Optical sensors
33C/ 35C Series
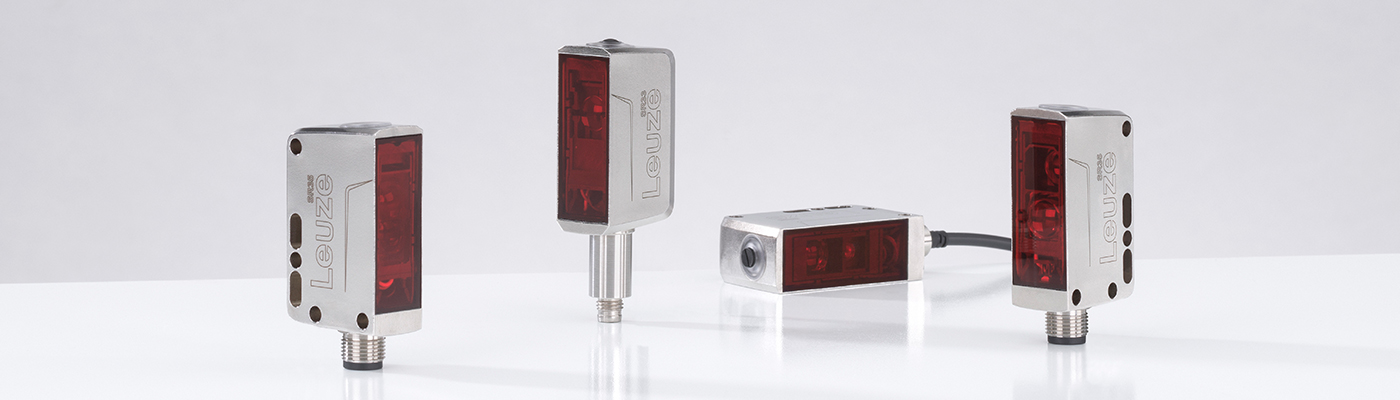
Robust and hygienic: On the safe side with stainless steel sensors
Largest selection of photoelectric sensors in stainless steel housings
To ensure stable and economical production and packaging processes, the sensors used in the system must function reliably and be available in the long term. In hygiene-sensitive or wet environments, as well as in a harsh production environment, sensors in stainless steel housings are the perfect choice. They are characterized by high resistance to moisture, cleaning agents, temperature fluctuations, dust, chips or vibrations, as well as mechanical loads.
Discover our new sensor portfolio of the 33C series in hygienic design and the 35C series in robust wash-down design. The two full series in stainless steel housings with photoelectric proximity sensors, through-beam and retro-reflective photoelectric sensors also include many specialized sensors for particularly demanding applications. With the extensive portfolio with different light sources (Power PinPoint LED, laser, infrared), light spot geometries and connection types, applications in packaging systems, in machine tools or in the automotive industry can be solved reliably and economically.
33C series: Specialist for hygienic processes in the food industry
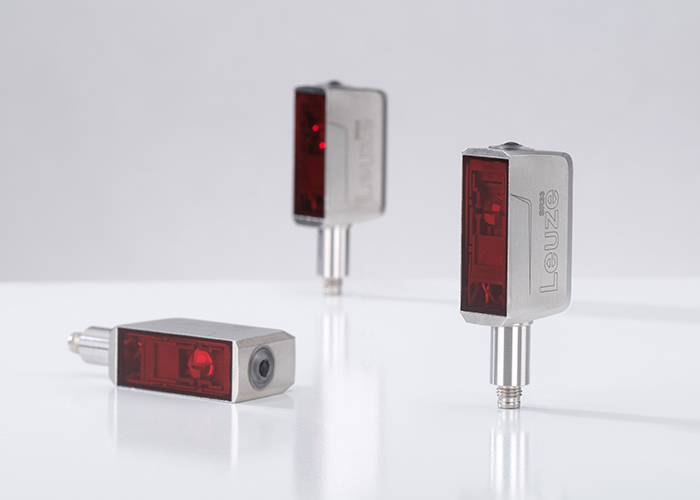
35C series: Robust all-rounder for packaging processes, the automotive industry and for machine tools
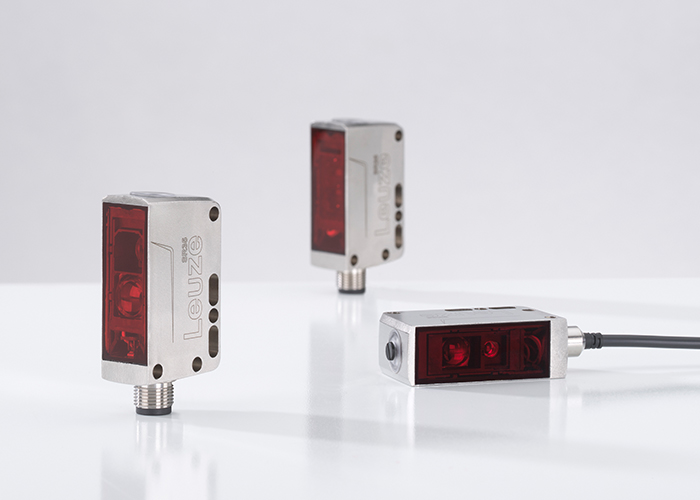
Advantages for you
- Two full series in stainless steel housings with all operating principles (proximity sensors, throughbeam sensors and reflective light barriers)
- Wide range of possible uses thanks to an extensive portfolio with many special solutions for packaging processes,
e.g. for film irradiation, clear glass detection or multi-track conveyor systems - High resistance in harsh or hygiene-sensitive areas of application
- V4A (AISI 316L) stainless steel housing with smooth surfaces (≤ 0.8 Ra) prevent product deposits and bacterial carryover
- Housing materials are approved for direct contact with food (FDA-compliant)
- High reliability thanks to extensive certifications: ECOLAB, Diversey and CleanProof+
- The IP 69K protection class confirms the tightness of the sensors
- Easy commissioning and alignment thanks to Power PinPoint LED
- IO-Link interface for quick and easy parameterization, diagnostic data and predictive maintenance
- Easy mounting: sensors in stainless steel housings do not require additional enclosures
- Everything from a single source: suitable connection cables, mounting parts and reflectors
Highlights
Stainless steel sensors: problem solvers for demanding environmental conditions
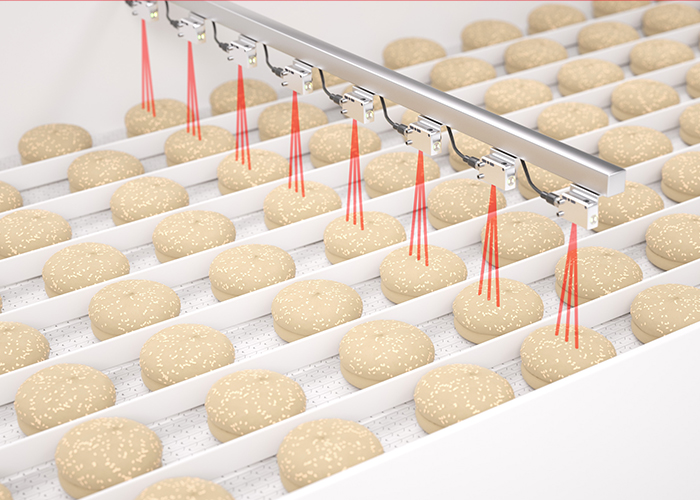
"In industry, we often see sensors with plastic housings installed in harsh environmental conditions. To ensure that they can withstand the high hygiene standards or the mechanical requirements, they are protected with a specially manufactured and structurally complex stainless steel enclosure. This is not necessary with our sensors in stainless steel housings – which saves money and effort during installation,” says Heidi Wacker, product manager at Leuze.
Harsh environments require perfectly matched solutions
Your requirements for machines and systems, as well as the appropriate sensor technology, are high: Our sensors offer you perfectly matched solutions.
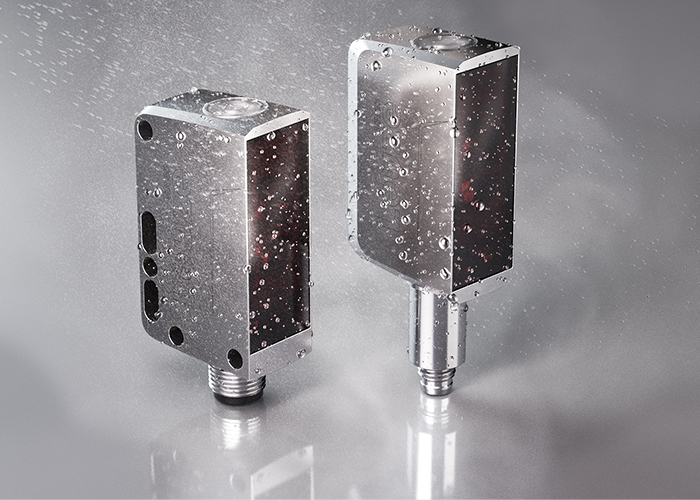
Impermeability
Systems and the sensors installed in them are very often cleaned with high-pressure cleaners. Sensors are constantly exposed to moisture and humidity due to the high number of cleaning cycles.
