Sensor solutions for stacker cranes
Stacker cranes handle the storage and retrieval of goods in automatic high-bay warehouses. The speed and reliability of the stacker cranes - also in the low temperature range - are decisive for the overall performance and system availability.
The easy alignment of our sensors ensures fast and error-free commissioning. During operation, our sensor solutions ensure the best possible function of the stacker crane. In this way, your throughput can be optimized through dynamic and precise storage and retrieval of goods. Optical compartment occupation checks and push-through protection reliably protect the stored goods and system.
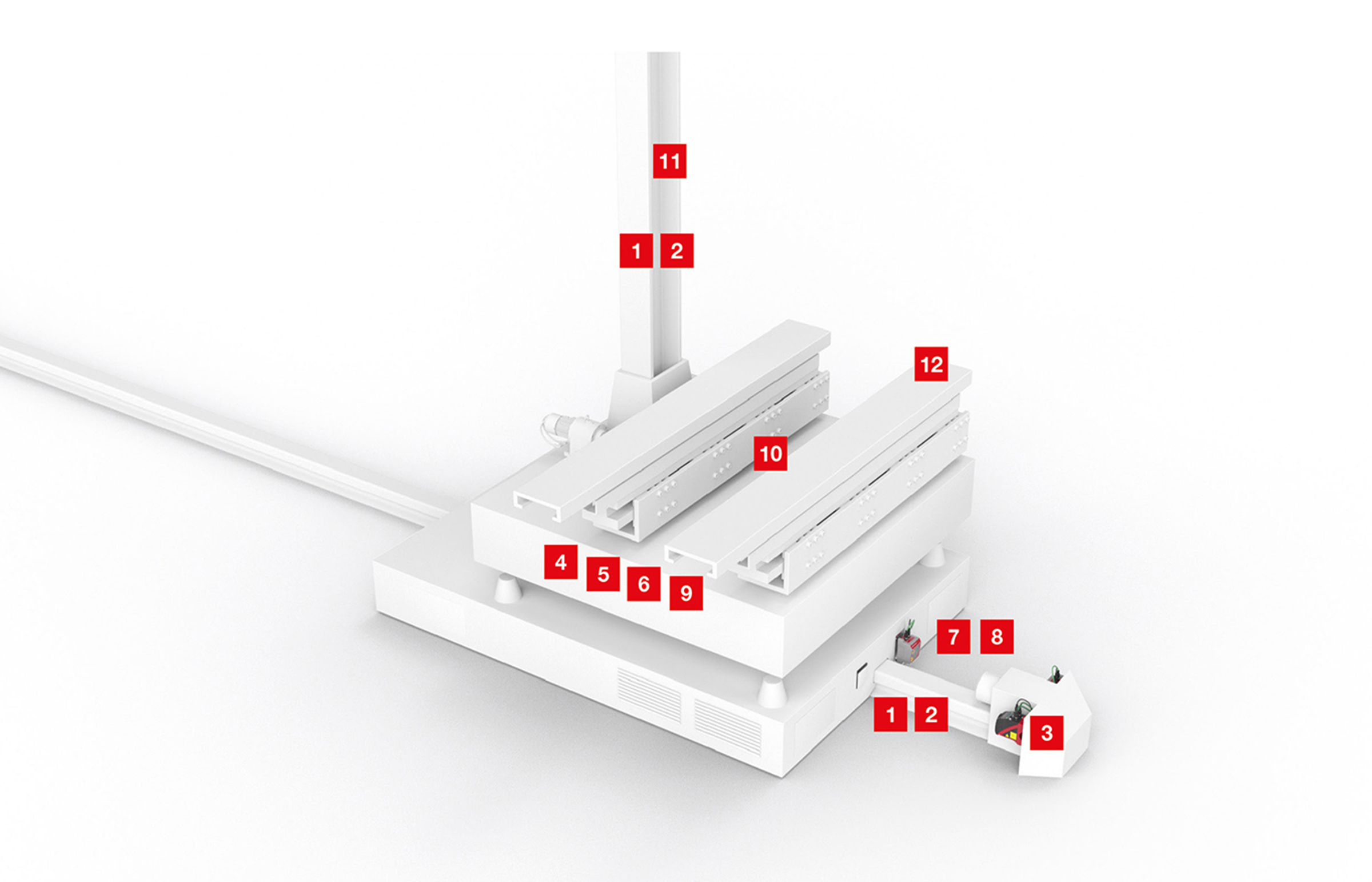
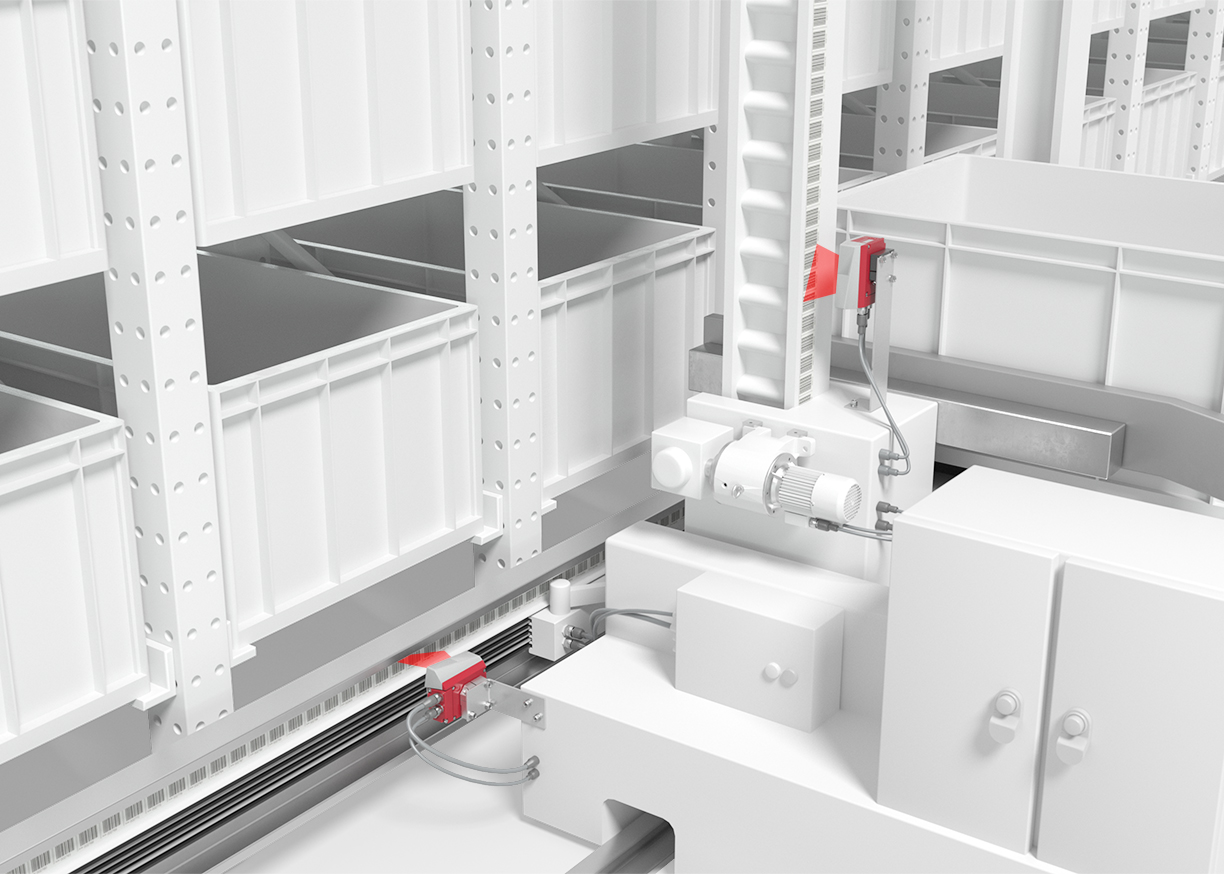
Requirement:
The stacker crane or load receptacle must be positioned in the X-direction (travel axis) and Y-direction (lifting axis) accordingly for the position to be approached.
Solution:
