Sensor solutions for automated guided vehicles (AGV)
Automated guided vehicles move goods from A to B. The distances can be easily adapted. This makes the production system very flexible. The demands on dynamics and safety are high. Especially when several vehicles are used at the same time.
Intelligent sensor solutions are a prerequisite for smooth operation and to prevent collisions. Safety laser scanners safeguard the vehicles. Our high-resolution and dynamic sensors provide the data for the precise navigation of the AGVs. The correct pick-up and transfer of goods is monitored by optical and inductive sensors.
White Paper: AGVs on the road to success – Which technology is right for you?
Automated Guided Vehicles (AGVs) have significantly changed intralogistics in recent years. Selecting the best navigation technology for AGVs plays a crucial role in the success of logistics processes in companies. But which navigation technology is suitable for which application scenario? What are the advantages of the different technologies? You can find answers to these questions in this white paper.
In this white paper, we answer the following questions:
- What navigation technologies are available for AGVs?
- What is the principle on which the individual navigation technologies are based?
- Which navigation technology is suitable for which application scenario?
- What are the advantages and disadvantages of the individual technologies?
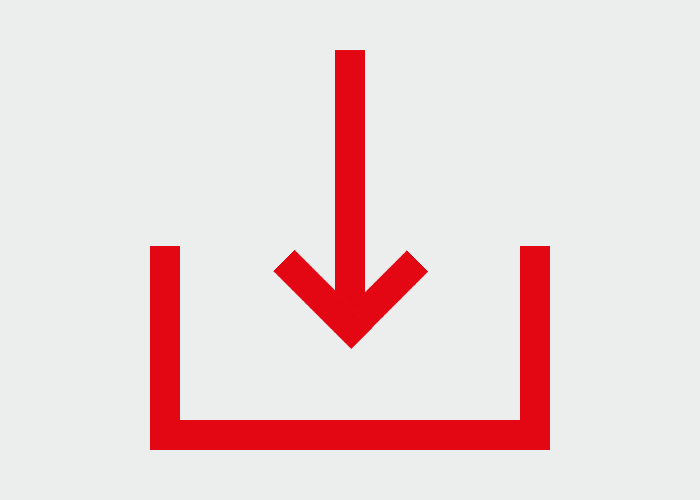
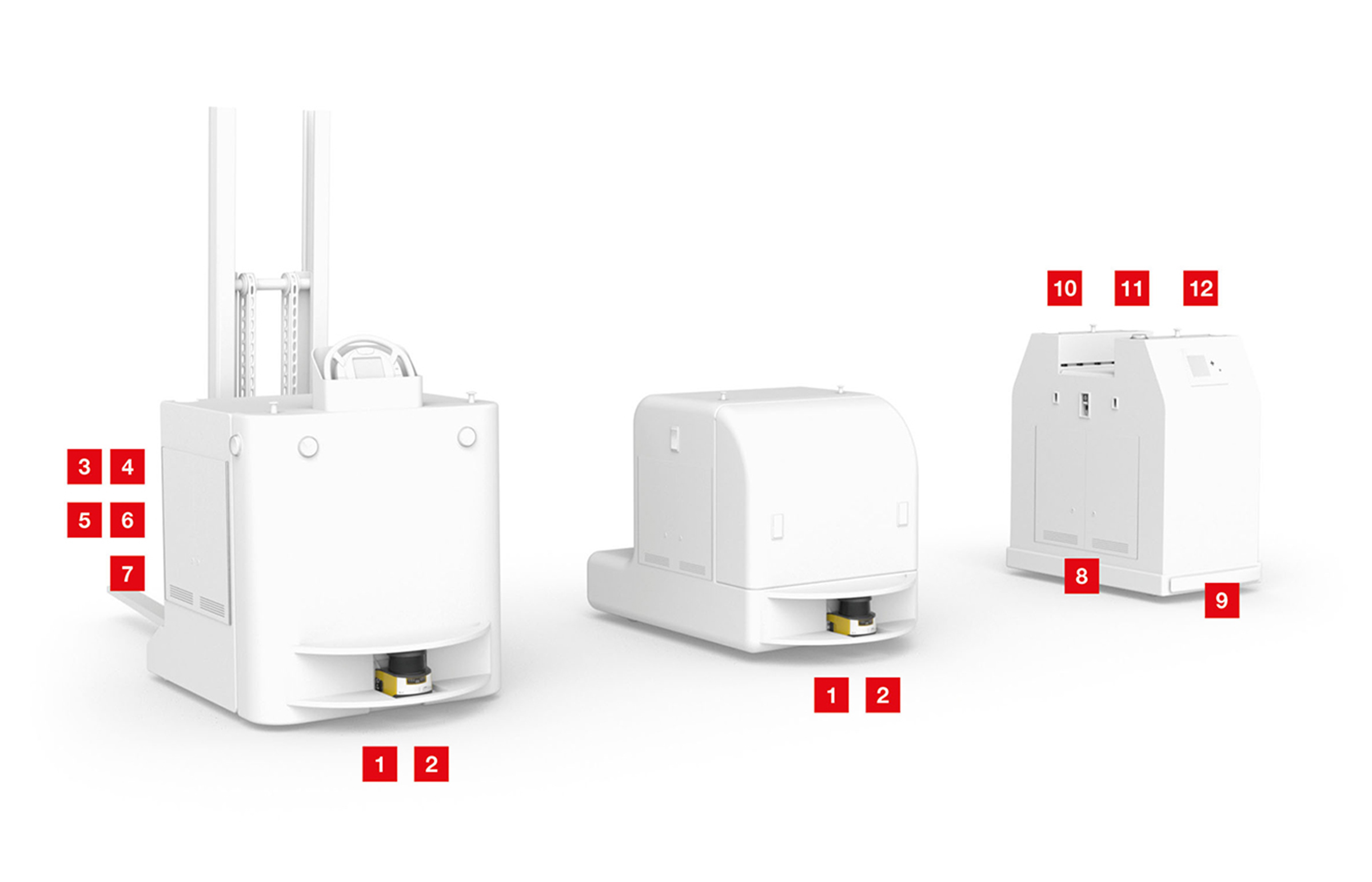
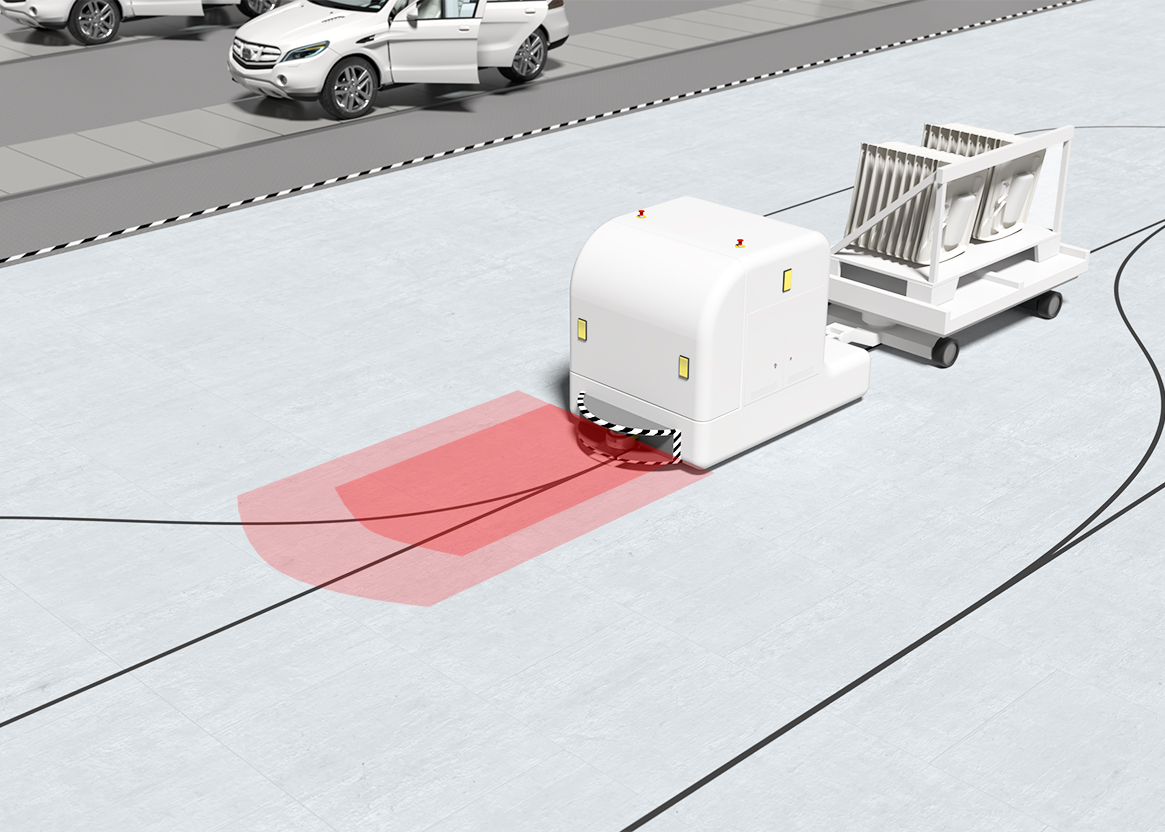
Requirement:
To safely stop the AGV in the presence of persons or objects, a defined area in front of the AGV must be monitored. To adapt to speed and transportation path, the size and direction of the area should be switchable.
Solution:
The RSL 400 safety laser scanner has a scanning range of 270° and up to 100 switchable field pairs. This allows the protective field to be optimally adapted to the speed and the transportation path.
