Sensor solutions for beverage filling
Beverage filling systems fill glass bottles, cans and PET containers in highly automated processes and at an impressive speed. Apart from speed, the reliability and maximum availability of the system are also of key importance. As market leaders for sensor systems used in beverage filling, we offer solutions for all applications along this process chain – from filling, labeling and packaging to palletizing and shipping.
The applications are as diverse as our sensor product range, which is tailored to these applications. The precise retro-reflective photoelectric sensors of the PRK 18B series are our specialists for the challenging task of detecting transparent media. A special tracking function integrated in the sensors compensates for any contamination that may occur and increases the availability of your systems. The stainless steel sensors of the 53C and 55C series are characterized by a hygienic design as well as a high degree of resistance against cleaning agents and robustness to large temperature fluctuations. The LS55C.H2O water sensor reliably detects all aqueous liquids in many different types of container. These compact stainless steel sensors meet the high protection class IP 69K and have ECOLAB certification.
3 Guarding of points of operation during bottle cleaning
5 Bottle detection in transfer star
6 Fill level detection when filling
8 Presence control of bottle caps
10 Monitoring of doors and flaps
13 Bottle detection during transport
14 Fill level detection in mass transport
15 Position detection in mass flow
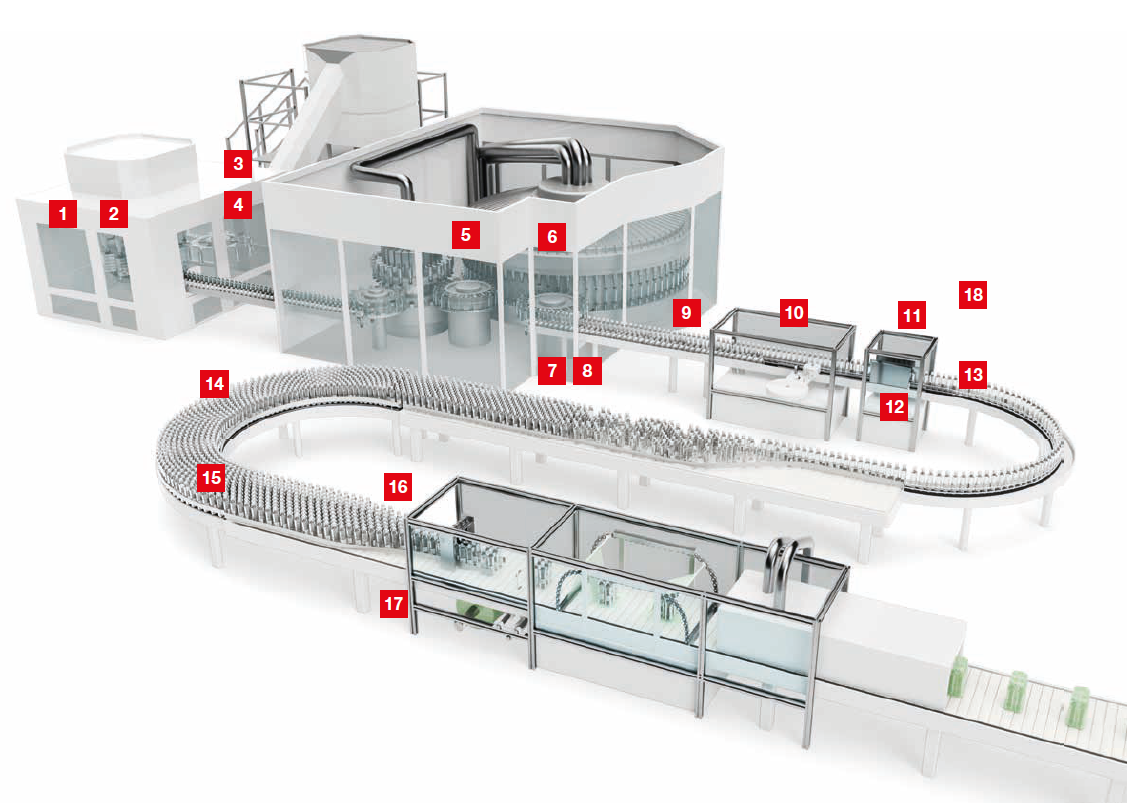
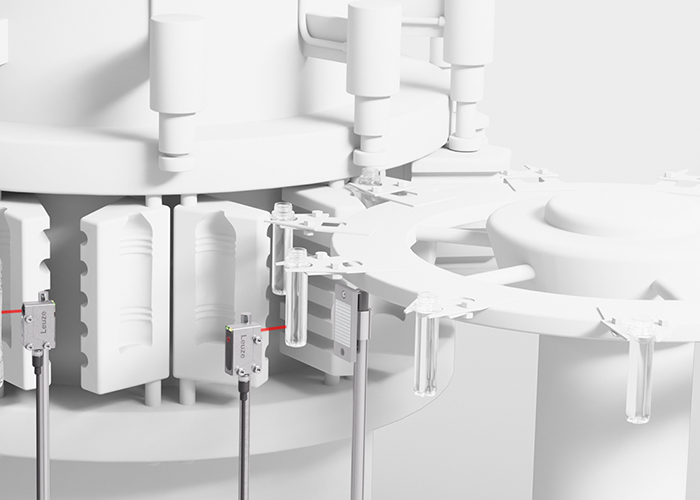
Requirement:
PET bottles are blown from preforms in filling systems for plastic bottles. For this purpose, the transparent preform must be detected on the feed to the stretch blow molding machine.
Solution:
The retro-reflective photoelectric sensors of the 25C, 55C and 18B series with autocollimation reliably detect transparent objects. They are ideally suited for detection tasks on stretch blow molding machines, as they can compensate for temperature fluctuations and contamination.
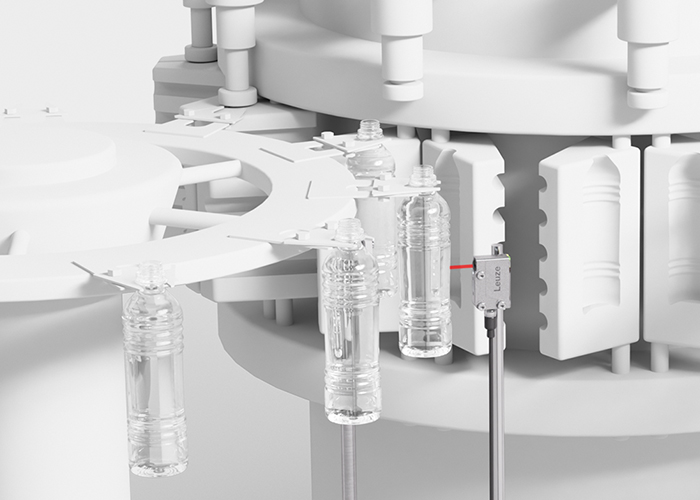
Requirement:
After the preform has been heated and blown into the mold, the now very thin and highly transparent PET bottle must be detected by the sensor with an extremely high level of reliability. This is the only way to ensure fault-free operation of the stretch blow molding machine.
Solution:
The PRK 55C and PRK 18B retro-reflective photoelectric sensors with polarization filter are specially developed for the detection of highly transparent bottles. Temperature and contamination compensation offsets environmental influences. In this way, the sensors enable the machine to be operated over long periods without unplanned maintenance stoppages.

Requirement:
Machine openings ensure good accessibility to the system. The points of operation must be secured with optical protective devices during operation. Even in harsh environments, such as bottle cleaning machines.
Solution:
The MLC 500 safety light curtains are a flexible solution for guarding machine openings. They are available with a resolution from 14 mm and in protective field lengths up to 3,000 mm. For demanding environments, the models with a degree of protection IP 69K in an encapsulated protection tube are suitable.
