Safety applications
Requirement:
The safeguarding point of operation at a machine or system is to be guarded by an electro-sensitive protective device. The necessary distance between the protective device and safeguarding point of operation is to be as small as possible.
Solution:
The safety light curtains of the MLC series with various resolutions ranging from 14 to 40 mm offer reliable finger and hand detection. This allows small safety distances between the safety sensor and the safeguarding point of operation.
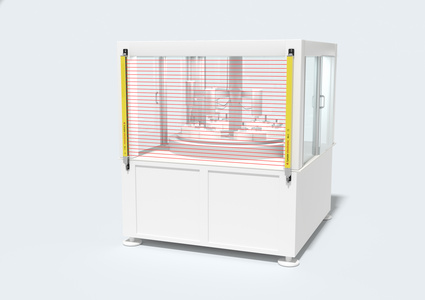
Requirement:
Access to the safeguarding point of operation is to be guarded by a safety light curtain. If this sensor can be reached under or stepped behind, then a further safety light curtain is required in order to detect these situations.
Solution:
The cascadable MLC 520 and MLC 520-S safety light curtains allow up to 3 segments to be linked together. They are integrated in the control via a common connection. This makes installation easy and cost‑effective.
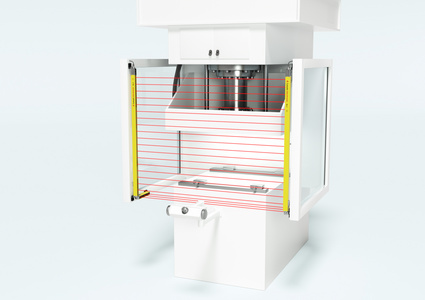
Requirement:
The safeguarding of the point of operation must detect an intrusion into the protective field. Fixed or moving machine parts or work pieces inside the protective field, however, are to be permitted and must not cause a shutdown.
Solution:
The MLC 530 safety light curtains feature the fixed blanking, floating blanking and reduced resolution functions. These functions can be configured so that certain objects are permitted inside the protective field.
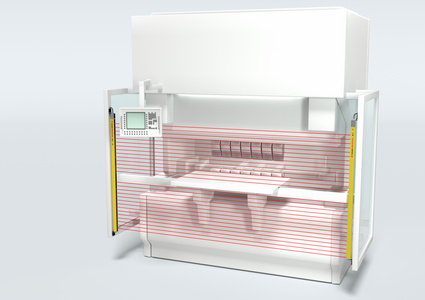
Requirement:
While the side-tracking shelf is moving, the foot space is to be monitored for the presence of persons. If multiple shelf rows are installed one behind the other, there must be no interference between the sensor signals of the rows.
Solution:
The SLS 46C single light beam safety devices monitor the foot space over a length of up to 70 m. They are available as a type 4 variant and as a particularly easy‑to‑align type 2 variant. The use of models with red light and infrared light prevents mutual interference between the shelf rows.
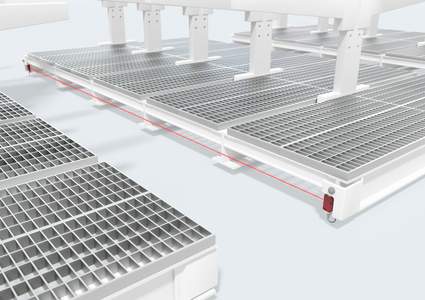
Requirement:
If it is possible to reach through a narrow opening into an area where a hazardous movement takes place, then this opening must be guarded to prevent access.
Solution:
The single light beam safety devices SLS 46C are used for small openings. They are available as type 2 and type 4 variants and can be integrated easily using connectors or cables.