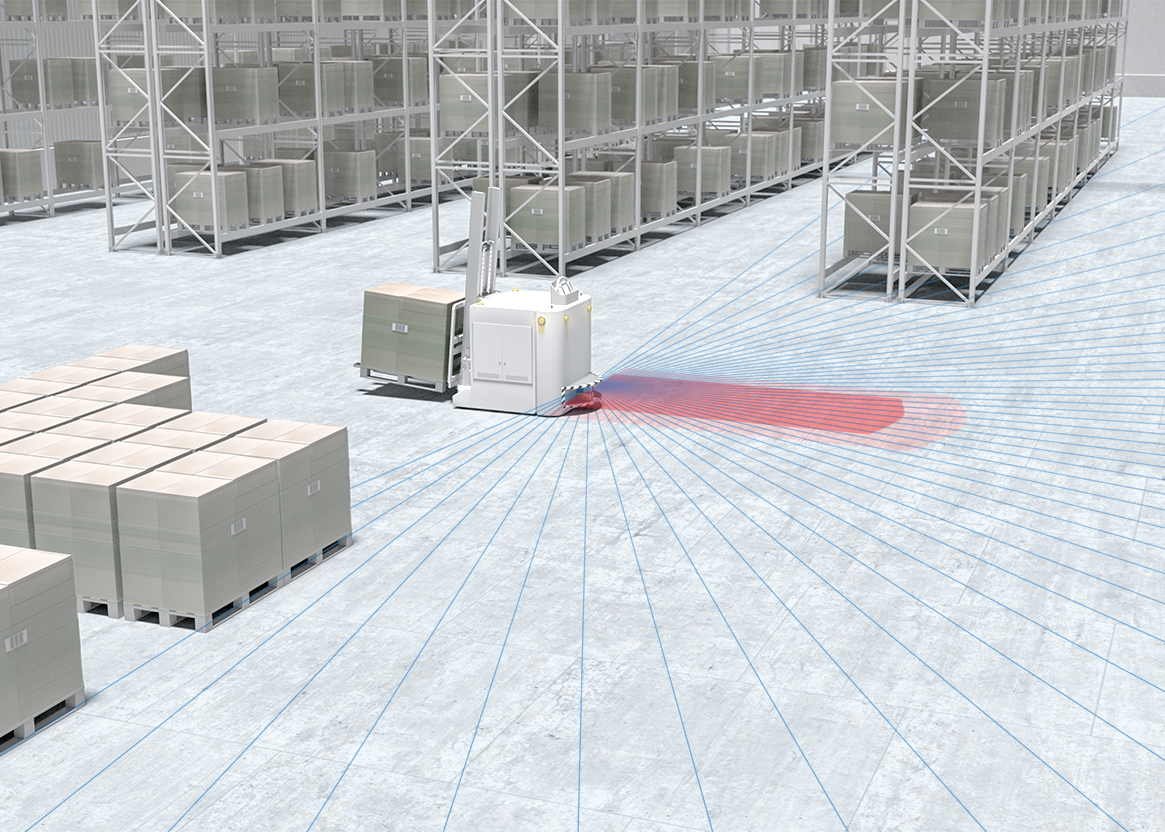
Requirement:
If the principle of natural navigation is used, the safety sensor should simultaneously provide the measurement data for the navigation software in addition to safeguarding the transportation path in different driving situations.
Solution:
The RSL 400 safety laser scanner merges safety technology and high-quality measurement value output in a single device. It has up to 100 switchable field pairs. The measurement data have a high angular resolution of 0.1°, which allows a very accurate map of the environment to be created.
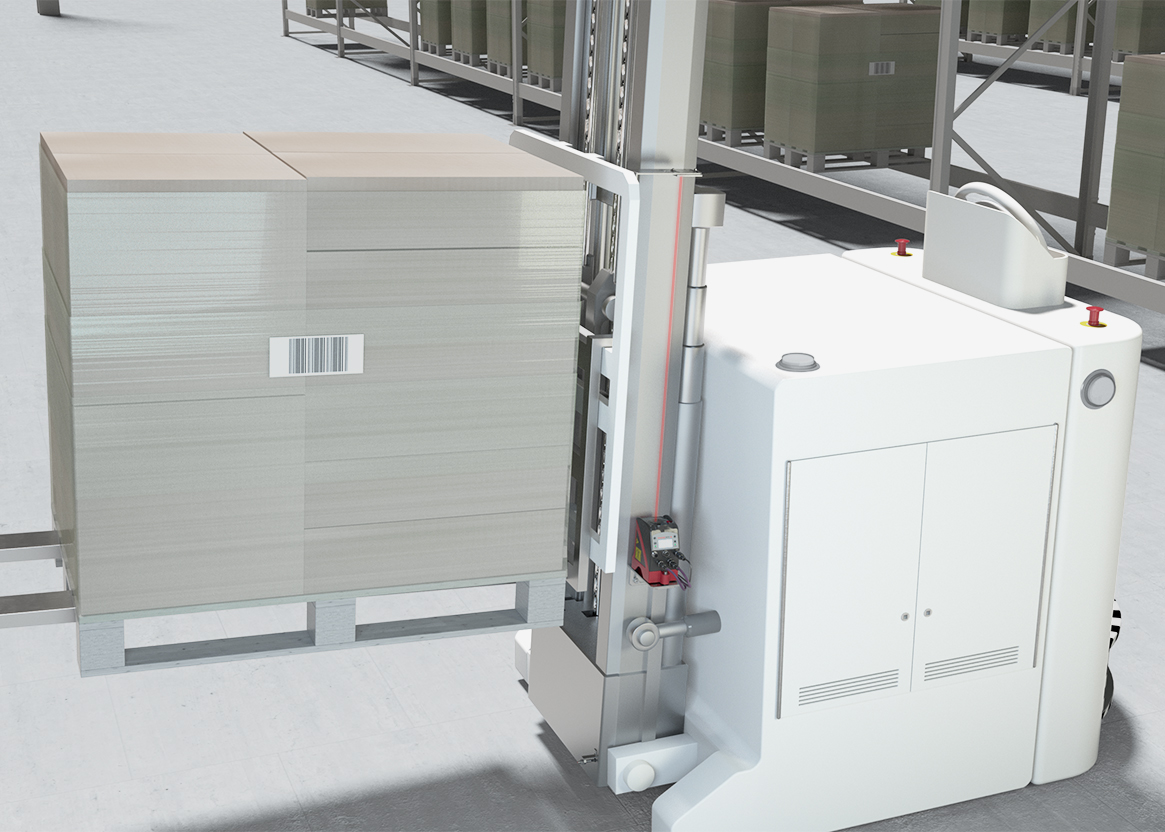
Requirement:
For reliable storage and retrieval of the pallet, the load receptacle must be positioned precisely and repeatably at the correct height.
Solution:
The AMS 300i laser positioning system delivers measurement data every 2 ms with an absolute accuracy of ± 2 mm. The data can be transferred to the control via a wide range of interfaces.