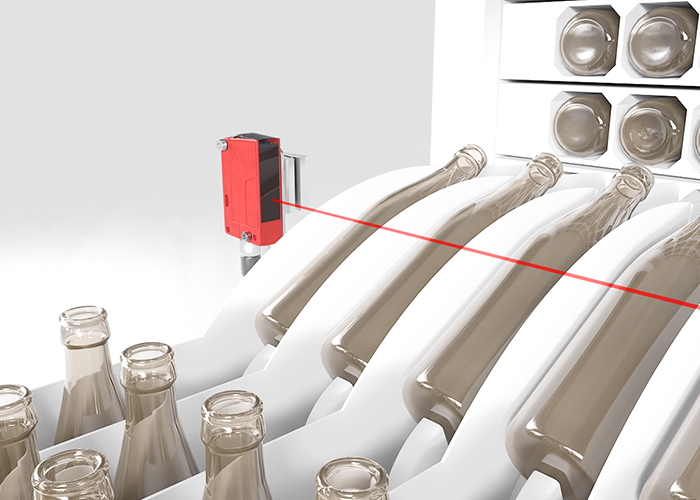
Requirement:
Reusable bottles are conveyed via mass transport to the bottle cleaning machine, where they are separated into aisles. They are then automatically inserted into the cleaning cells via a gripper system. Sensors are used to detect potential collisions or "bouncing" bottles.
Solution:
The PRK 46C retro-reflective photoelectric sensors in a plastic housing with degree of protection IP 69K are equipped with a high function reserve for this application. The special light-spot geometry reacts only to bottles, not to splashes, thus ensuring high availability.
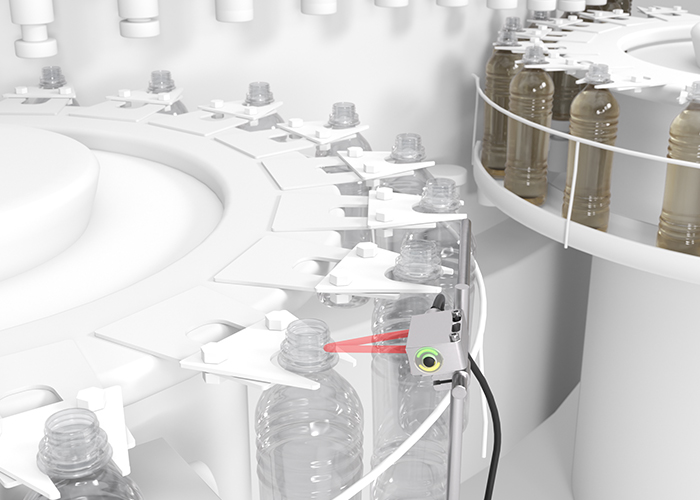
Requirement:
Bottle filling is characterized by very high speeds. For a smooth process, it must be ensured prior to filling that all positions of the transfer star are occupied with bottles.
Solution:
The HT55C diffuse sensor with background suppression reliably detects bottles during the filling process and does so without reflectors. ECOLAB certification and the enhanced Leuze cleaning agent long-term test CleanProof+ ensure the functionality of the sensor in wet areas and during intensive cleaning processes.
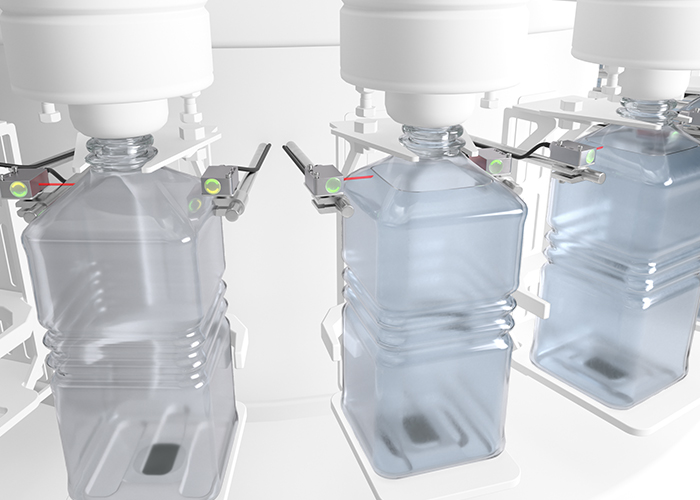
Requirement:
Water is filled into containers in a filling machine. The fill level must be exactly the same in all containers – underfilling should be prevented.
