Sensor solutions for shuttles
Shuttles are compact warehouse vehicles for automatic operation of high-bay warehouses. They are used in parallel and move largely independently in the rack construction. The dynamic shuttles are tasked with transporting the goods safely, reliably identify open spaces, and avoid collisions.
Our sensors are optimized for this area of application and assume tasks in the compartment fine positioning, compartment occupation check and presence control. Sensors switching within milliseconds ensure optimum positioning. Even in low vehicles, our space-saving sensors can be easily integrated, allowing flexible design. All our sensors are designed to be user-friendly, ensuring fast mounting and commissioning.
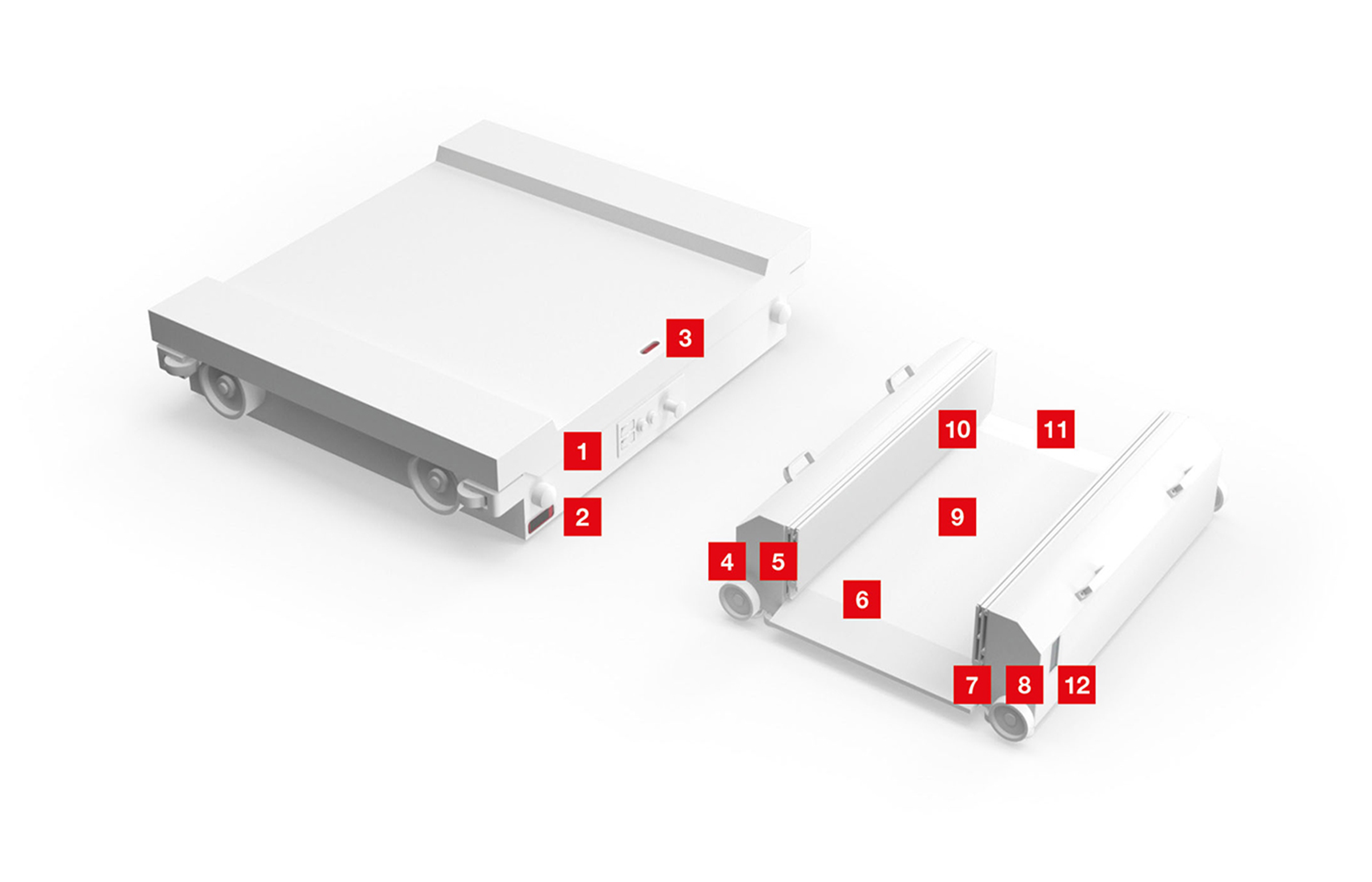