Sensor solutions for carton and container packaging
In secondary packaging, primary-packaged individual products are packed into cartons or grouped into packages to facilitate handling. Here our sensors have a wide range of applications: Before final packing takes place, it must be checked whether the contents in the respective packaging are complete, whether the packages are aligned correctly for transport or whether cartons have been sealed properly. In cartoning machines, correct filling of the outer packaging is detected, a stack height is measured or the position of stacks is detected and checked.
Switching and measuring light curtains can detect or measure objects in small resolutions across the entire conveyor width. The CML 730 measuring light curtains as PS variant have been specially developed for detecting objects inside packaging film. The CMS 700i modular volume measurement system, available as a complete system, determines the volume of shipping cartons during transport. By doing so, it assists the palletizer system further along the process in creating a correct layer pattern for the product stack on the pallet. The light-band sensor of the 46C series (VarOS) uses a 45 mm wide light-band to detect e.g. defective pallets or containers with openings such as mesh baskets on a conveyor.
1 Detection of objects with openings
2 Monitoring of package combination
5 Documentation of carton content
7 Position and presence control
8 Measurement of stack heights
10 Safeguarding of points of operation in machines
12 Detection of objects in film
15 Alignment monitoring of packages
16 Closure control of packaging
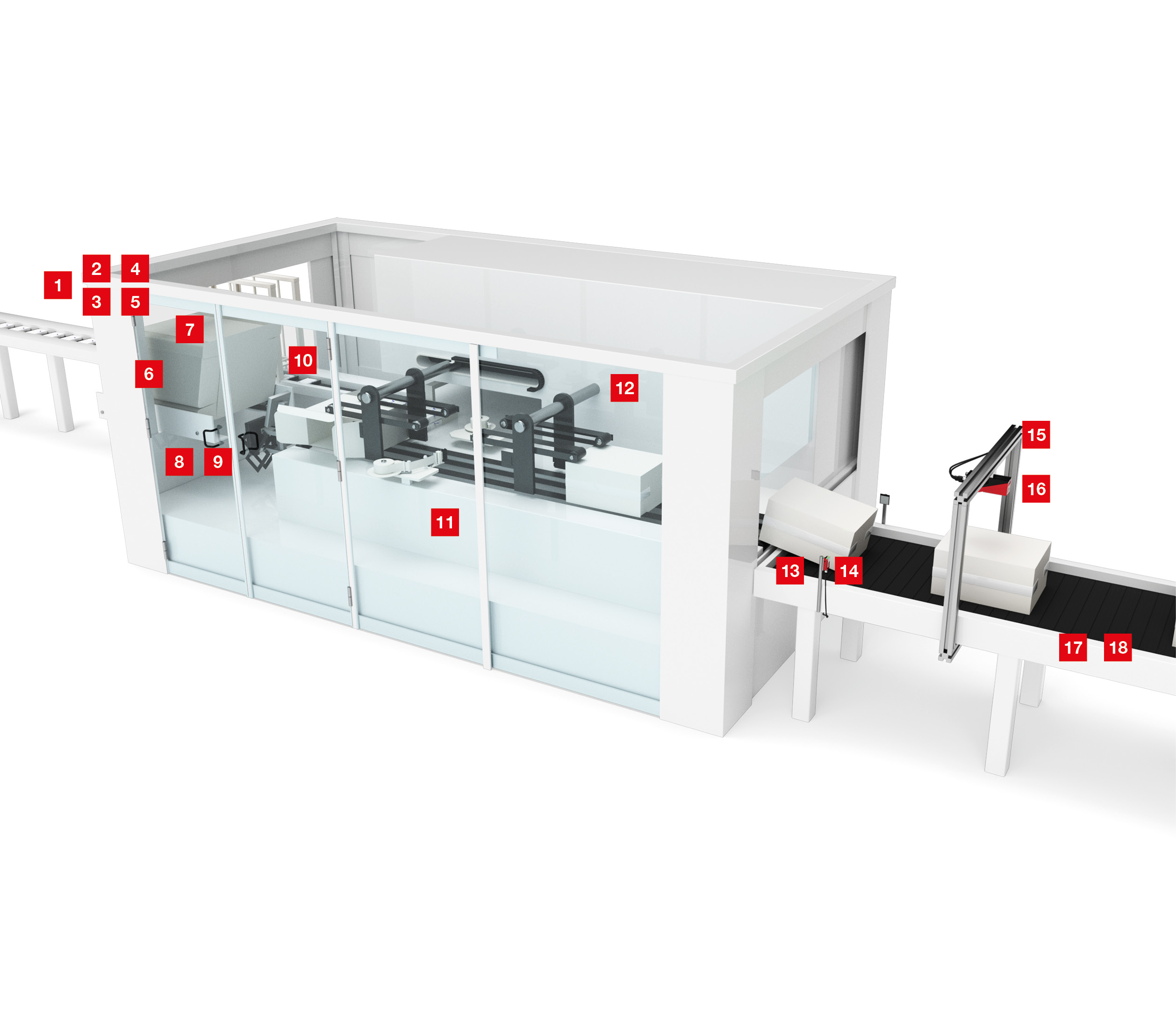
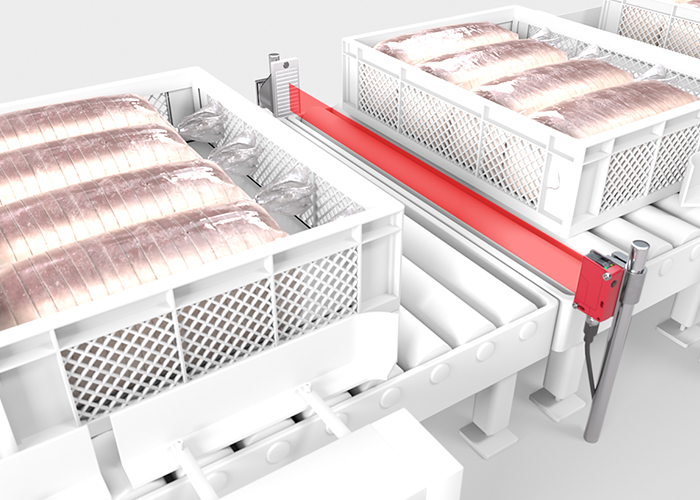
Requirement:
Food is transported in plastic baskets between individual process steps. Sensors with suitable light-spot geometry are required for reliable detection of the baskets. Small interruptions, different colors, surfaces or container heights must not impair detection.
Solution:
The RK46C.DXL VarOS light-band sensor reliably detects objects with a 45 mm wide light-band. Detection takes place at any point within the light-band. Irregular front edges or interrupted containers, e.g. baskets, are thereby reliably detected. Standard reflectors can be used on the opposite side.
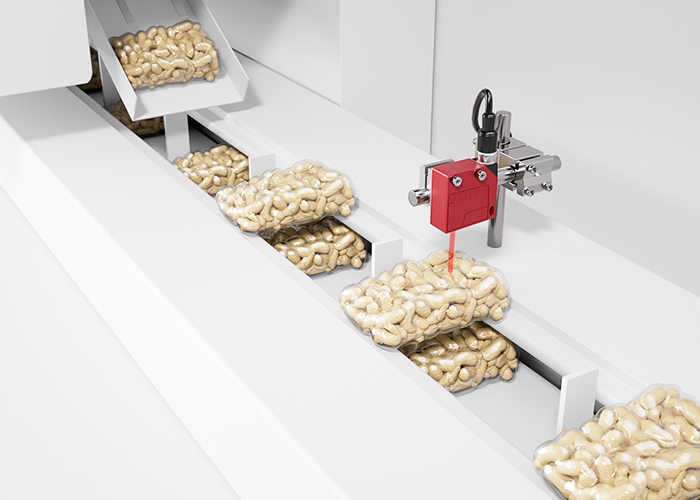
Requirement:
Several objects are to be combined and packed together in a secondary packaging. To prevent missing parts in the packages, the presence of the objects is to be checked.
Solution:
The ODS 9 measuring sensor provides distance values of objects on stacked tracks to the machine. With an evaluation on a difference range, objects that belong together can be detected.