Solution:
The LS / LE55CI.H2O throughbeam photoelectric sensors are developed for the detection of aqueous liquids and for fill-level monitoring. The transmitter and receiver system of the stainless steel 55C series in wash-down design has a high radiation capacity and is also used with non-transparent containers and containers with plastic labels.
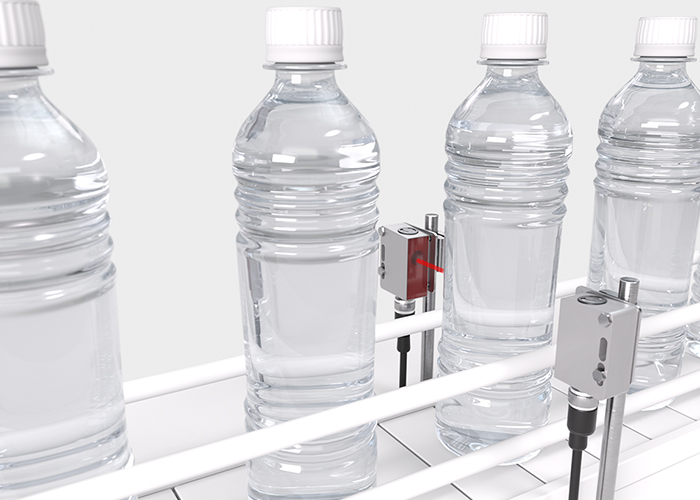
Requirement:
After the filling process, empty bottles must be detected in order to recognize leaks in PET or glass bottles. This becomes particularly challenging when a clear liquid is in a non-transparent container.
Solution:
The LS / LE55CI.H2O throughbeam photoelectric sensor is developed with an optimum wavelength for detecting aqueous liquids in transparent or opaque containers. During the filling process, the cleaning and environmental requirements are high, which is why the sensors are designed in stainless steel housings with a degree of protection IP 69K.
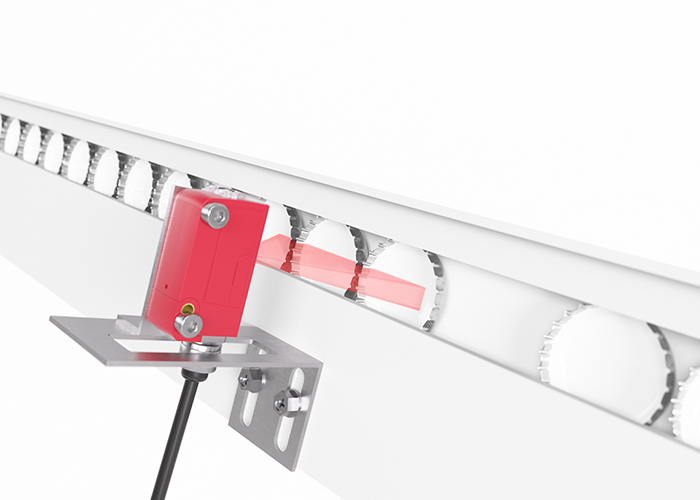
Requirement:
After the filling process, the bottles are automatically sealed with screw caps or crown caps. For a continuous production process, the presence of the bottle caps in the feeder must be checked. A reflector cannot always be attached here.