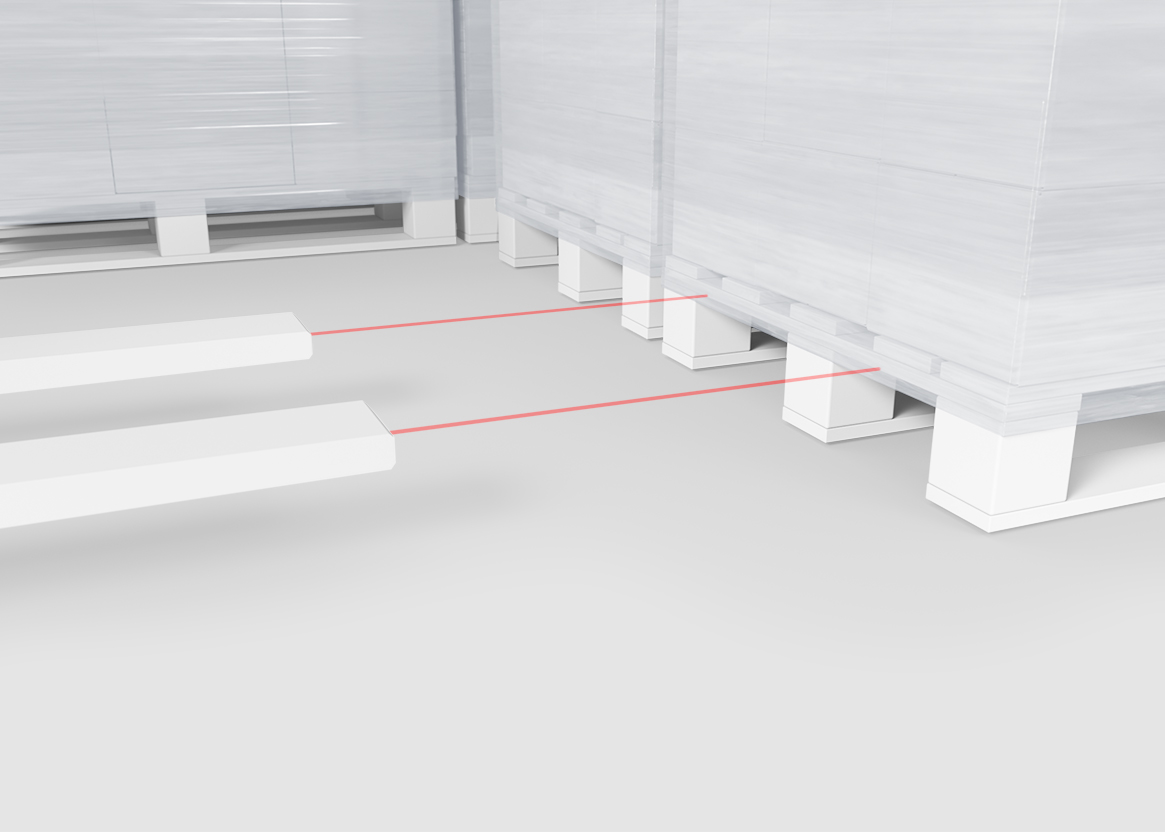
Requirement:
In order to detect the pallet with the load receptacle, it must be detected where the spaces of the pallet feet are located and whether they are freely accessible.
Solution:
The HT 3C series diffuse sensors operate independently of the material and have precise switching points. Two digital switching outputs allow the same sensors to be used for compartment fine positioning.
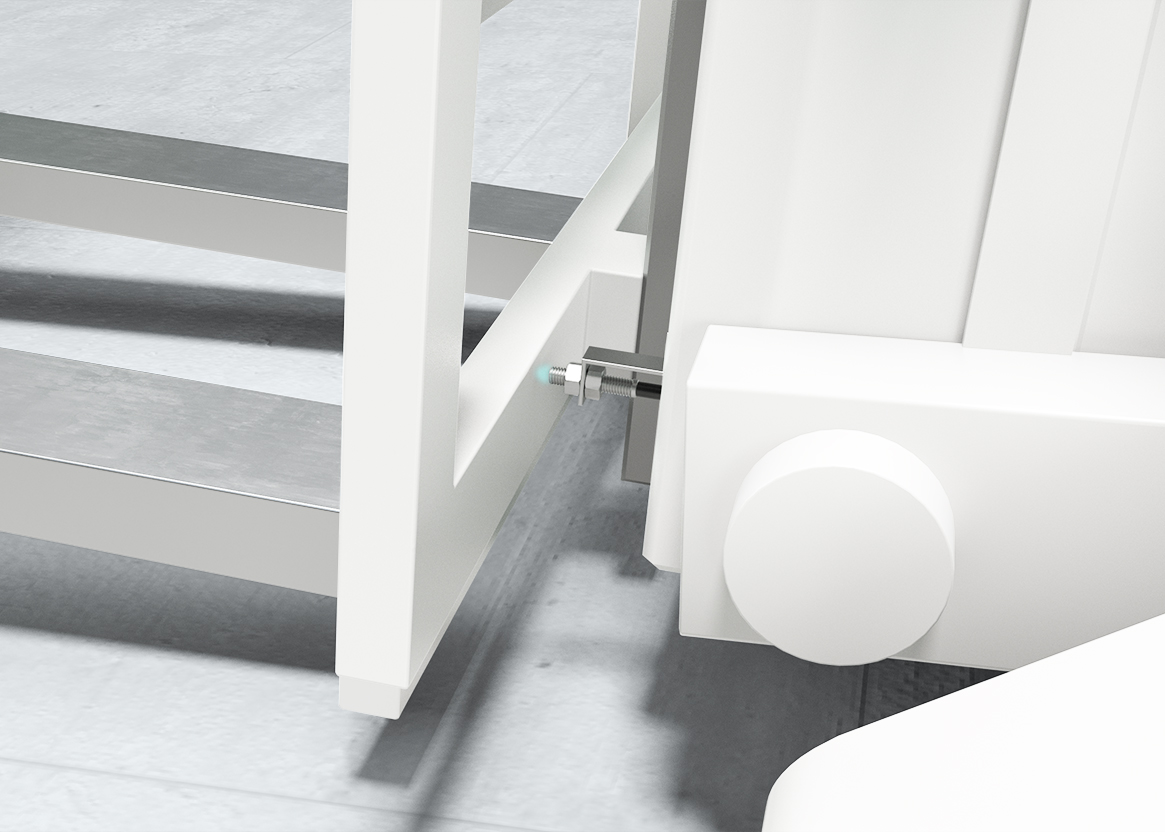
Requirement:
Before certain functions of the vehicle can be activated - such as switching from creep speed to normal speed - it must be ensured that the load receptacle is in the final position.
