Press line
Made from massive steel rolls – known as coils – molded parts, such as car body parts, are produced in various work steps. Whether for cutting the coils or punching, pressing and shaping the blanks: our sensors accompany and safeguard all manufacturing steps, even under harsh environmental conditions.
The applications are as diverse as our product range, which is tailored to these applications. Our inductive and optical sensors check and monitor the presence and position of parts. Our identification systems record data to ensure the traceability of those parts. And at the cutting systems, our sensors supply measurement values for loop control and edge control.
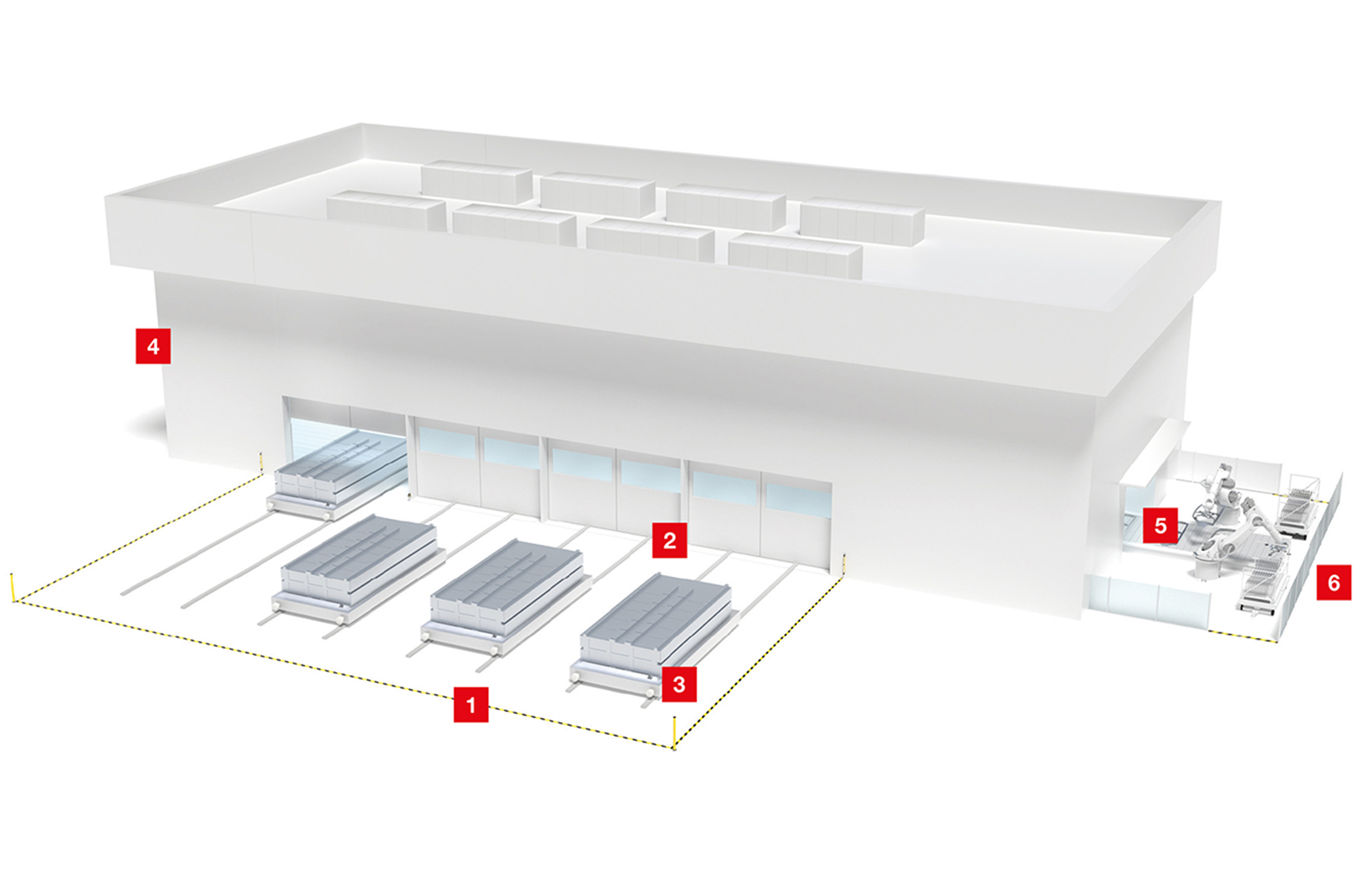