Sensor solutions for confectionery and bakery packaging
With automated packaging processes in the confectionery and baked goods industry, flexibility is a decisive requirement: It is usually the case that very different products are produced and packaged on the same system. Here sensors are required that detect all of these products reliably and, wherever possible, without adjustments or additional settings having to be made. This becomes particularly challenging if confectionery is packaged in high-gloss and/or transparent films.
Our innovative sensors are optimized for applications in processing and packaging systems for confectionery and baked goods. The DRT 25C dynamic reference diffuse sensor uses the conveyor of the system as a reference and is therefore a specialist in detecting products with challenging shapes or surfaces. The LS 25CI Super Power throughbeam photoelectric sensor transilluminates even metalized film without problem and thereby detects products packaged inside films. When it comes to more complex inspection tasks, the flexible Simple Vision sensors are an optimum solution. Most of our sensors have an IO-Link interface. This allows presettings and recipes to be transferred directly from the machine control to the sensors. In this way, any sensor settings that may be required when the product is changed over can be made extremely flexibly and without long downtimes.
4 Detection of products on conveyor belts
5 Multiple-track object detection
6 Identification of empty molds
7 Detection of residual quantities in empty molds
8 Quality and object height monitoring
10 Code identification on flowpacks
12 Ejection monitoring and product count
13 Detection of cut marks in film feed
15 Detection of packaging content
16 Detection of packaged products
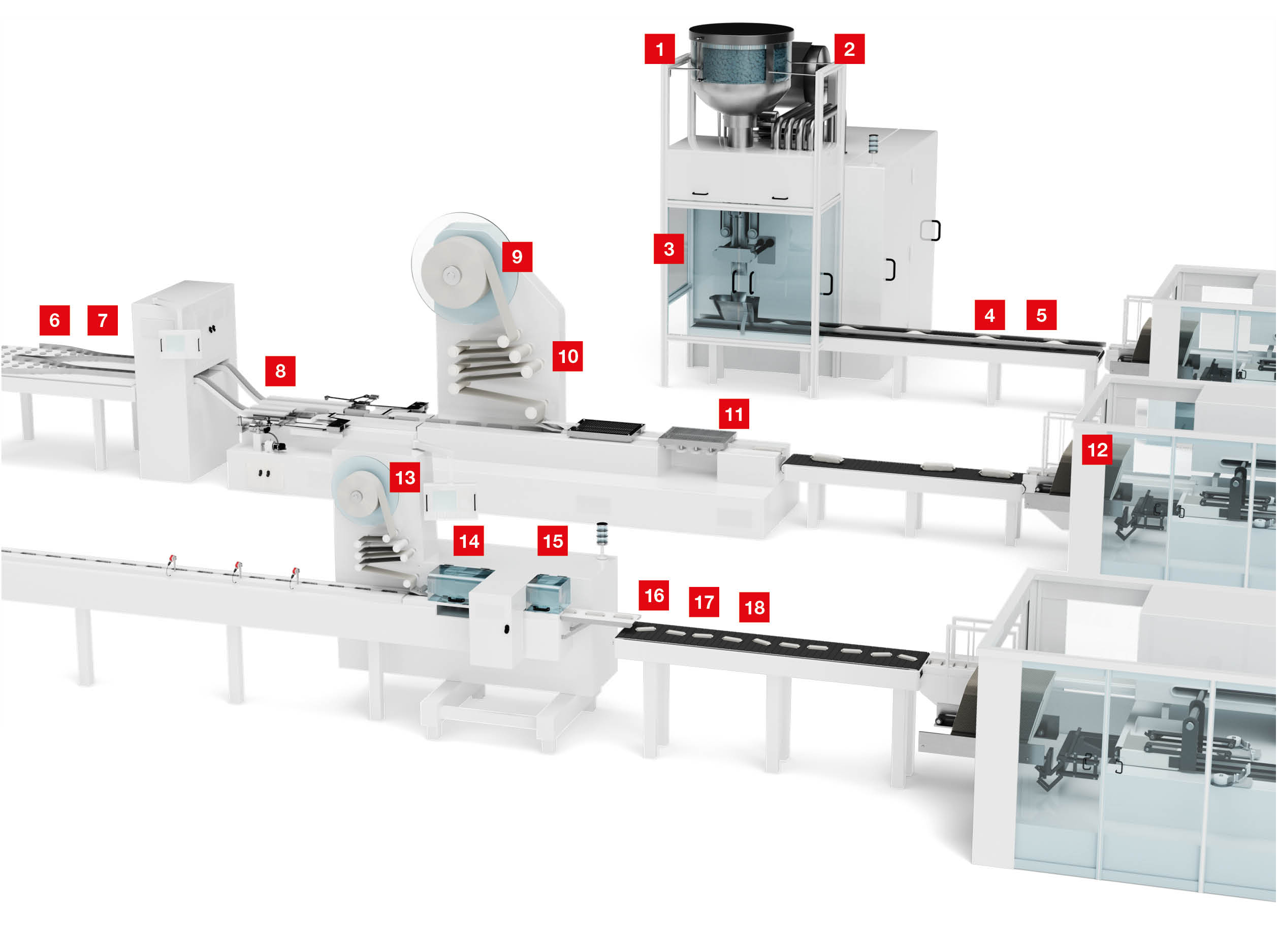
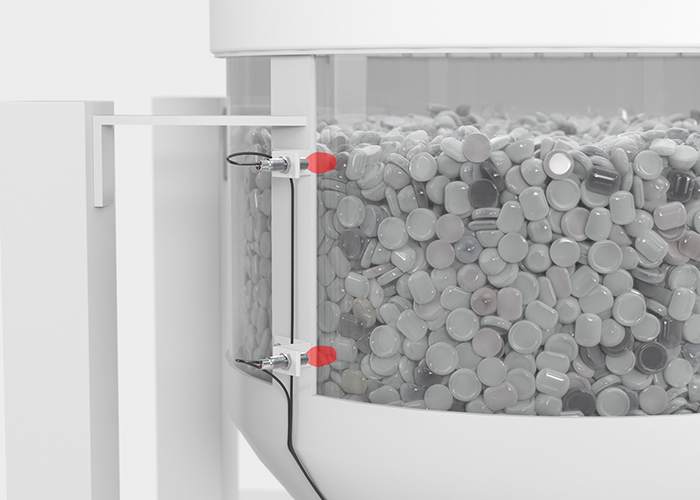
Requirement:
In confectionery production, numerous ingredients and additional items such as chocolate buttons, liquids, etc. are used. For continuous control of the provision of ingredients, the fill levels in the respective containers must be detected.
Solution:
The LCS capacitive sensors detect the fill levels of liquids or bulk materials in plastic or glass containers. The sensors detect through the container wall and without contact with the product. The position of the sensors defines a minimum and a maximum fill level.
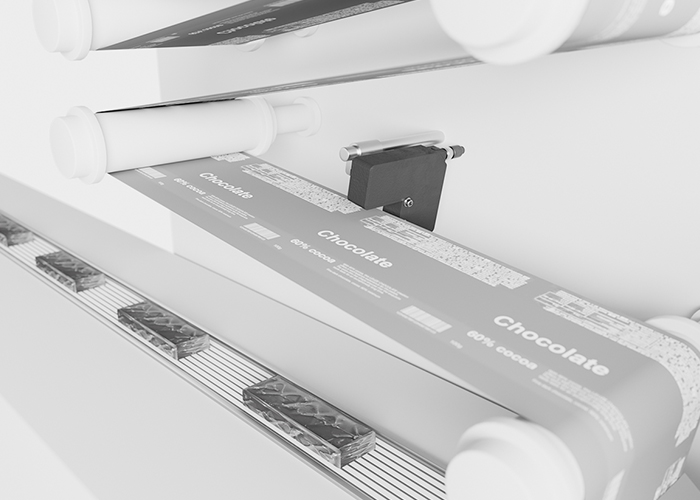
Requirement:
In order to guarantee a parallel run of the film and right-angled cuts, a web edge control along the film run is helpful. High demands on accuracy require a precise measuring sensor.
Solution:
The GS 754 measuring fork sensor is available in different mouth widths for edge control with maximum precision. The resolution of 0.01 mm allows for very fine web guiding. The GS 754 is a reliable solution for a wide range of materials.
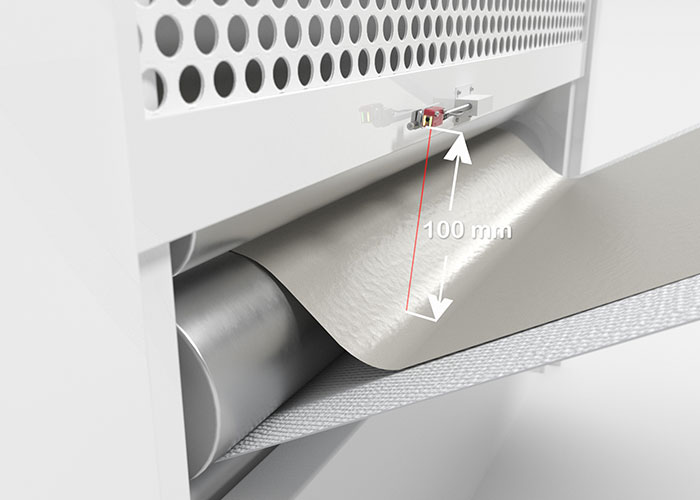
Requirement:
Dough is rolled out in a machine and later processed into baked goods. The dough is precisely rolled out to a required thickness. A sensor monitors that the dough retains its shape unchanged when transferred to the conveyor belt. The distance between the dough and the sensor is used as the measured variable.