Solution:
The IS 212 series inductive sensors detect metal objects with a maximum working distance of 10 mm. The devices are well protected against environmental influences and cleaning processes by the robust metal housing.
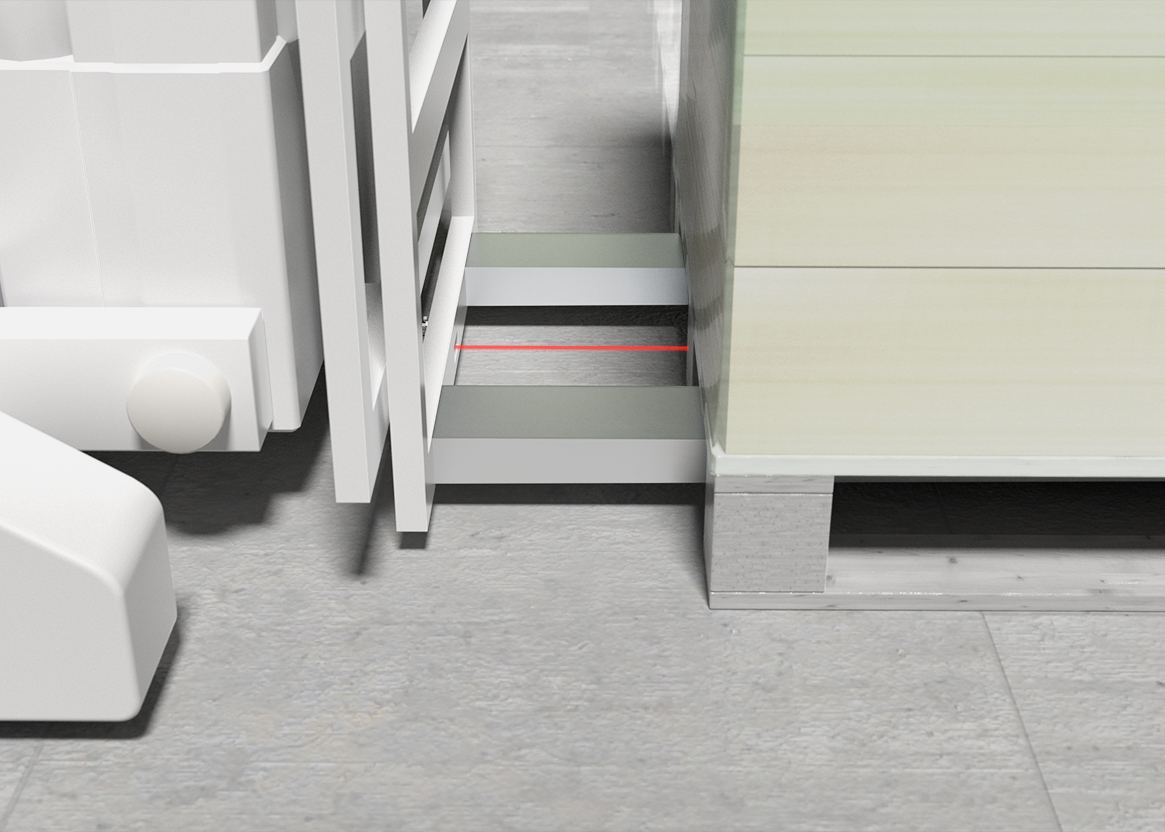
Requirement:
When picking up the pallet, the distance between the pallet and the end face of the load receptacle must be determined in order to stop the forward movement in good time.
Solution:
With their large light spot, the HRT 25B LR series distance sensors determine the distance to objects with a wide variety of colors and surfaces reliably and with repeatable accuracy. Thanks to TOF (time of flight) technology, the devices also have a high operating range of 2,500 mm and a high angle tolerance.