The BPS 300i compact bar code positioning systems enable exact positioning. Interfaces for fieldbuses, industrial Ethernet as well as SSI or serial connections make integration in the control simple and flexible. The configuration and diagnosis of the devices are just as easy.
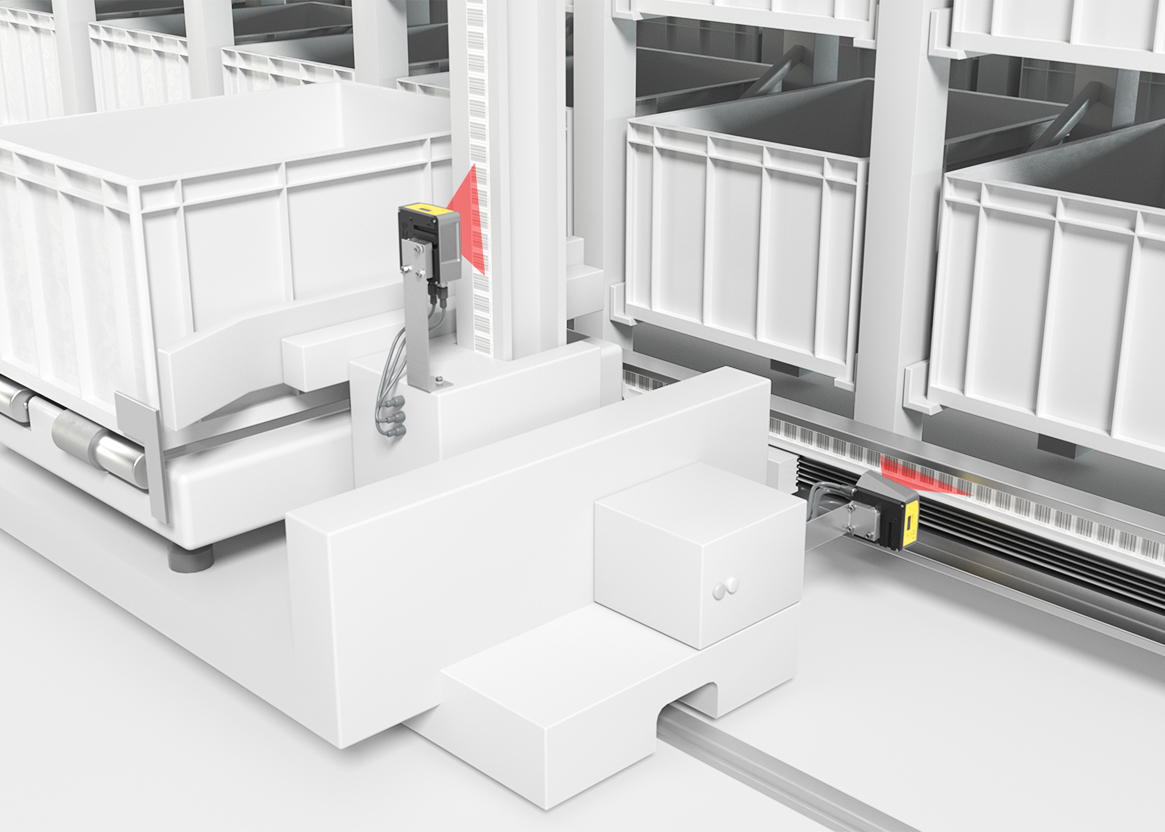
Requirement:
The stacker crane or load receptacle must be positioned in the X-direction (travel axis) and Y-direction (lifting axis) accordingly for the position to be approached. Often the risk assessment requires safe position and speed monitoring. For this purpose, safe position detection is necessary.
Solution:
The FBPS 600i fail-safe bar code positioning system requires just one sensor for safe position detection. The device is connected to a safe evaluation unit – e.g. a frequency inverter – via two SSI interfaces and is suitable for applications up to PL e. This means that safety functions can now be easily implemented.
