IO-Link: The standard for networked factories
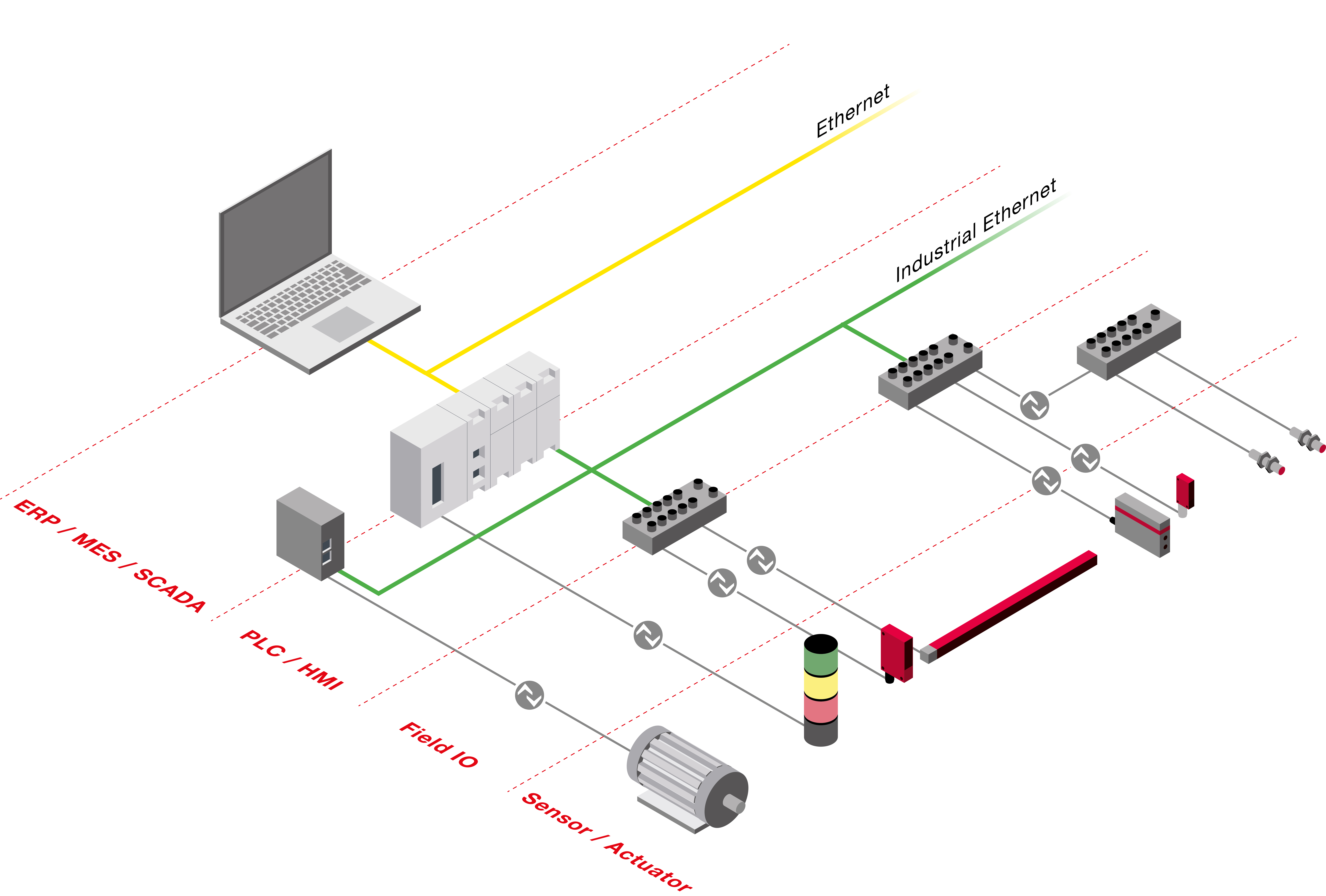
As founding member and technology developer of IO-Link, we have broad know-how and offer an extensive line of IO-Link sensors and system components such as IO-Link master and connection technology.
You always receive the latest technology – such as Smart Sensor Profile – and many sensors with additional functions as well as connection options to the cloud. With our networked solutions, you are ideally prepared for current and future requirements of the smart factory.
Your benefits with IO-Link:
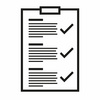
Quality assurance – Maximum process transparency
- Access to all process and diagnostic data as well as device information is ensured.
- The respective hardware and software version is available in the system documentation.
- Built-in devices are identified via the serial number.
- Recipe settings are managed via the PLC. The sensor is configured according to the requirements of the production order.