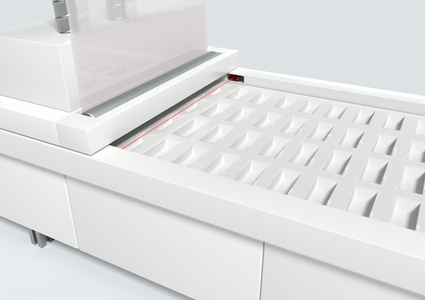
Requirement:
Access to a dangerous area on a machine or system is to be secured. Optoelectronic safety sensors are to be used to enable the simple supply and removal of material.
Solution:
The MLD 300/500 multiple light beam safety devices offer affordable access guarding solutions. The transceiver models with an operating range of up to 8 m are especially easy to install. For wide-area guarding, transmitter/receiver models are available with a range of up to 70 m.
.jpg)
Requirement:
Access to the working range is to be guarded while the machine is in operation. To enable material entry and exit, the machine must be easily accessible from multiple sides.
Solution:
The MLD 300/500 multiple light beam safety devices in combination with the UMC mirror columns safeguard access to the machine on multiple sides and over lengths of up to 70 m. The integrated laser alignment aid makes installation quick and easy.
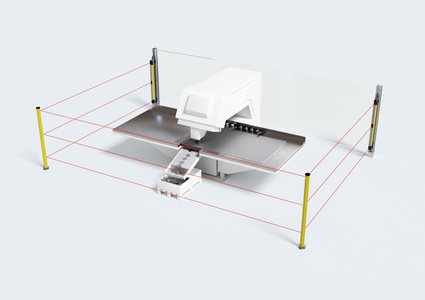
Requirement:
Access to dangerous areas by persons and vehicles is to be monitored using safety sensor technology. The sensors must not hinder free movement within the working range.
Solution:
The RSL 400 safety laser scanner is installed above the access area and the protective field is aligned vertically. This ensures that the working range is not restricted. By using two safety functions working in parallel, one RSL 400 can monitor two stations simultaneously and independently from each other.
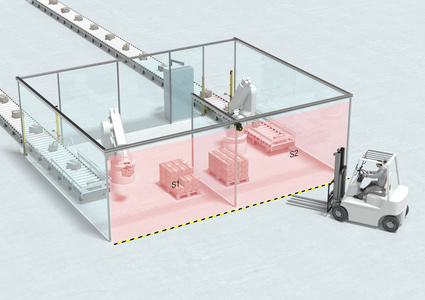
Requirement:
Access guarding on conveyor lines is to prevent persons from accessing the danger zone, while at the same time allowing the transported goods to pass through.
Solution:
The muting function bridges the safety sensor in a controlled manner to allow the transported goods to pass through. This function is already integrated in the MLD 300/500 multiple light beam safety devices and the MLC 500 safety light curtains. The MSI-MD-FB muting interface and MSI 400 safety control provide an external muting control.
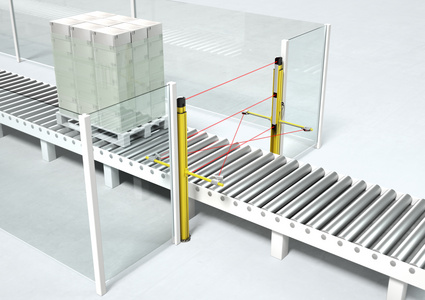
Requirement:
Access guarding on conveyor lines is to prevent persons from accessing the danger zone, while at the same time allowing the transported goods to pass through.
Solution:
With Smart Process Gating, the safety sensor is bridged by means of a control signal from the PLC. The function is integrated in the MLC 530 SPG safety light curtain. Additional muting sensors are no longer required and the systems have low space requirements thanks to SPG.
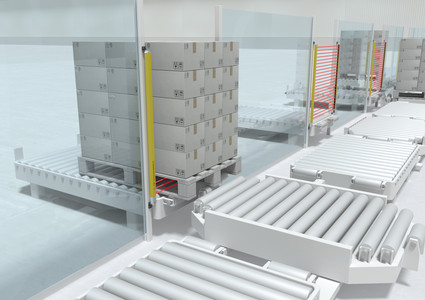
Requirement:
The hazardous working range of the machine is to be secured against access by and the presence of persons. The outline of the monitoring area is to be adapted to the contour of the machine.
