Camera-based compartment fine positioning
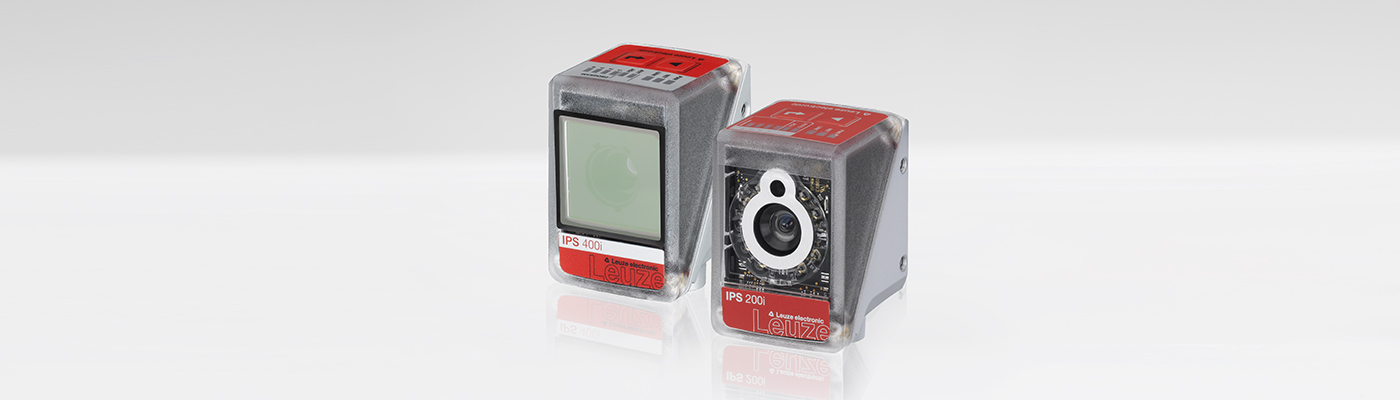
Camera-based compartment fine positioning
Stacker cranes – from rough to fine positioning
A camera-based positioning system with an evaluation algorithm tailored to the specific application provides a smart solution to compartment fine positioning. Solutions where the camera and evaluation unit are integrated in a compact system are particularly popular with users. These offer straightforward commissioning and operation, without the need for special knowledge.
With the IPS 200i / IPS 400i product family, Leuze offers the smallest camera-based sensor available on the market for the compartment fine positioning of stacker cranes. By means of an additional quality score, it helps to reduce downtimes of stacker cranes, thereby satisfying the call for condition monitoring. Tedious mounting, alignment, and readjustment during operation is no longer required, saving the customer valuable time
Download
You can find more information in white paper "Always in front of the right rack: Less downtime for compartment fine positioning with camera-based positioning sensors"
Advantages for you
- Flexible use on stacker cranes thanks to its small size
- Eliminates the need for multiple diffuse sensors with only an IPS 200i/400i
- Reduces downtimes through an innovative quality score
- Fast commissioning via the integrated web server or directly at the sensor via configuration codes
- Can be used in various temperature ranges
Highlights