03 Checking of content
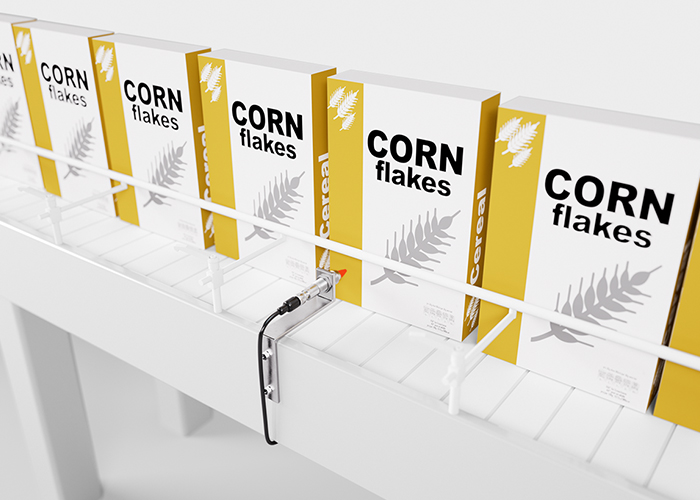
Requirement:
It should be checked whether the carton has been filled as intended. In the case of opaque packaging, this is an extremely challenging task for which capacitive sensors are well suited.
Solution:
The LCS capacitive sensors check for content through the carton during single-lane transport. The cylindrical design of the sensors allows for space-saving integration.
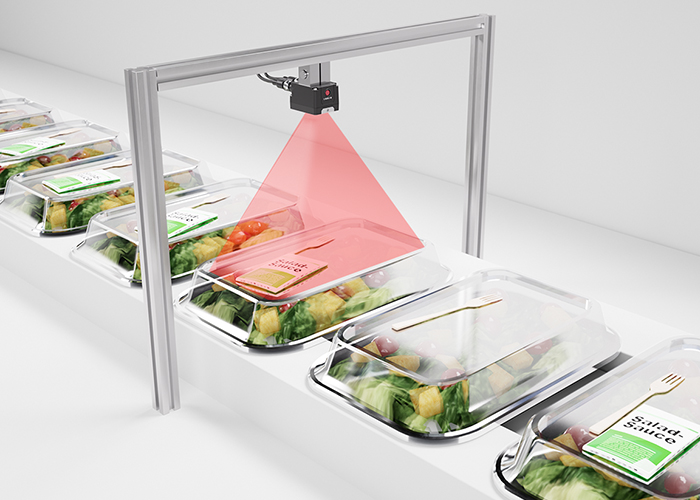
Requirement:
In the feed of a sealing machine, the completeness and the presence of several products is to be detected. Incomplete packages are to be discharged.
Solution:
The IVS 108 Simple Vision sensor detects missing products via reference images or/and via pattern matching. With integrated software tools, the sensor can be easily and quickly adapted to different inspection tasks.
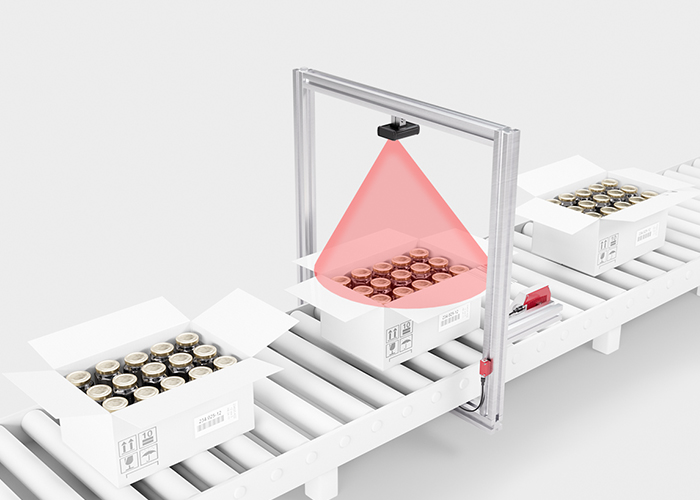
Requirement:
Before a shipping carton is sealed, the content should be documented for tracking purposes. For this purpose, an image of the content is to be recorded and saved.
Solution:
The LCAM 308 industrial webcam records a single color image via external activation. In this way, the carton content can be documented and transmitted to a higher-level control via the Ethernet interface. Settings can be made via the integrated web browser.
