inspection
- We summarize the results in a detailed report, including a risk value for each hazard
Advantages for you
- The “status check” identifies hazards for employees as well as deviations with respect to legal requirements
- The results provide recommendations for a rapid response to acute hazards
- We determine a risk value for every hazard. This makes it easier to prioritize any necessary corrective measures.
Hazard assessment
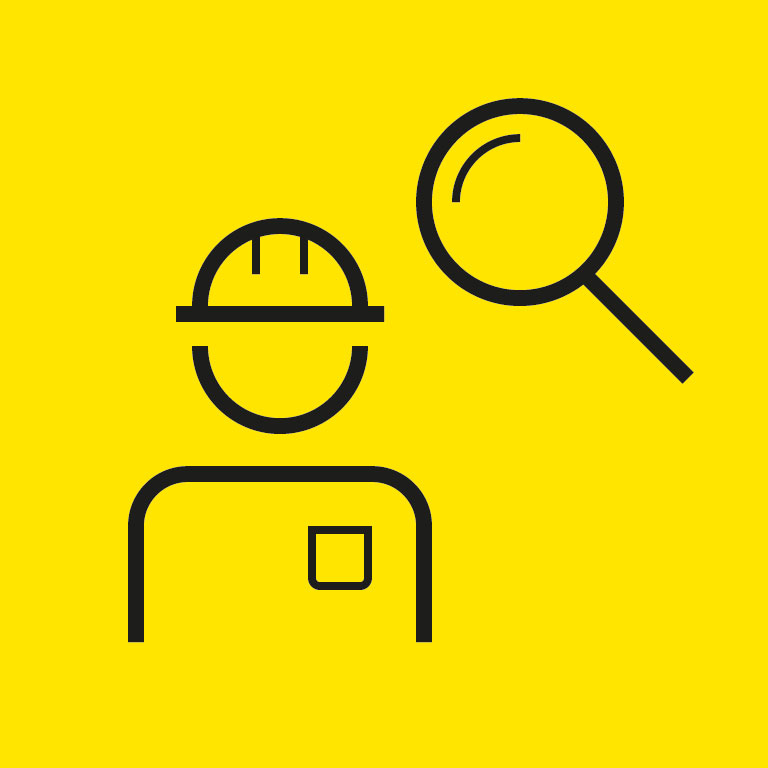
Your requirement
- As the operating company, you are obliged to carry out a regular risk assessment in accordance with the state of the art on the basis of the German Industrial Safety Ordinance
- In the case of modifications, extensions or wear over the lifetime of a machine, you must identify deviations between the safety-related target state and the actual state.
Our solution
- Analysis of the existing mechanical dangers
- Estimation of the existing dangers and calculation of a risk value
- Report with description of the required action
Advantages for you
- Legally compliant implementation of the requirements of the German Industrial Safety Ordinance
- A guaranteed safe work environment
- Machine-specific directives and standards research
- Independent, external assessment with extensive knowledge of the hazards from comparable machines