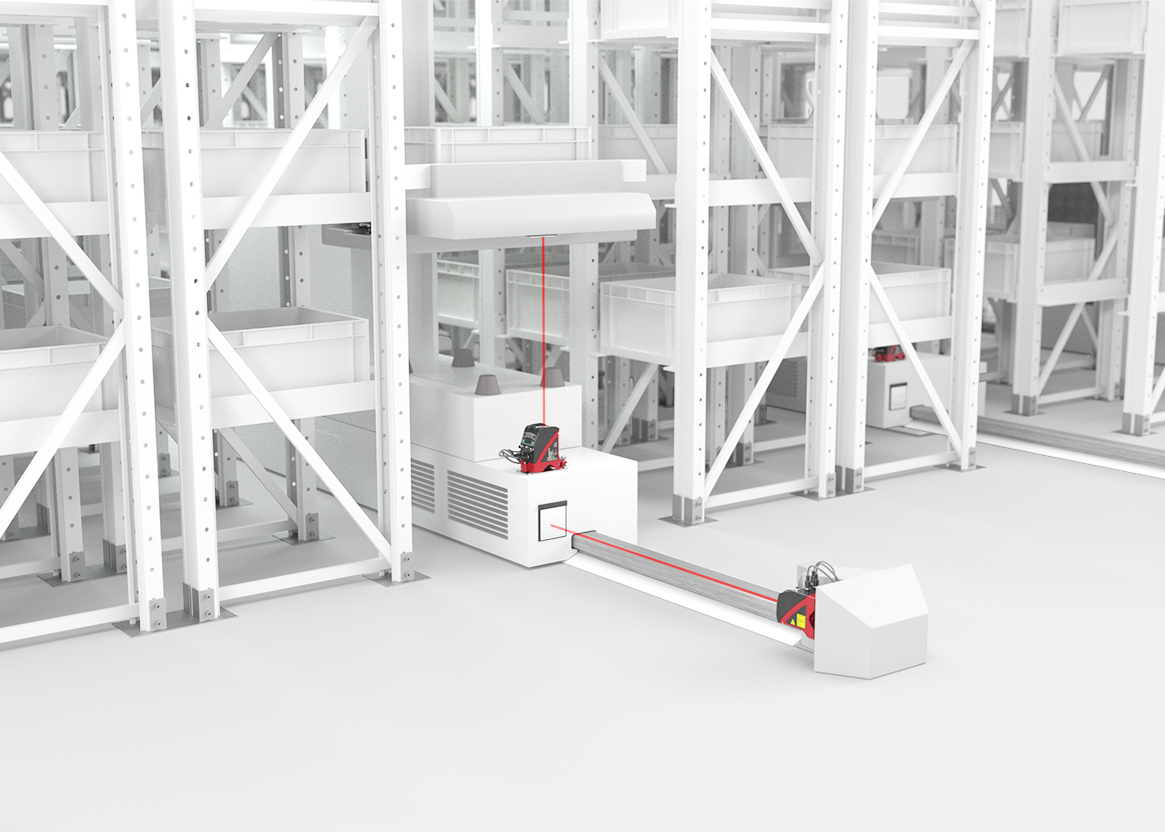
Requirements:
The stacker crane or load receptacle must be positioned in the X-direction (travel axis) and Y-direction (lifting axis) accordingly for the position to be approached.
Solution:
The AMS 300i laser positioning system quickly determines distances to moving system parts over a distance of up to 300 m with high absolute accuracy. In millisecond intervals, the devices make the measured values available for dynamic control via an extensive selection of industrial Ethernet or fieldbus interfaces.
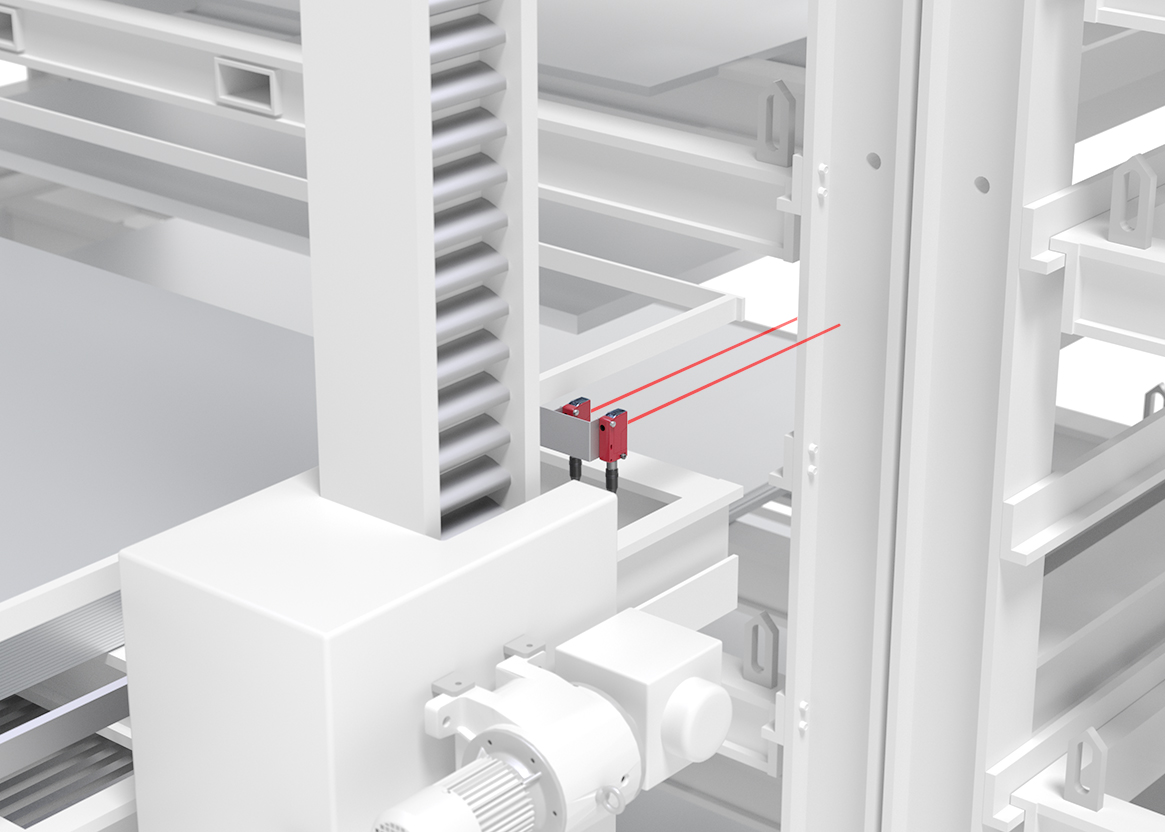
Requirement:
After the rough positioning of the stacker crane, the compartment fine positioning should take place in the horizontal (X) and vertical (Y) direction. For this purpose, the bar and column edges should be optically sensed at a distance of 100 to 600 mm.