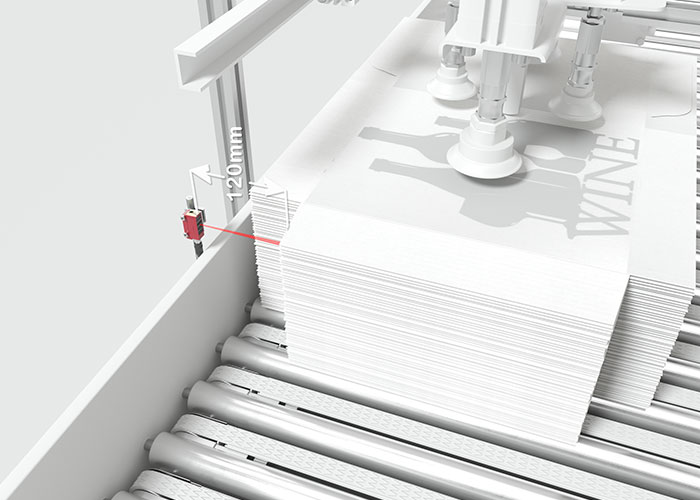
Requirement:
The pre-cut cartons prepared on a stack must be automatically removed from the stack, separated and then provided for the gluing and folding process. To ensure optimum performance of the downstream process steps, the carton stack must be positioned at a specific point on the conveyor belt.
Solution:
The compact ODT 3C measuring sensor checks the presence of the carton stack with the switching sensor function. The exact position of the stack can be output with the measuring sensor function via the IO-Link interface.
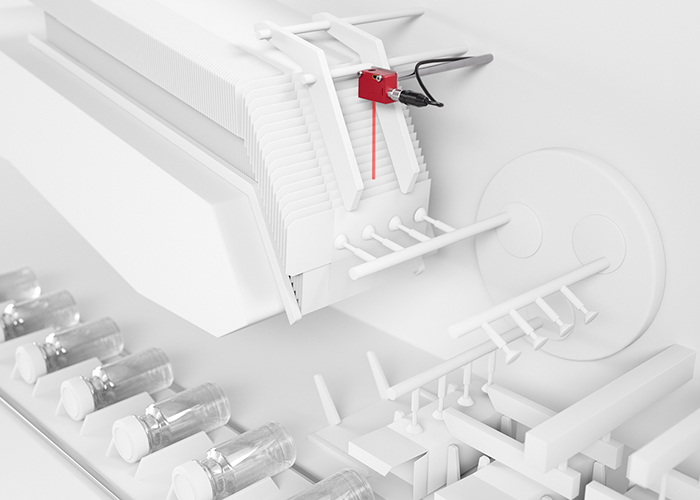
Requirement:
In a cartoning machine, the fill level of the folding box magazine is to be detected. Detection should be independent of color and surface as much as possible.
Solution:
The precisely adjustable HT 3C diffuse sensor with background suppression or HT 25C with visible light spot are suitable for position and presence control. There are models with different light-spot geometries. A format changeover with distance changes is possible with the HT 3C.3 via the IO-Link interface.

Requirement:
Primary packaging is stacked in the magazine of a packaging machine. To ensure that the stack contains the correct quantity, its height must be monitored. This requires sensors with high resolution and accuracy as well as a precise and easy-to-position light spot.
Solution:
The ODS 9 measuring sensors with staggered operating ranges and laser class 1 can be used easily and flexibly for measuring stack heights. The distance value is output as an analog current or voltage signal. The IO-Link interface ensures fast integration as well as additional parameterization options.
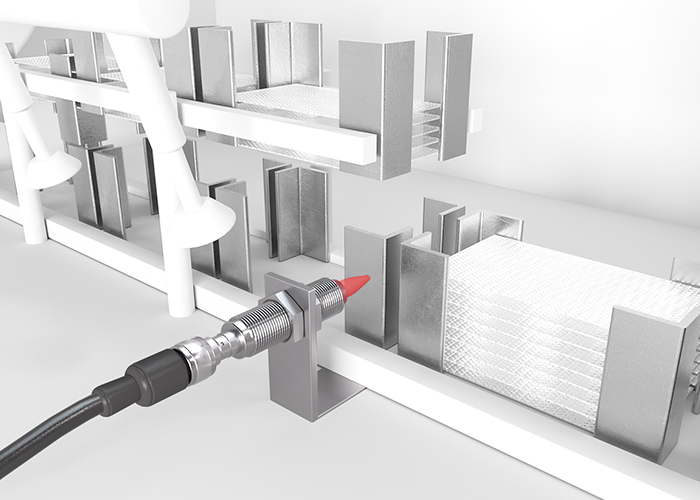
Requirement:
Primary packaging is often stacked and fed in magazines. The position of these magazines or feeder fingers are to be detected in order to prevent collisions and to control the feed.
