Laser positioning systems
Advantages for you
- Solution of positioning tasks up to 120 m in intralogistics: Applications on stacker cranes, automated guided vehicles (AGV) and lift systems
- Outstanding integration in tight installation spaces: Most compact design (105 x 68 x 75 mm) with the smallest dead zone (100 mm) of any positioning sensor currently available on the market.
- Maximum constructional freedom: Easy implementation even in innovative applications with low space availability as well as in mobile and increasingly compact vehicles. Flat housing surfaces without interfering contours.
- Implementation of positioning applications extremely close to the sensor: With a minimal measurement range of up to 100 mm – even just a few millimeters if a deflecting mirror is used – the available space is utilized efficiently
- No minimum distances to the optical data transceiver thanks to zero interference: There is no interference between the AMS positioning sensor and the DDLS optical data transceiver, ensuring maximum freedom in terms of design and installation
- Matching performance for your application: Select the ideal option from our product range featuring two device models (AMS 100i and AMS 300i)
- Cost optimization: The AMS 100i offers you an attractive price/performance ratio
- Flexible mounting: Modular installation possibilities and mounting options as well as easy alignment ensure that the device can be installed flexibly and quickly
- Operation also at low temperatures and in hot environments: A model with integrated device and window heating enables operation from -30°C, for low-temperature applications, up to +60°C
Highlights
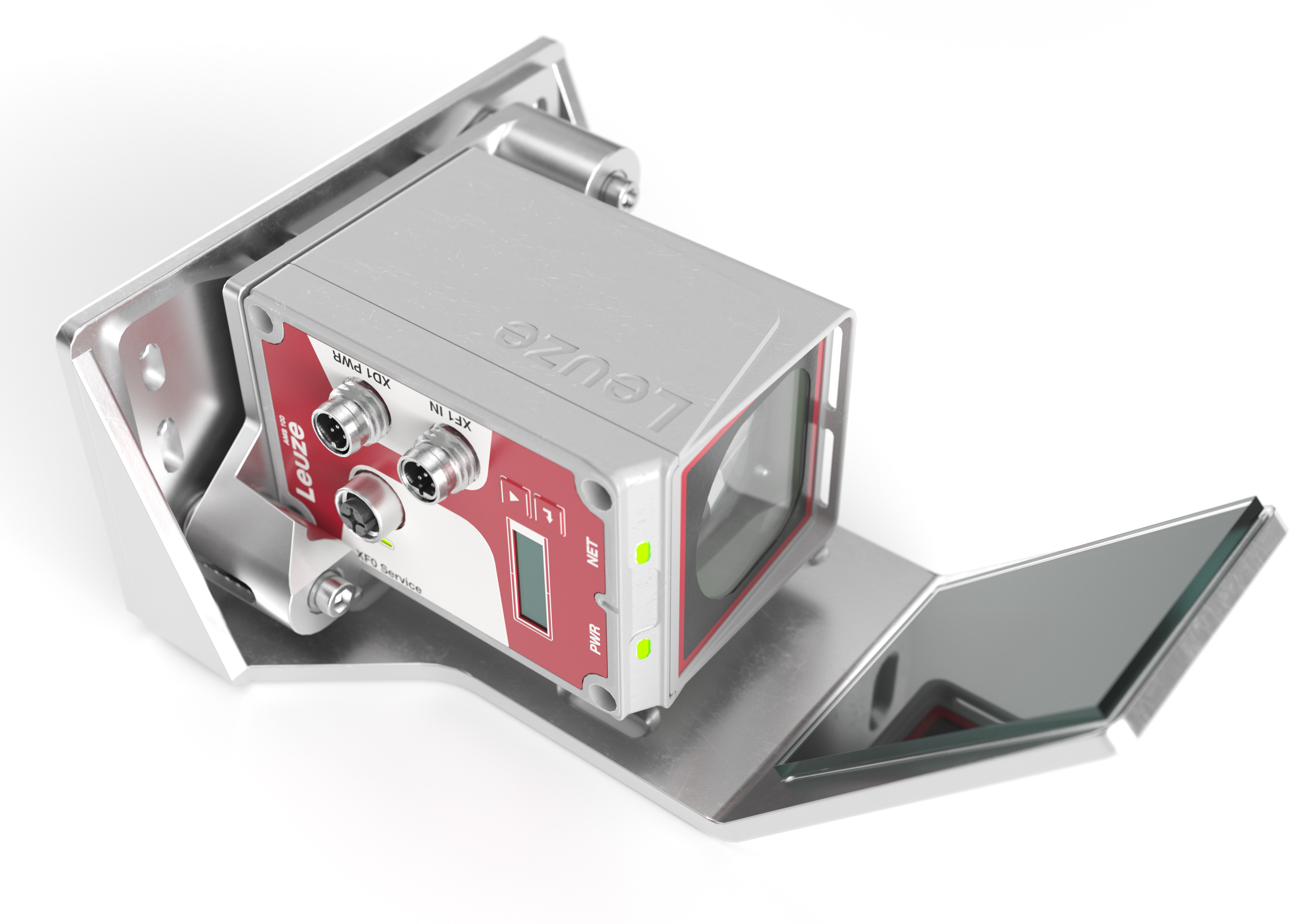
Most compact design with smallest dead zone on the market
Measuring 105 x 68 x 75 mm and with a dead zone of just 100 mm, the new AMS 100i positioning sensor is the most compact device on the market. This provides design engineers with maximum constructional freedom: The AMS 100i can be implemented without problem in innovative applications in confined spaces as well as in mobile and increasingly compact vehicles.