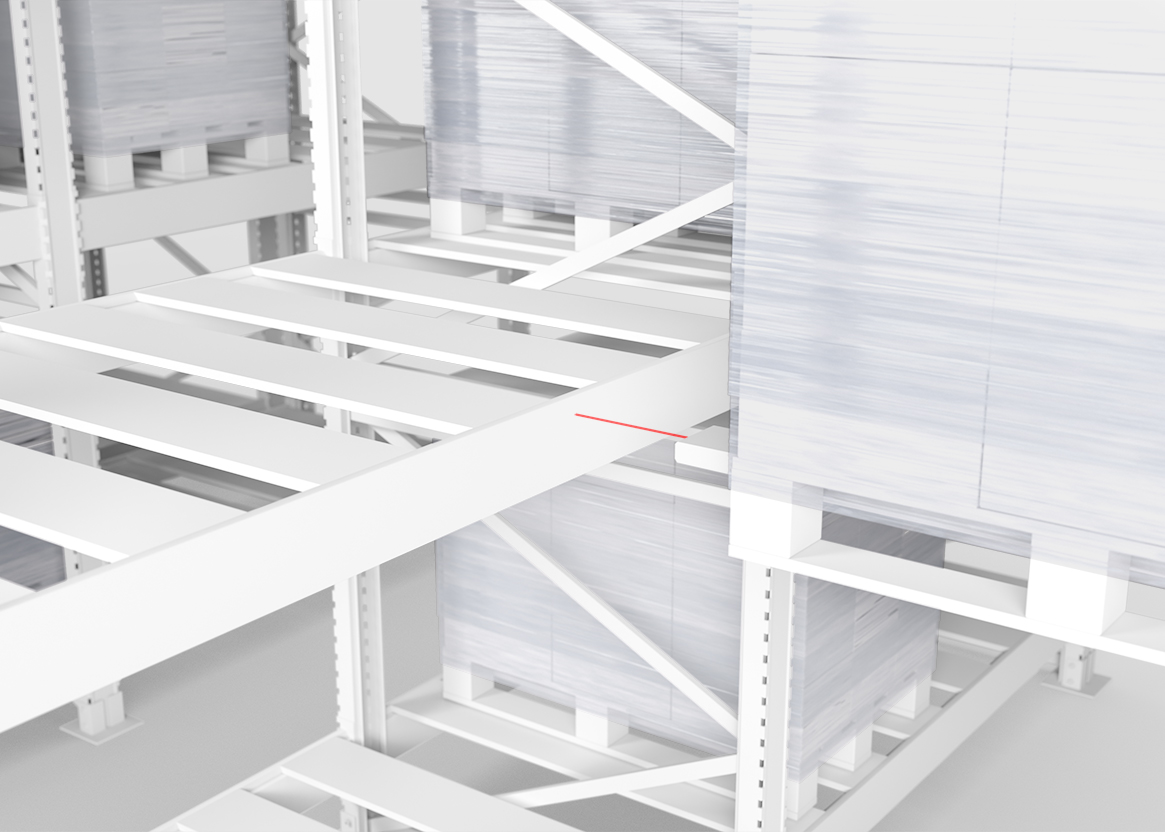
Requirement:
In order to place the pallet safely in the warehouse, the edge of the shelf rack on which the pallet is to be placed must be reliably detected.
Solution:
The HT 3C series diffuse sensors operate independently of the material and have precise switching points. Two digital switching outputs allow the same sensors to also be used for positioning the load receptacle.
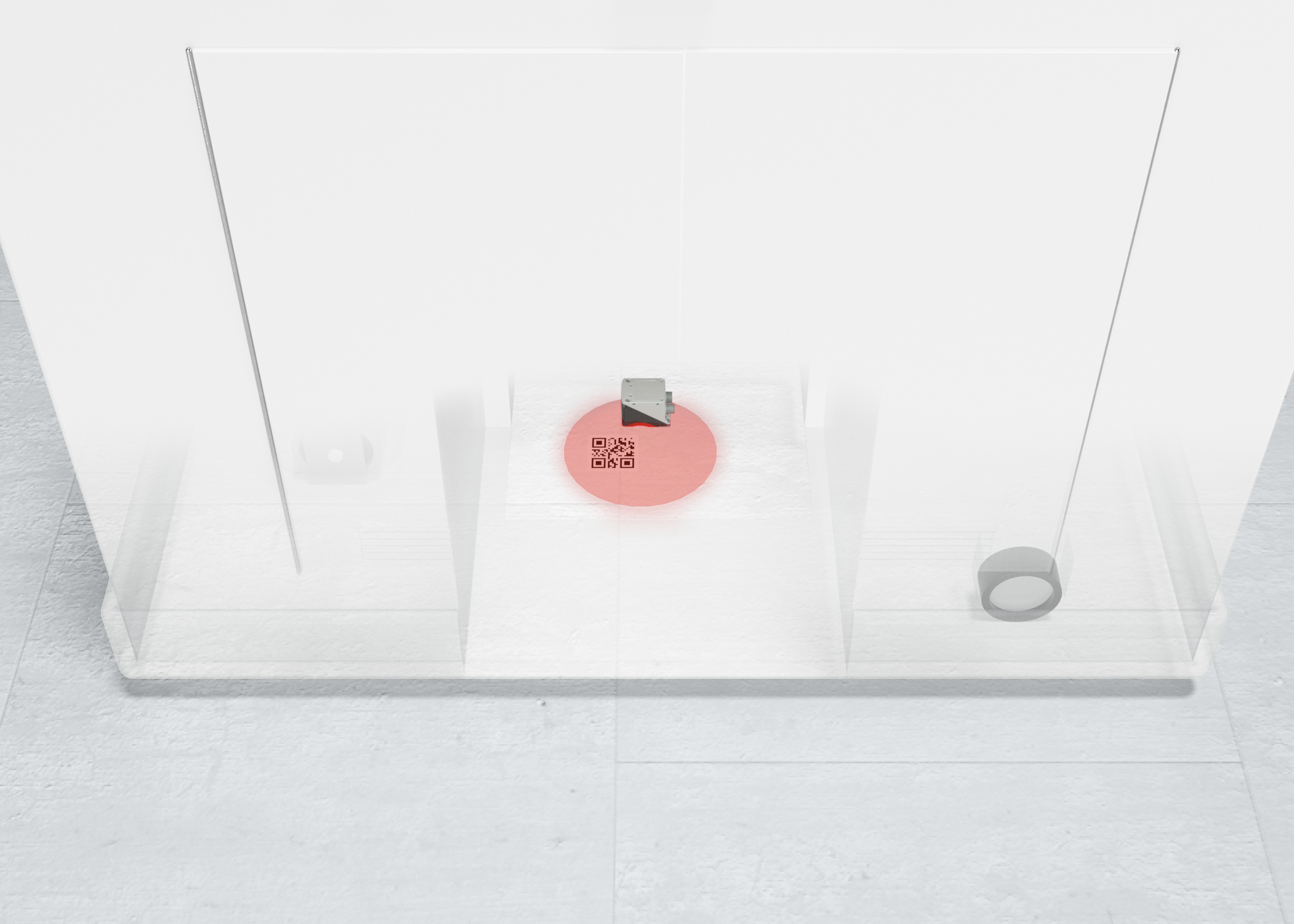
Requirement:
Labels with 2D-codes are affixed to the floor in a fixed grid. By reading the code and determining the angular position of the code in relation to the sensor, the direction of movement of the AGV should be corrected so that the next 2D-code can be approached.
