Diffuse sensors with background suppression
Advantages for you
- 2-in-1 sensor: Detection and measurement tasks solved by a single sensor
- Measurement value transmission in the process data with IO-Link
- Range adjustment via the teach button, cable or IO-Link
- Excellent black-and-white behavior (< ± 3 mm at 150 mm)
- The advantage of a sensor with IO-Link: Extensive diagnostic data from the device, e.g. temperature value, signal quality and warning
- Remote setting: Range adjustment with numerical entry via IO-Link (e.g. 100 mm)
- The devices have two independent switching outputs (OUT1 and OUT2)
Â
- Active ambient light suppression: No faulty switching despite direct light from LED hall lighting
- Models available with warning output (as OUT2)
- IO-Link models with Smart Sensor Profile acc. to Ed. 2 V1.1 (2021)
- Protection against tampering thanks to lock for the operational controls
- Status LEDs visible from all sides
- Device-specific IO-Link function modules available for Siemens, Beckhoff, Rockwell, etc.
Applications
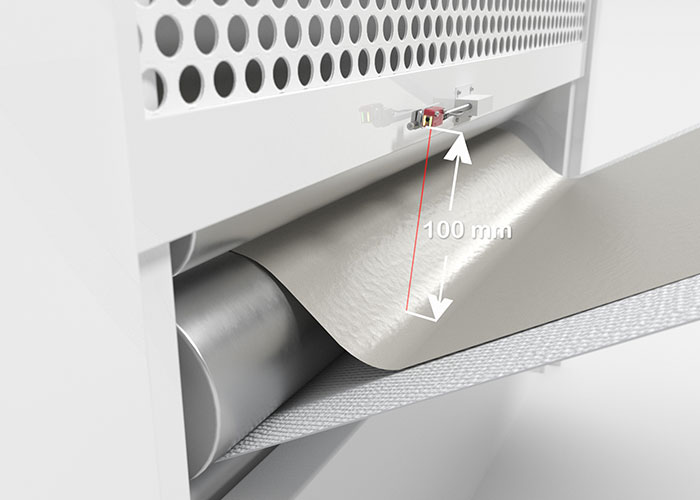
Dough loop control in the baking industry
Requirement:
In the food industry, a machine rolls out dough that is later processed into baked goods. This machine rolls out the dough precisely to the required thickness. While being transferred to the conveyor belt, the dough must retain its shape. Sensors are needed to monitor this. The measured variable is the distance between the dough and the sensor, which must always be between 100 and 120 mm.
Solution:
The sensor ODT 3C is positioned at the outlet of the rolling machine above the dough loop and points from above at the surface of the dough, which has been pressed by the machine, to supply a distance value to the superior PLC. The goal is to regulate the dough within an optimum distance range of 100–120 mm. If the sensor detects a measurement value outside this target range, the conveyor belt motors adjust the speed of the conveyor accordingly.
The measurement value is evaluated in the process data via IO-Link. In addition, diagnostic data is transmitted to the controller via IO-Link for Industry 4.0 purposes.
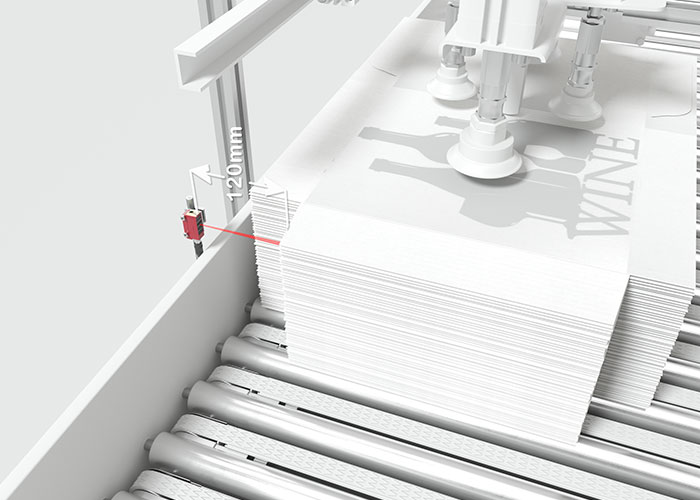
Pile positioning in the beverage/packaging industry
Requirement:
In the beverage industry, the filled bottles are often provided with secondary packaging in a carton packaging machine, where they are grouped together and combined into a unit pack ready for sale. The pre-cut cartons prepared on a pile must be automatically removed from the pile, separated and then provided for the gluing and folding process. To ensure optimum performance of the downstream process steps, the carton pile must be positioned at a specific point on the conveyor belt and then adjusted to be a defined distance from the laterally positioned sensor.