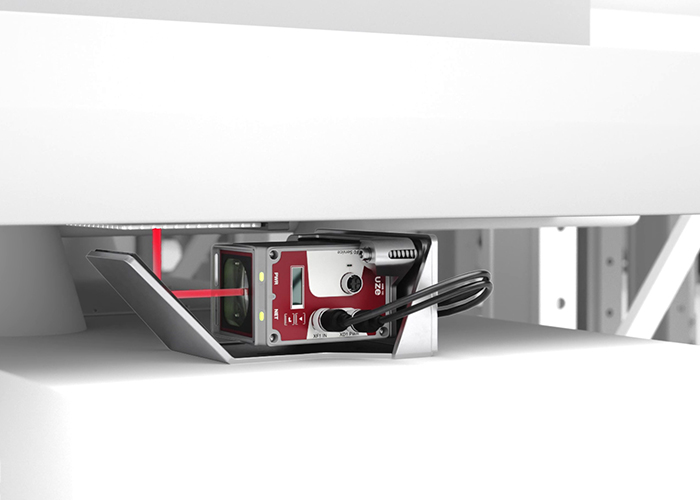
Positioning possible up to a close range of 100 mm
The minimal measurement range of up to 100 mm – even just a few millimeters if a deflecting mirror is used – enables an extremely high level of constructional freedom. As a result, it is possible to implement a positioning application extremely close to the sensor. This ensures that the available space is utilized efficiently.
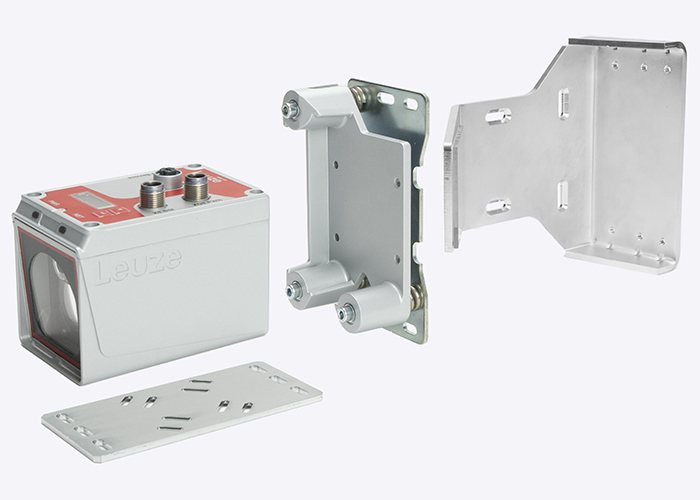
Modular installation options and easy alignment
The AMS 100i is available with and without an alignment device. Other mounting options such as a deflecting mirror and two brackets for mounting on the underside are also available. The modular design of these installation options means that the AMS 100i can be adapted individually to various applications.
The visible laser light makes it extremely easy to align the defined light spot on the opposing reflector. This is done using two hexagon socket screws.
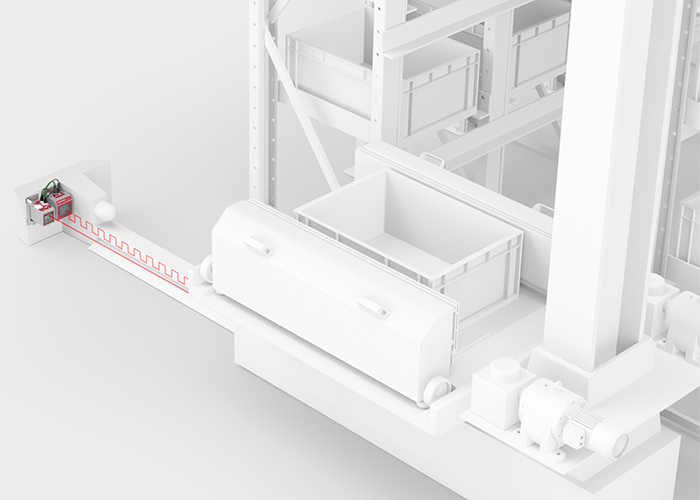
Interference-free directly next to an optical data transceiver
The AMS 100i can be mounted directly next to the DDLS 500i optical data transceiver without the devices being affected. Both systems thus remain free from interference. This means that the AMS 100i and DDLS 500i can also be used in constrained installation spaces.