Solution:
The ODT 3C is positioned at the output of the rolling machine above the dough loop and provides a distance value to the higher-level control. The measurement value is evaluated using the process data via IO-Link. In addition, diagnostic data is transmitted to the controller via IO-Link for Industry 4.0 purposes.
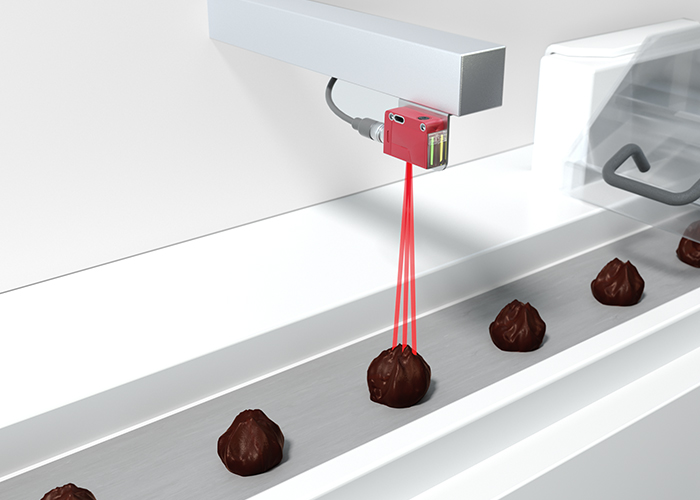
Requirement:
To control the buffer section, the front edges of the products on the conveyor belt must be reliably detected. The sensor must also detect products with challenging dimensions from very flat to very tall, in order to prevent machine downtimes due to incorrect detection.
Solution:
Due to its operating principle, the DRT 25C dynamic reference diffuse sensor reliably detects the entire range of products, from small and flat to tall and spherical. The single button teach function makes the DRT 25C easy to set up. Additional sensor functions can be controlled via the IO-Link interface.
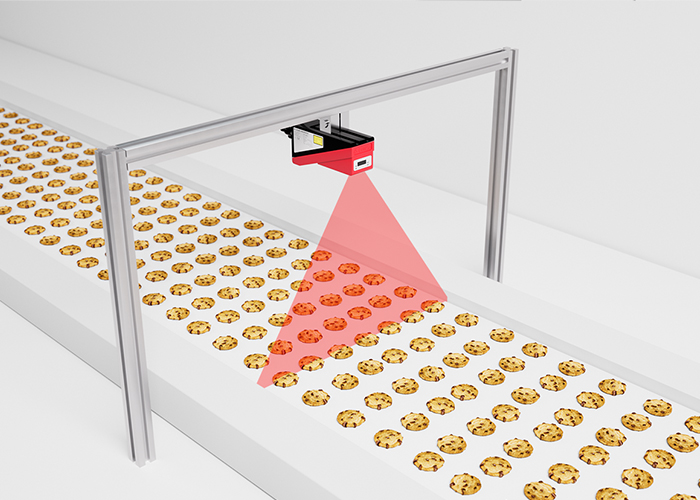
Requirement:
In the food industry, products are often transported between processes in multiple tracks. Detection of products for presence and/or completeness can only be done from above and should cover all tracks.
Solution:
The light section sensors LRS 36 (object detection), LES 36 (object measurement) and LPS 36 (profile measurement) detect different objects over a measurement field width of 600 mm. Missing products are thus easy to identify. The sensors output object position and height.