Solution:
The HT 25C and HT 46C diffuse reflection sensors with background suppression are used for positioning the load receptacle. A wide range of profile types as well as color or glossy surfaces are reliably detected. Thanks to the optimized beam path, the sensors function reliably even in the case of columns with holes.
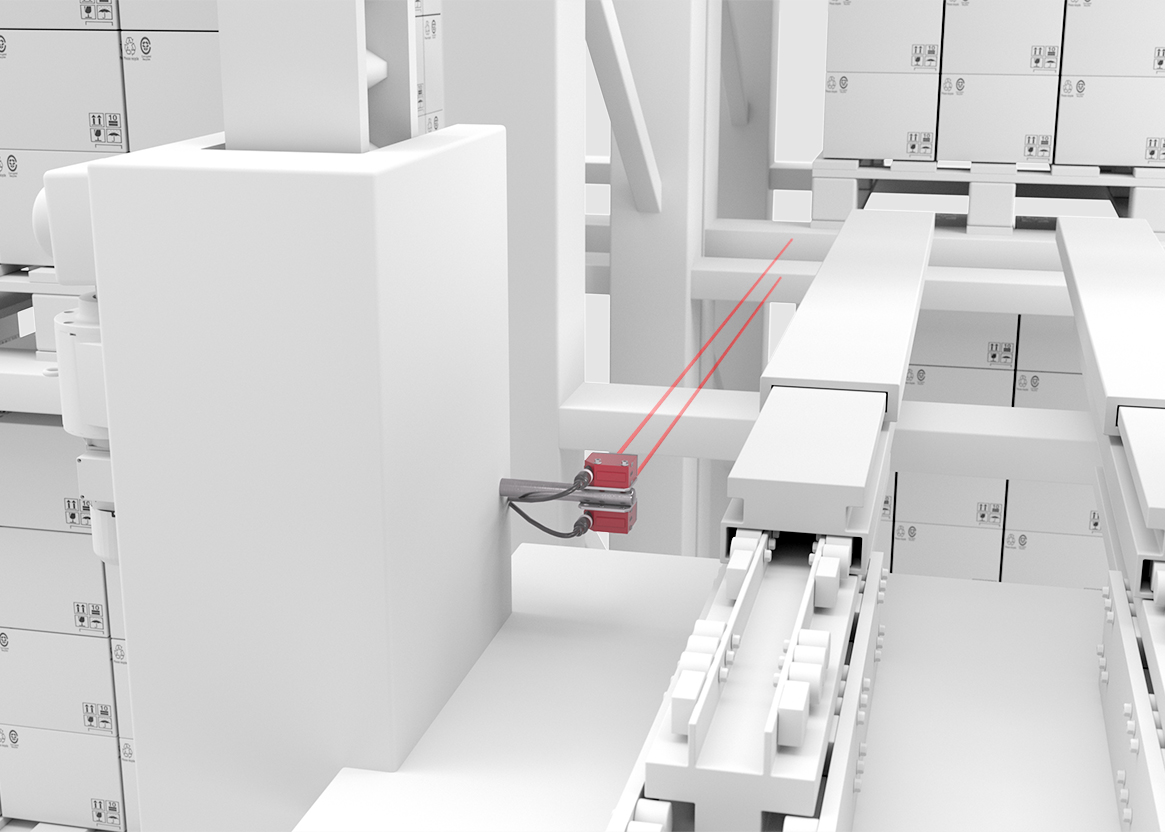
Requirement:
After the rough positioning of the stacker crane, the compartment fine positioning should take place in the horizontal (X) and vertical (Y) direction. For this purpose, the bar and column edges should be optically sensed at a distance of 100 to 1,900 mm.
Solution:
The HT 110 series diffuse sensors reliably detect different materials even under changeable conditions. They are characterized by precise switching behavior at profile edges. With their operating range of up to 5,000 mm, they are also suitable for use in double-depth storage locations.
