Sensor solutions for dairy packaging
In the case of filling and packaging milk and dairy products, the hygiene requirements on automation systems are particularly high. Furthermore, there are also large temperature differences between the operating periods and the regularly performed cleaning cycles. During the cleaning process, all components of the packaging machines must withstand high pressures and temperatures as well as aggressive cleaning agents.
In production areas where there is direct contact with the food, only sensors with stainless steel housing and plastic screens are allowed to be used. We have a wide range of products for hygiene-sensitive food packaging applications. Our stainless steel sensors of the 53C and 55C series with ECOLAB certification have been developed for challenging detection tasks. The MLC 500-IP safety light curtains in an additional protective tube are also designed for these application areas and environmental requirements. Encapsulation of the devices in a protective tube means that they achieve the high degrees of protection IP 67 and IP 69K. To safeguard doors or flaps, the L250 safety locking devices with hygienic design and the appropriate degree of protection can be used.
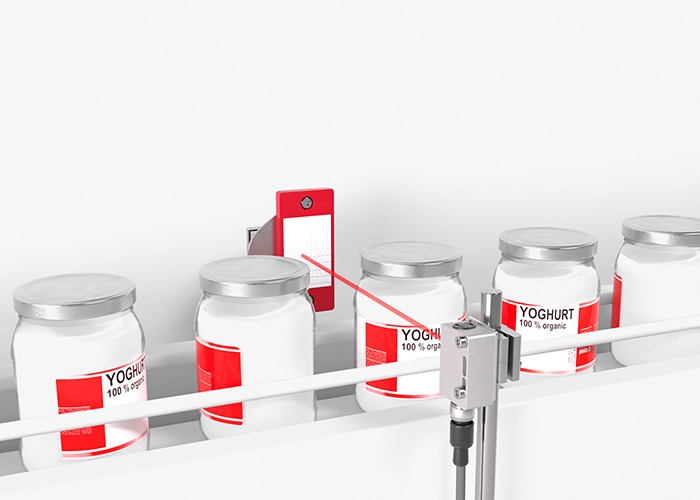
Requirement:
In a filling system for yogurt jars or milk bottles, their position on the conveyor belt is to be reliably detected. Sensors for this application must withstand the demanding environmental conditions in the clean zone.
Solution:
The PRK 55C retro-reflective photoelectric sensor reliably detects transparent containers. The sensitivity can be set via a teach button. An optional tracking function automatically compensates for soiling on the reflector or sensor. The robust stainless steel housing in wash-down design has a degree of protection IP 69K.
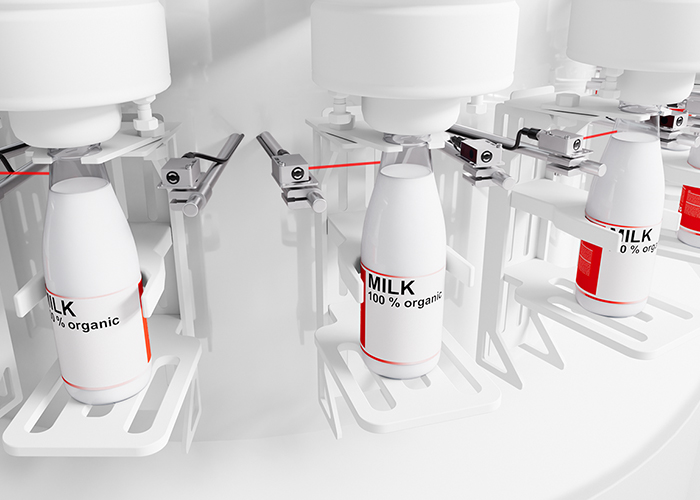
Requirement:
The fill level should be exactly the same in all bottles – underfilling of bottles must be prevented. Optical sensors can be used for reliable detection of the fill level of aqueous liquids in any container type in demanding environmental conditions.
Solution:
The LS55CI.H2O and LE55CI.H2O throughbeam photoelectric sensors are suitable for the detection of aqueous liquids due to the wavelength of the LEDs. The transmitter and receiver system of the 55C stainless-steel series in wash-down design has a high radiation capacity and also detects liquids in colored containers and containers with plastic labels.
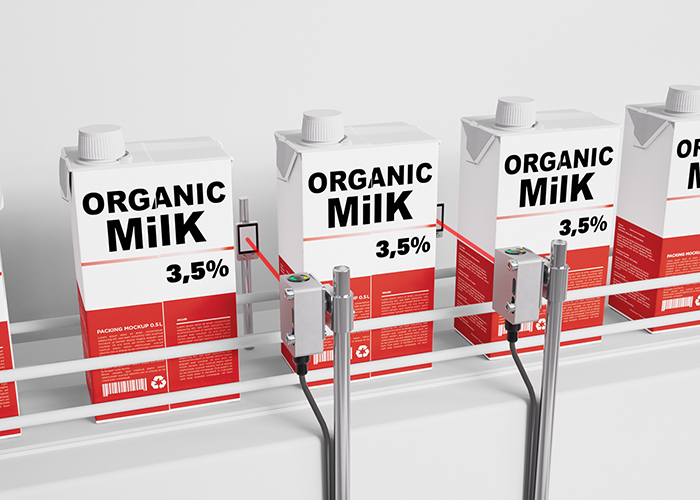
Requirement:
The flow of goods is to be detected for transport control of a single-lane transport line of soft packaging. Optical sensors can detect even the smallest gaps between soft packages.