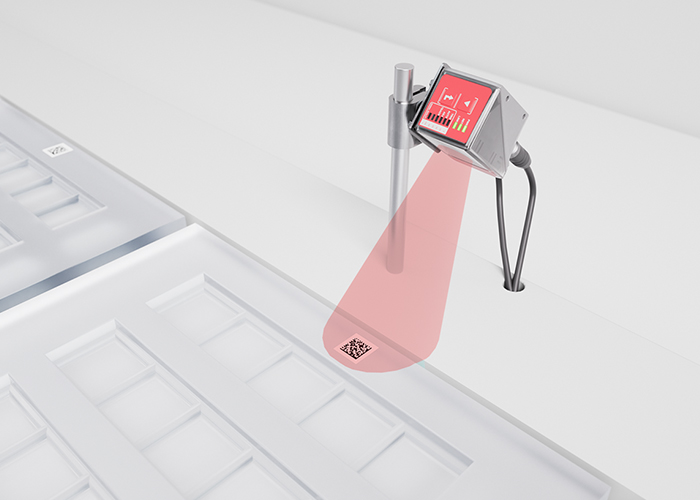
Requirement:
In confectionery production, molds are used to manufacture or mold products. In the process, the first step is to identify and verify the empty mold.
Solution:
The universal compact DCR 200i code reader reliably captures 1D or 2D codes. It is available with a stainless steel housing for use in food processing. For larger distances to the empty mold, the high-performance DCR 1048i Simple Vision sensor is suitable.
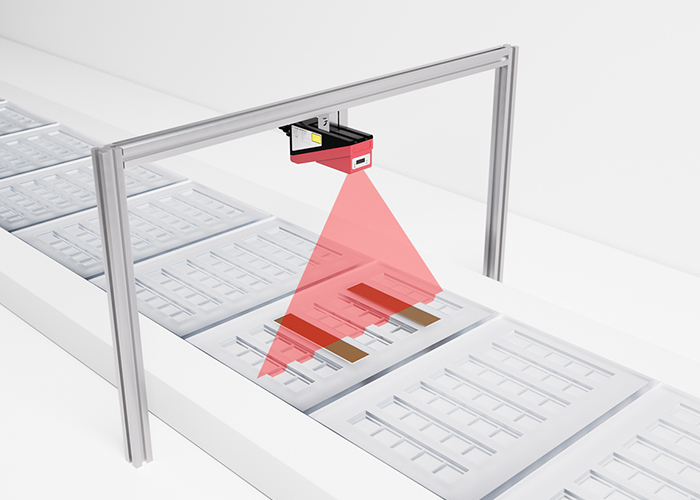
Requirement:
Before reusing empty molds, it must be ensured for a reliable production process that no residues are present in any of the molds.
Solution:
The LPS 36 light section sensor records a profile of the mold and provides a distance and position value for each measuring point along the laser line. The connected control evaluates "empty" or “residues in the mold". Alternatively, the IVS 1048i Simple Vision sensor with integrated image processing can be used.
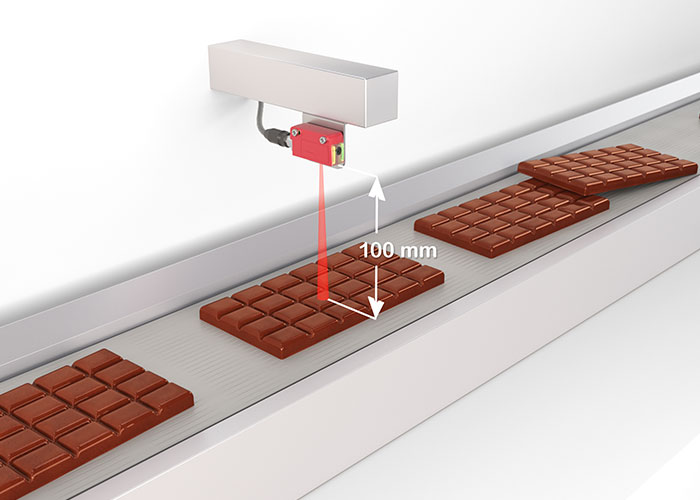
Requirement:
For further processing in a horizontal packaging machine, it must be checked that the manufactured products (e.g. chocolate bars) run separately on the conveyor belt. For this purpose, monitoring is performed to determine whether the defined product height (e.g. overlapping objects) is maintained.
Solution:
The ODT 3C sensor is installed above the conveyor belt, looking down at the products. It detects the objects (switching sensor function) and simultaneously measures their height (measuring sensor function). This ensures that products run separately on the conveyor belt. The measurement data is output via the IO-Link interface of the sensor.
