Processing Center
In machining centers, objects of various materials are machined, turned, and drilled. The prerequisite for processing work pieces in complex machining centers with a high degree of precision is having the right tool available for each work step. Industrial robots are often used for the automated loading and unloading of processing centers. Before the robot picks up a part, the part must be uniquely identified to ensure that the correct processing step is carried out. The robots perform numerous swivel and gripping movements in a very short period of time. The working ranges of the robots must be reliably safeguarded in terms of access by and the presence of persons.
Our inductive and optical sensors check and monitor the presence and position of work pieces and parts.
Our identification systems record data for the traceability of those work pieces and parts and for the next work step. And our safety sensors reliably monitor danger zones and safeguard points of operation.
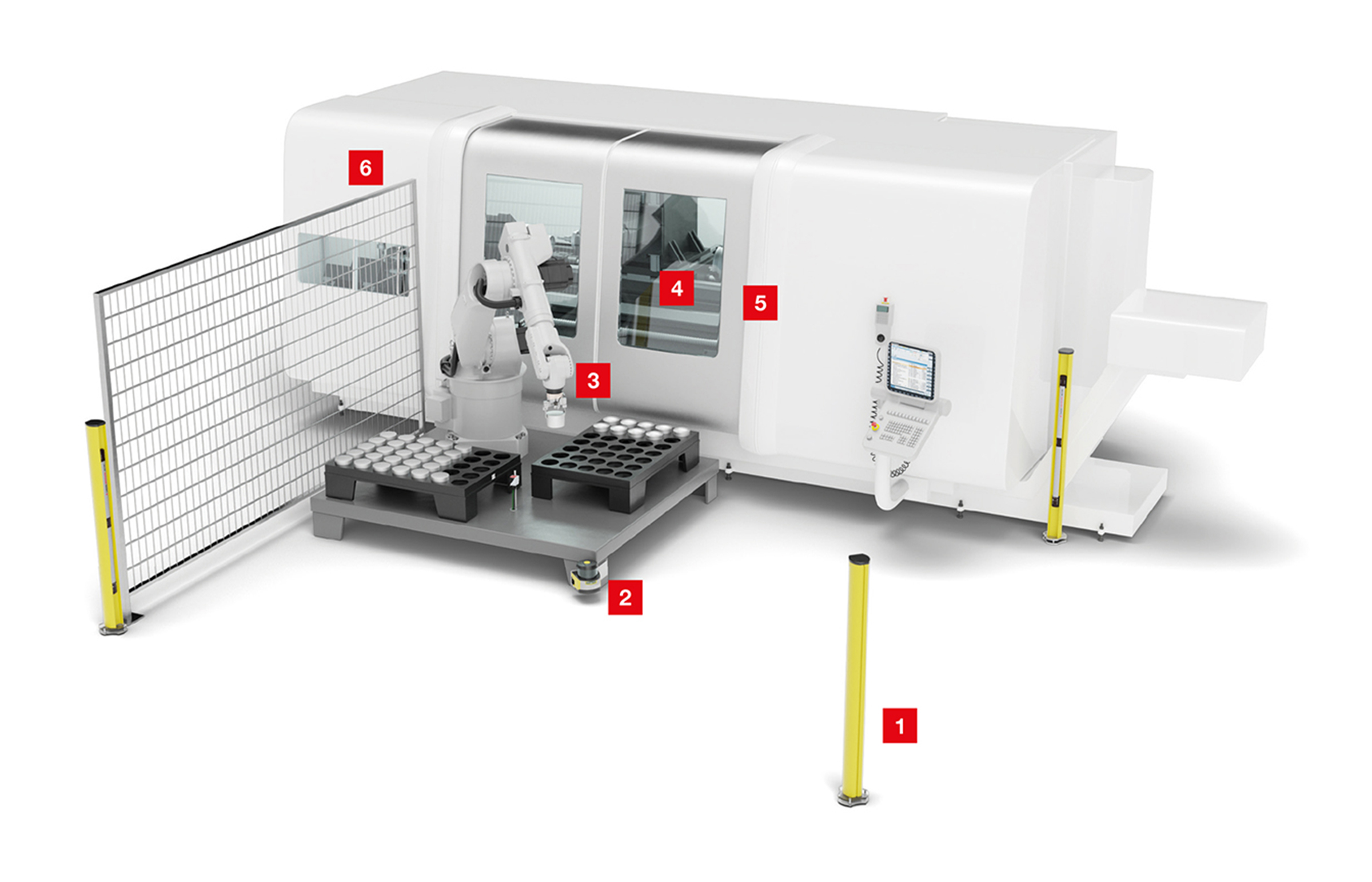