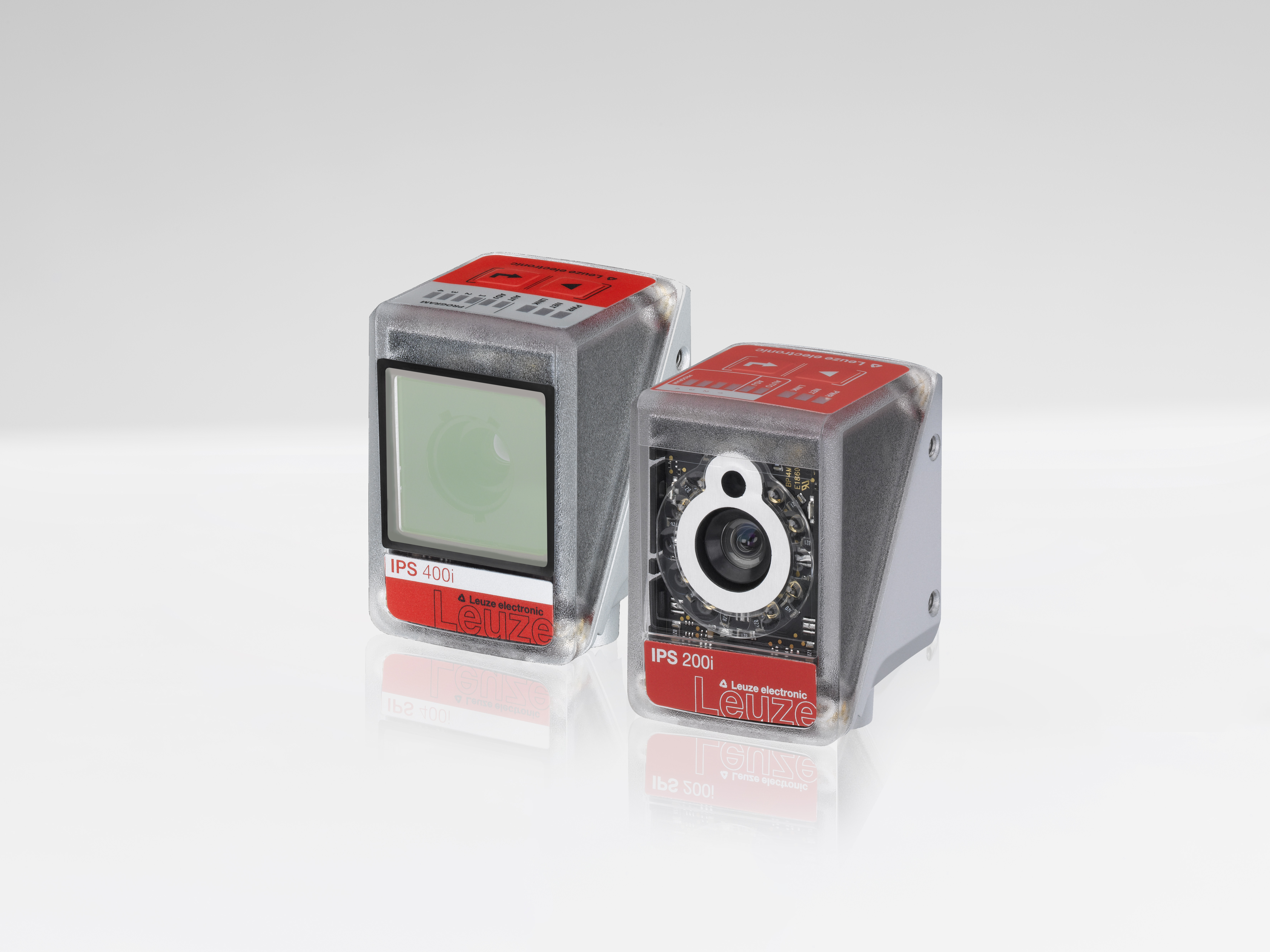
Highlights: IPS 200i / IPS 400i
These camera-based sensors are ideal for the compartment fine positioning of chassis (X-axis) and lifting unit (Y-axis) of the stacker crane in front of single- or double-depth shelf compartments. Any deviations from the target reference position that occur during absolute positioning are thereby detected. The reference position is defined by simple bore holes or reflectors (markers) in the steel profiles (crossbeams or columns) in the shelf compartments. If the marker is located in the working range of the sensor, it delivers the current position relative to the reference position via the integrated interface (Ethernet TCP/IP, EtherNet/IP, PROFINET) or via four digital switching outputs. When the current absolute and reference positions match, the ideal positioning of the stacker crane is reached.
IPS 200i
The IPS 200i is a camera-based sensor for the compartment fine positioning of a stacker crane with single compartment depth. With just one device model, a large working range from 100 to 600 mm can be achieved; the also available, heated version can be used at ambient temperatures as low as -30 °C. Its dimensions are unrivalled with respect to the small size. As a result, installation in constrained spaces poses no problem. Other highlights include the simple operation, the configuration via the integrated web server or directly on the sensor, the four alignment LEDs and the information about the function reserve, which is output as a quality score.