- Absolutely sealed housing
- Diffusion-tight materials for optical covers and operating elements
- protection classes IP 67, IP 68 and IP 69K
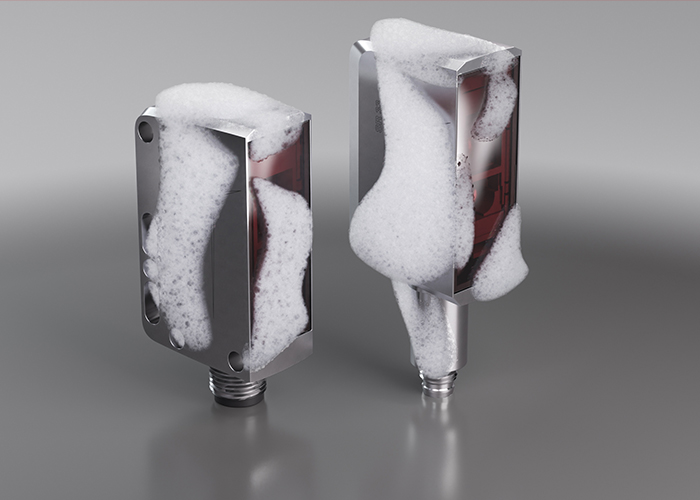
Chemical requirements
Regular cleaning cycles with foam cleaners, disinfectants, alkaline or basic cleaners require resistant sensors.
- ECOLAB certification
- Diversey certification
- Clean Proof+-certification
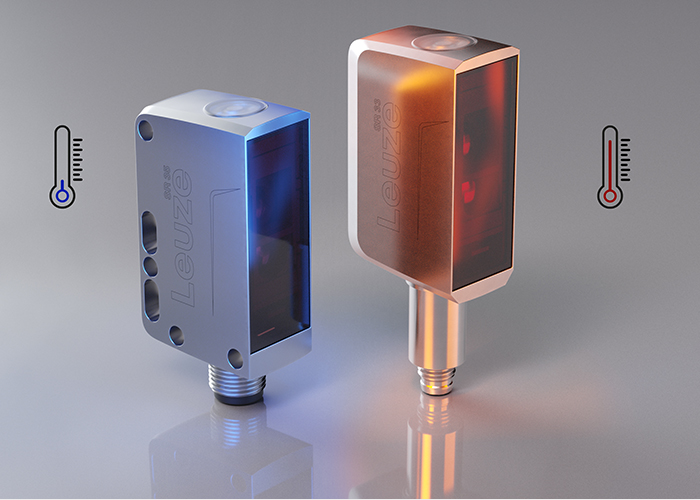
Thermal requirements
Strong temperature fluctuations between ambient temperature and cleaning temperature put a high load on sensors.
- Sensor tests in the climate cabinet
- Thermal shock tests (water bath hot-cold)
- Steam jet test as part of the IP 69K approval
- Temperature ranges from -40 °C to +70 °C
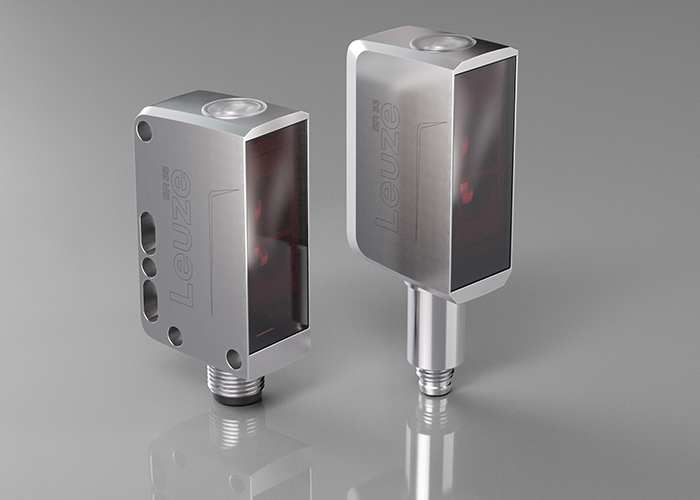
Mechanical resistance
In harsh production environments, sensors are exposed to dust, shavings, vibrations and other mechanical stresses.
- Absolutely sealed housing
- Robust housing: no additional housing necessary
- Vibration and shock resistance
To the point: Power PinPoint LED
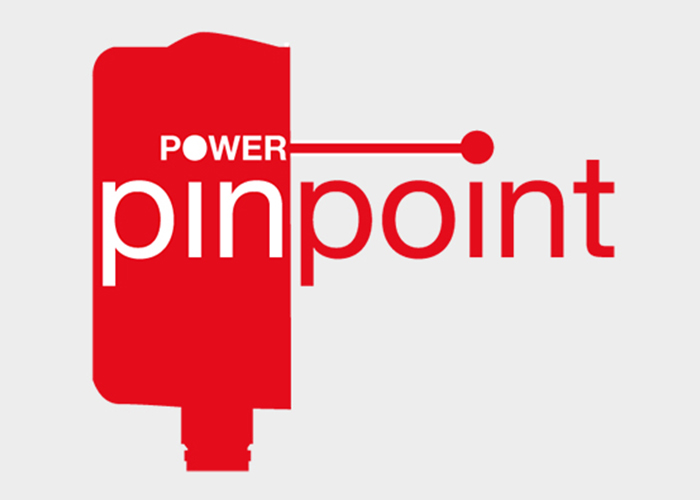
Everything from a single source: connection cables, mounting parts and reflectors
In demanding environments, not only the sensors but also the connection cables, mounting parts and reflectors must meet the high requirements. Our connection cables are approved for direct contact with food (FDA-compliant materials). The cables achieve the IP 69K degree of protection and thus withstand intensive cleaning processes with high-pressure cleaners (important: must be installed with a special tightening torque). ECOLAB certification confirms the cables' resistance to aggressive cleaning agents. The cable portfolio for use in hygienically demanding industrial areas includes M8 and M12 as well as cable lengths of 2, 5 and 10 meters.
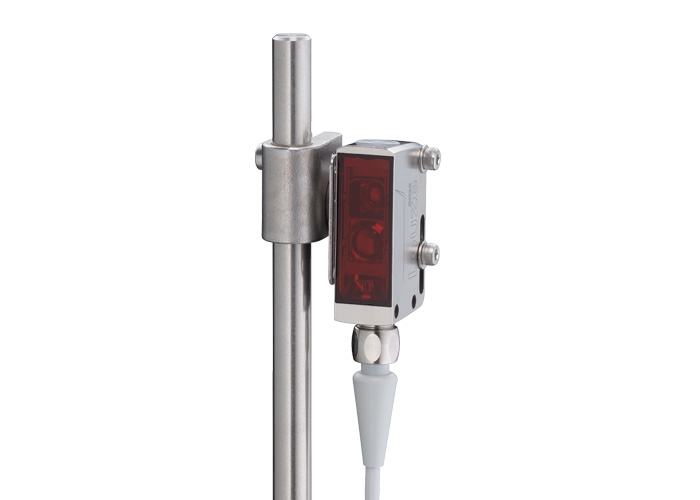
Reflectors
Just how reliably retro-reflective photoelectric sensors can detect depends upon the selected reflector, among other things. We offer reflectors with plastic or stainless steel housings as well as reflective tapes for different requirements: Reflectors in the advanced segment are often used in the food and pharmaceutical industry on account of their resistance against cleaning agents. The Solidchem reflectors made of chemically resistant plastic also stand out for their high temperature resistance. The reflectors from the extended segment are suitable for production areas with high air humidity or large differences in temperature.