Applications
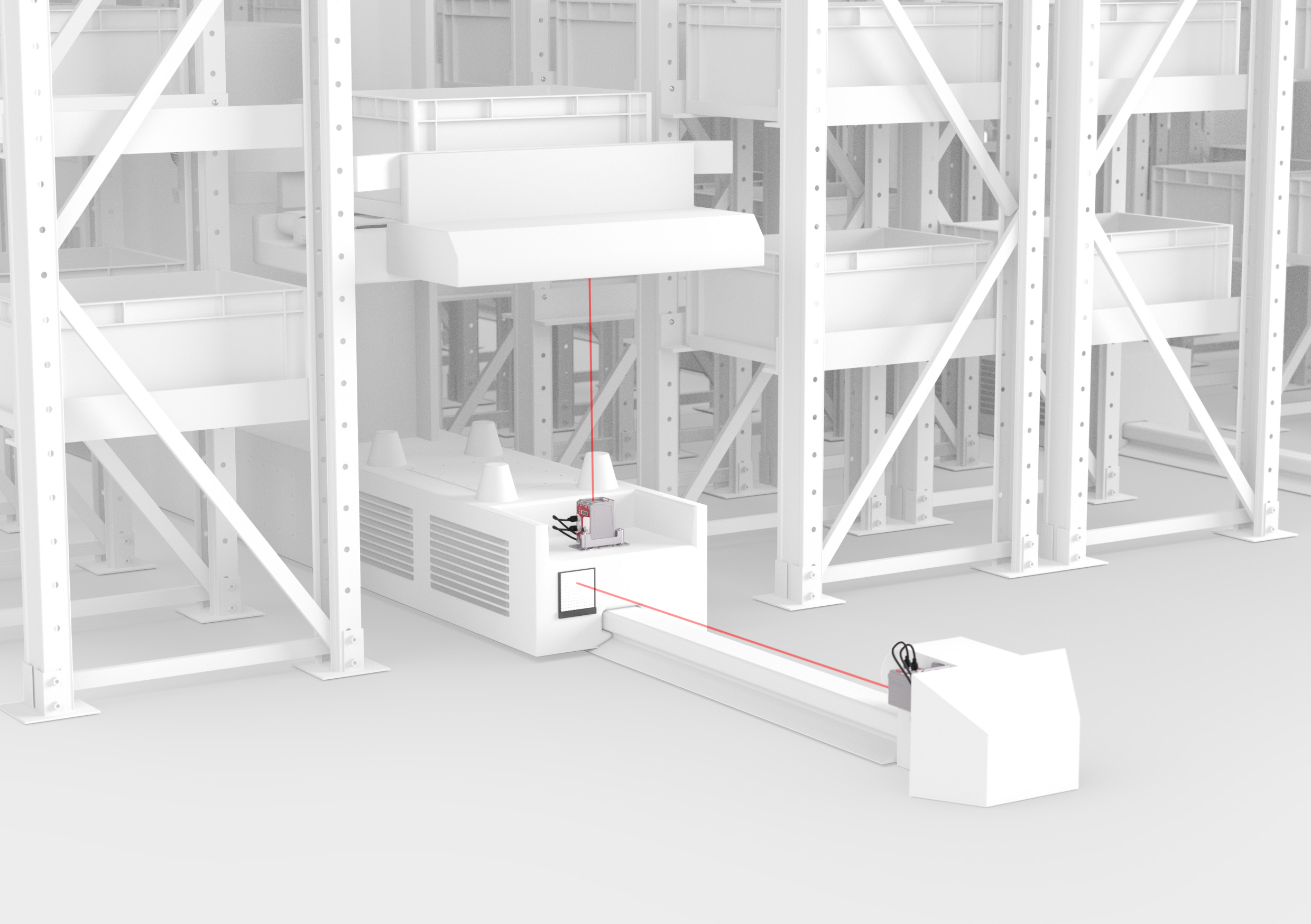
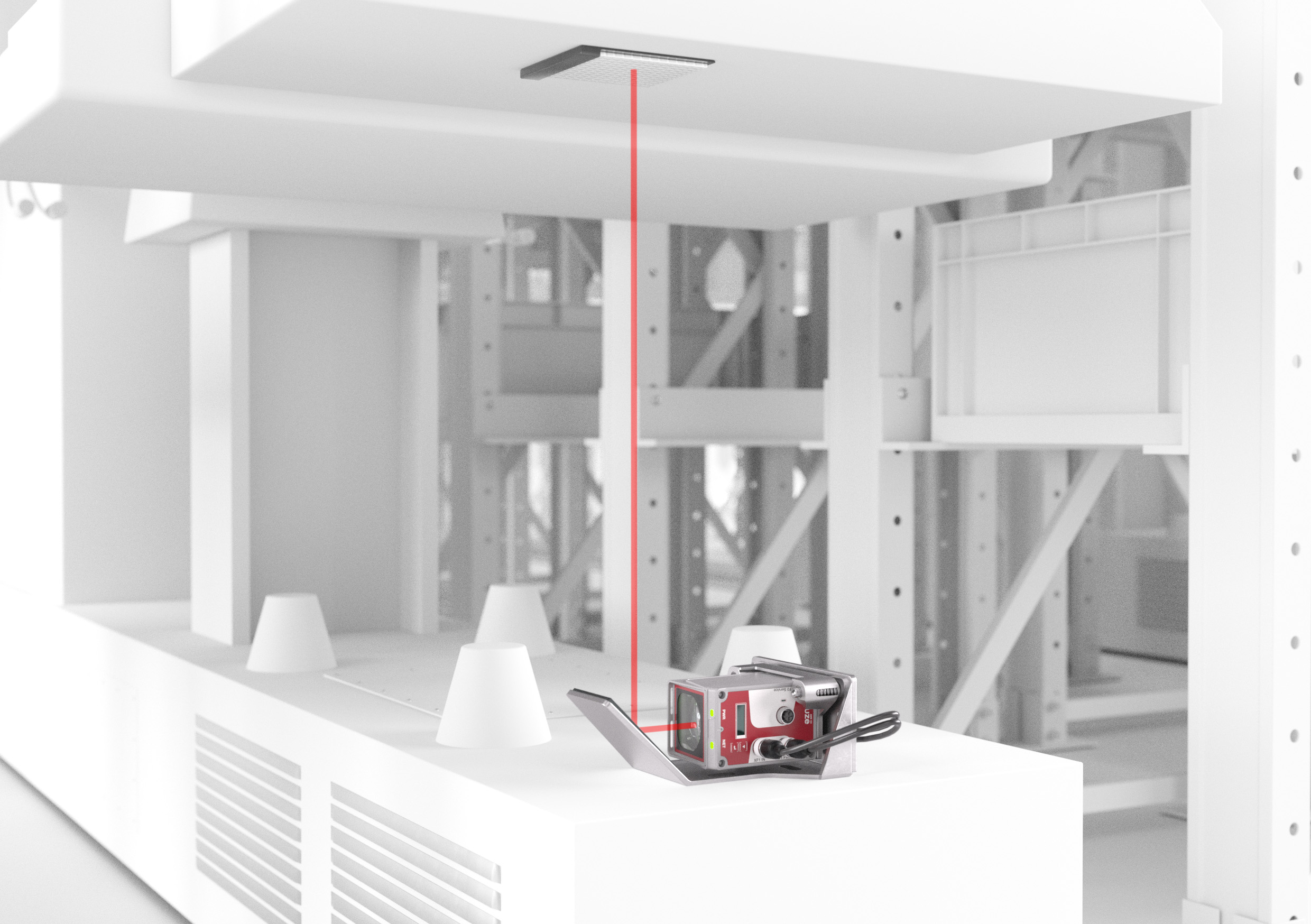
Positioning tasks on stacker cranes in a high-bay warehouse
Requirement:
In a high-bay warehouse with an aisle length of 120 m, load carriers (boxes, cartons and pallets) are to be stored and retrieved using a stacker crane. Automation and control must be controlled by a sensor and actuator system. Mechanical distance sensors, which are subject to wear or prone to contouring errors, are not to be used.
Solution:
The position of the stacker crane can be ascertained by means of an optical system which determines the distance between the vehicle and the end of the aisle. The new AMS 