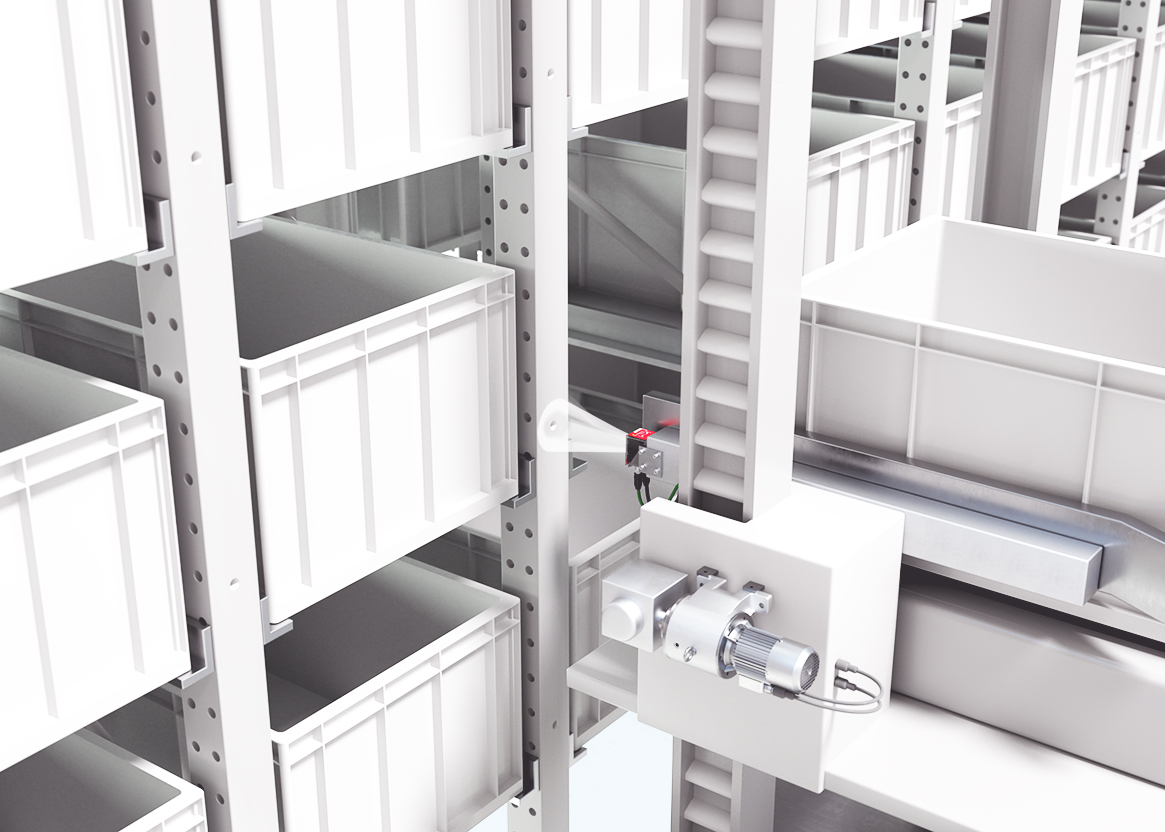
Requirement:
After the rough positioning of the stacker crane, the compartment fine positioning should take place in the horizontal (X) and vertical (Y) direction. For this purpose, the bar or column markings are to be sensed by a camera at a distance of 100 to 1,900 mm.
Solution:
The compact IPS 200i/400i camera-based sensors are used for compartment fine positioning in front of single-depth or double-depth racks. Via the integrated Ethernet TCP/IP, PROFINET or Ethernet/IP interface, the devices can be easily integrated into different controls and easily configured via the integrated web server.
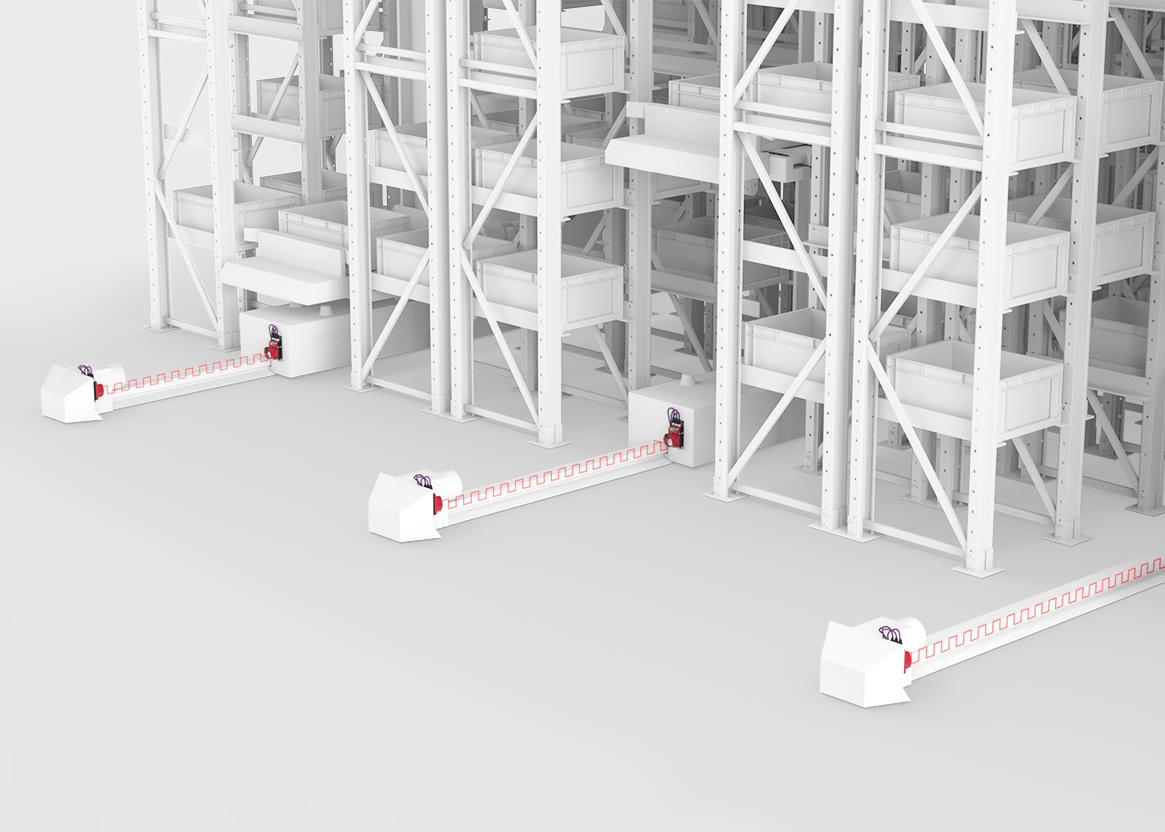
Requirement:
Data is to be transmitted wirelessly from fieldbuses such as PROFIBUS, CANopen and Interbus to the stacker crane or the load receptacle. The transmission rate should be up to 2 Mbit/s.