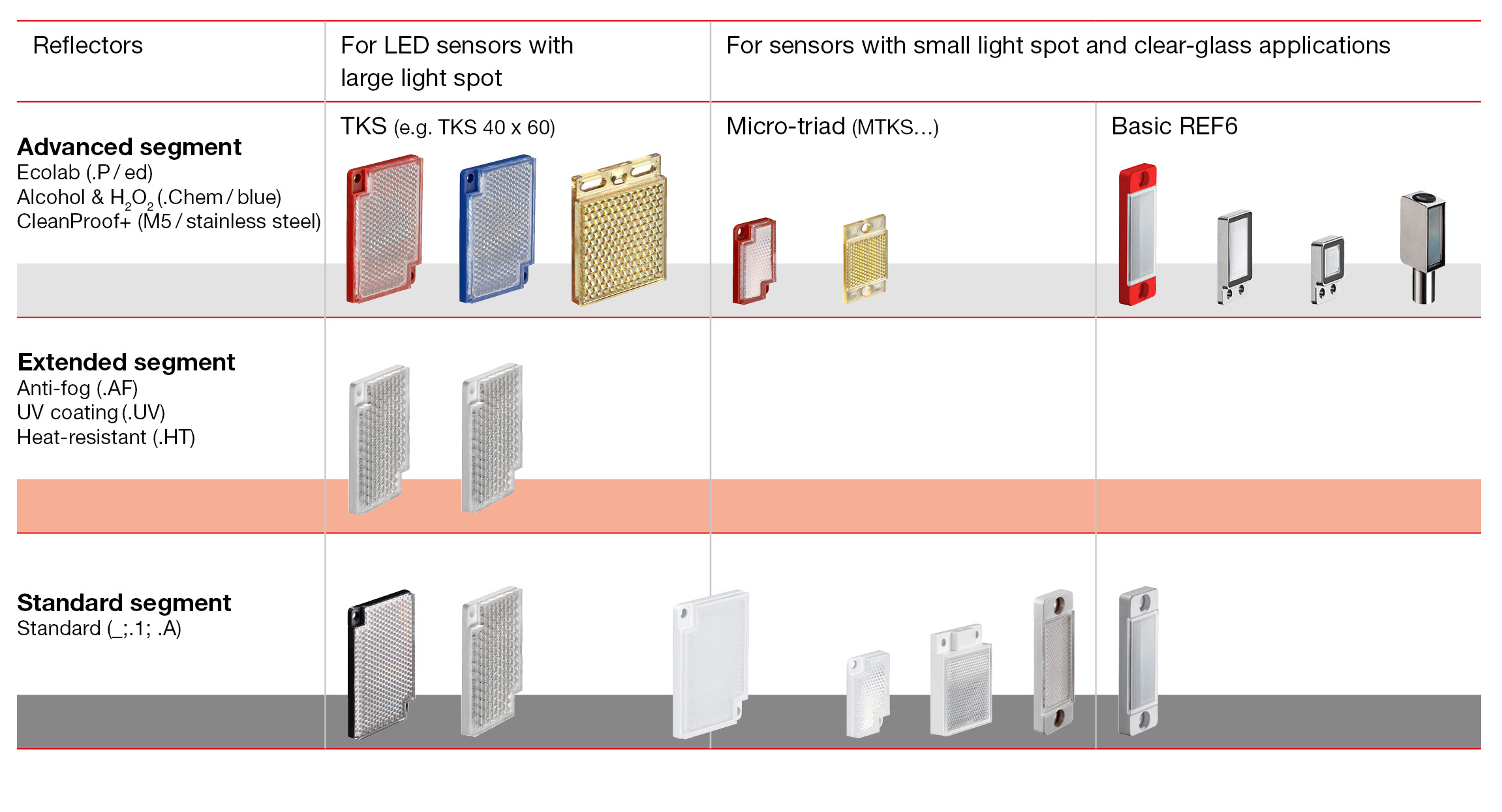
Applications
The 33C and 35C sensor series are designed to cover a wide range of applications in food packaging. Using stainless steel sensors in process steps reduces the complexity of the system and ensures that you are always on the safe side. In packaging areas where products are still unpackaged, the 33C series sensors are a reliable solution. The 35C series variants are suitable as robust all-rounders that can withstand intensive cleaning cycles and mechanical loads. Light scanners, through-beam photoelectric sensors and reflection light barriers are available in both series. The range is complemented by special operating principles designed for the food packaging industry.
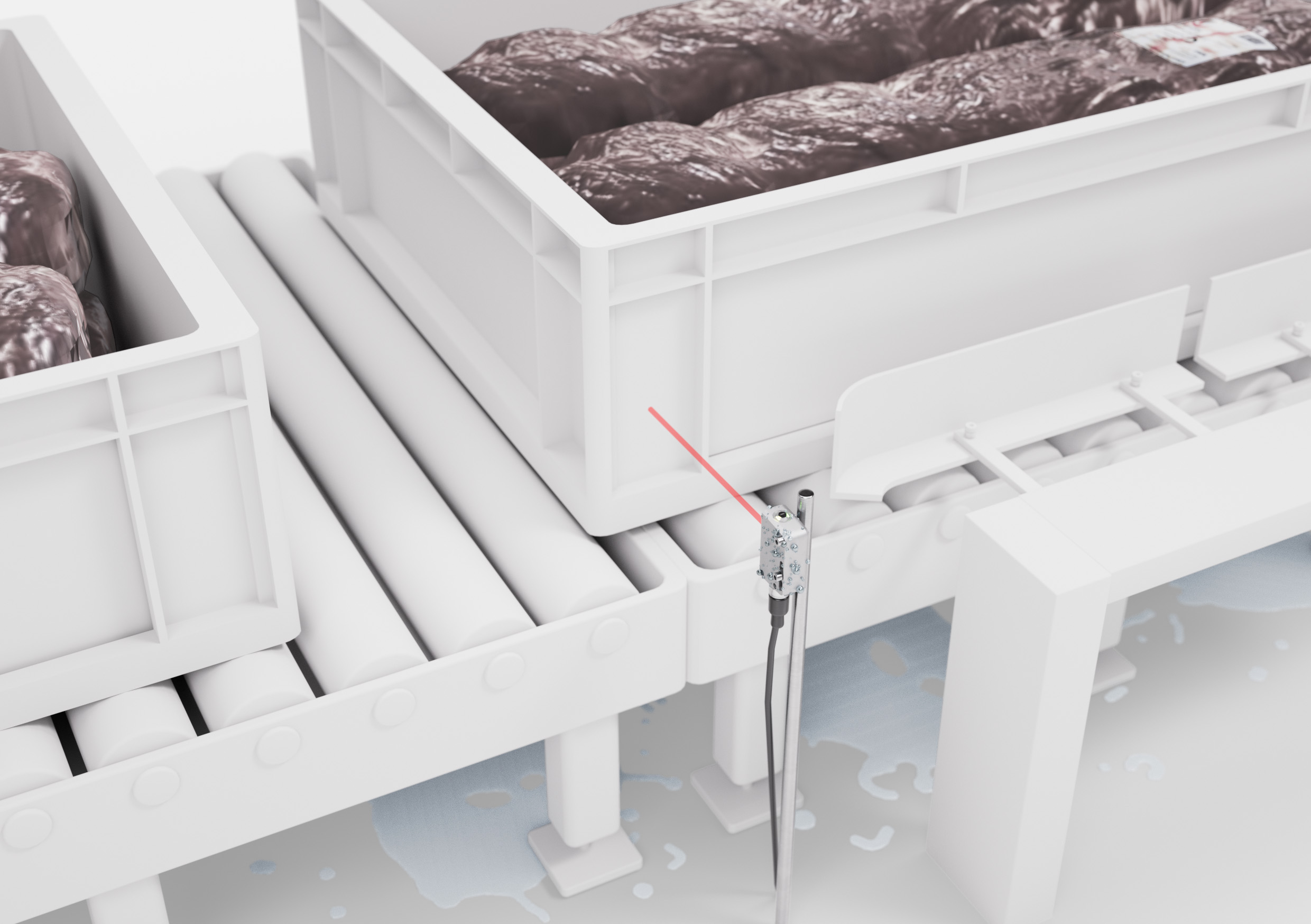
Detection of boxes in food conveyor technology
Requirement:
Solution:
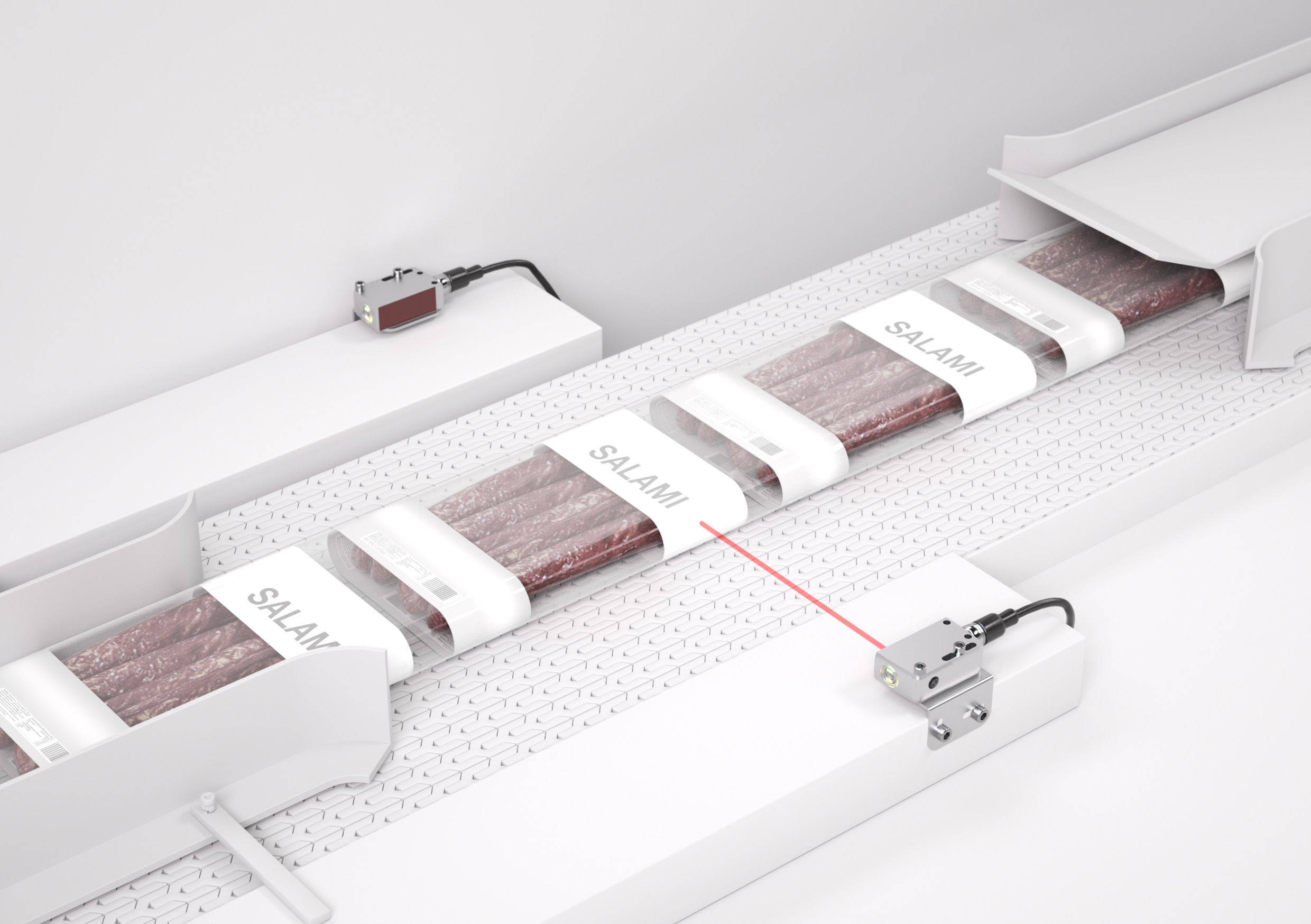
Detection of products through a film
Requirement:
Solution:
The LS35CI.XXR super power through-beam photoelectric sensor radiates even metallized films and reliably detects the front edges of the objects inside. This ensures that the seal is always applied in the correct place. The stainless steel sensors are completely watertight and certified according to ECOLAB, Diversey and CleanProof+.