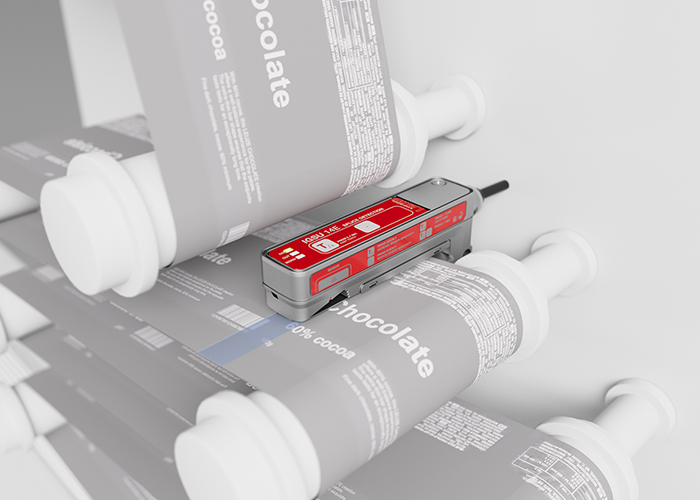
Requirement:
Splices that occur when changing the packaging film rolls must be reliably detected and discharged in the process. The detection of the splice should be as independent of color and surface as possible, since the printing on the packaging film can be very diverse.
Solution:
IGSU14E SD fork sensors reliably detect splices. Due to the ultrasonic principle, it is possible to work with any type of printing. The sensors can be taught quickly and easily with the aid of the teach function. A diagnostics function is possible via the integrated IO-Link interface.
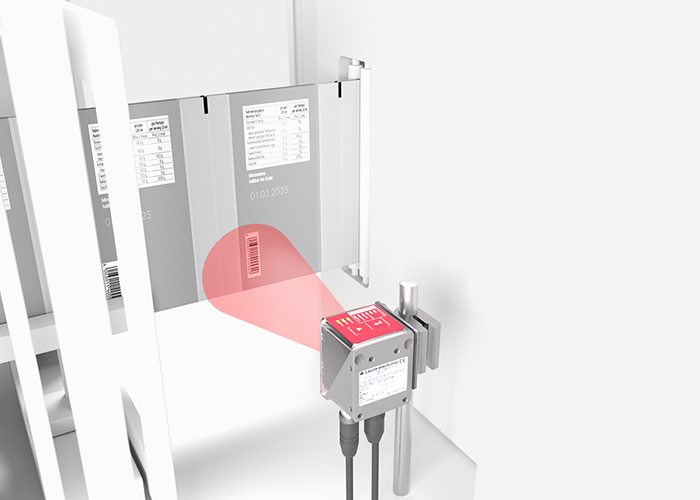
Requirement:
In packaging processes, an attached code must be used to ensure that the packaging material and product are correctly assigned. Sensors must control different types of codes and the readability of the code. A camera-based code reader can be used for this purpose.
Solution:
The DCR 200i camera-based code reader decodes 1D- and 2D-codes. With the aid of the integrated reference code function, the sensor can compare the read code with the reference or target code. The result is output in real-time via digital IOs. Alternatively, the code content can be transferred to the machine control via the fieldbus interface.
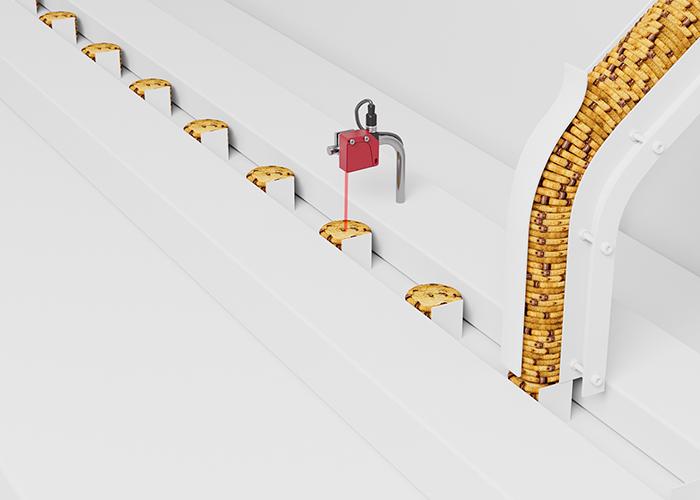
Requirement:
If several flat products are stacked on top of each other, the stack height must be monitored so as not to impair the subsequent packaging process. At the same time, the number of stacked products can be controlled.
Solution:
Thanks to their different measurement ranges and resolutions, the ODS 9 measuring distance sensors are suitable for fill-level monitoring. Due to the parameterizable analog current or voltage output and the IO-Link interface, they can be easily adapted to the control environment used.