Solution:
The DCR 200i 2D-code reader reads the codes as the AGV passes over them. The large working range of 40-360 mm allows flexible installation in the AGV and ensures stable operation. The integrated set-up wizard makes it quick and easy to put the devices into operation.
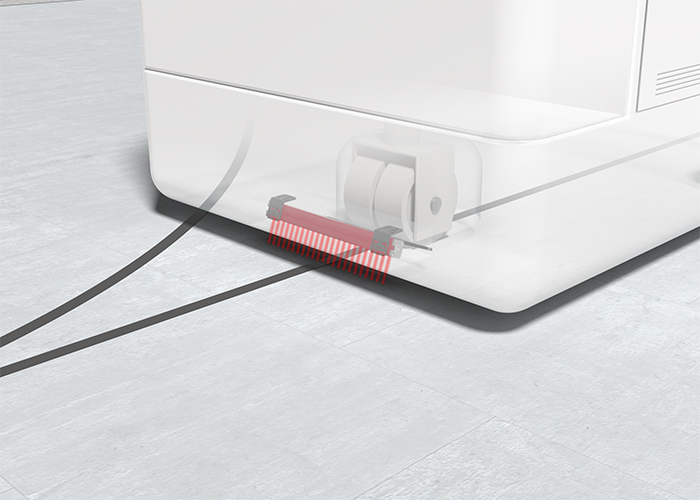
Requirement:
For fast and efficient movement, AGVs should follow a defined path marked by a trace placed on the floor. For use in flat vehicles, the sensor used should only require a low installation height.
Solution:
The OGS 600 optical guidance sensor detects the trace by means of edge detection and sends corresponding signals to the control. The devices work particularly reliably in combination with our optimized OTB trace tapes. Since the minimum distance from the floor is only 10 mm, the OGS 600 can be integrated into the AGV to save space.
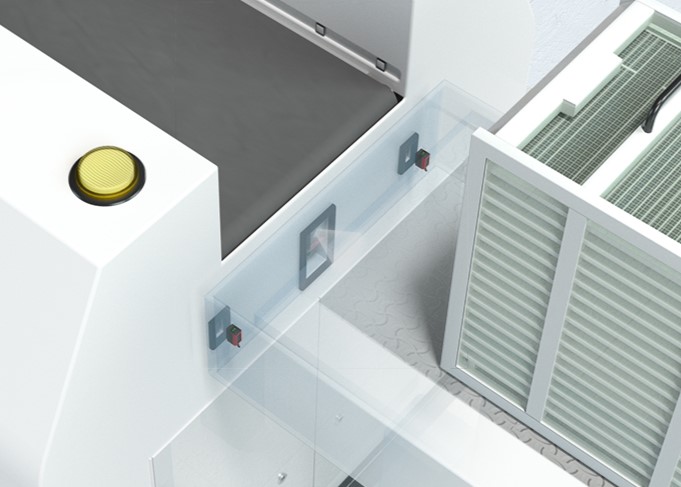
Requirement:
The conveyor on the AGV should be activated by the transfer station in the required direction of movement without contact.
Solution:
The cost-effective series 5 throughbeam photoelectric sensors transmit the switching information to the AGV. The devices are insensitive to ambient light and are easy to align thanks to the highly visible red light.
