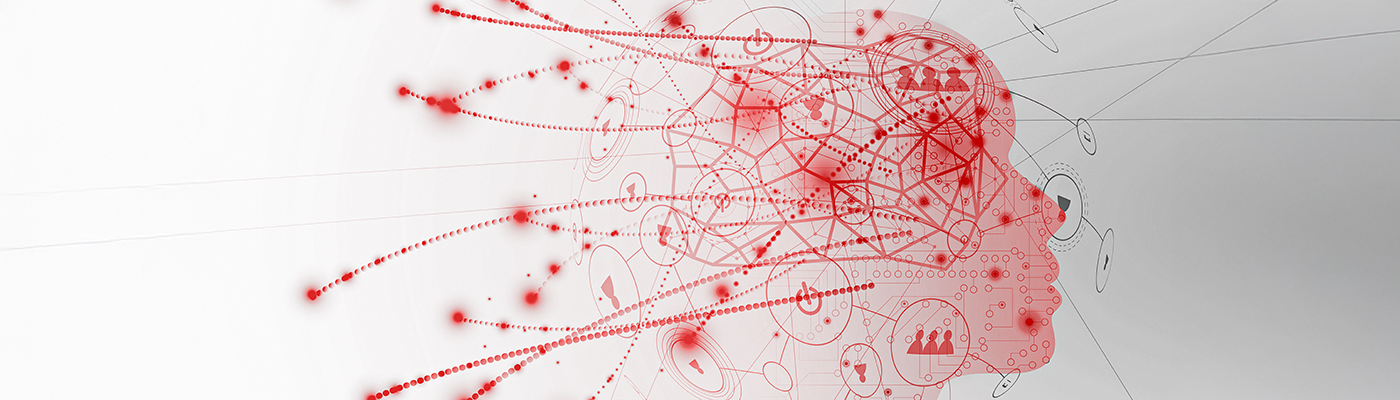
Artificial Intelligence: Sensor Data for Increased Efficiency
Sensor data as the gateway to factory automation
Data is the key to success when it comes to intelligent production systems. Sensors generate large amounts of process data on a daily basis, and this data is transferred to the control system via a communication interface and processed. This data is already being used to manage systems and production lines and evaluate information, for more flexible processes and increased system availability.
Artificial intelligence provides the context
Artificial intelligence helps to make production processes more intelligent, flexible and economical by drawing on data generated from field components. AI algorithms evaluate large amounts of data and ascertain key performance indicators or actions that need to be taken so as to continuously improve system productivity.
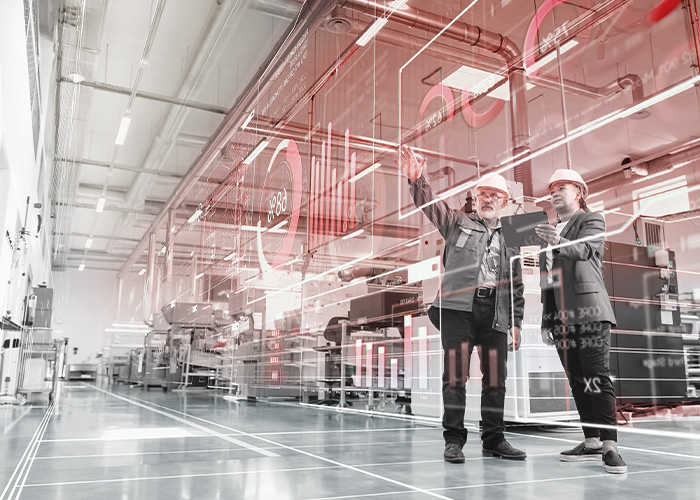
Artificial intelligence can be used, for example, to help differentiate various fault causes and quickly detect any nuisances. This especially pays off if there are multiple intelligent sensors installed in a system: When it comes to intralogistics, it’s possible for up to 1,000 bar code readers to be installed across distances that stretch for miles but are part of one system. Searching for the specific bar code reader that isn’t working properly can be as hard as searching for a needle in a haystack. Every bar code reader shares its status with an Ethernet-based Bus interface, for example: “Reading is precise” or “Reading is particularly poor”. Sensor data can be aggregated and context illustrated through an AI-supported evaluation process. Does the poor reading rate always occur on one bar code reader, only one label, with a certain type of label, or at a certain installation location? Nuisances can be quickly identified and rectified.
From the sensor to the cloud
Issues such as condition monitoring or predictive maintenance require sensors that are capable of making data available worldwide and in a standardized format. We have been a forerunner from the start, and we are working on standardizing industrial communication.
We offer sensors that deliver data, e.g. through IO-Link or via OPC UA, to the control or make it available to the cloud and edge devices. In this way, our smart sensors are capable of managing production processes and evaluating information so that any problems can be detected early on.
