Production cell
The factory of the future is characterized by flexible production cells. From individual production cells to a fully networked production system of a smart factory. What all have in common are the automated and linked processes in and between the cells. This improves productivity, allows for a more efficient use of materials and enables higher product quality.
With our sensor solutions, processes run efficiently: from material flow, in which the presence of work pieces or parts is detected, to information flow via intelligent sensors, whose data is captured and analyzed with the help of new communication technologies across all levels of a production system. The applications and possibilities here are as diverse as our product range tailored to them. Our inductive and optical sensors check and monitor the presence and position of work pieces and parts. Our identification systems record data for the traceability of those work pieces and parts and for the next work step. Our safety solutions reliably and flexibly safeguard hazardous areas.
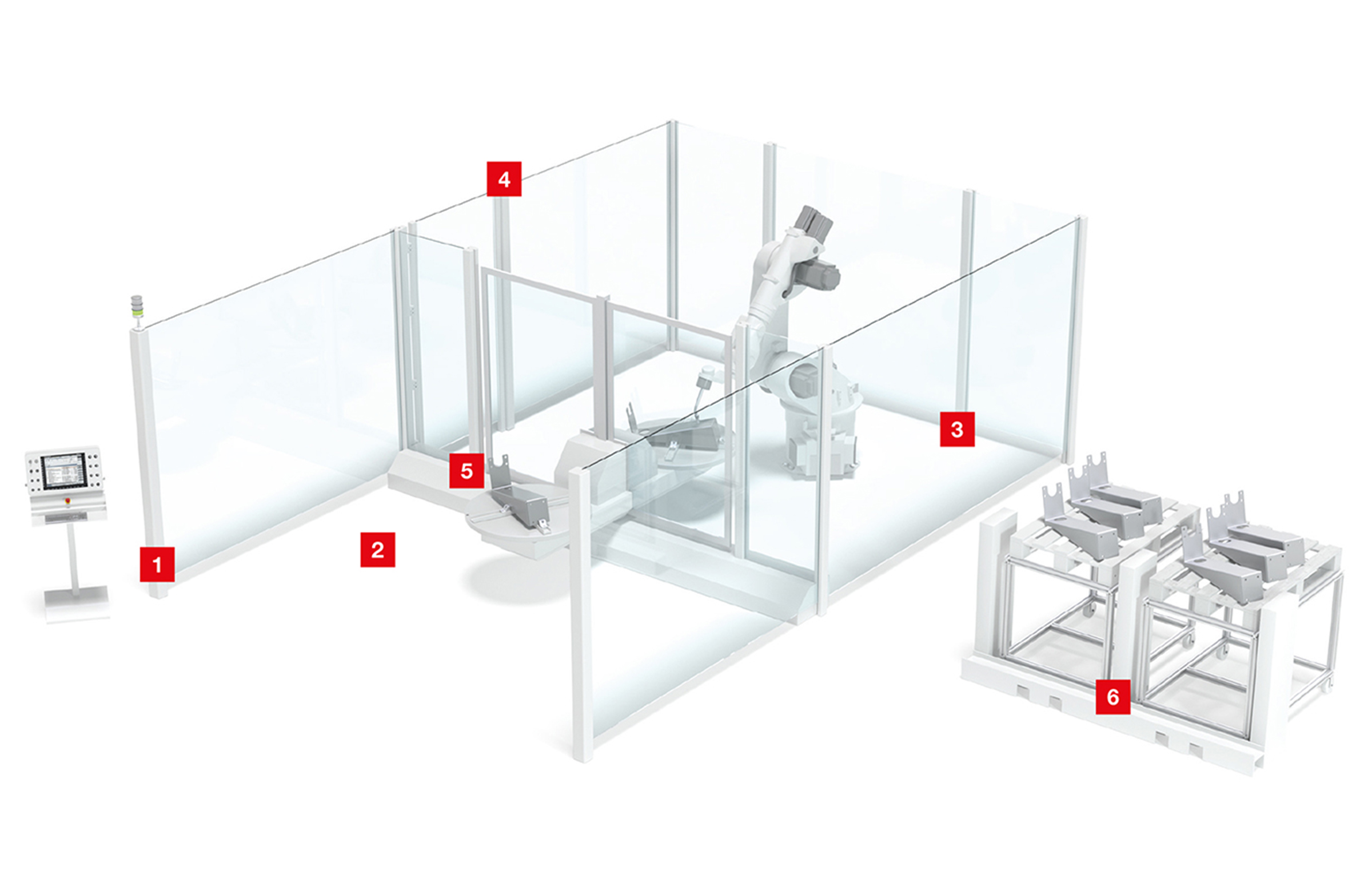