Solution:
Inductive sensors detect the metal structures of the magazines reliably and precisely. With their small design and defined switching distances, sensors of models IS 288 or IS 208 are particularly well suited for this application.
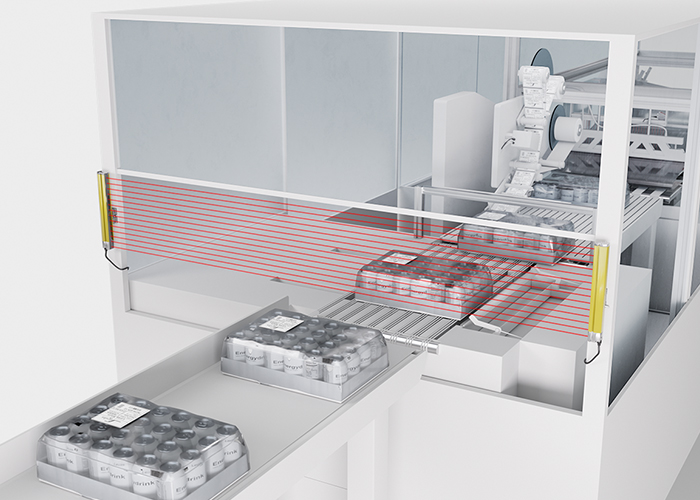
Requirement:
On packaging machines, openings are required at the machine infeed and outfeed. To prevent access to dangerous movements within the machine, the openings must be safeguarded mechanically or with optical safety sensors.
Solution:
The ELC 100 and MLC 500 safety light curtains with their wide selection of protective field lengths and resolutions offer the right solution for safeguarding points of operation. Here, the ELC 100 devices focus on a cost-efficient machine design. The extensive MLC 500 series is also suitable for special application cases.
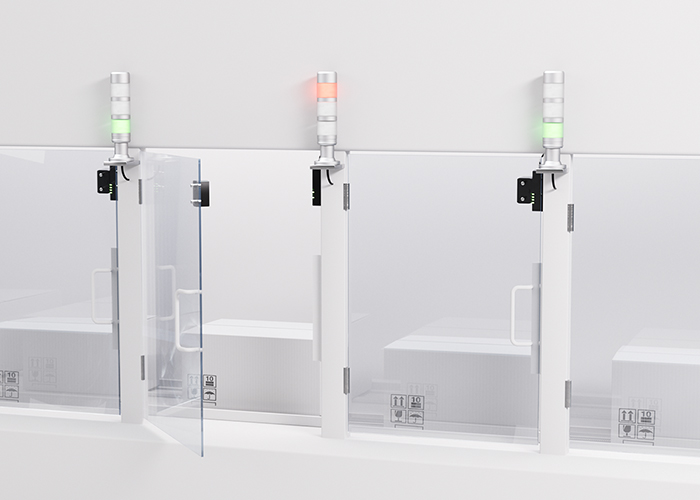
Requirement:
For access to individual machine areas, machines are equipped with doors and flaps, e.g. to allow magazines to be changed or areas to be cleaned. While the machine is in operation, these doors and flaps must remain closed and monitored for safety-related reasons.
Solution:
The RD 800 safety proximity sensors monitor doors and flaps and with their RFID-coded actuators provide maximum protection against tampering. Thanks to degree of protection IP 69K and an operating temperature up to 70 °C, the devices can be used for a wide variety of applications. OSSD outputs and performance level PL e ensure easy integration.