100i provides a reliable solution for positioning tasks up to 120 m and impresses with a traverse rate of up to 10 m/s as well as an accuracy of +/- 2 mm. And, unlike mechanical systems, it is absolutely free from wear.
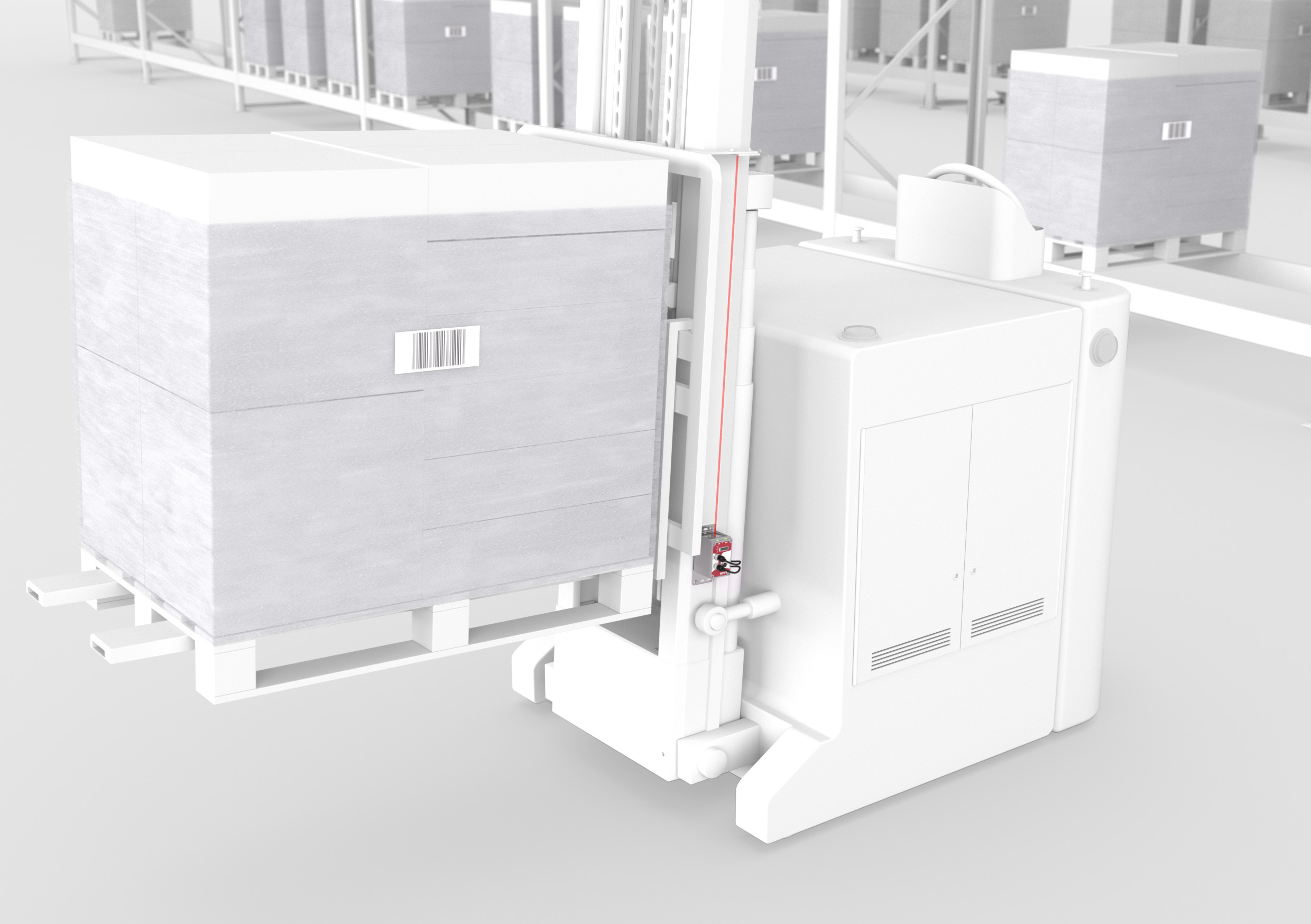
Lifting positions of corridor conveyors/load receptacles
Requirement:
In a manufacturing company, AGVs move along the corridors of storage and production areas. Mechanical distance sensors have until now been used for determining the height of the extendible forks of the load receptacles. The wear and the susceptibility to error caused by objects projecting into mechanical rope length sensors reduce the reliability and