Storage system with stacker crane
Flexible storage systems make a significant contribution to the automation of production processes. In high-bay warehouses, the performance of the stacker cranes is especially important. They perform the automatic storage and retrieval of materials such as sheet metal plates and long goods. Their speed and reliability are, thus, decisive for the overall performance and availability of the systems.
Our sensor solutions enable optimum operation of the stacker cranes. They capture position data in the travel/lifting area and optically transmit travel commands and position data to the control. In addition, our sensors perform the compartment occupation check and prevent material from being pushed through. Reliable operation and high availability of the system are thereby ensured.
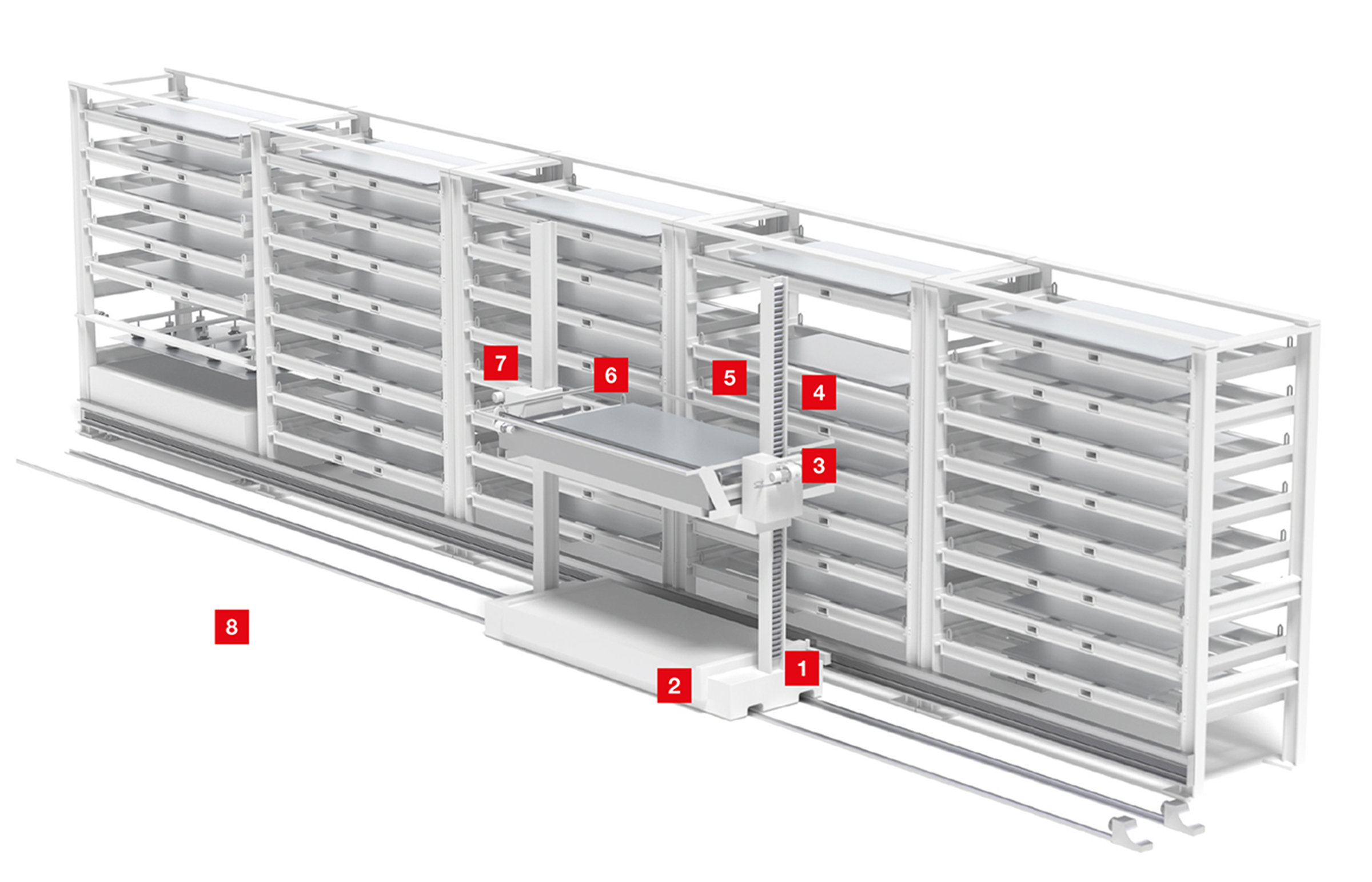