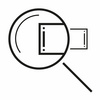
Diagnosis – Preventive maintenance
- Precise diagnostic information enables preventive maintenance and optimization of the maintenance planning.
- Data storage of the parameters is thereby automated.
- The service technician can prepare for use by means of remote diagnostics.
- The amount of work involved in troubleshooting is significantly reduced.
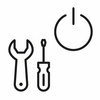
Commissioning – Device exchange made easy
- Device types and application-specific designations are visible in the higher-level systems.
- A new sensor or actuator is configured via the IO-Link master or by means of a function module.
- Configuration is also possible with just a few mouse clicks using remote access.
- Sensor settings can simply be copied and duplicated.
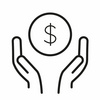
Cost savings – On all levels
- Fast project planning and commissioning saves time and money.
- Storage costs are reduced by standardizing the connection technology.
- Independent of their complexity, there is a standardized, uniform interface for all sensors and actuators, regardless of whether switching, measuring, multi-channel binary or mixed signal.
- As a complete system, IO-Link saves costs on all levels, from project planning and commissioning to repair and maintenance.
Application examples
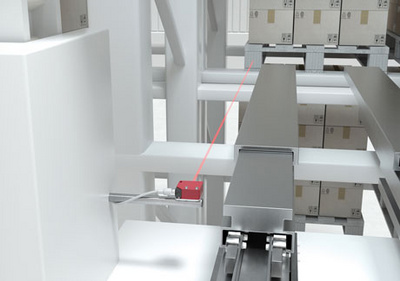
Requirement:
Before a pallet or a container is stored in a rack, it must be ensured that the rack is empty. As the telescopic arm or fork moves in, it needs to be ensured that the stored goods are not pushed in the wrong direction.
Solution:
The diffuse sensors of the HT 10, 110 and HRT 25B series also detect a wide range of pallets and containers. With their precise switching points, they can be used on nearly every stacker crane for compartment occupation checks or for push-through protection.
Advantages of IO-Link:
- Should an exchange be necessary, stored parameters of the previous device are taken over
- Improved diagnostic options via remote maintenance
- Remotely adjustable switching points
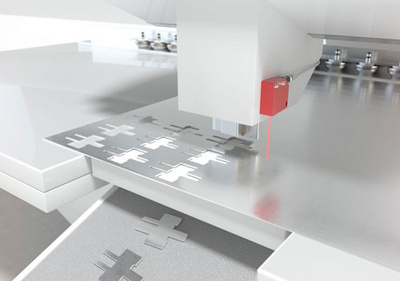
Requirement:
To ensure an optimum punching process, the material thickness must be checked. This is performed by measuring the distance to the material with high resolution.
Solution:
The ODSL 8 and ODS 9 sensors measure the distance with resolutions of up to 0.01 mm and thereby supply the basis for a high quality of this process step.
Advantages of IO-Link:
- High process transparency by signaling relevant diagnosis events
- Automatic configuration by means of IO-Link master or function module
- Process data – such as the material thickness of the sheet metal plate – is available in real time
- Measurement data is digitally transferred and processed loss-free
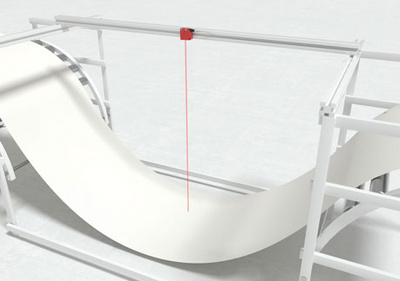
Requirement:
If, during clocked processes, raw material is fed in from coils, loop control must be performed to compensate for feed fluctuations. To do this, it is necessary to check how taut the material is tensioned. By feeding in material in a timely manner, breakage is prevented.
Solution:
The tension of the material can be monitored by measuring the sag. Due to their various light-spot geometries, the ODSL 8, ODS 10 and ODSL 96 sensors can reliably measure the sag of a wide range of different material surfaces.
Advantages of IO-Link:
- High process transparency by signaling relevant diagnosis events and measurement data in real-time
- Automatic configuration by means of IO-Link master or function module
- Optimizations using the controller or by the machine operator during the ongoing process are possible
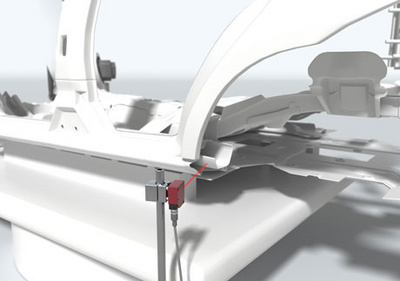
Requirement:
In automotive body shop, structure parts and different variants are to be reliably detected. The checks take place during the ongoing work process. If necessary, attachment of the sensor system must be performed outside of the robot work area.