availability of these vehicles. A compact, optical system is therefore needed to resolve this problem. The sensors must be optimally integrated and it must be possible to mechanically mount them flexibly according to the type of vehicle and at as many different positions as possible.
Solution:
An optical system – like the new AMS 100i – is free from mechanical wear. Furthermore, it only measures the actual distance to the associated target and does not output any incorrect positions when load carriers or packaging material enter the measurement path.
The new AMS 100i, which measures 105 x 68 x 75 mm and has a dead zone of just 100 mm, is the smallest positioning sensor on the market. It therefore fulfills the requirement of sensor compactness, an important consideration because the vehicles need to be as small as possible and the sensor system is often built around them. Thanks to its modular installation concept, the AMS 100i can also be mounted with a very high degree of flexibility.
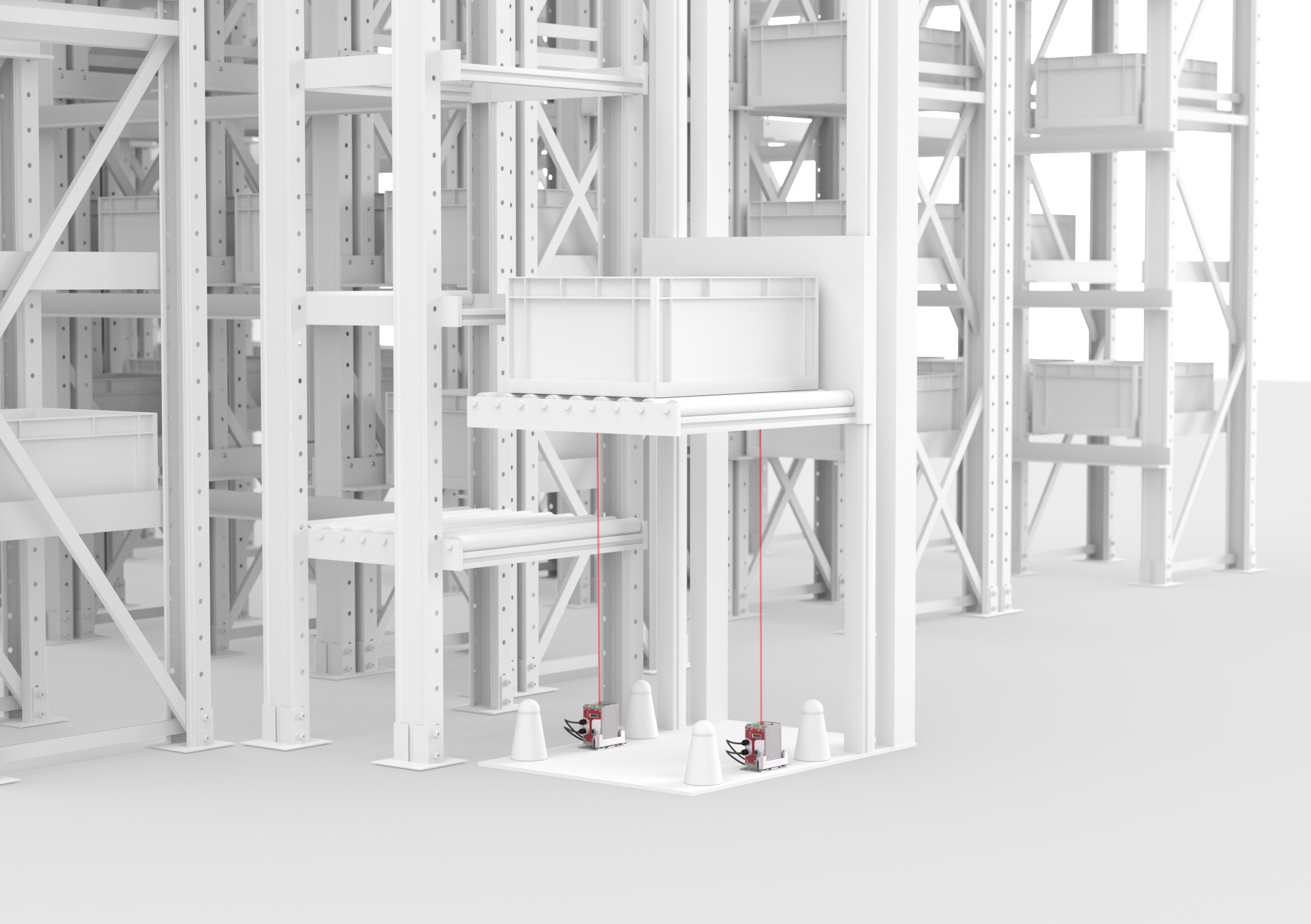
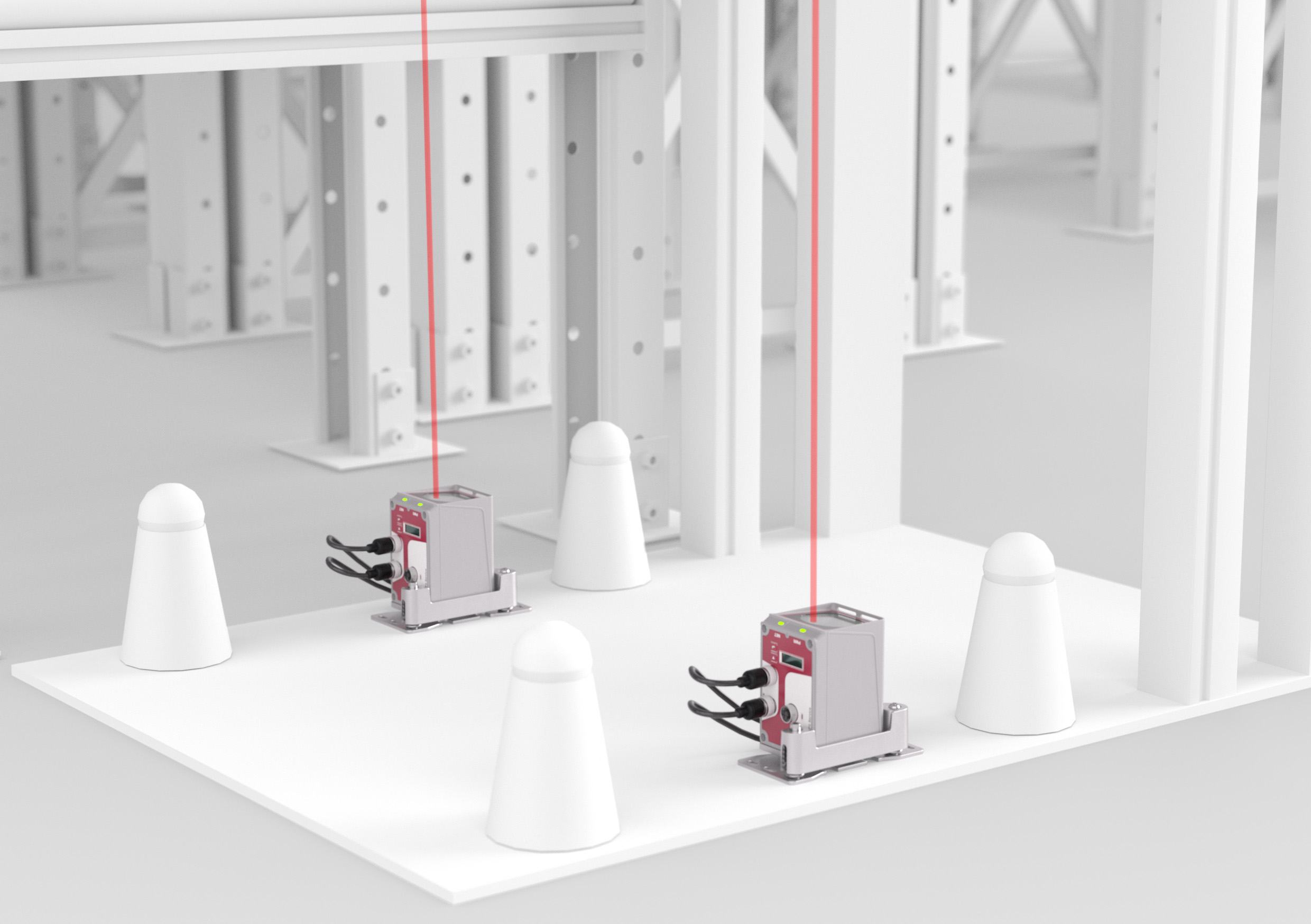
Optical positioning sensors on lift systems
Requirement:
In addition to stacker cranes, flexibly scalable shuttle systems are also to be used for storing and retrieving load carriers. Both the load carrier itself and the shuttles must be moved to various levels using lift systems.