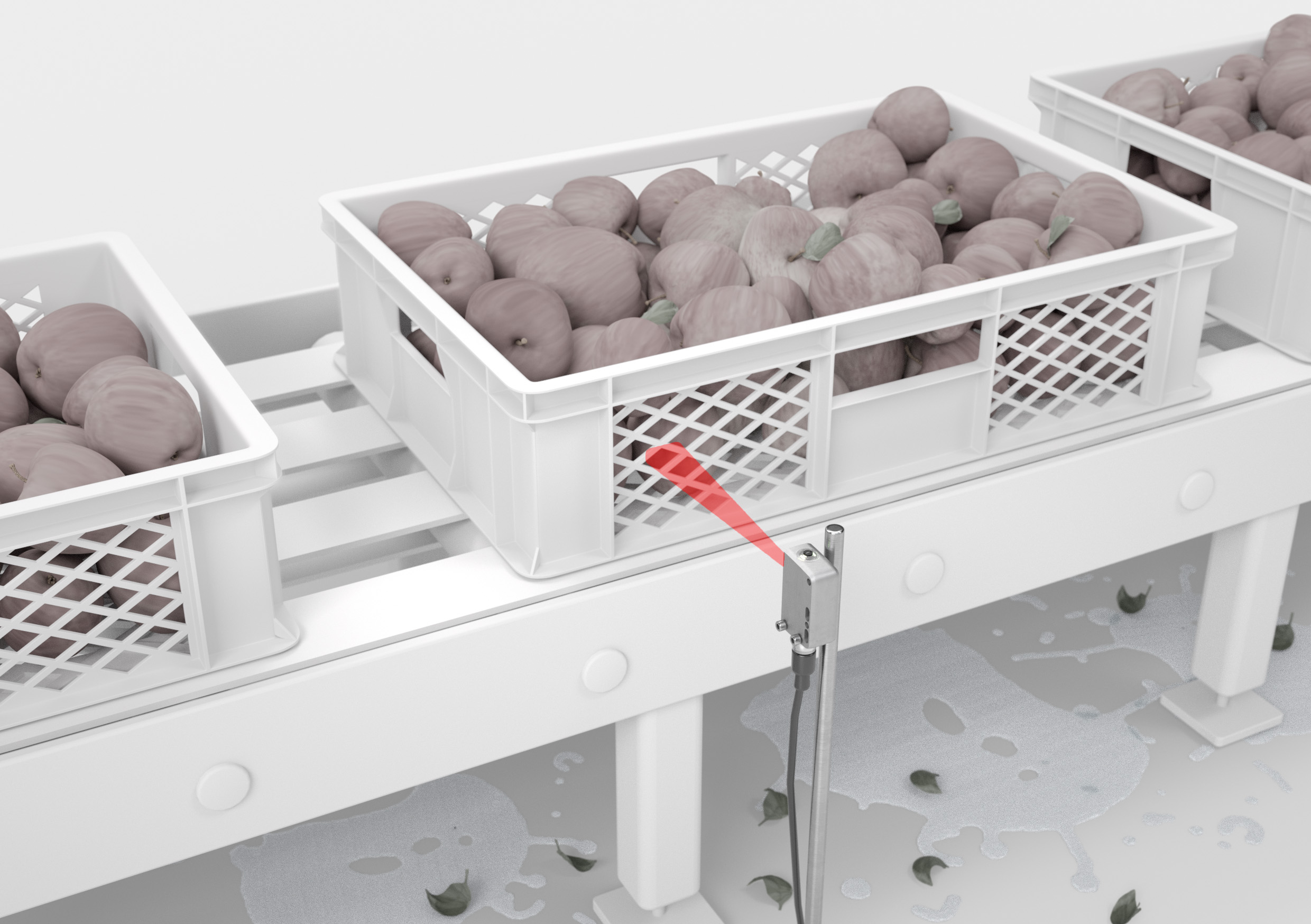
Detecting interrupted objects
Requirement:
Solution:
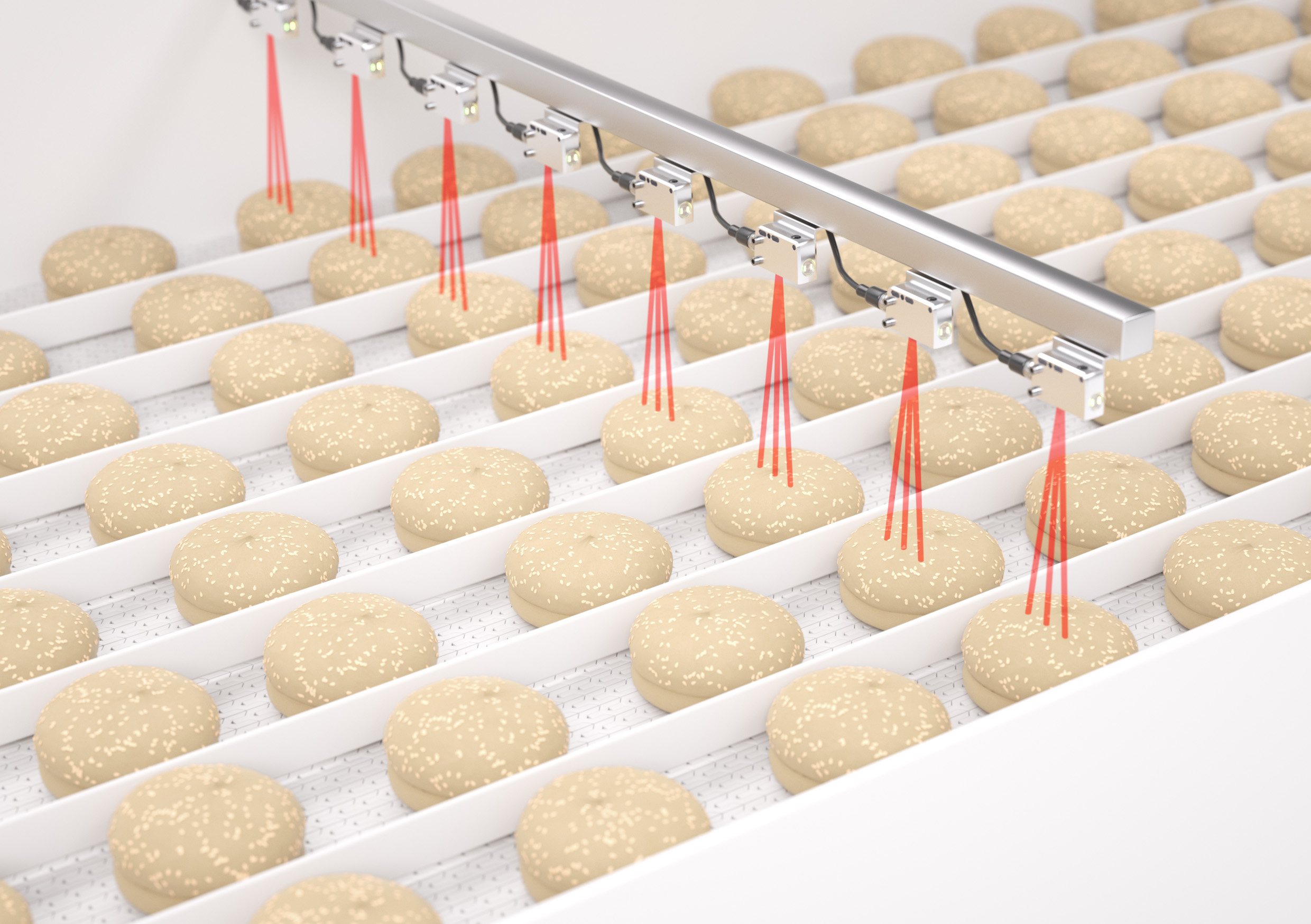
Detection of unpackaged products on conveyor belts
Requirement:
Solution:
The DRT35C dynamic reference sensor detects any products by using the conveyor belt as a reference. The sensor, with a high-quality stainless steel housing with smooth surfaces (typical value ≤ 0.8 Ra), is the perfect solution for mounting above open food. Thanks to the stainless steel housing, no additional sensor enclosure is required.