Solution:
Presence control can be solved with retro-reflective photoelectric sensors such as the PRK 3C. If no reflector can be attached, a diffuse sensor with a long light spot, such as the HT3C.XL, is suitable for interrupted and irregular objects. For the detection of crown caps, an IS 200 inductive sensor can be used alternatively.
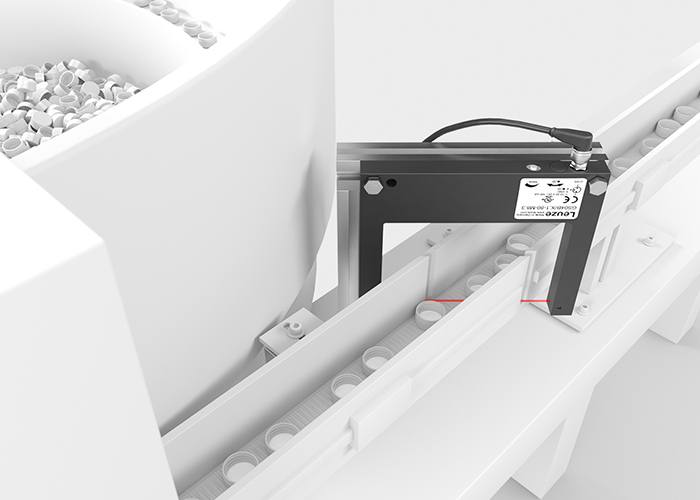
Requirement:
In filling and sealing machines, individual bottle caps in the cover feed must be reliably detected on their way to the capping machine.
Solution:
The GS 04B and GS 08B fork photoelectric sensors are ideal for detecting small parts. As the transmitter and receiver are located in one device, the compact solution can be integrated easily and without alignment work. The sensors are positioned horizontally to the feed, so each cap interrupts the light beam.
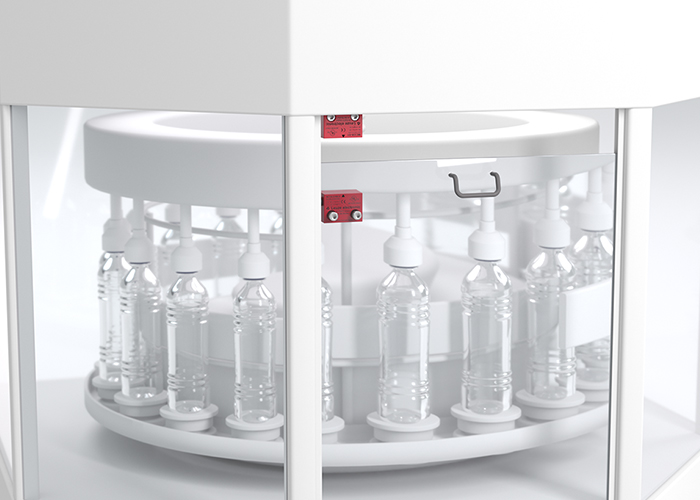
Requirement:
Doors or flaps are often required on machines, for example to change consumables or to clean the machine. These must be closed during operation. To prevent hazards, the closing state must be monitored in terms of safety.
Solution:
The magnetically coded MC 300 safety proximity sensors monitor doors and flaps. Owing to their enclosed design and contact-free operating principle, they are ideal for use in harsh and damp environments. With their cubic and cylindrical designs, the devices are also easy to integrate.
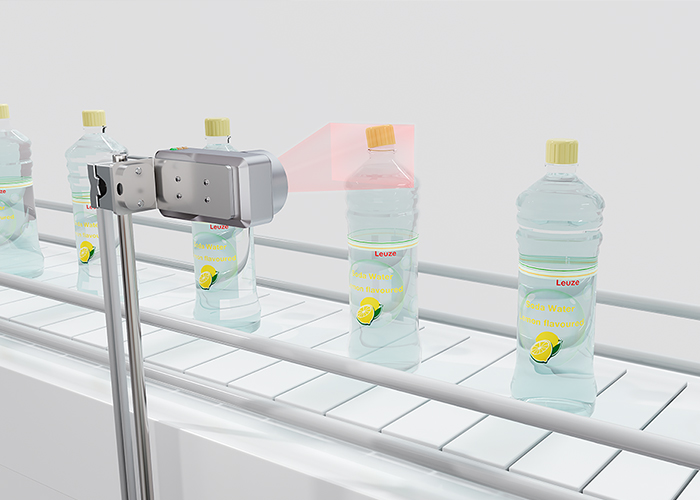
Requirement:
After the bottles have been sealed, the fit of the cap is checked at a test station. Only correctly fitted caps ensure a proper sealing of the bottle.