Solution:
The DDSL 200 data transmission photoelectric sensor is available with all common industrial fieldbus interfaces and is therefore easy to integrate into the system. Different operating range models from 80 to 500 m always offer a tailor-made solution.
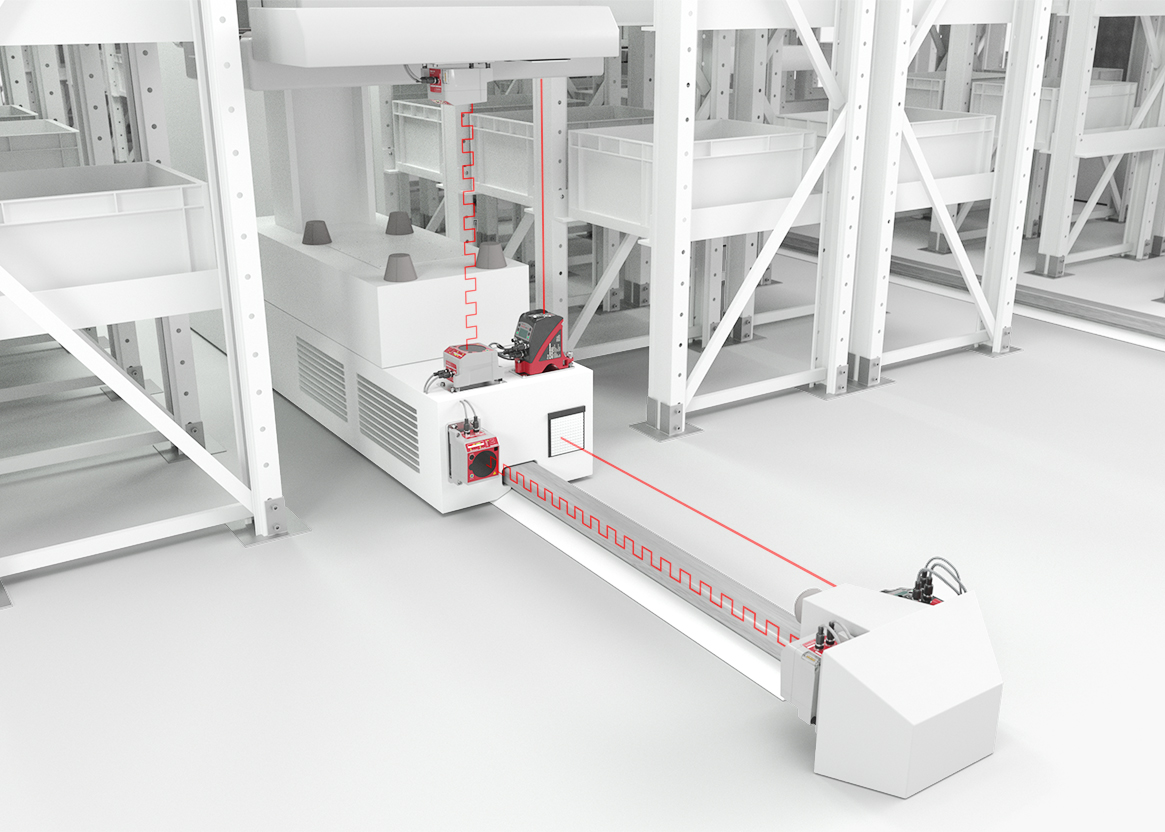
Requirement:
Data should be transmitted wirelessly from Ethernet-based fieldbuses such as PROFINET, EtherCAT and Ethernet TCP / IP to the stacker crane or the load receptacle. The transmission rate should be designed for data volumes of up to 100 Mbit/s.
Solution:
The DDLS 500 data transmission photoelectric sensor with industrial Ethernet interfaces transmits data at a rate of up to 100 Mbit/s. The alignment laser and the pre-mounted mounting plate make it particularly easy to align the devices, and the integrated web server ensures fast and location-independent remote diagnosis.
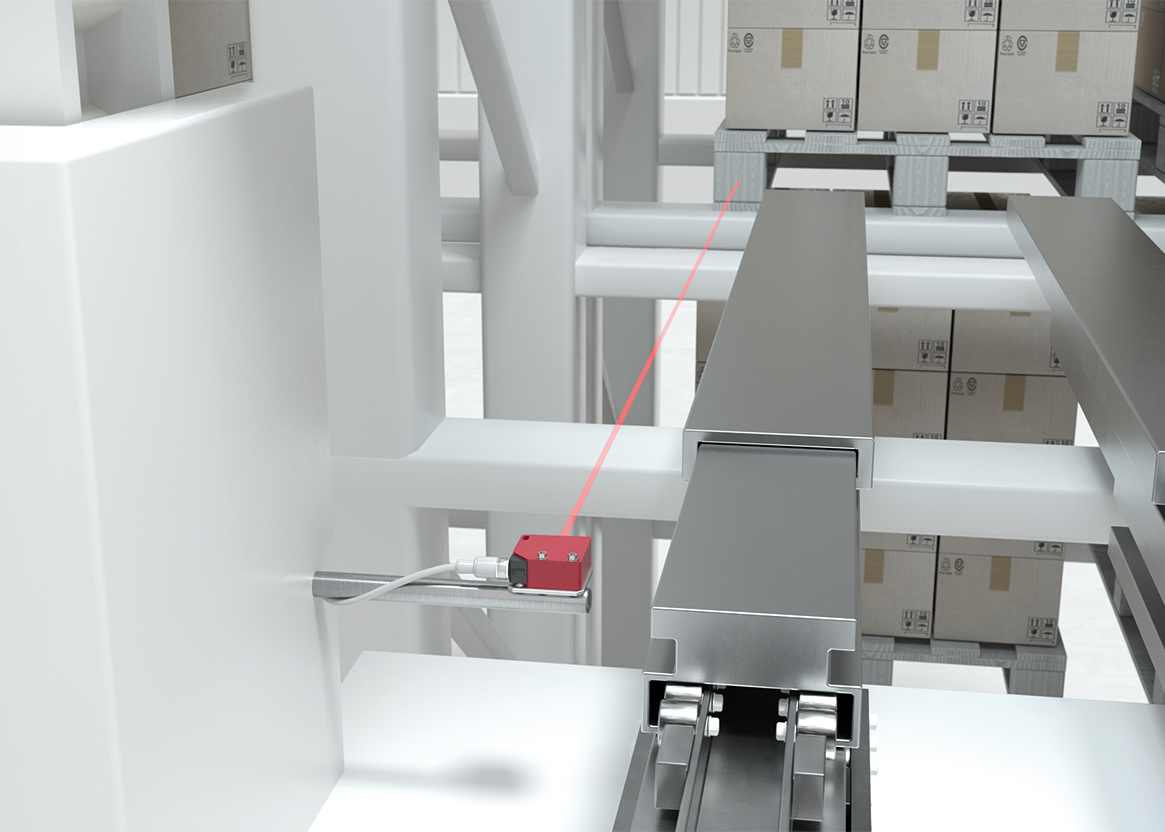
Requirement:
Before a pallet or a cassette can be stored in a rack, a check must be performed to determine whether the rack is empty. During retrieval, it must be monitored that the stored material is not pushed through when the telescopic arm or fork is moved.