Solution:
Using the ODT 3C, the carton pile can be scanned along its long side for purposes of presence monitoring (switching sensor function) and then continuously positioned to a defined distance (e.g. 120 mm) at the edge of the pile flap by means of a measurement value (measuring sensor function).
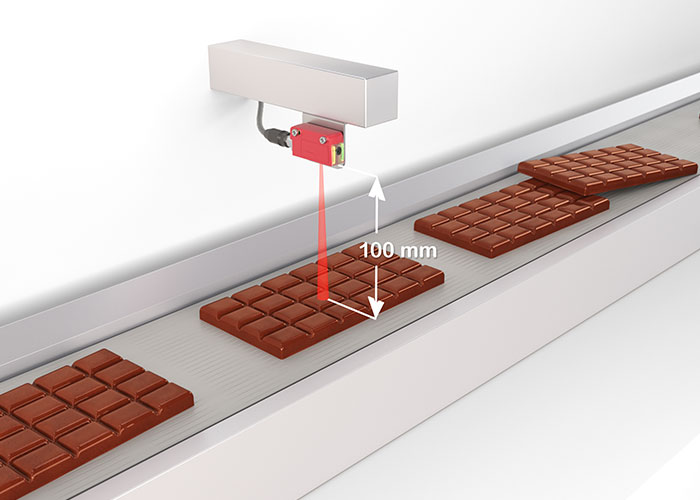
Quality and object height monitoring on the conveyor belt
Requirement:
In the food industry, the manufactured products (e.g. chocolate bars) are conveyed separately on the conveyor belt. During this process it is important to monitor whether any objects are lying on top of each other, meaning that they cannot be used for further processing (e.g. packaging).
Solution:
The sensor ODT 3C is installed just above the conveyor belt so that it looks down on the products from above. It detects the objects (switching sensor function) and measures their height (measuring sensor function). In this way, the sensor ensures that the products are conveyed separately on the conveyor belt, are not lying on top of each other and can therefore be used for the packaging process.
Technical properties
Â
 | Dimensions | 11 x 34 x 18 mm (W x H x L) |
Operating range | 10 … 150 mm | |
Measurement range | 30 … 150 mm | |
Resolution | 1Â mm | |
Accuracy | < +- 3 mm at 150 mm (6% … 90% remission) | |
Protection classes | IP67, IP69K | |
Ambient temperatures | -40°C up to 60°C | |
Connections | M8/M12 and cable variants | |
Models | Red light |
Application
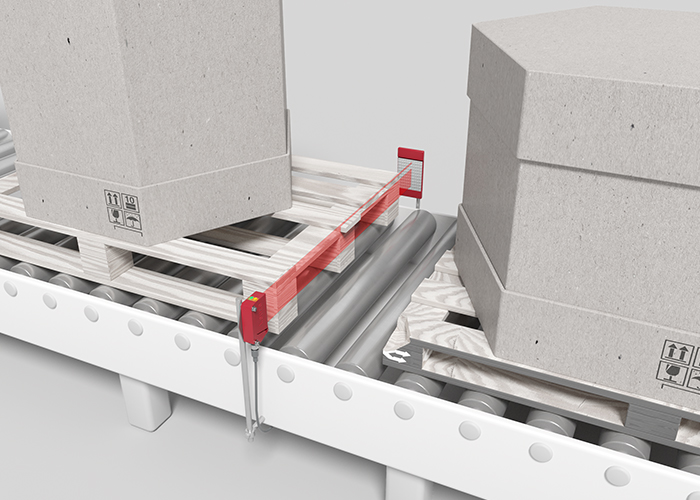
Classic application solution for pallet detection with retro-reflective photoelectric sensor
Mounting, alignment and commissioning
of the sensor system takes place on-site
- Retro-reflective photoelectric sensor with mounting device, rod extension arm and mounting bracket on the conveyor (front in figure)
- Reflector with mounting device, rod extension arm and mounting bracket on the conveyor (rear in figure)
Requirement:
Various pallet types with different dimensions run on the conveyor. All are to be reliably detected.