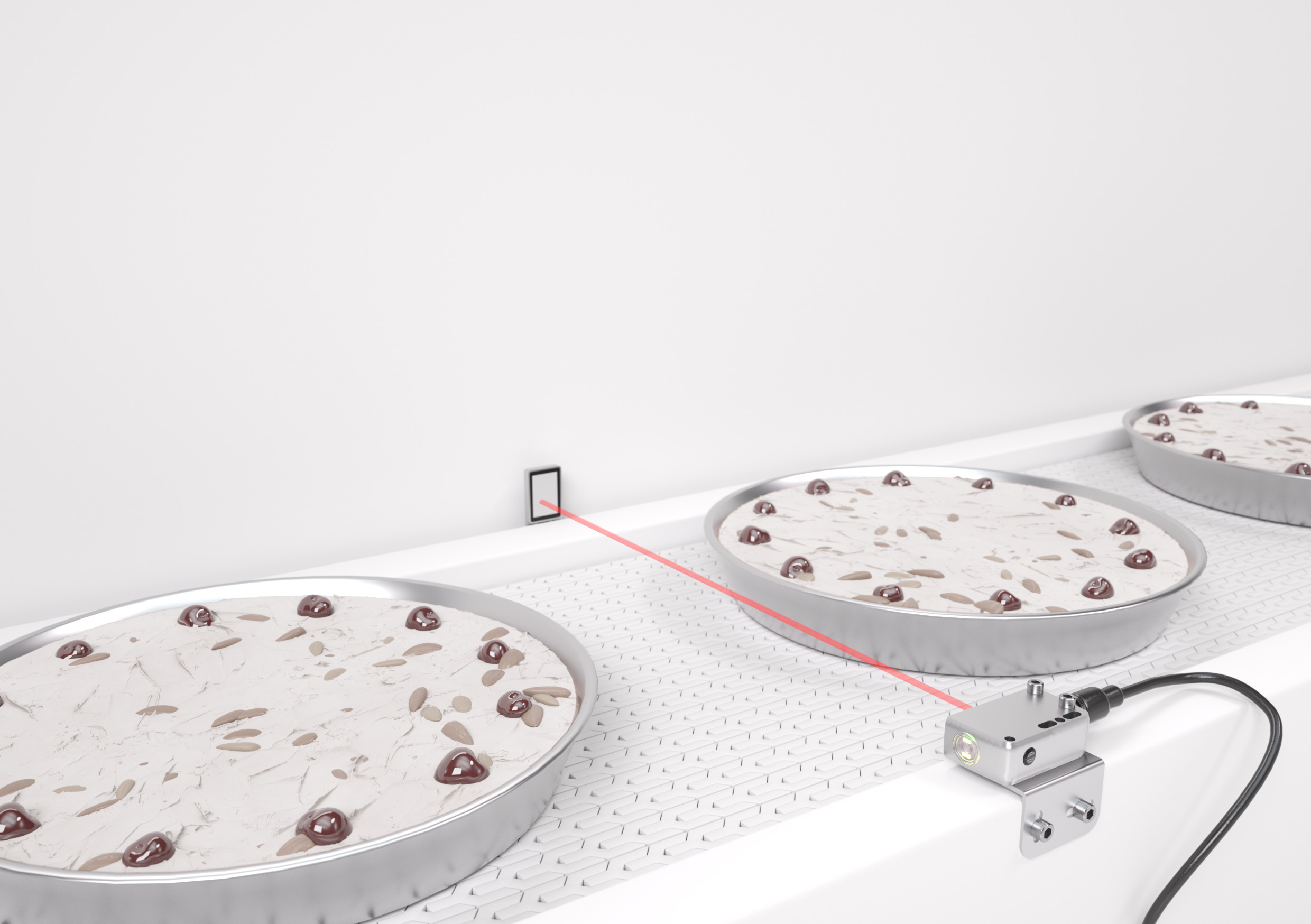
Detection of unpackaged baked goods on the conveyor belt
Requirement:
Solution:
The PRK 35C photoelectric reflex switch is designed for this detection task and also reliably detects shiny objects. The high-quality stainless steel housing is robust against mechanical loads and withstands intensive cleaning cycles.
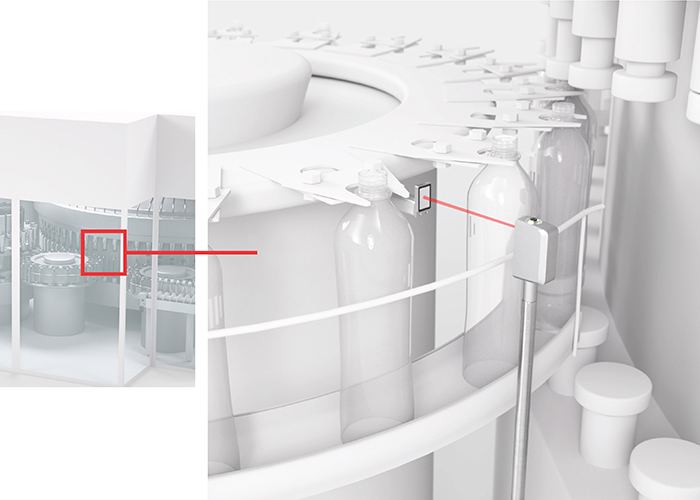
Detecting bottles in an aseptic filling system
Requirement:
Solution:
The PRK33C.PPTT3 photoelectric reflex switch has been developed for the detection of transparent objects. The stainless steel sensor in hygienic design is an optimal choice for the detection of transparent bottles in aseptic filling and for other sterile production environments in the food and pharmaceutical industry. A particularly smooth housing without mounting holes prevents deposits. The sensor is mounted gas-tight using a mounting spigot.