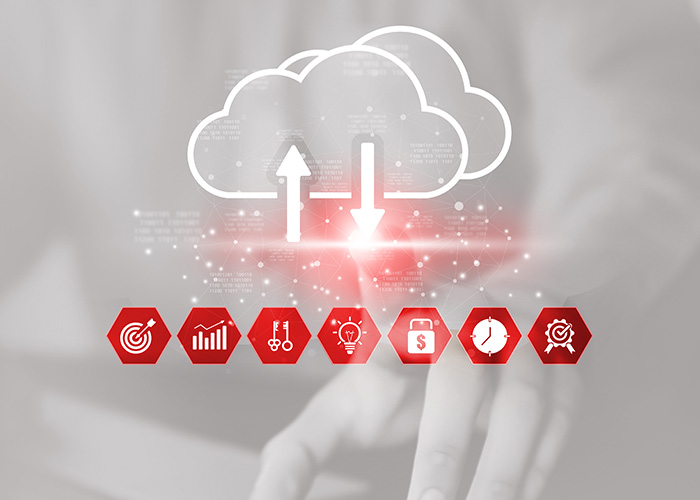
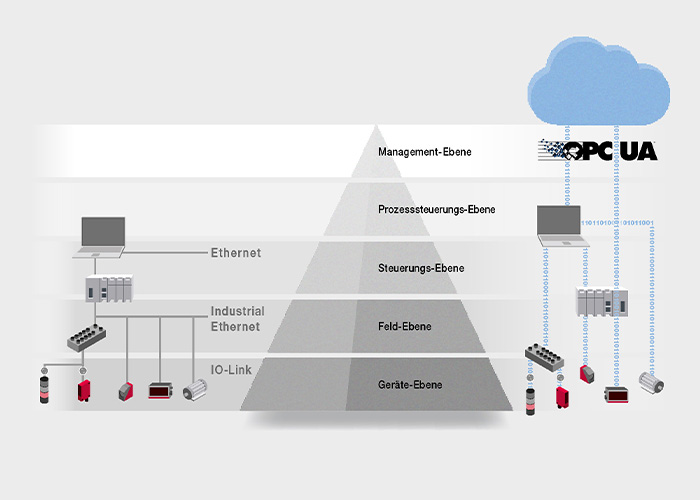
Our dual channel principle involves measurement data for process control being transferred in real time over the first channel, then the information for monitoring and analyzing the machine being transmitted over the second channel. The dual channel principle is also helpful in state monitoring and predictive maintenance during production. Soiling or misalignment of a sensor can change the signals to such an extent that switching faults occur. The dual channel principle can also assist commissioning. Based on the OPC UA communications standard, which has established itself as the standard protocol, the sensors transfer data into the cloud. Error messages can be sent to an operator this way and then resolved together. And this can be done on a global scale. OPC UA-certified sensors have been part of our range since as early as 2016.
Using the IO-Link communication system, sensors and actuators can be integrated into a digital machine environment. Measurement data and other information can be prepared, such as device information or diagnostic data. This creates high process transparency, means sensor systems are easy to commission and makes preventative maintenance possible. As the founding member and technology developer of IO-Link, we possess extensive know-how. You always receive the latest technology – such as Smart Sensor Profile – and many sensors with additional functions as well as connection options to the cloud. With our networked solutions, you are prepared for the requirements of the smart factory.
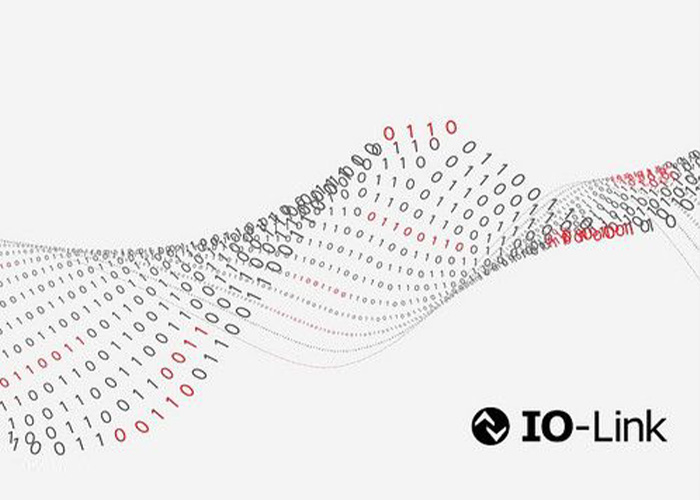
Our intelligent sensors for economical processes
Our innovative sensors can be used to manage processes in networked systems. What’s needed from the sensor system varies greatly depending on how and where it’s going to be used. In order for processes to be stabile and economical, sensors should be tailored as well as possible to fit with how they are going to be used - it’s likely that not every sensor will need a microchip or individual AI-engine even in the future.
Innovative sensors to benefit you
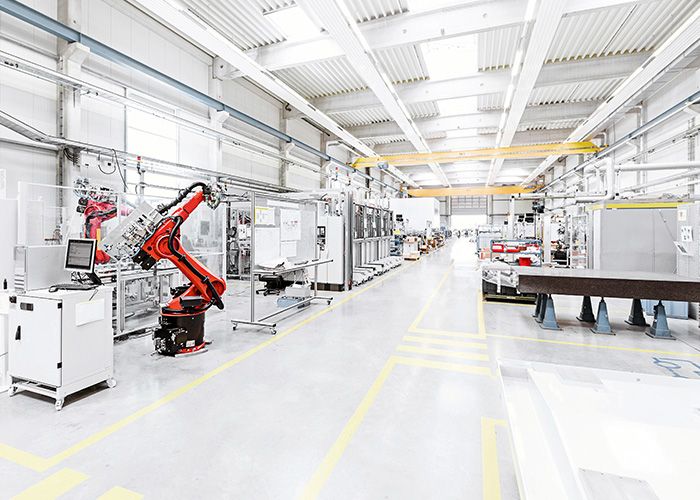
Technologies
Industrial Ethernet, integrated connectivity and more kinds of technology: we are constantly working on technological challenges and important issues in the markets of our customers.