Solution:
The RSL 400 safety laser scanners use configurable protective fields for area monitoring. Thanks to the 8.25 m operating range and a 270° scanning range, even large areas can be safeguarded with just one device.
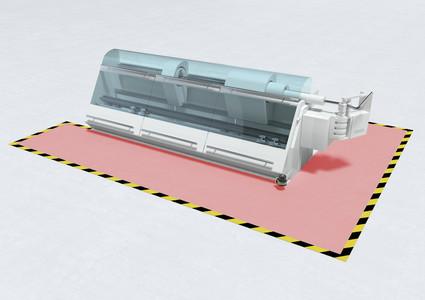
Requirement:
To prevent danger, the process may only be restarted once it has been ensured that no person is present in the working range or in the hidden area.
Solution:
The RSL 400 safety laser scanner monitors the presence of people with its configurable protective field. The LBK 3D safety radar system is used in harsh environmental conditions and also permits the presence of static objects in the monitored area.
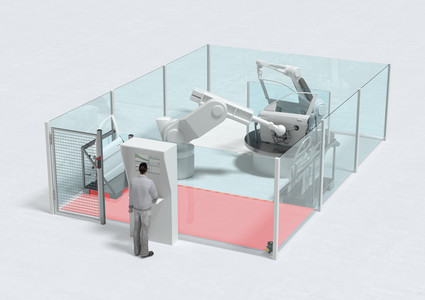
Requirement:
The hazardous working range of the machine should be secured against access and the presence of persons. Safe operation and high availability must also be guaranteed under harsh ambient conditions such as dirt, welding sparks, sawdust or humidity.
Solution:
The LBK 3D safety radar system detects movements in the monitored area and operates reliably even under harsh environmental conditions. The radar technology also permits the presence of static objects in the monitored area to be detected.
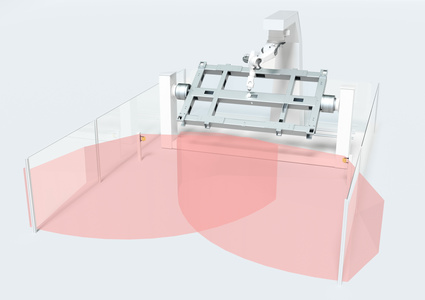
Requirement:
The AGV’s transportation path must be protected by safety sensors. The protective fields are to be flexibly adapted to the movement and loading situation. If the principle of natural navigation is used, the device is also to provide the measurement data for the navigation software at the same time.
Solution:
The RSL 400 safety laser scanner combines safety technology and high-quality measurement value output in one device. It has a scanning range of 270° and 100 switchable field pairs. Two scanners therefore provide optimum guarding of the AGV. The measurement data has a high angular resolution of 0.1° and a low measurement error.
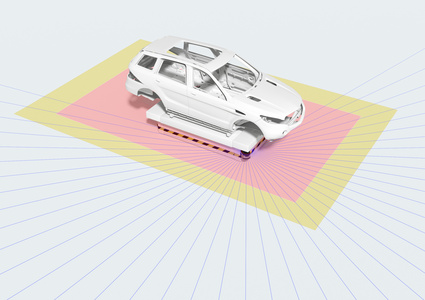
Requirement:
Movable safety guards such as doors and flaps protect the operator from hazards. The closed state of such protective devices must be monitored.
Solution:
The S20/200 series safety switches can be used universally thanks to their robust housings and wide range of installation options. The contactless, magnetically coded switches in the MC series are ideal for use in harsh, dirty or damp environments.
.jpg)
Requirement:
The closed state of safety guards such as doors or flaps must be monitored. EN ISO 14119 stipulates that measures to protect against manipulation must also be provided. If this is not possible though constructive measures, the sensor must have a high level of protection against manipulation.