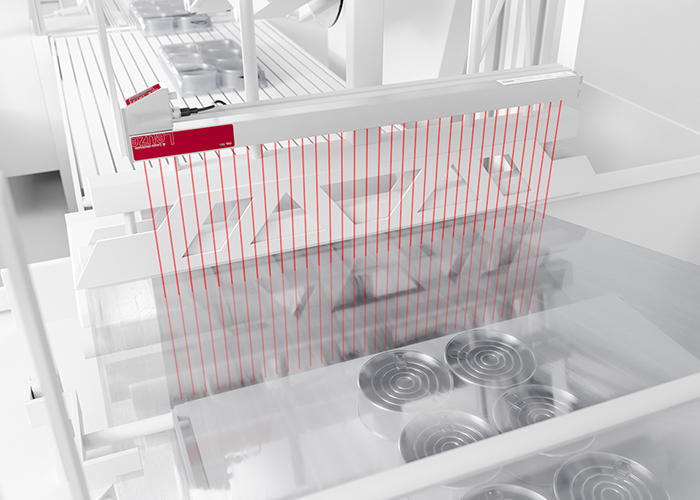
Requirement:
Objects are to be detected in a packaging film to avoid collision with the weld bar. The objects to be packed can have any shape.
Solution:
The CML 730PS measuring light curtains are developed for the detection of objects in film. With the aid of the power setting, different packaging films can be transilluminated in one or more layers and the products inside can be detected.
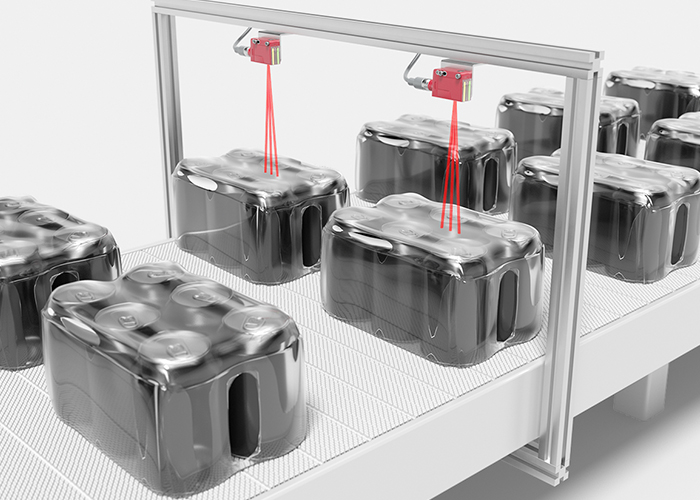
Requirement:
If bottles and cans are shrink-wrapped into packages using film, they must also be detected on multitrack conveyors. Different types of packages with transparent film or different film printing are to be reliably detected.
Solution:
The DRT25C.R unit pack sensor uses the surface of the conveyor belt as a reference. As a result, it reliably detects the complete range of package types. Therefore, no adaptations to the sensor are necessary when changing products.
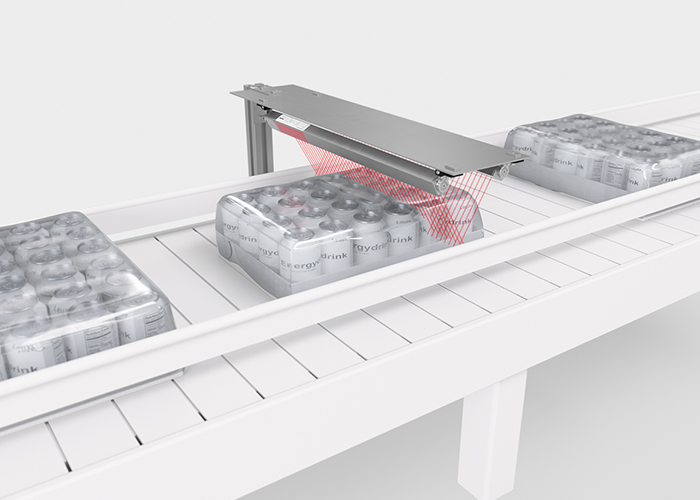
Requirement:
If different package widths are transported on a conveyor system, the alignment of the packages must be checked before palletizing. The sensor system used for this purpose must reliably detect the entire width of the packages and all variants occurring.
Solution:
The CML 730i measuring light curtain in V-arrangement allows the width and completeness of packages to be evaluated from above. For this purpose, emitted light beams are reflected by the object onto the receiver. Various beam spacings and measurement lengths are available.