Solution:
With its extensive tool set, the IVS 1048i Simple Vision sensor can determine whether the bottle cap is sealed correctly. A user-friendly, graphical interface ensures fast setup and smooth operation of the sensor.
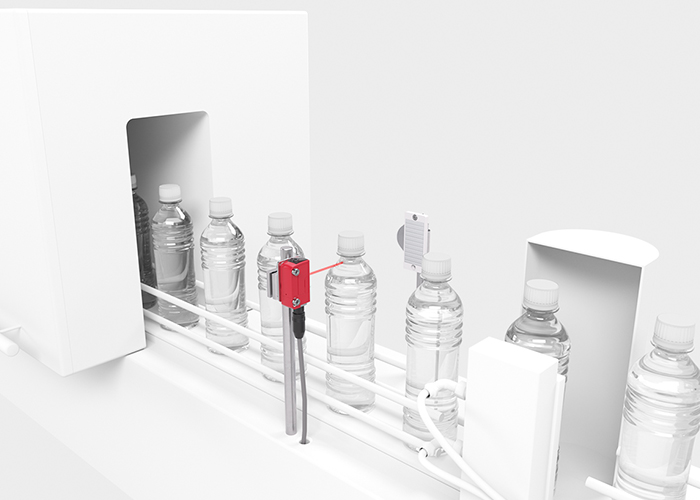
Requirement:
In the fast processes of beverage filling, it is important to detect containers as precisely as possible. For inspection machines, the camera must be triggered with position accuracy. This requires sensors with short response times and focused, aligned light spots.
Solution:
Retro-reflective photoelectric sensors with laser light in plastic housing (PRK 3CL series) or in metal housings (PRK 55CL or PRK 18B) enable precise triggering with very low jitter.
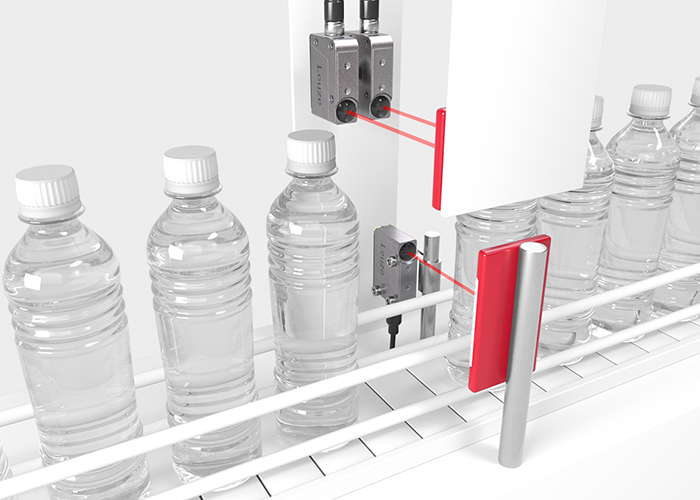
Requirement:
For the subsequent filling process, the bottles must be spaced apart to prevent them from colliding and thus causing noise pollution. In the transport line there are short conveyor sections where sensors detect the position of the transparent bottles.
Solution:
The PRK 18B and PRK 55 retro-reflective photoelectric sensors feature a focused light spot and autocollimation (to detect small signal differences) for long-term fault-free operation. The PRK5.R with special reflector is available as an entry-level solution.
