Sensor solutions for continuous conveyors
Continuous conveyors ensure the continuous flow of goods. For reliable operation of the systems, the presence of pallets and containers must be detected, dimensions and fill levels controlled, and bar codes reliably read. This guarantees a seamless production process.
Our extensive sensor product range offers reliable and fast object detection. It also protects people and the system. Individually deployable reading principles, such as bar code, 2D-code, and RFID guarantee maximum flexibility. With their high performance reserve, our sensors offer reliable detection even with glossy, dark or stretch-wrapped packages, and rough environmental conditions. Thanks to the intelligent mounting technology, easy alignment and simple integration into existing systems via fieldbus interfaces such as PROFINET, our sensors can also be quickly put into service.
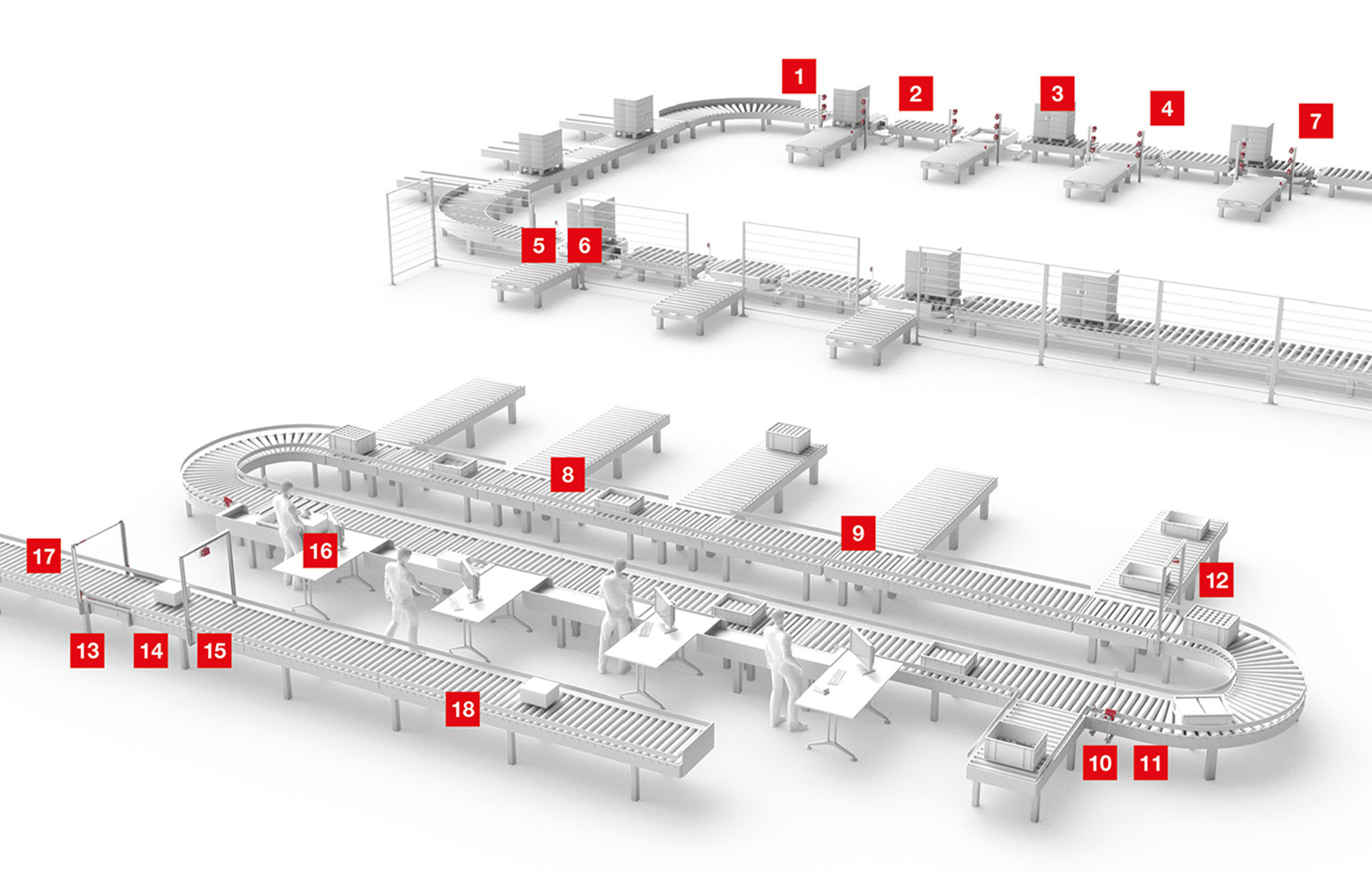