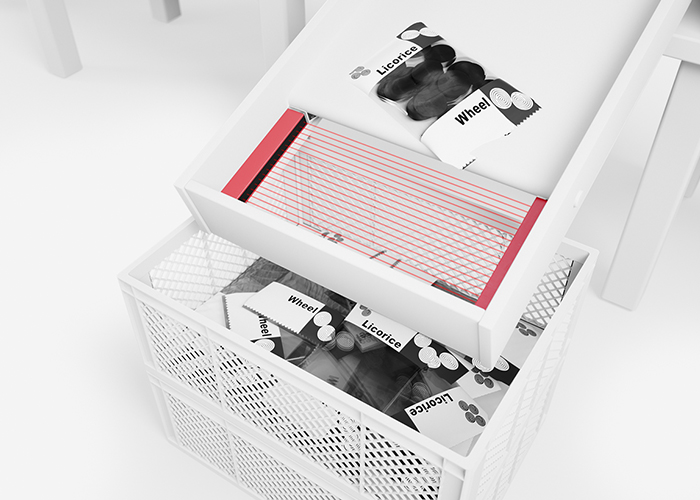
Requirement:
Defective or incomplete products are ejected without sorting or alignment on a packaging machine. Switching light curtains can detect these products. Alternatively, a fast switching light curtain can be used at the outlet of the machine to count the properly packaged products.
Solution:
The CSL 710 switching light curtain is suitable for monitoring larger ejection openings thanks to its various lengths and resolutions. The compact CSL 505 light barrier is a space-saving solution for simple applications. The CSR 780 retro-reflective light curtain is suitable for fast object counting due to its short response time.
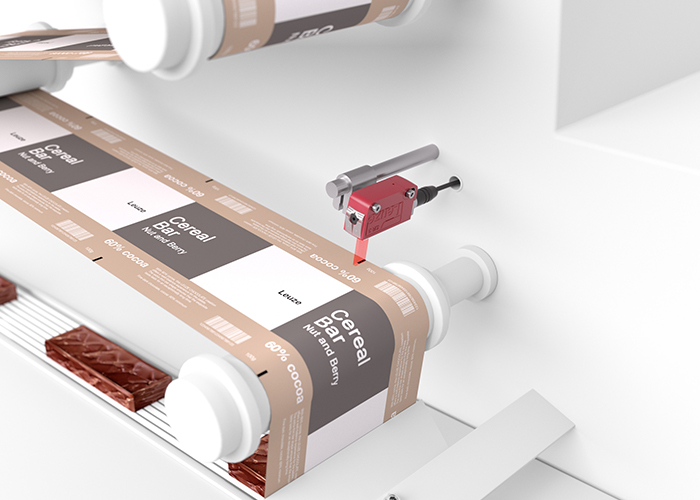
Requirement:
Products are packed in packaging films in horizontal packaging machines. Sensors must detect the printed contrast markers and thus control the precise cutting process. Common challenges are the limited installation space and the frequent format changeovers due to films and contrast markers of different colors.
Solution:
The compact KRT 3C contrast sensor is available in three models: the flexible version with RGB LEDs, a universal version with white light, and a version for larger distances with laser-generated red light. The sensors can be taught via the integrated teach button, IO-Link, or cable.
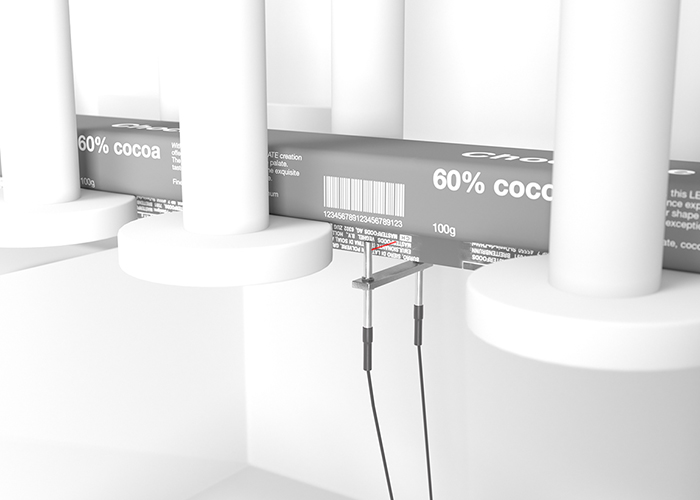
Requirement:
For food packaged in film, a correctly executed sealed seam ensures the shelf life of the packaged products. For this purpose, the sealed seam must be continuously checked in the horizontal process. The sensors used must be adapted to the space available in the machine.
Solution:
The KF and KFX fiber optics with different optical outlets and mounting options can be used flexibly in confined installation situations. Combined with amplifiers with high optical power, LV463.XR is a solution tailored to the application. Further advantages are the analog output and the IO-Link interface.