Solution:
The PRK 55CL retro-reflective photoelectric sensor with a small laser light spot is suitable for detecting small gaps. A matching reflector in the MTKS.5 stainless steel housing is available in several sizes. The sensor and reflector are ECOLAB-certified.
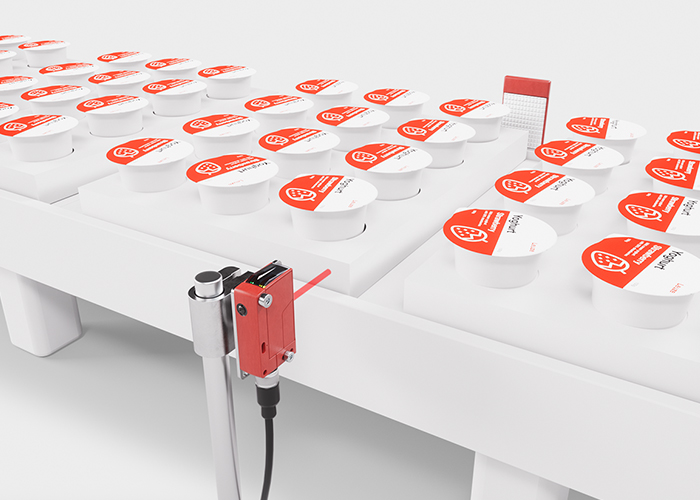
Requirement:
If identical products are combined into larger packages, they must be reliably detected independent of shape, color and surface. High-performance sensors are an important prerequisite for a high degree of automation.
Solution:
The PRK 46C retro-reflective photoelectric sensors are suitable for detecting outer packaging thanks to their high function reserve and good optical properties. The sensors have a degree of protection IP 69K and ECOLAB certification. Other models with different light spot geometries are available.
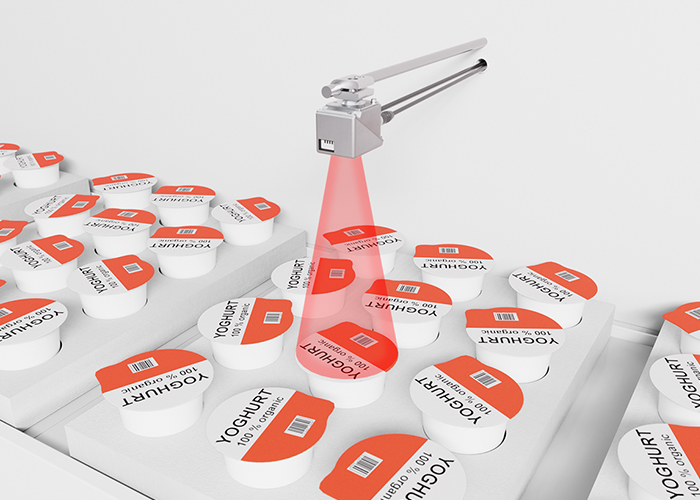
Requirement:
For process monitoring and traceability, the printed code on a bucket lid can be read with a code reader. As the orientation of the code often cannot be guaranteed, image-based code readers should be used.
Solution:
The DCR 200i code reader in a stainless steel housing is suitable for these environments thanks to various lens covers, for example made of glass or plastic. The integrated web browser and various Industrial Ethernet interfaces make the code reader flexible to use.
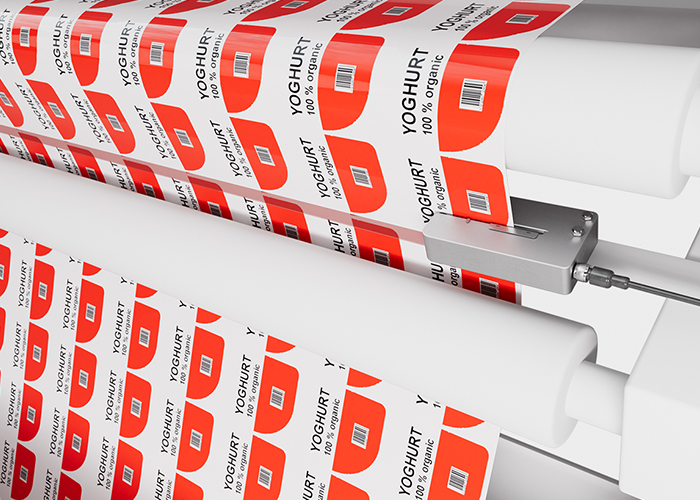
Requirement:
For a safe production process, splices in the sealing film must be detected and subsequently discharged. Detection should be as independent of colors or surfaces as possible.
Solution:
The IGSU 14E SD ultrasonic fork sensor is optimized for splice detection. The ultrasonic technology used can be applied with transparent and non-transparent material, as well as with any adhesive tapes. Adjustment to the base material is possible using a simple teach event.