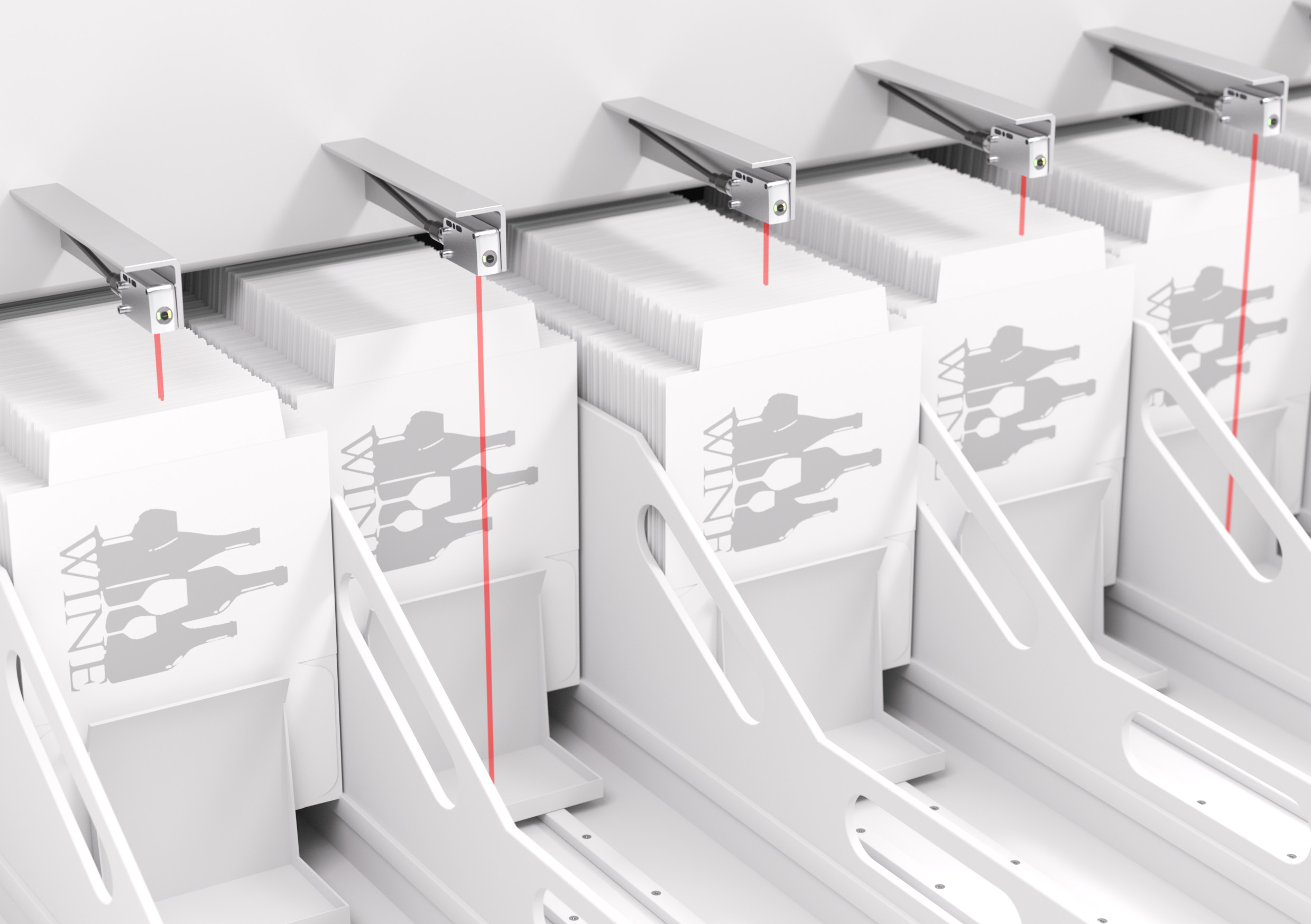
Detecting the carton feed
Requirement:
Solution:
The precisely adjustable HT 35C.PP light scanners with background suppression are optimally suited for the position and presence check. The Power PinPoint LED technology ensures a high level of precision in stack detection: The size of the homogeneous light spot is constant over the entire operating range of the sensor.
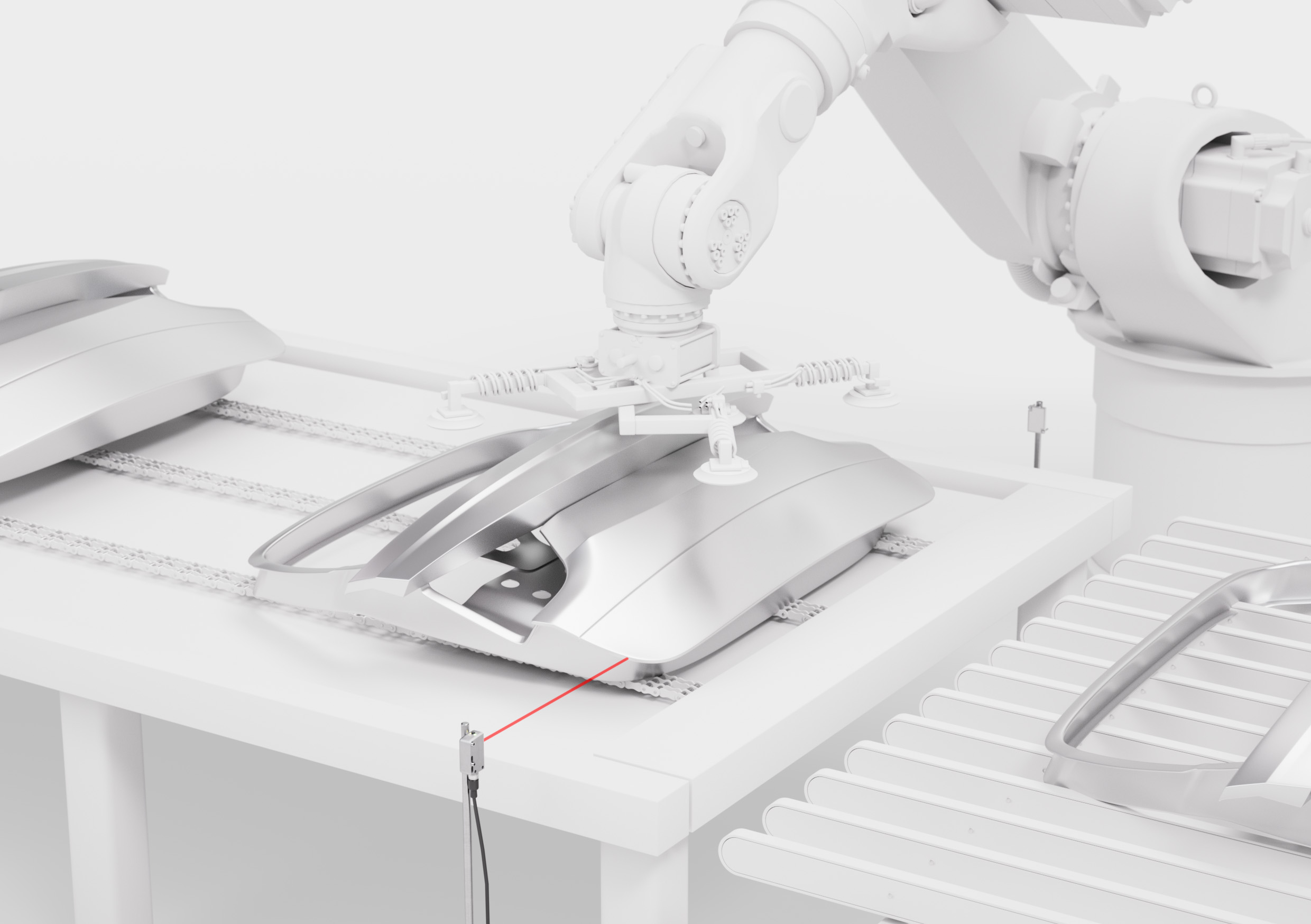
Presence check for controlling the gripper robot in the automotive industry
Requirement:
Solution:
The PRK35C retro-reflective photoelectric sensors with Power PinPoint LED feature a high function reserve and easy commissioning. They also detect shiny objects very reliably. Robust stainless steel sensors are an optimal choice in this harsh production environment.
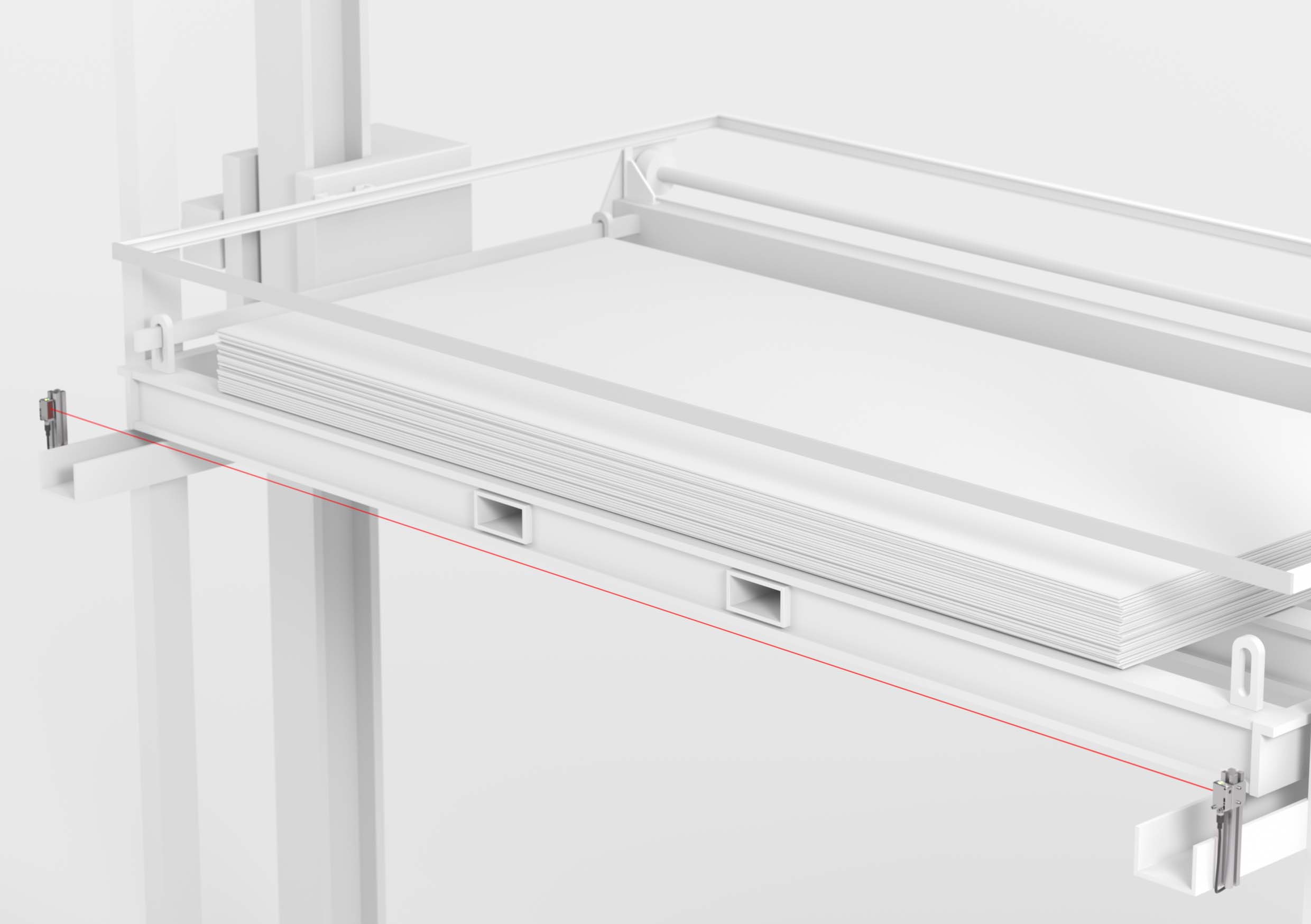
Presence control
Requirement:
Solution:
The LS35C through-beam photoelectric switch with Power PinPoint LED ensures precise detection of the metal plates. The rugged and shock-resistant stainless steel housing is particularly resistant to the harsh environmental conditions in the metal industry and to mechanical loads.