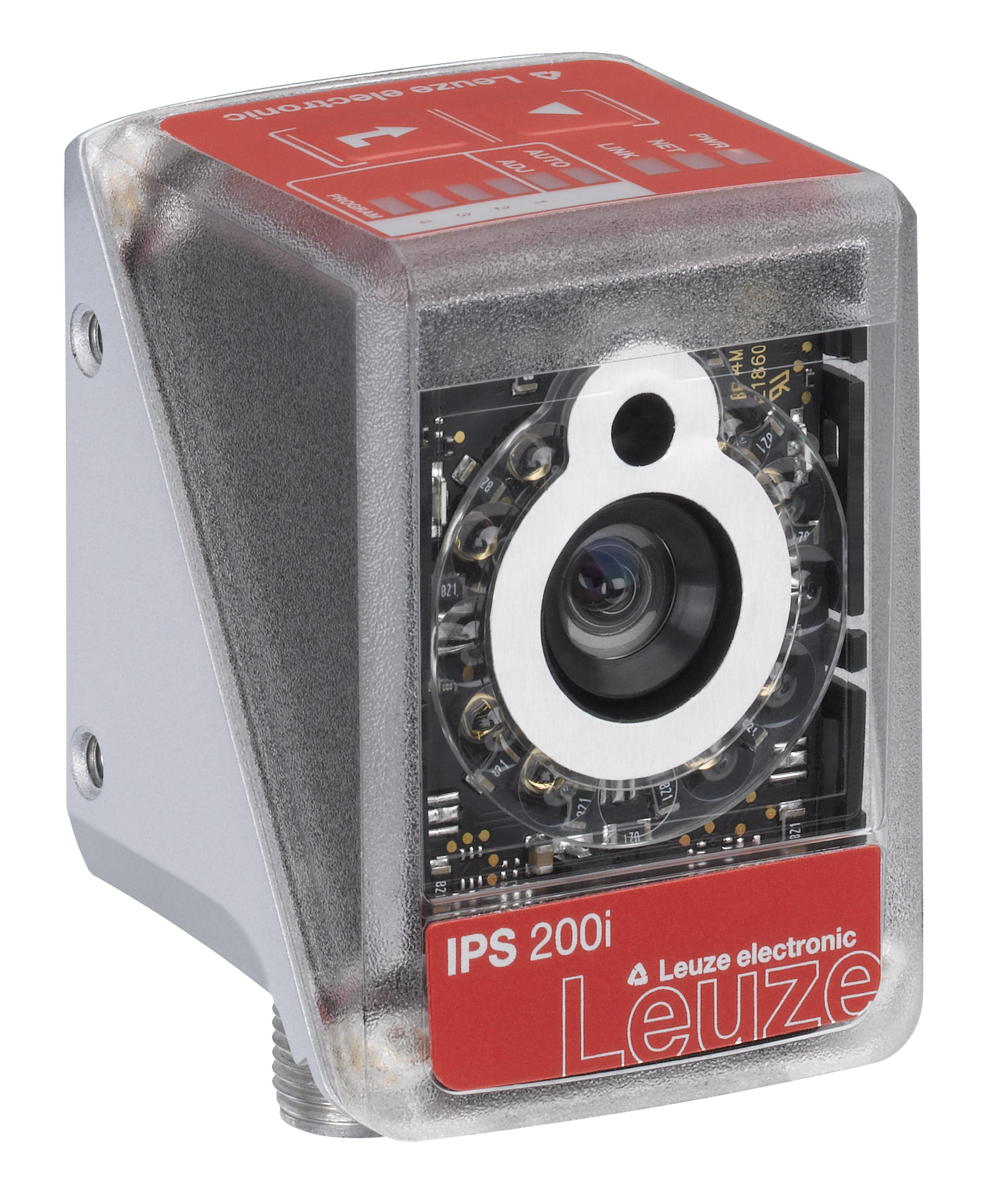
Application
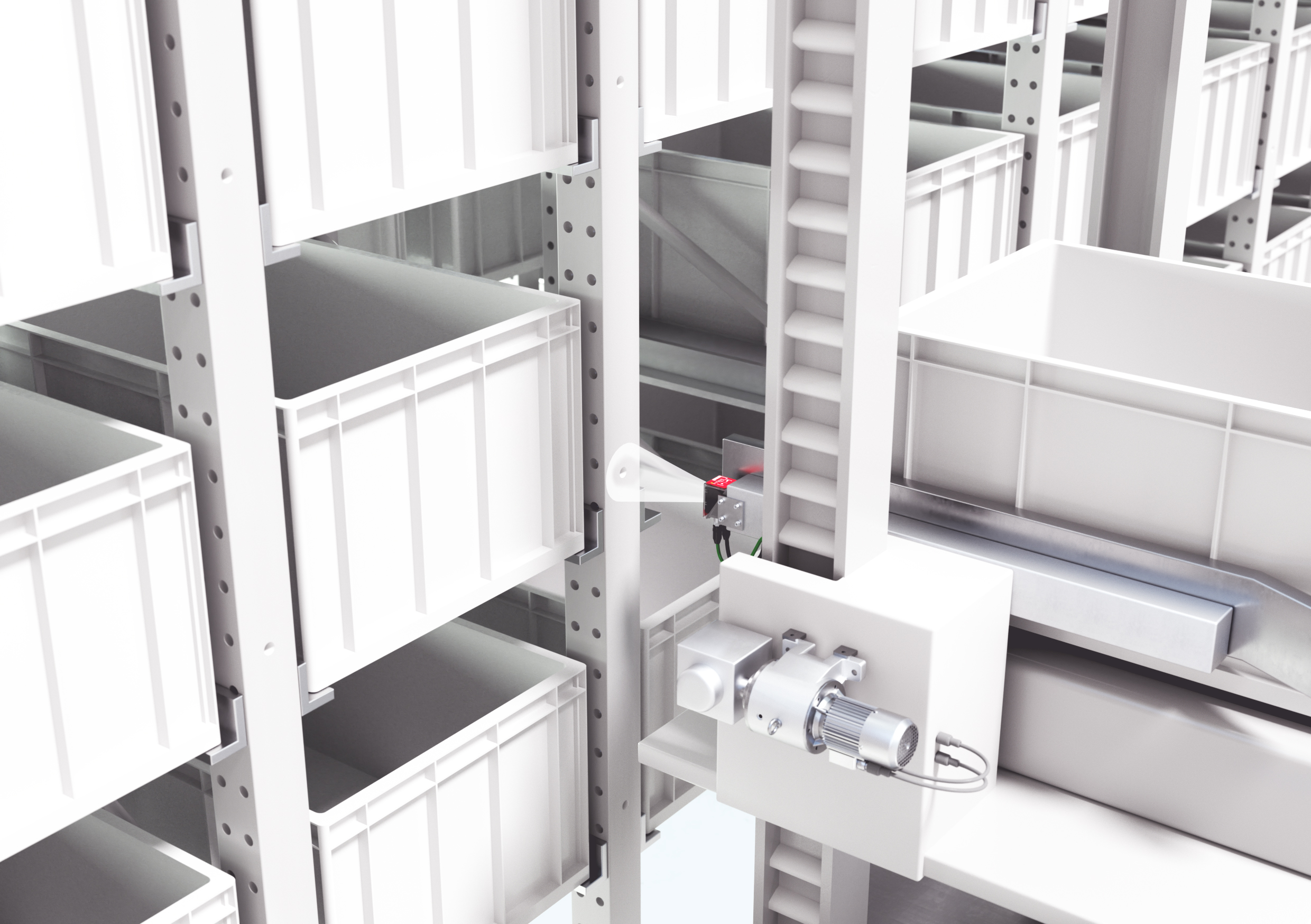
Compartment fine positioning on columns in container warehouse
Requirement: In an automated small-parts warehouse, containers, for example, should be stored and retrieved at high throughput rates. Constrained spaces and short distances call for innovative solutions for compartment fine positioning.
Solution: The IPS 200i reliably solves positioning tasks at distances of 100 mm to 600 mm on round markings in columns. Furthermore, it impresses with its large field of view and its various integrated industrial interfaces.
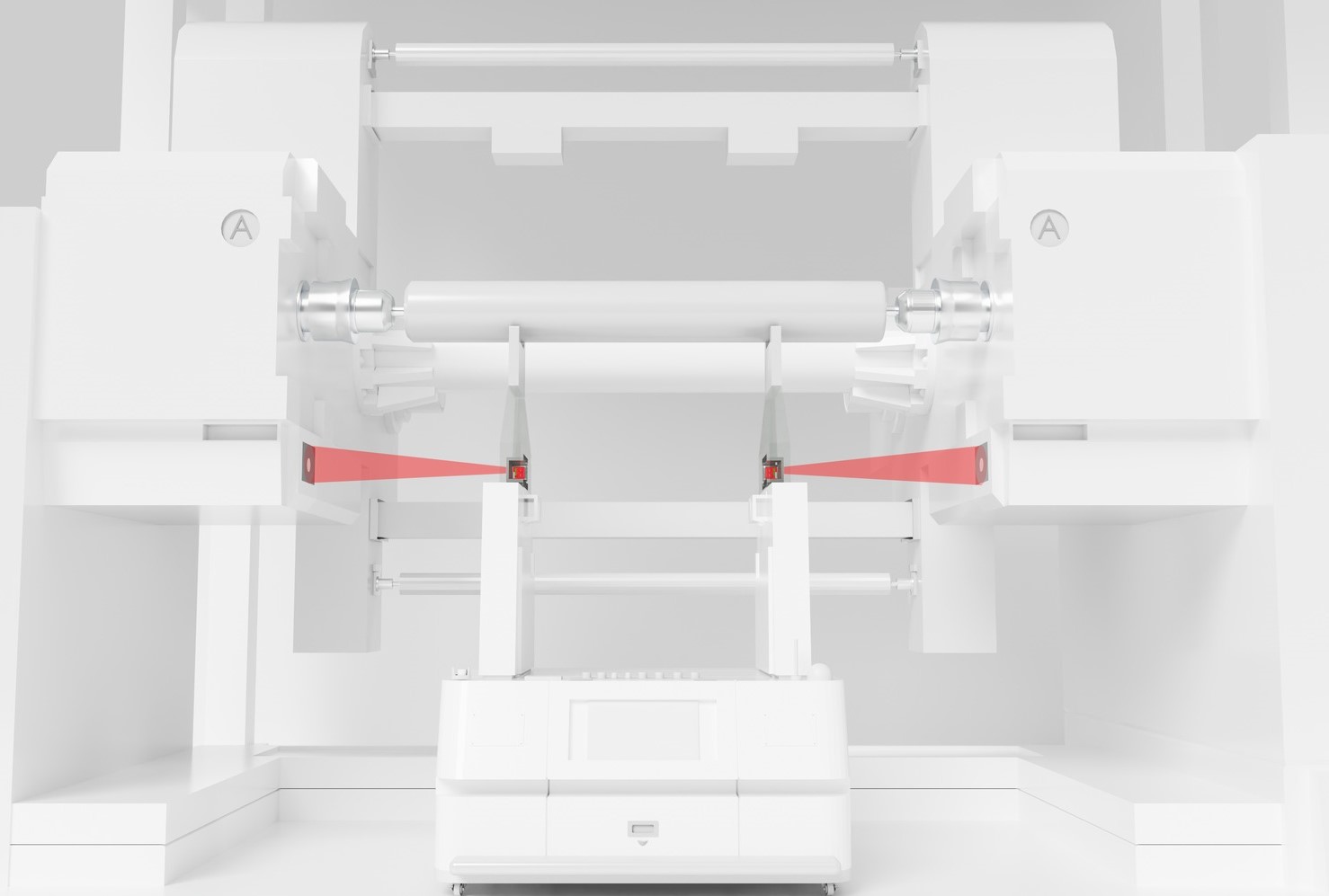
Fine positioning of automated guided vehicles (AGVs)
Requirement: Automated guided vehicles (AGVs) must be precisely positioned at various stations in order to transfer load carriers (boxes and workpiece holders). The position of the AGV must be determined by means of an optical system that ascertains the X/Y position between vehicle and transfer station.
Solution: The IPS 200i reliably solves positioning tasks, and its compact design and reproducibility of 0.1 mm make it ideally suited for this application.
IPS 400i
The IPS 400i is the smallest camera-based sensor on the market for the compartment fine positioning of a stacker crane with double-depth shelves. It helps stacker cranes to quickly and easily find the right rack.
Thanks to its high-performance, ambient-light-independent IR-LED illumination, fault-free use is possible for a working range of up to 2,400 mm. The also available heated version can be used at ambient temperatures as low as -30 °C. Its dimensions are unrivalled with respect to the small size. As a result, installation in constrained spaces poses no problem. Other highlights include the direct configuration on the device, the simple operation, four alignment LEDs and the information about the function reserve, which is output as a quality score. Critical applications with background reflections are solved using customized additional lighting.