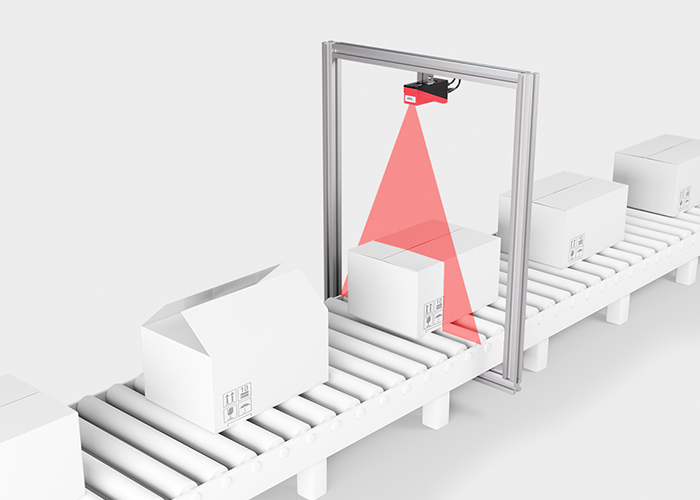
Requirement:
After filling, the shipping cartons are automatically sealed. A testing device is to be used to detect whether the flaps are closed and glued.
Solution:
The LRS 36 laser profile sensor can correctly detect closed cartons using a reference contour. Different reference contours can be saved in the sensor and selected via a digital interface. Due to the high accuracy of measurement, even small deviations can be detected.
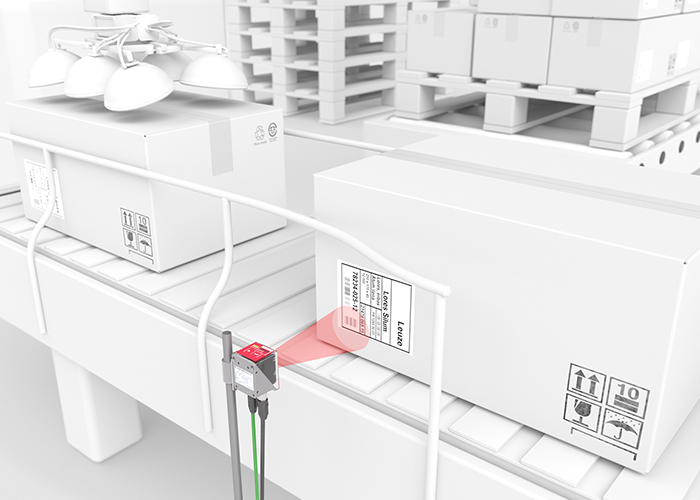
Requirement:
After filling and sealing the shipping carton, a label is attached. The printed code must be checked for readability and correctness.
Solution:
The DCR 200i code reader can decode both bar codes and 2D-codes independently of their alignment, making it a very flexible solution. The code content is output via the integrated Ethernet interface.
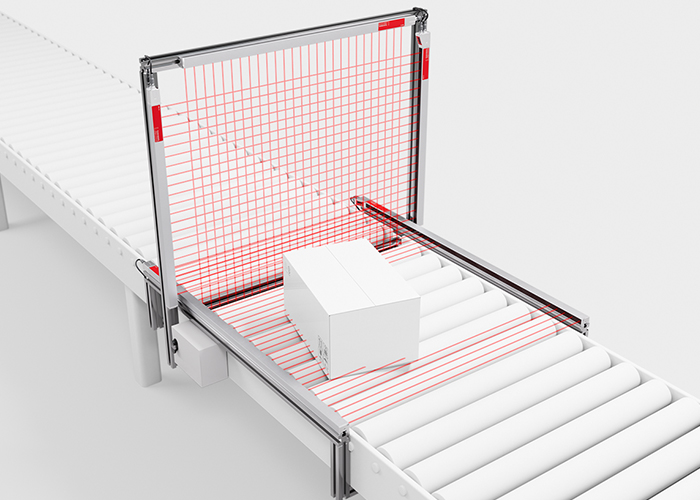
Requirement:
In order to correctly allocate shipping cartons, the volume is to be determined. For this purpose, the dimension of the shipping cartons passing through must be measured in all three dimensions.
Solution:
As objects pass through, the CMS 700i contour measurement system determines their height, width, length, orientation angle and position relative to the edge of the conveyor. The complete system contains all components required for installation and operation. Communication is Ethernet-based via PROFINET and TCP/IP.