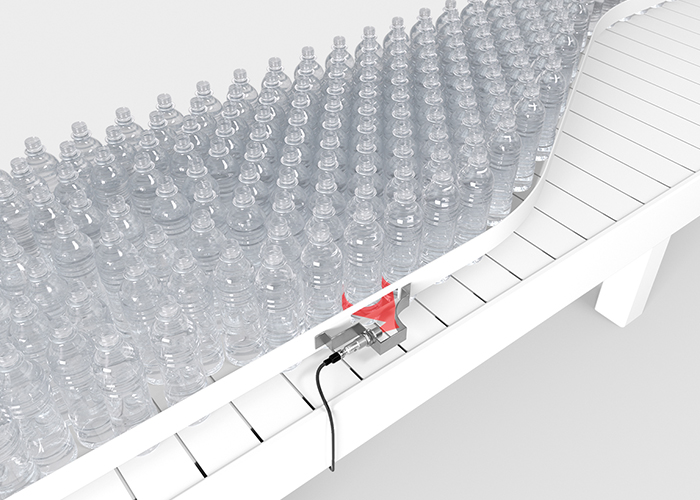
Requirement:
Containers are transported in mass flow on conveyor belts to the next station. For a continuous flow, the fill level must be monitored. To reliably detect different container sizes and shapes, a sensor with a large detection range is required.
Solution:
The robust and insensitive HTU 318 and HTU 418 ultrasonic sensors in metal or plastic housings with a large detection lobe and one or two switching points that can be set independently via IO-Link are ideally suited for changing container formats or colors.
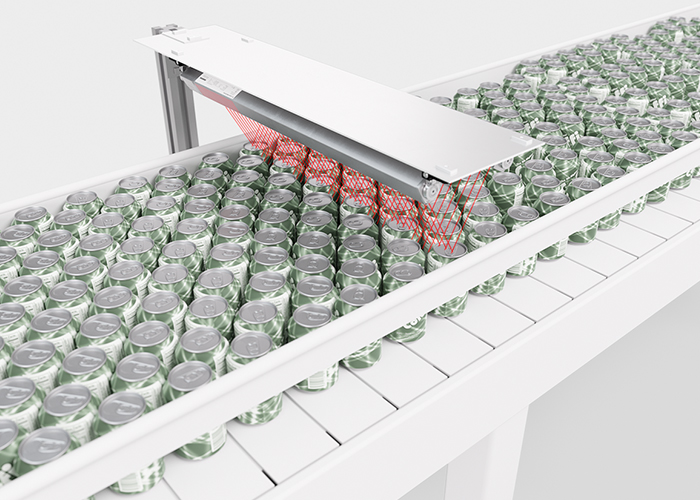
Requirement:
To detect interferences in the mass flow, a uniform profile of the surfaces can be made from above. Gaps, for example caused by fallen cans, must be reliably detected.
Solution:
The CML 700 light curtain in V-configuration is developed for measuring moving objects that pass and detects interferences across the entire measurement width. As defects do not reflect light from the transmitter to the receiver, the sensor detects them immediately. Various interfaces are available.
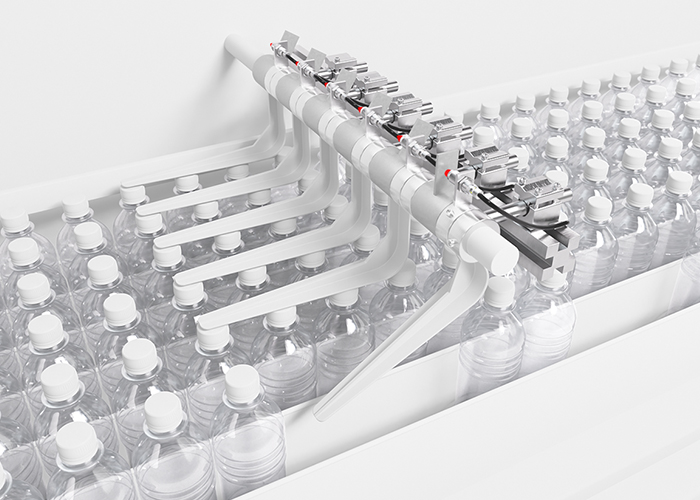
Requirement:
Gaps should be avoided for aisle control in the feed to the package formation. For this purpose, the containers are lined up in aisles and stowed at suitable locations. A gap that occurs must be detected and eliminated via the conveyor control system.