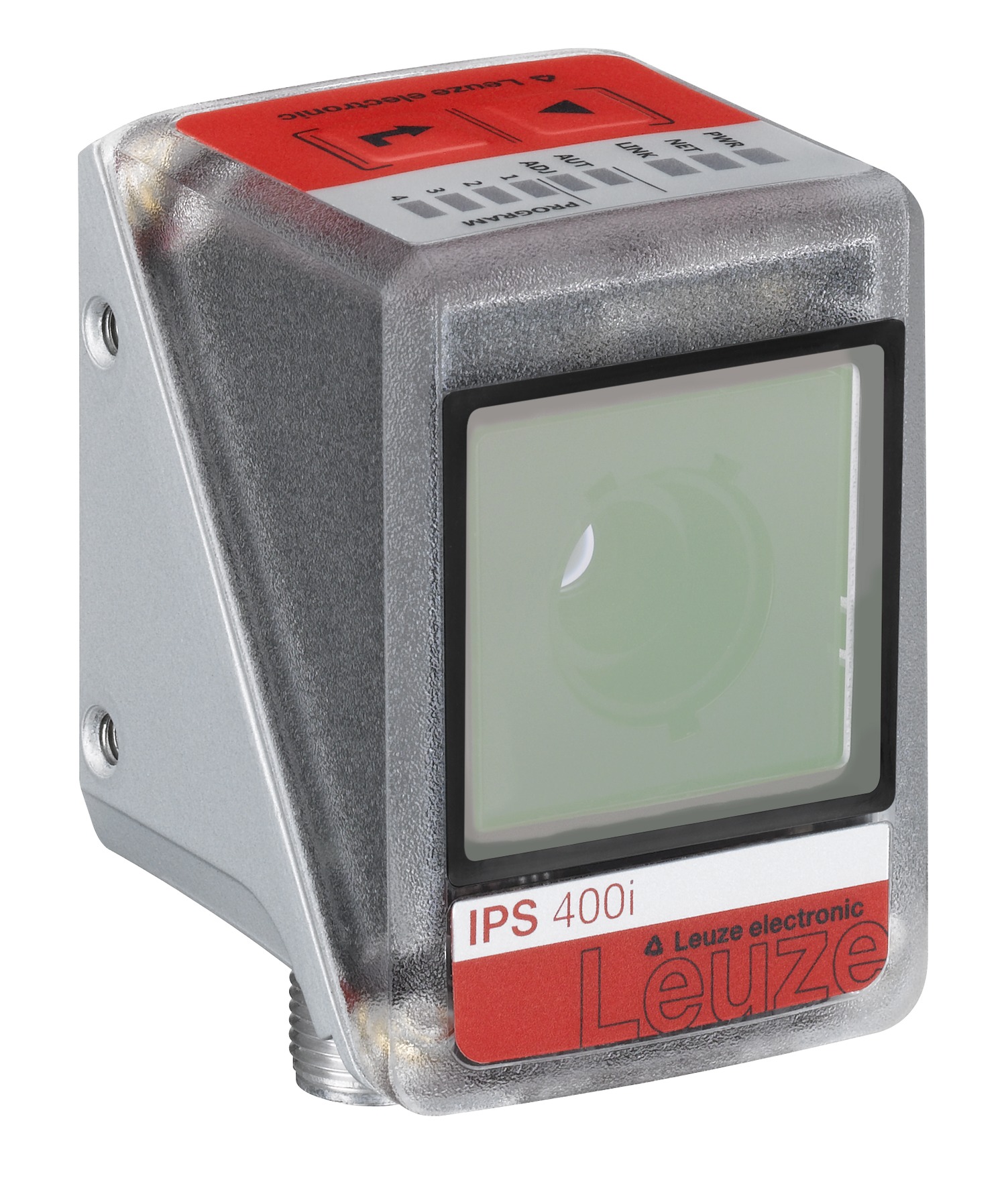
Application
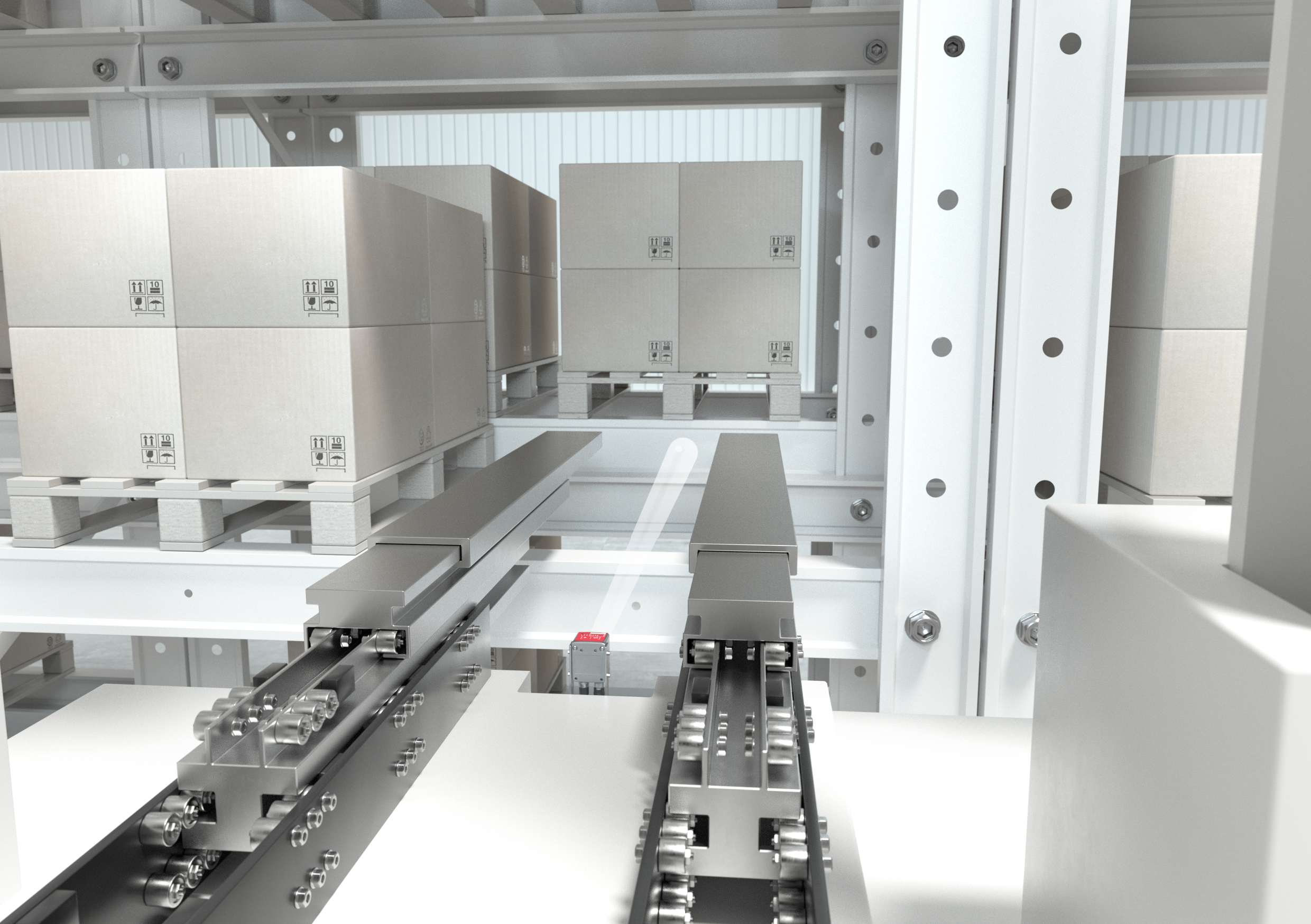
Compartment fine positioning on bar in double-depth pallet warehouse
Requirement: In a high-bay warehouse, after performing rough positioning and subsequent fine positioning of a stacker crane, the pallets should be stored and retrieved. Due to thermal and dynamic influences, fine positioning is required on the X and Y axes.
Solution: The IPS 400i reliably solves positioning tasks for single- and double-depth pallet warehouses with just one sensor. It scores with its compact design, its operating range of up to 2.4 m, and its powerful algorithm for round markings in bars.
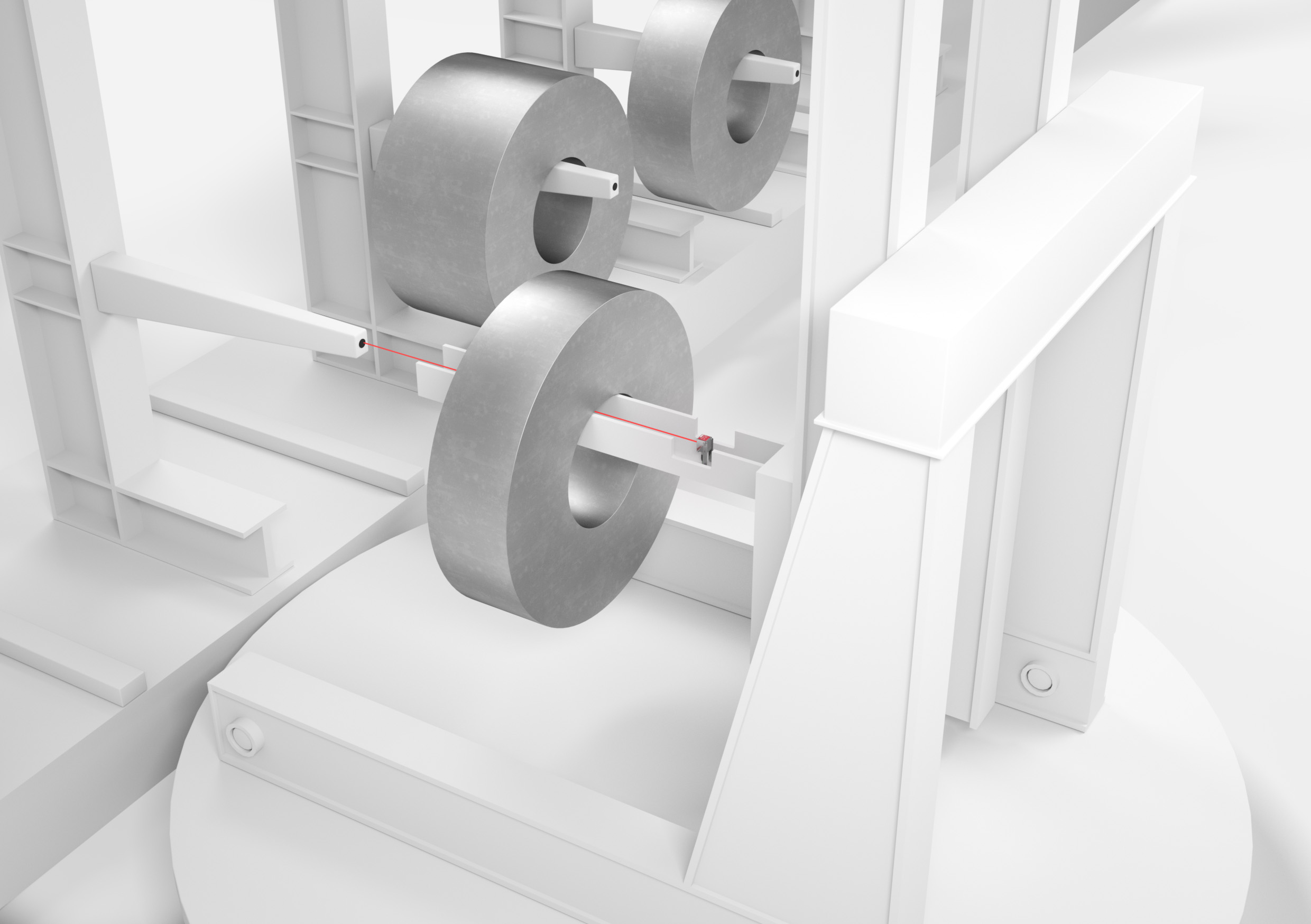
Fine positioning of stacker cranes in warehouse with cantilever racking
Requirement: In a warehouse with cantilever racking, coils or rolls must be stored and retrieved. Due to the heavy weights sometimes involved, fine positioning of the automated stacker crane is necessary.