Solution:
Thanks to their focused laser, sensors HRT 25B Long Range, ODS / HT 10 and ODS / HT 110 detect the goods at an operating range of up to eight meters and thus offer a high function reserve. With switching product models, the movement of the cassette can be detected with the help of the window function.
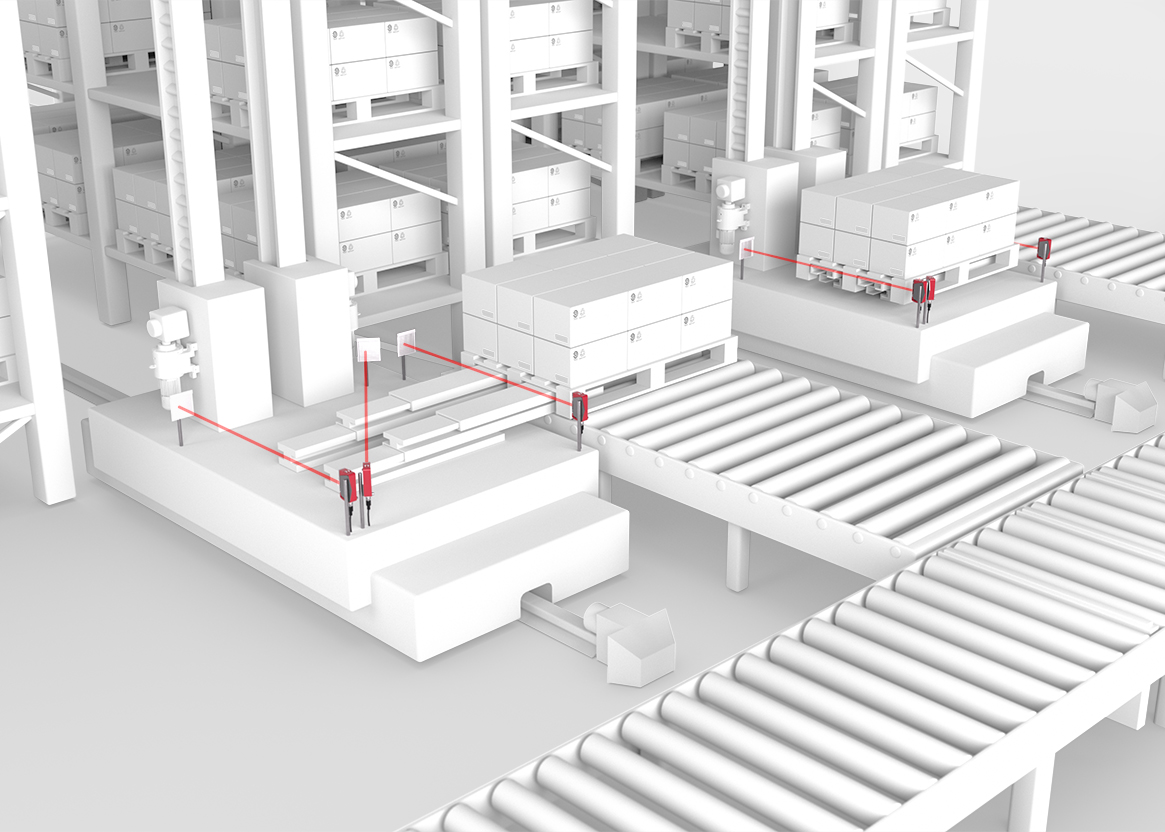
Requirement:
After storage or retrieval, a check must be performed to ensure that the load receptacle has completely unloaded or pulled in the material in order to avoid collisions and downtime.
Solution:
The optical sensors of the 3C, 25C and 46C series are characterized not only by their long operating range and increased function reserve, but also by their easy handling. With their different optics models, the devices stand for reliable object detection - e.g. even with shrink-wrapped or perforated packages.