Solution:
Our compact and switching TOF sensorsODS 110/HT 110 are the perfect solution – even in situations with limited installation space. Models ODS /HT 10 are suitable for measurement ranges over 5 m. They can also be mounted outside of the robot cells.
Advantages of IO-Link:
- When changing models or variants, new distances or switching points of the sensors are assigned by the PLC; the sensor is reconfigured depending on the parts
- Current measurement values and process data are available live
- Optimizations can be performed during the ongoing process
- Switching points can be adjusted remotely
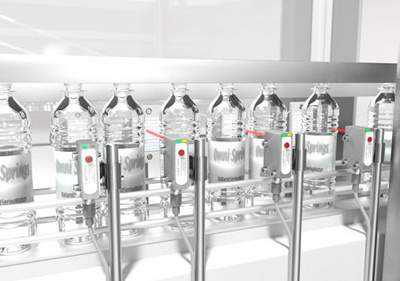
Requirement:
Transparent objects on a conveyor belt must be reliably detected during the ongoing process – even in cases of challenging environmental conditions such as fogging, water vapor or soiling.
Solution:
Through the use of a retro-reflective photoelectric sensor for transparent objects with IO-Link – such as our PRK 3C, PRK 55 or PRK 18B – environmental influences can be detected and analyzed so that the machine control can respond.
Advantages of IO-Link:
- Output of the process data in real-time by means of dual channel:
- Channel 1: fast trigger signal via the switching output
- Channel 2: configuration and monitoring via IO-Link
- Output of the actual values and of the switching thresholds for online process diagnosis
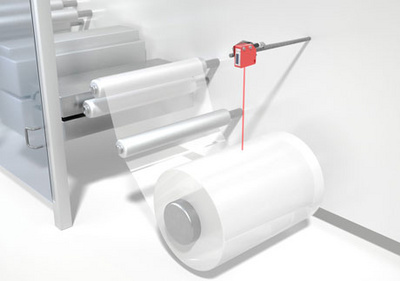
Requirement:
The diameter of a material roll is to be configured to control the tensile force and unrolling speed of the machine and to detect the time remaining before a roll needs to be changed.
Solution:
An optical or ultrasonic distance sensor – such as ODS 9 or ODS 96B – measures the distance from the sensor to the roll. The measurement values are digitally transmitted to the machine control via the IO-Link process data. No conversion of measurement values from analog to digital is necessary.
Advantages of IO-Link:
- Digital transmission of the distance values
- Switching thresholds can be used by the machine control depending on the material and surface
- Simple and fast possibility of diagnosis
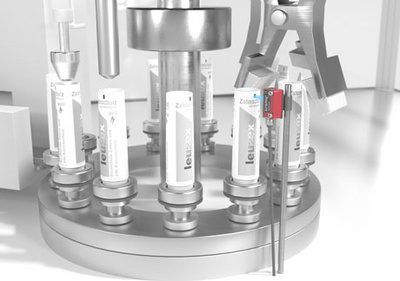
Requirement:
With the help of a contrast sensor, print marks on a product need to be detected. The print marks and backgrounds may vary from product to product.
Solution:
An optical contrast sensor – such as the KRT 3B or KRT 18B – is used that determines the optimum contrast ratios by means of multiple transmitter colors. The transmitter colors are taught in once using a teach routine and stored in the sensor or control. IO-Link can then be used to select defined and taught products from the recipe memory of the sensor or transfer them from the control. No new teach-in process is necessary.
Advantages of IO-Link:
- In the event of a product change, presettings of the recipes are taken over from the memory
- Output of the current actual values of the contrast ratios and evaluation in the machine control
- Output of the process data in real-time by means of dual channel:
- Channel 1: fast trigger signal via the switching output
- Channel 2: configuration and monitoring via IO-Link
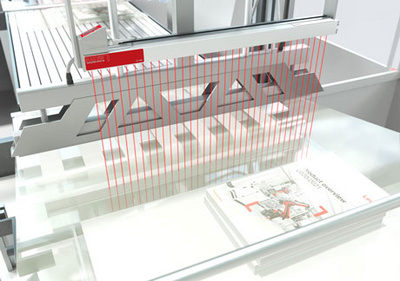
Requirement:
Objects that lie between two film webs must be detected and their width measured.
Solution:
The measuring light curtain of type CML 730 with power setting transilluminates the only partially transparent films with its transmitter that has been set to high power. The number and position of the interrupted beams is output to the machine control via the IO-Link interface. Preset, material-dependent beam parameters can be output to the light curtain via IO-Link.
Advantages of IO-Link:
- Fast output of all beam data
- Presettings possible via recipe management
- Simple possibility of diagnosis