Solution: The IPS 400i offers an operating range of up to 2.4 m and a powerful algorithm for round markings in cantilevers. Thus, this positioning task can be reliably solved with just one sensor.
Products in the overview
IPS 200i | IPS 400i | |
Description | Camera-based positioning sensor for round markings | Camera-based positioning sensor for round markings |
Area of application | Single compartment depth | Double compartment depth |
Reading distance | 100...600mm, marker dependent | 250...2,400mm, marker dependent |
Integrated interfaces | Ethernet TCP/IP, UDP; PROFINET IO/RT; EtherNet/IP | Ethernet TCP/IP, UDP; PROFINET IO/RT; EtherNet/IP |
Ambient temperature (operation) | 0…+50°C (with heating: -30…+50°C) | 0…+50°C (with heating: -30…+50°C) |
Dimension (W x H x L) | 43 x 61 x 44 mm | 43 x 61 x 44 mm |
Article list
- Application: Single compartment depth, Single compartment depth
- Series: IPS 200i
- Application: Double compartment depth, Double compartment depth
- Series: IPS 400i
- Special version: Heating, Heating
- Application: Double compartment depth, Double compartment depth
- Series: IPS 400i
- Application: Double compartment depth, Double compartment depth
- Series: IPS 400i
- Special version: Heating, Heating
- Application: Double compartment depth, Double compartment depth
- Series: IPS 400i
- Application: Single compartment depth, Single compartment depth
- Series: IPS 200i
- Special version: Heating, Heating
- Application: Single compartment depth, Single compartment depth
- Series: IPS 200i
- Application: Double compartment depth, Double compartment depth
- Series: IPS 400i
- Special version: Heating, Heating
- Application: Double compartment depth, Double compartment depth
- Series: IPS 400i
- Application: Double compartment depth, Double compartment depth
- Series: IPS 400i
- Special version: Heating, Heating
- Application: Double compartment depth, Double compartment depth
- Series: IPS 400i
- Application: Double compartment depth, Double compartment depth
- Series: IPS 400i
- Special version: Heating, Heating