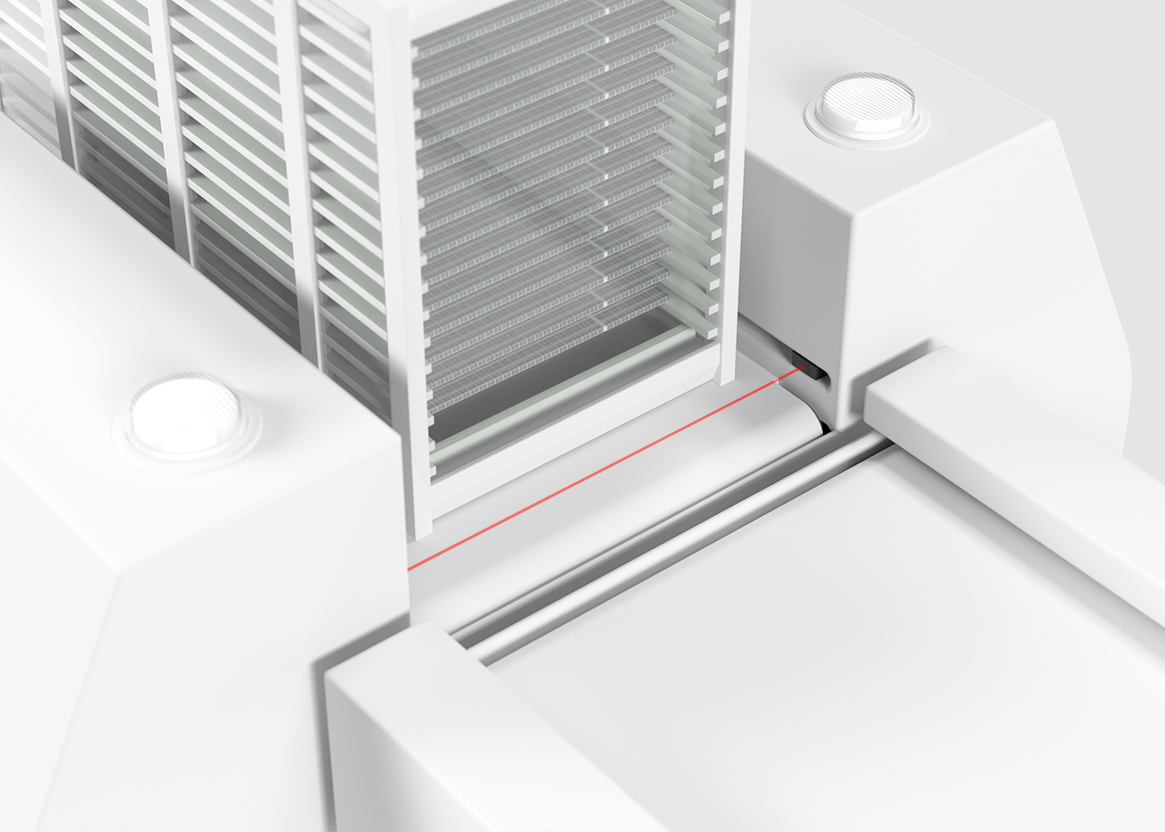
Requirement:
It should be checked whether the transport material has been transferred to the AGV completely and without overhang.
Solution:
The cost-effective series 5 retro-reflective photoelectric sensors are easy to integrate with their compact design. Due to the active ambient light suppression, the devices operate particularly reliably.
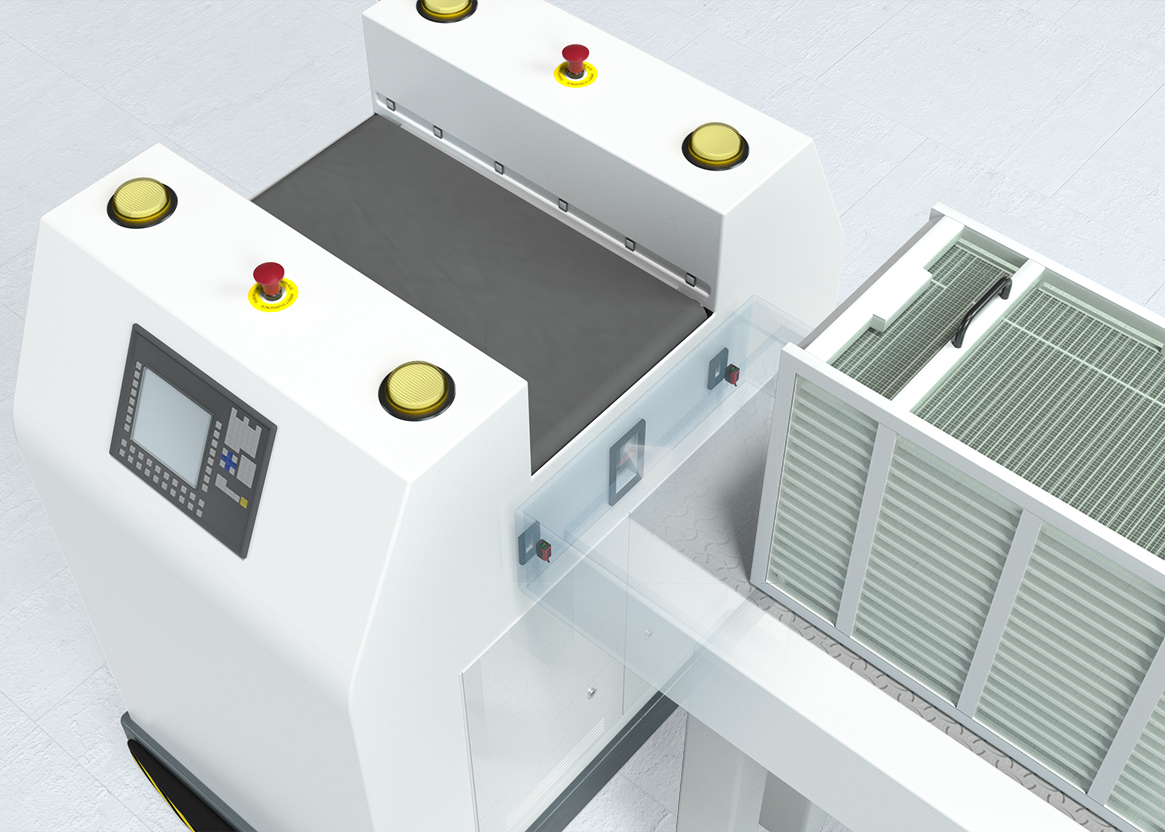
Requirement:
At the transfer station, the transported goods should be transferred without vibration. For this purpose, the AGV and/or the load receptacle must be positioned with millimeter precision.
Solution:
The IPS 200i smart camera determines its position in relation to a marker (hole or reflector) with an accuracy of up to 0.1 mm. The distance can be up to 600 mm. The results are output via an Ethernet TCP/IP, PROFINET or EtherNet/IP interface.