Technical properties
Overview of our stainless steel sensors
Parameter | PRK33C / PRK35C | LS/LE33C / LS/LE35C | LS/LE33CI LS/LE35CI |
HT33C / HT35C | DRT35C / DRT33C DRT35C.R / DRT33C.R |
Function principle | Retro-reflective photoelectric sensor | Throughbeam photoelectric sensor | Throughbeam photoelectric sensor for film (high power and super power) | Diffuse reflection photoelectric sensor with background suppression | Dynamic reference scanner |
Housing design and dimensions (W x H x D) | 33C series: Hygienic design (18.8 x 52.8 x 32.4 mm) 35C series: Wash-Down Design (18.8 x 52.8 x 32.4 mm) |
||||
Housing material | Stainless steel V4A (AISI 316L) | ||||
Light sources | Power PinPoint LED, red (type 645 nm) | Power PinPoint LED, red (type 645 nm) | LED infrared (860 nm) | Power PinPoint LED, red (type 645 nm) | LED, red (645 nm) |
Laser, red (650nm; Laser class 1) | Laser, red (650nm; Laser class 1) | ||||
Switching frequency | 1500 Hz (Power PinPoint) | 1500 Hz (Power PinPoint) | 100 Hz (Infrared) | 1,000 Hz (Power PinPoint) | 750 Hz (Teach 2 and 3) 500 Hz (Teach 1) |
2500 Hz (Laser) | 2,500 Hz (Laser red) | 300 Hz (DRT33C.R/DRT35C.R) | |||
Operating range | 0.05... 14m (Zweilinser Power PinPoint) | 0 … 25 m (Power PinPoint) | 180 m High power (infrared) 340 m super power (infrared) |
0... 1200 mm (Power PinPoint) | 0.05 … 0.15 m |
0 … 5 m (autocollimation) | 0... 600 mm (XL light spot) | 0.08 … 0.4 m (six-pack detection) | |||
0 … 3 m (Detection of transparent objects) | 5... 600 mm (Laser) | ||||
0... 20m (Laser Zweilinser) | |||||
IO-Link | V1.1 (COM2) | V1.1 (COM2) | V1.1 (COM2) | V1.1 (COM2) | V1.1 (COM2) |
Operation | Multi-turn potentiometer, teach button (single lens), 270° potentiometer (laser) | - | 270° potentiometer (LE, LS high power) | multi-turn spindle | Teach button |
Temperature range | -40 to +70°C | -40 to +70°C | -40 to +70°C | -40 to +70°C | -40 to +70°C |
Protection class | IP 67, IP 68, IP 69K | IP 67, IP 68, IP 69K | IP 67, IP 68, IP 69K | IP 67, IP 68, IP 69K | IP 67, IP 68, IP 69K |
Certifications | CE, UL, ECOLAB, CleanProof+, Diversey | CE, UL, ECOLAB, CleanProof+, Diversey | CE, UL, ECOLAB, CleanProof+, Diversey | CE, UL, ECOLAB, CleanProof+, Diversey | CE, UL, ECOLAB, CleanProof+, Diversey |
Connection | M8 (SR33C) M12, cable, pigtail cable M12 (SR35C) |
M8 (SR33C) M12, cable, pigtail cable M12 (SR35C) |
M8 (SR33C) M12, cable, pigtail cable M12 (SR35C) |
M8 (SR33C) M12, cable, pigtail cable M12 (SR35C) |
M8 (SR33C) M12, cable, pigtail cable M12 (SR35C) |
5B Series
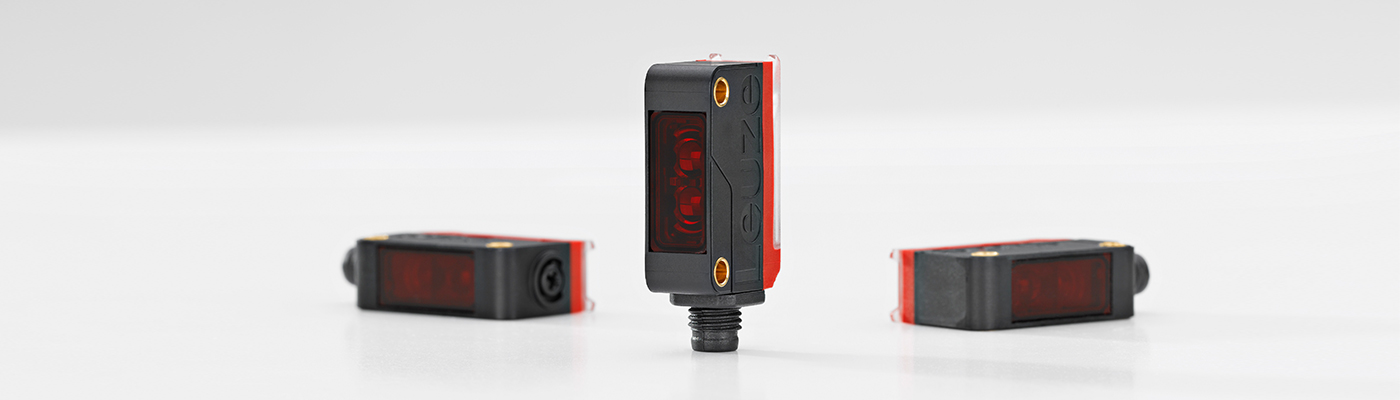
Sensors with convincing cost-effectiveness
Presence monitoring in intralogistics and packaging processes as well as in the automotive industry with the new 5B Series
When carrying out presence checks in automated processes, the sensor system should reliably detect different objects. The handling of the sensor, including mounting, alignment and adjustment, should also be quick and easy, especially since a large number of sensors often have to be installed. Therefore, standardization on the one hand and adaptation of the sensor to the individual needs of the customer on the other are very important for cost-efficient commissioning of a system.
We have developed an optimized sensor generation precisely for these requirements:
the new 5B series. Convincingly economical. Perfect handling.
Advantages for you
- Flexible use: Full range of products with all functional principles, each in identical and mounting-compatible housings. You can choose between throughbeam photoelectric sensors, retro-reflective photoelectric sensors and diffuse reflection photoelectric sensors to suit the respective application
- Housing: New, more compact housing (dimensions W x H x L: 11mm x 32.4mm x 20mm) – mounting compatible with predecessor series – ideal for confined installation situations. With protection rating IP 67 and ECOLAB certified
- Mounting and installation: Fast mounting and easy installation thanks to metal inserts with M3 thread
- Commissioning: 360° visible display LEDs for easy installation and status display. Fast alignment through homogeneous and highly visible light spot
- Optimal configuration: Simple adjustment and adaptation to the application through user-friendly potentiometer
- Reliable detection of depolarizing objects: Optimized performance for the detection of reflective, shrink-wrapped, and shiny objects
- Electrical connection: Adaptation to individual customer requirements through various connection options (e.g., cable, M8 plug, pigtail, etc.)