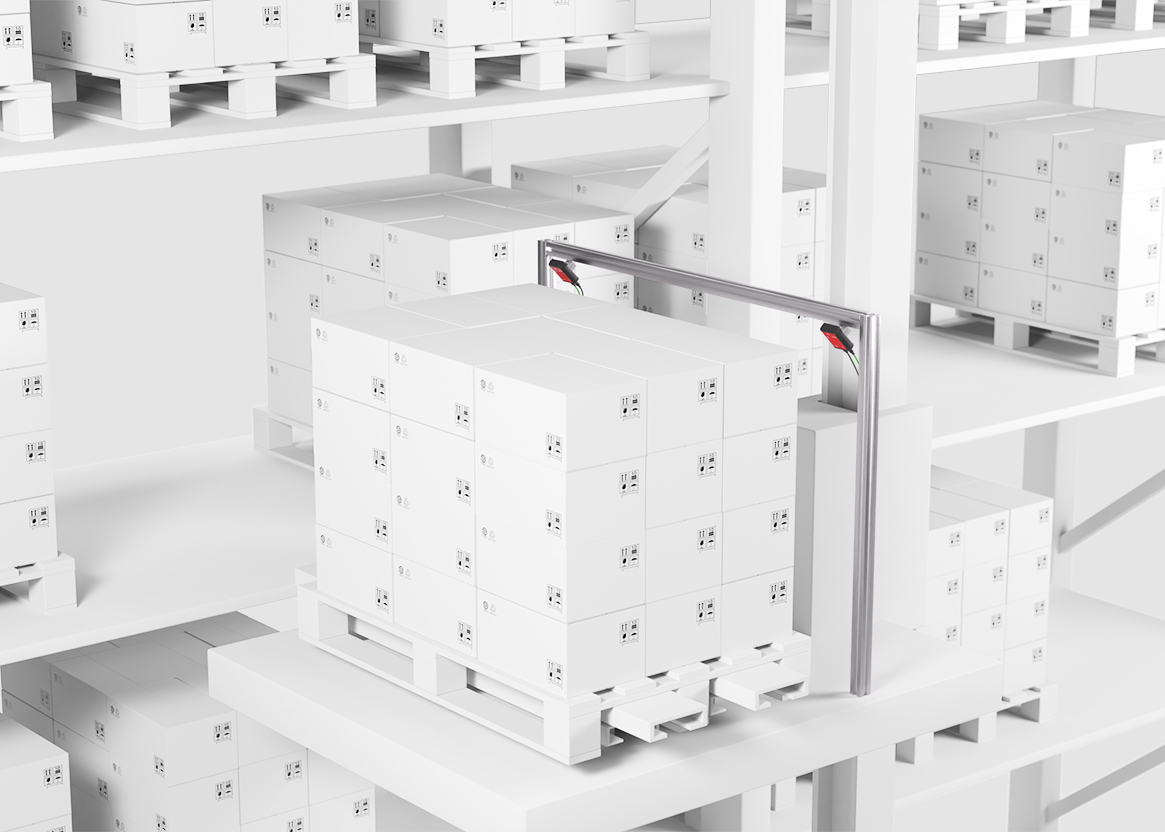
Requirement:
In order to be able to make a visual diagnosis of the stacker crane and load receptacle without having to be on site in person, a camera is needed directly on site.
Solution:
The industrial IP camera LCAM 308 offers insights into areas which are not accessible by plant operators. This simplifies troubleshooting in case of failure. The robust camera delivers live streams at high image quality due to its Ethernet interface. In addition, the recording of the last minute can be retrieved.
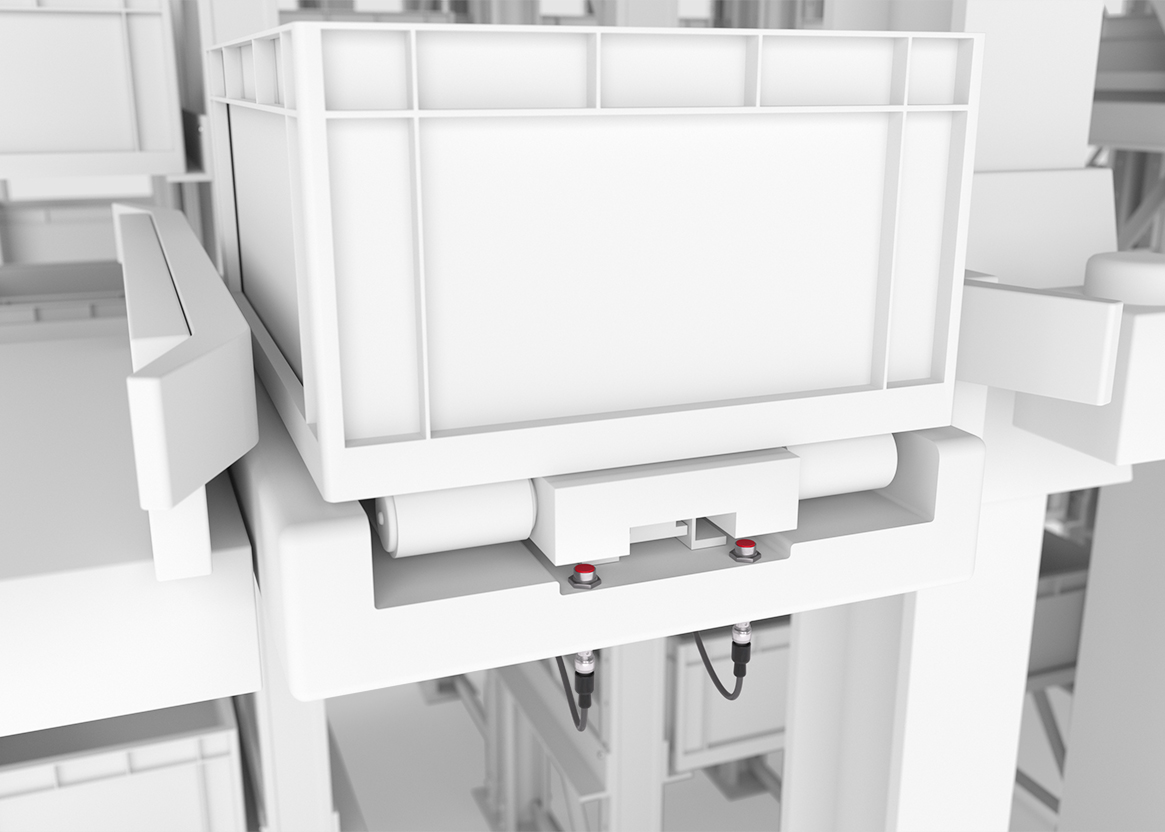
Requirement:
Before the stacker crane is allowed to move, it must be checked whether the load receptacle is in the final position.
Solution:
The inductive sensors of the IS 208 and IS 212 series reliably detect metal objects. The devices with robust metal housing can be optimally adapted to the respective application by selecting the switching output, the connection and the operating range.