Solution:
This task can be solved using the new AMS 100i optical positioning sensor, which covers many different operating ranges and enables dynamic and accurate measurement. The low close range of just 100 mm has the advantage that the sensor can be installed just below the load receptacle. In the case of wide load receptacles and in order to prevent misalignment (tilting), it is also possible to install and operate two measurement systems parallel to each other. Here too, the compact AMS 100i positioning sensor offers an attractive price/performance ratio.
Advantages for you
- Integrated connectivity: All well-known fieldbuses are directly integrated in the device
- Configuration in and via control: Configuration takes place directly in and via the control
- Automatic transfer to the new device: In case of replacement, all parameters are transferred automatically via the fieldbus (by means of the parameter data retention function in the configuration tools) to the new device.
- Multitude of selectable functions: A multitude of selectable functions can be optimally matched to your application. Interfaces, heating, operating ranges
- Continuous checking of relevant parameters e.g. laser, temperature, received signal level, position window or speeds. This enables the system to output a message well before a failure occurs, allowing the system to be checked and maintained in advance.
- Integrated mounting solution for easy adjustment and fixing of the set alignment
- Interference-free parallel operation with the DDLS series optical data transceivers
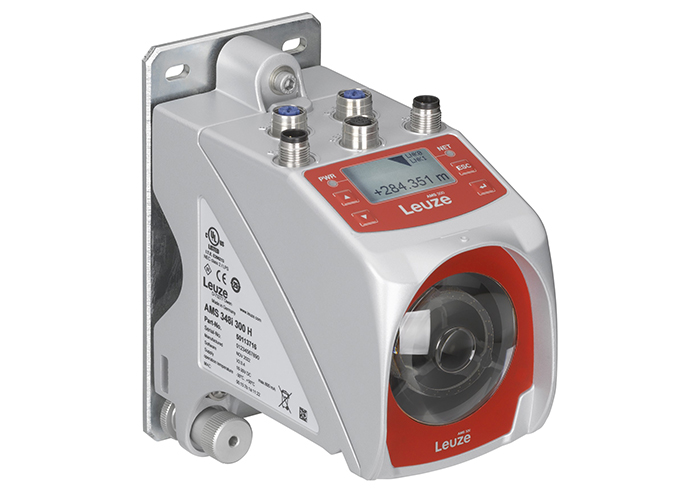
Application
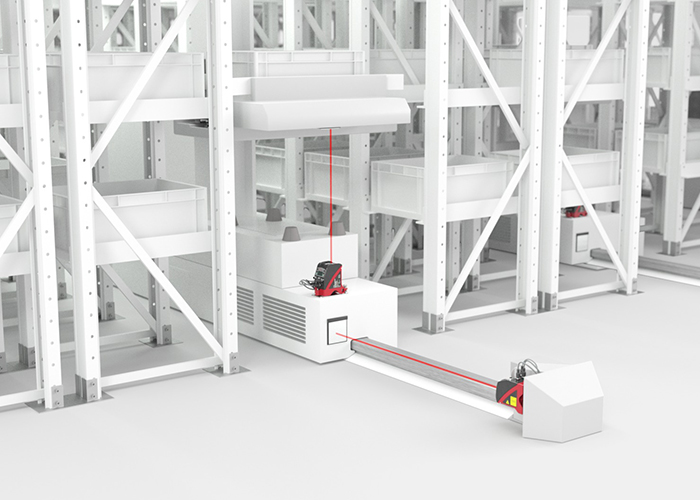
Positioning with laser positioning system in intralogistics
Requirement:
The stacker crane or load receptacle must be positioned in the X-direction (travel axis) and Y-direction (lifting axis) accordingly for the position to be approached.
Solution:
The AMS 300i laser positioning sensor quickly determines distances to moving system parts over a distance of up to 300 m with high absolute accuracy. In millisecond intervals, the devices make the measured values available for dynamic control via an extensive selection of industrial Ethernet or fieldbus interfaces.
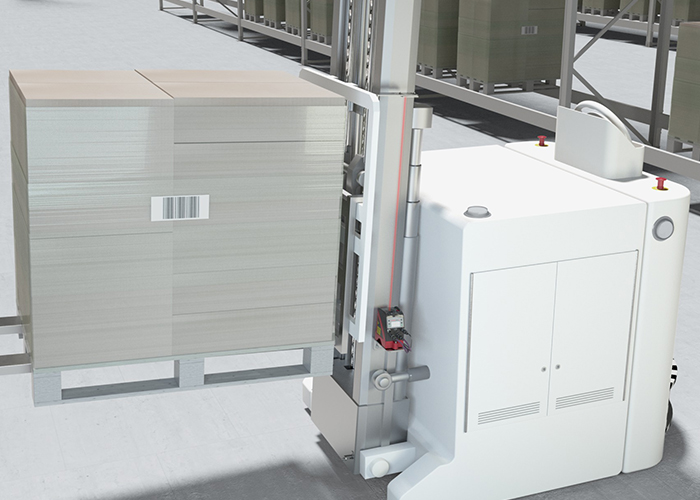
Vertical positioning of the load receptacle in intralogistics
Requirement:
For reliable storage and retrieval of the pallet, the load receptacle must be positioned precisely and repeatably at the correct height.