Solution:
The retro-reflective photoelectric sensor of the 46C series with broad, powerful light-band for the detection of objects with variable shape and openings reliably detects all pallet types.
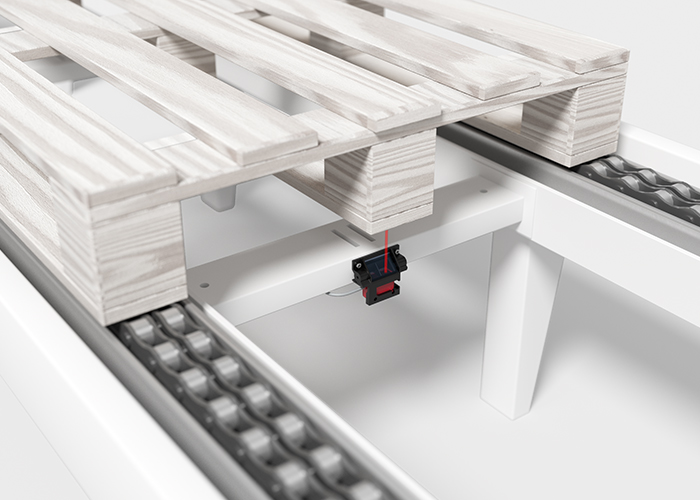
Pallet detection on conveyor systems with pre-installed sensor system
Requirement:
The efficiency of a new conveyor line is to be maximized during commissioning. The employees should be able to begin immediately with operation after setting up on the conveyor line without needing to perform mounting and alignment work for the sensor system. Various pallet types are to run over the conveyor system, all of which need to be reliably detected. The high-frequency hall lighting should not affect the sensor. The sensors should repel dirt particles and the system must be low‑maintenance.
Solution:
The sensor system is mounted already at the manufacturer of the conveyor system in the inner area of the conveyor by means of a special holder equipped with an integrated front screen for deflecting dirt particles.
Different pallet types can be reliably detected in transverse and lengthwise transport.
The sensor features ambient light sensitivity even with high-frequency LED hall lighting.
Digression:
Sensor mounting in the inner area of the conveyor and pallet detection from below
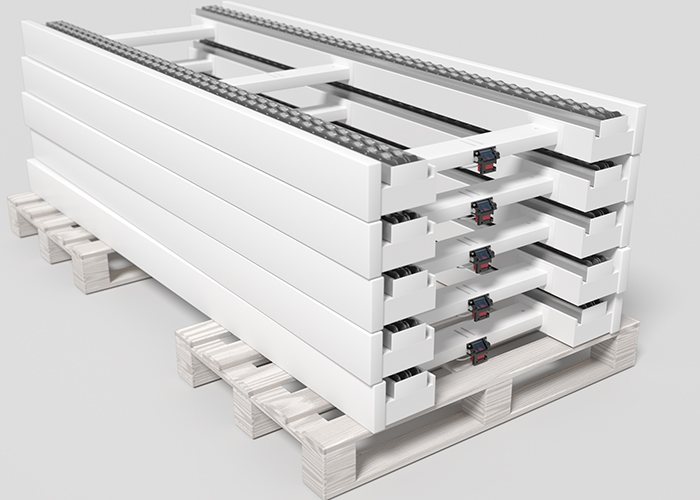
Advantage: Conveyors can be stacked
By mounting the sensors in the inner area of the conveyor, it can be stacked even with pre-mounted sensor and can be loaded and transported to the end customer problem-free.