Solution:
The RD 800 contactless safety transponders offer maximum protection against manipulation thanks to RFID coding. Their OSSD outputs are also easy to integrate into the safety circuit.
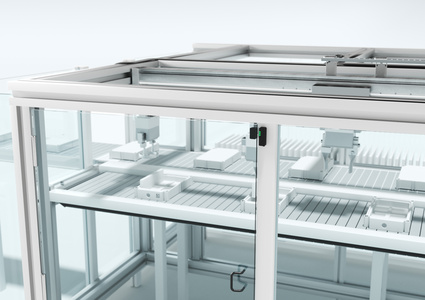
Requirement:
Areas with hazardous movements can be accessed via safety doors to allow maintenance. If the movement does not stop immediately after opening the door, the door must be secured by a safety switch with a safety locking device.
Solution:
The robust L series safety switches with locking device keep safety doors securely locked until access is released by an electrical signal. The series includes standard designs, devices with integrated operational controls, as well as devices with RFID-coded actuators.
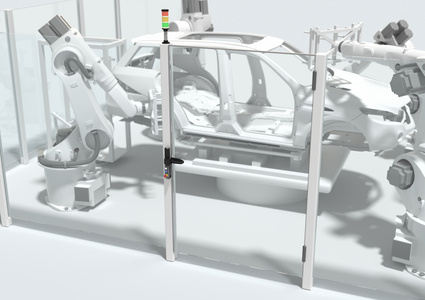
Requirement:
When doors or flaps are opened, the process is allowed to stop only at defined positions in order to avoid scrap or maintenance work when the process starts up again. The doors or flaps are only to be released once these positions are reached.
Solution:
The L series safety switches with locking device keep safety doors locked until the process control sends an electric release signal.
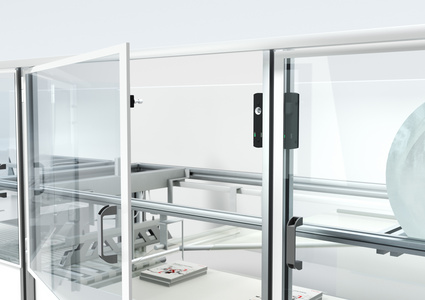
Requirement:
The final position of the saw blade is to be monitored so that it can be switched off at the end of the cutting process or for service work.
Solution:
The S300 position switch monitors when the final position is reached. Variants with plunger and various actuators make the device suitable for universal use. With its forced normally closed contacts, the S300 can also be integrated directly into the safety circuit.
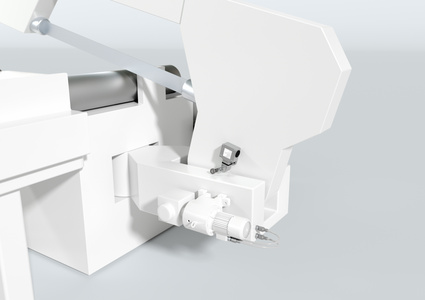
Requirement:
Machines and systems with dangerous movements must be equipped with an E-stop device. This can be operated manually in the event of danger.
Solution:
The ESB 200 E‑Stop button is used wherever it makes sense to be able to enter a stop command at a specific location. The ERS 200 E-stop rope switch is used for larger danger zones.
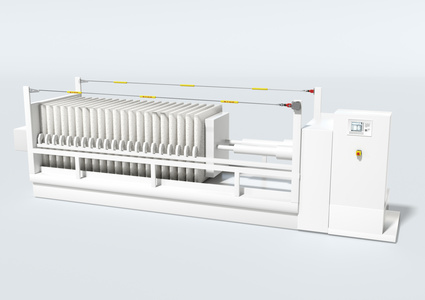
Requirement:
For correct execution of the safety function, safety sensors must be integrated into the machine circuit using safe control components in accordance with the requirements defined in EN ISO 13849-1.