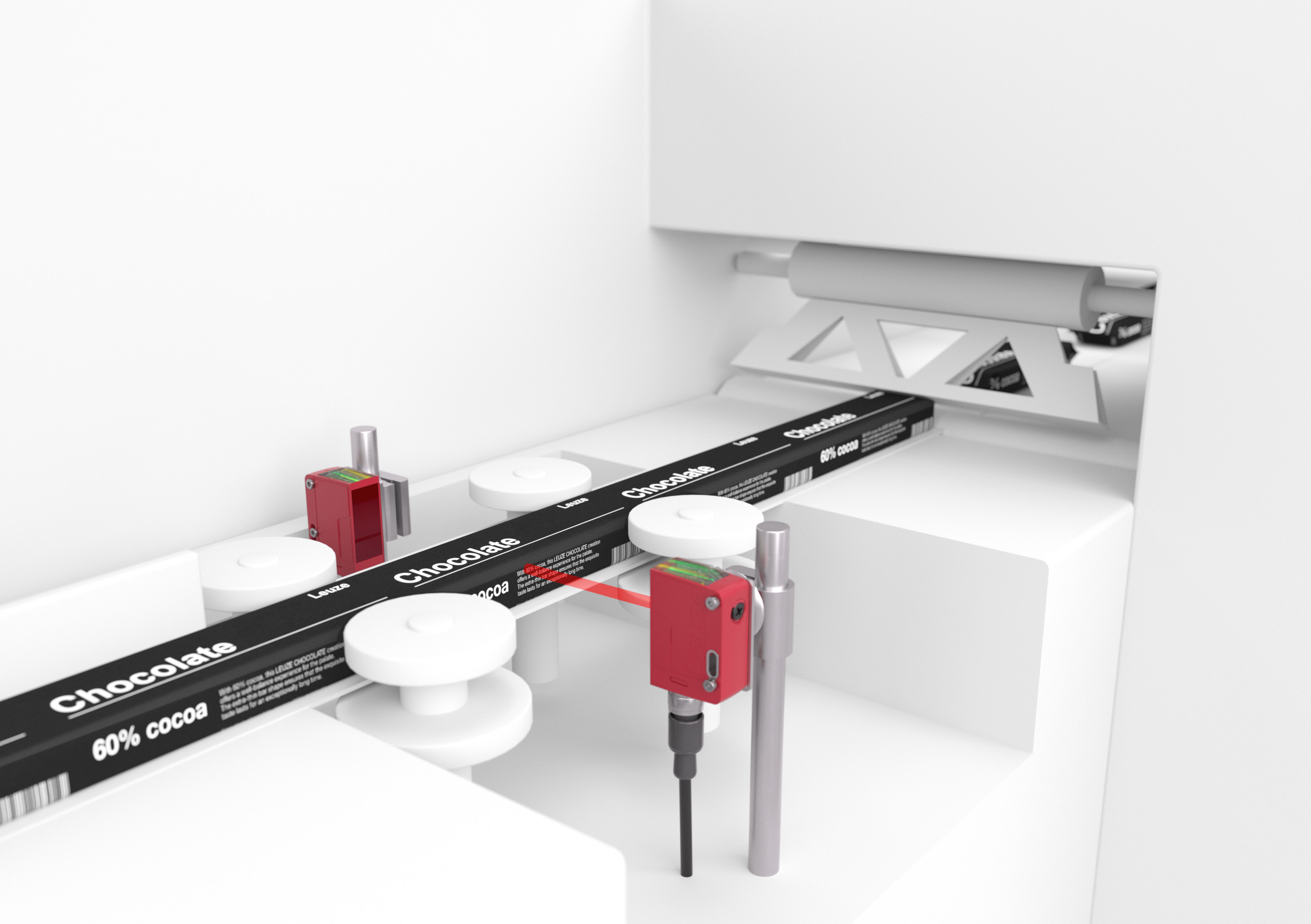
Requirement:
Chocolate bars, for example, are packed in film in a horizontal packaging line. The packaging film mostly has a colorful print and is opaque. To ensure that sealing occurs at the correct point on the film tube, the front edge of the bar located inside the film tube needs to be reliably detected.
Solution:
The high-performance LS25CI.XXR super power and LS25CI.XR high power throughbeam photoelectric sensors effortlessly transilluminate most metallized and dark-colored films. Even in the sealed film tube, the front edges of the products in the packaging are reliably detected.