Solution:
The AMS 300i laser positioning sensor delivers measurement data every 2 ms with an absolute accuracy of ± 2 mm. The data can be transferred to the control via a wide range of interfaces.
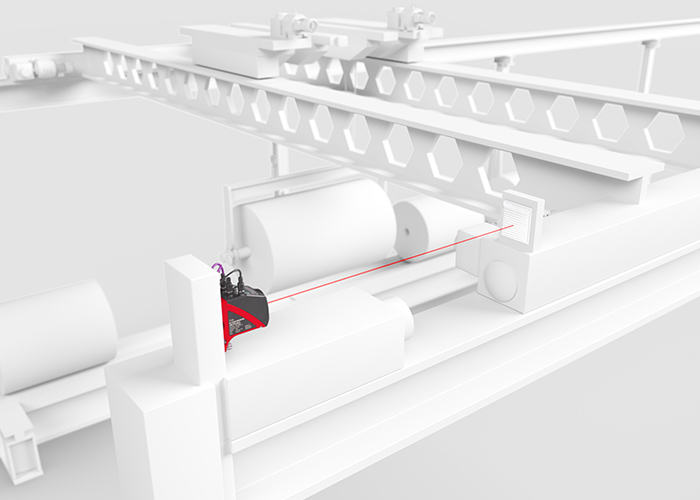
Positioning of cranes using laser positioning system
Requirement:
The crane or trolley should be positioned according to the position to be approached. It is not possible to attach a bar code tape for positioning.
Solution:
The AMS 300i laser positioning system quickly determines distances to moving system parts over a distance of up to 300 m with high absolute accuracy. In millisecond intervals, the devices make the measured values available for dynamic control via an extensive selection of industrial Ethernet or fieldbus interfaces.
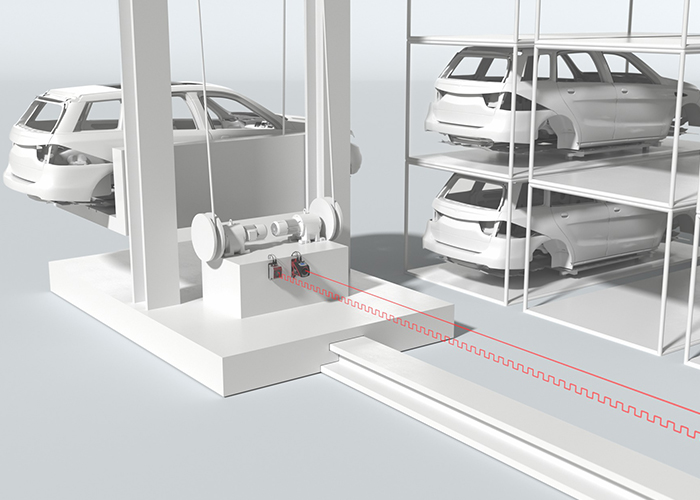
Positioning of the lifter and optical data transmission in the automotive industry
Requirement:
The stacker crane or lifter must be positioned in the x-direction (travel axis) and y-direction (lifting axis) appropriately for the pallet that is to be moved to. Travel commands and positioning data are to be optically transferred to the control to ensure high availability of the system.
Solution:
The AMS 300i laser distance measurement devices or BPS 300i bar code positioning systems are used for the exact positioning. The DDLS 500i data transmission photoelectric sensors function fault-free without offset directly next to the AMS 300i devices. Selectable operating ranges, interfaces and protocols ensure optimum solutions.
Overview of technical data
Feature | AMS 100i | AMS 300i |
Operating range | 0.1 – 120 m | 0.2 – 300 m |
Accuracy | ± 2 mm | ±5 mm (±2 mm up to 200 m) |
Repeatability (3 sigma) | 0.6 mm | 1.5 mm |
Light spot diameter | ≤80 mm | ≤220 mm |
max. traverse rate | ≤10 m / s | ≤10 m / s |
Supply voltage | 18 – 30 V DC | 18 – 30 V DC |
Current consumption | 250 mA without heating / 500 mA with heating | 250 mA without heating / 500 mA with heating |
Transmitter | Laser diode, red light, wavelength 655 nm | Laser diode, red light, wavelength 650 – 690 nm |
Laser class | Laser class 2 acc. to EN 60825-1; CDRH | Laser class 2 acc. to EN 60825-1; CDRH |
Operating temperature | -5 – 60 °C without heating / -30 – 60 °C with heating | -5 – 50 °C without heating / -30 – 50 °C with heating |
Degree of protection | IP 65 | IP 65 |
Interfaces | SSI, TCP/IP | PROFIBUS, PROFINET, DeviceNet, CANopen, EtherNet IP, EtherCAT, Ethernet, SSI, RS 232 / 422 / 485, Interbus |
Certifications | CE, UL, CDRH, ISO 9001 | CE, UL, CDRH, ISO 9001 |