Solution:
The reliable MSI safety relays allow individual safety sensors to be integrated quickly and easily into the safety circuit of machines and systems. The relays are tailored to specific applications or can be used universally depending on the model.
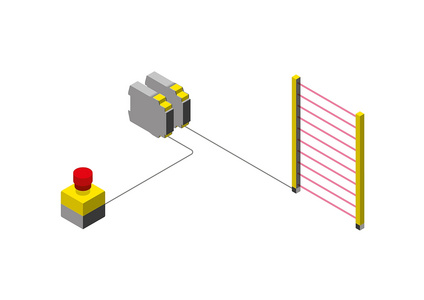
Requirement:
Multiple safety sensors must be integrated into the machine or system control. Functions such as a time delay for releasing a locking device or signal connections are also to be configured.
Solution:
The basic module of the MSI 400 expandable safety control already has 24 safe inputs/outputs as well as an Ethernet interface with Industrial Ethernet protocols. The project can be configured quickly and efficiently using the license‑free configuration software MSI.designer.
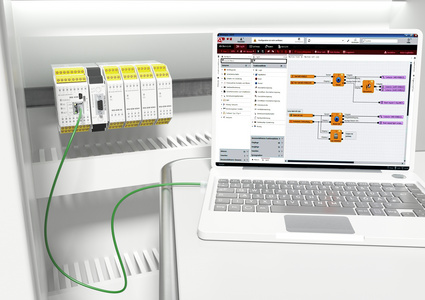
Requirement:
To protect employees during maintenance and set-up activities, dangerous machine movements must be reliably monitored. To protect machines and processes, upper and lower limit values – e.g. for speeds – must not be exceeded during operation.
Solution:
With the MSI 400 safety control, the inputs for safe movement monitoring are already integrated in the base module. It monitors the pulses from sensors for the limits required for safe operation, e.g. for speed, angle, position and direction information.
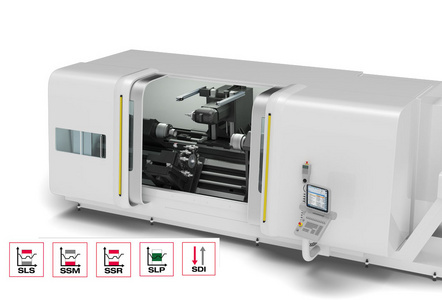
Requirement:
The dangers present at the system and the necessary Performance Level PLr have been determined with a risk assessment. The EN 528 standard provides support for safety requirements for stacker cranes. The necessary safe position and speed monitoring systems requires safe position detection.
Solution:
The FBPS 600i safe barcode positioning system offers safe position detection with just one device. It is certified as a safety device and meets the requirements for PL e / SIL 3. This makes safety functions particularly easy to implement.
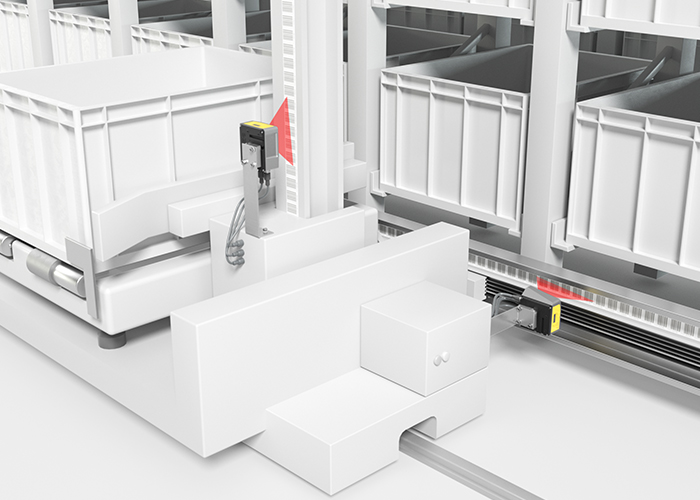