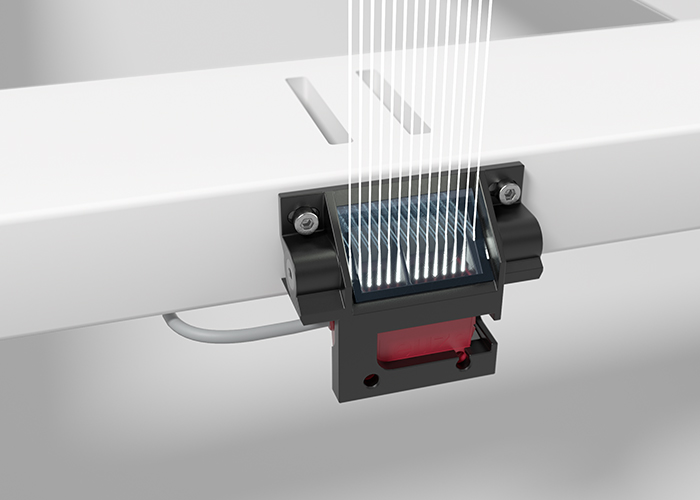
Challenge: Suppressing ambient light
Special ambient light configuration very efficiently suppresses ambient light sources (especially high-frequency LED lighting).
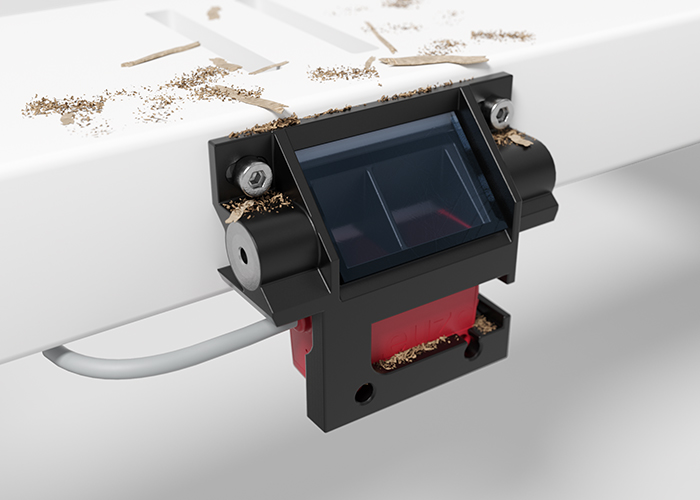
Clean solution: No soiling of the sensor
A 45° front screen in front of the sensor optics deflects dirt. The vibrations of the conveyor system cause particles to fall off automatically. Even larger dirt particles fall through the mounting bracket.
Technical properties
Â
 | Operating range | 1.3m |
Version | Optimized for ambient light | |
Setting | 300 mm fixed | |
Light source | LED, infrared 850 nm | |
Switching frequency | 250 Hz | |
Delivery | Various order sizes |
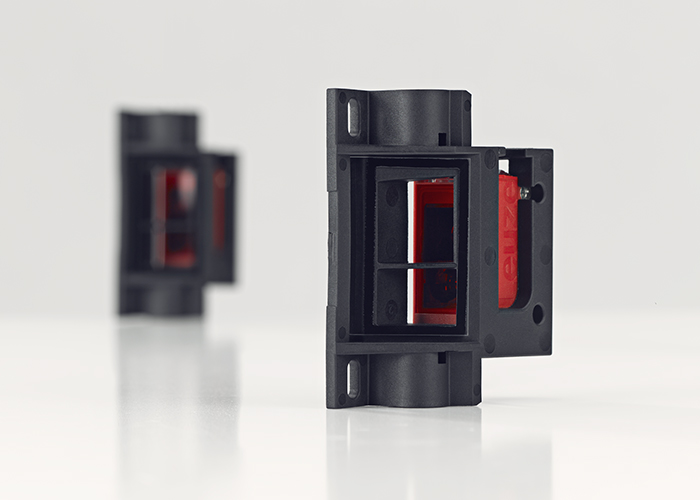