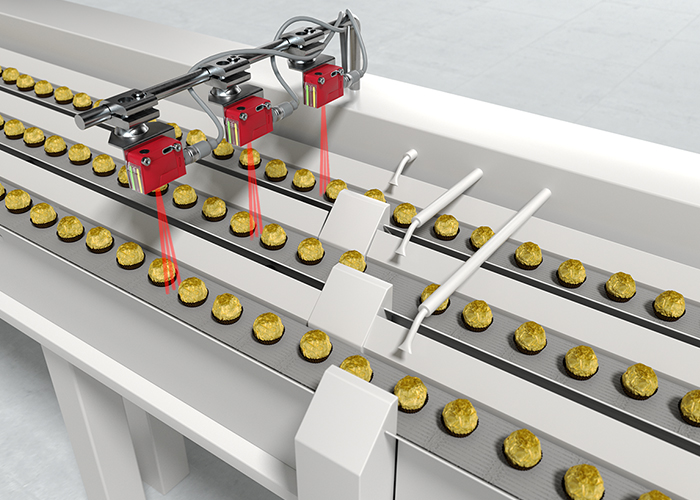
Requirement:
If several conveyor belts are arranged next to each other at a close distance, it is necessary to detect objects from above. In production plants, adaptations to sensors should ideally not be necessary during format changes in order to avoid downtimes.
Solution:
Using the conveyor belt as a reference and the processing of diffuse reflection and distance, the DRT 25C detects all objects. One teach event during commissioning is sufficient - no adaptation is required for format changes.
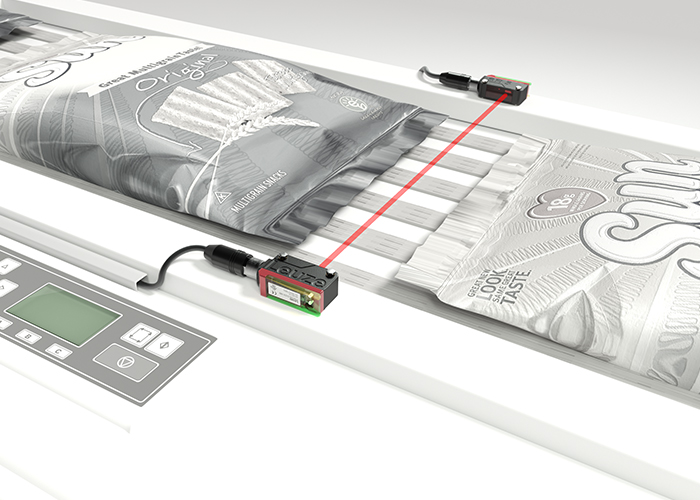
Requirement:
At a food manufacturer, products are packed in high-gloss primary packaging. The packages are then transported further on a conveyor belt where they are to be reliably detected. Sensors with short response time can detect even small gaps between products.
Solution:
The sensors of the 5B series can be mounted horizontally on the conveyor line. The advantage of the throughbeam photoelectric sensor is the very high function reserve. This ensures reliable detection even with critical surfaces.
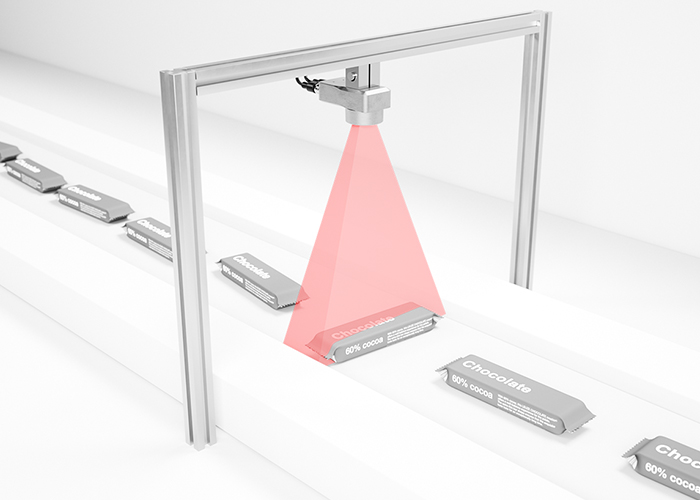
Requirement:
At the outflow of a horizontal packaging machine, the correct alignment of the products must be checked before they are automatically packed into a carton. For this purpose, a camera-based Vision sensor is to be used that looks down on the conveyor belt from above.
Solution:
The IVS 1048i Simple Vision sensor can check the position of the products on the conveyor. The evaluation tools that can be selected in the sensor, e.g. pattern detection or position detection, are used for this purpose. In addition, bar codes or 2D-codes on the product can also be read and checked.