Solution:
A simple solution is provided by mechanical brackets in conjunction with sensors for end position detection. The final position can be detected by an inductive sensor, e.g. IS 218 or IS 212 in metal or stainless steel housings, via metal arms on the plastic brackets.
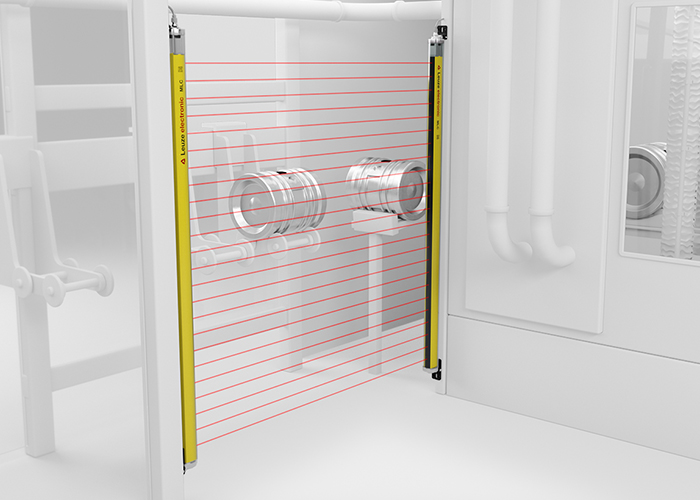
Requirement:
In a cleaning system for barrels and KEGS, there are access points for manual intervention. Safety sensors with a high IP degree of protection are required to safeguard the points of operation.
Solution:
The MLC 500-IP safety light curtains safeguard points of operation in hygiene-sensitive areas and have the highest degree of protection IP 69K. For this purpose, the light curtains are mounted in a transparent and encapsulated tube. Different resolutions and protective field lengths offer optimal adaptation to the application.
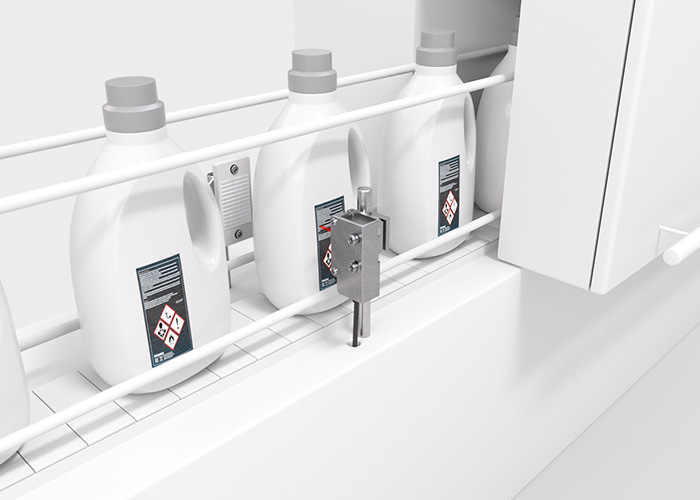
Requirement:
When filling potentially explosive materials, such as highly volatile substances or dusts, specially protected sensors must be used. Optical sensors need ATEX certification in hazardous areas.
Solution:
The PRK 55 Ex retro-reflective photoelectric sensor in combination with a reflector is a reliable solution for position detection in potentially explosive zones. 55 Ex series sensors are suitable for Ex-zone 2 (gas) or 22 (dust) environments.