- Switching frequency: Improved switching frequency of up to 900 Hz for throughbeam photoelectric sensors and up to 1,000 Hz for photoelectric proximity sensors for high performance and function reserve
- Tamper-proof: Light/dark switching is tamper-proof via the polarity reversal of the (cable) wiring
Available operating principles:
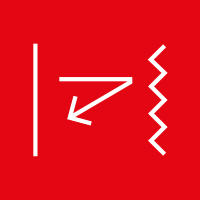
Retro-reflective photoelectric sensor
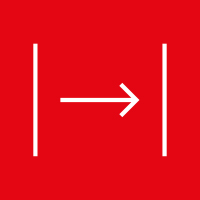
Throughbeam photoelectric sensor
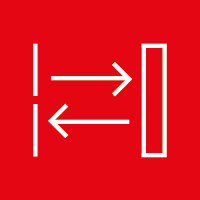
Diffuse reflection photoelectric sensor
Highlights
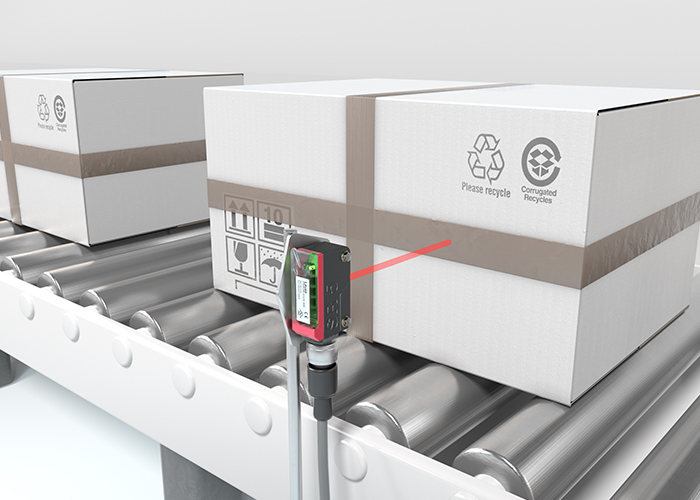
Cost-effective installation
The greater the number of sensors to be installed on a conveyor line, the more important the cost-effectiveness aspect becomes in terms of time and costs during installation and commissioning.
The intelligent and simple mounting concept using two convenient M3 metal threads makes it easier for the user to carry out quick installation.
The small and compact housing design also simplifies integration in confined installation situations.
Depending on individual preference or the on-site installation situation, various connection options are available, e.g. with M8 connector, cable or pigtail connector.
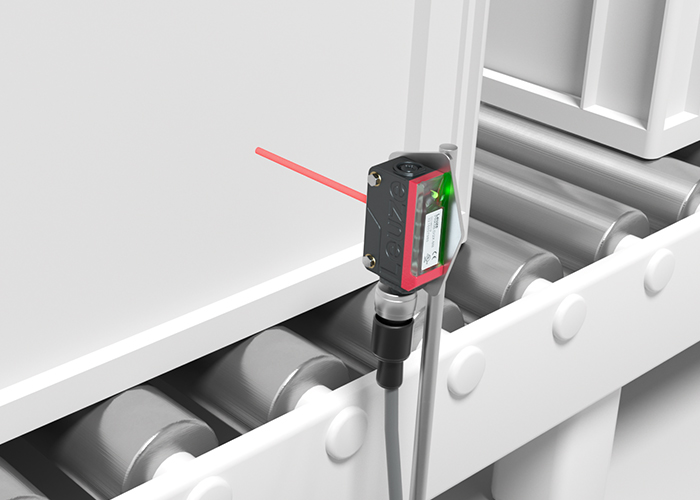
Quick and easy commissioning and adjustment
360° visible display LEDs ensure easy installation and a clearly visible status display. The simple alignment of the sensor using the highly visible light spot also saves time and thus reduces costs for the user. The new 5B series is also available with a potentiometer for better fine adjustment of the sensor. This allows the sensor to be quickly and easily adapted to changing conditions in the application. In addition,
the light/dark switching of the switching output can be implemented in a tamper-proof manner via the wiring.
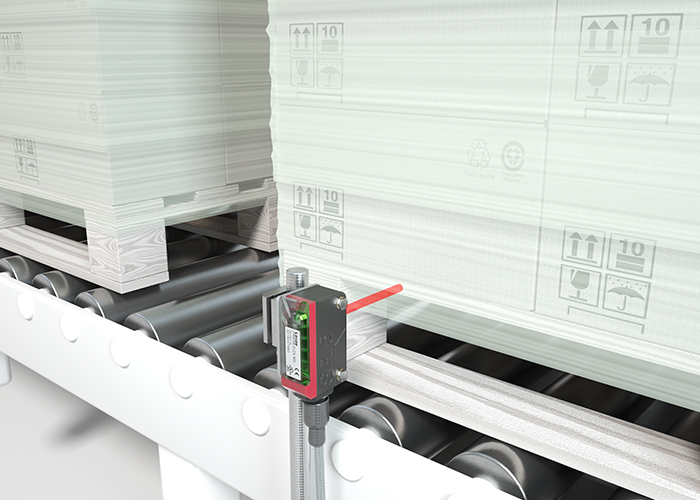
Reliable detection even with depolarizing objects
In conveyor and storage systems, pallets, cardboard boxes, and other containers are often wrapped in film, which can present challenges for sensor technology. With the new 5B series, we offer optimized variants specifically for this area of application. These sensors guarantee reliable switching even with shrink-wrapped or shiny objects.
Application
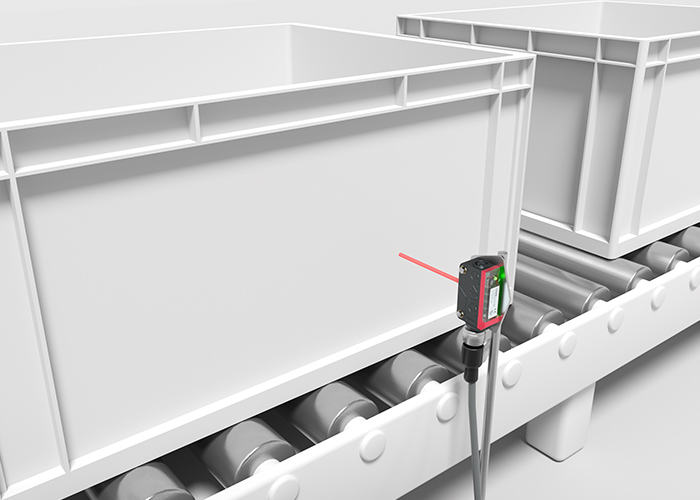
Presence checking in the area of intralogistics with retro-reflective photoelectric sensor
Requirement:
In a logistics center, various containers and boxes are to be transported on roller conveyors that are close together. Some boxes are also shrink-wrapped. All objects must be reliably detected. When the sensor is put into operation, it must be possible to install, align and adjust it quickly and easily. The light spot must be clearly visible.Solution:
The new sensor of the 5B series can be mounted directly on the roller conveyors, which are close together, thanks to its compact housing. Convenient metal inserts with an M3 thread are used for installation and high-strength mounting. Alignment is quick and easy thanks to a homogeneous and highly visible light spot and 360° visible display LEDs. The adjustment is user-friendly via potentiometer. Thanks to the optimized performance for the detection of shrink-wrapped and shiny objects, these can also be reliably detected.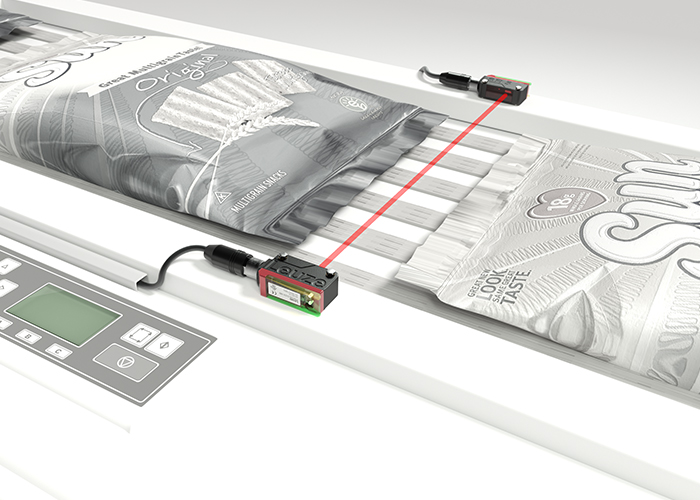
Presence control in the area of packaging technology with a throughbeam photoelectric sensor
Requirement:
A food manufacturer packs chips in primary packaging. The packages are then transported further on a conveyor line and are to be reliably detected there. The light spot should be visible. The sensor status should also be visible from a distance of 2 m.Solution:
The new 5B series sensor can also be mounted horizontally on the conveyor line and the light spot is clearly visible. The sensor status can be seen at all times, even from a distance from the conveyor line, thanks to the bright, 360° display LEDs. The advantage of choosing a throughbeam photoelectric sensor is that it has a very high performance reserve, which enables reliable detection even under demanding environmental conditions and reduces the risk of system downtime. The new 5B series also features an optimized switching frequency of 900 Hz.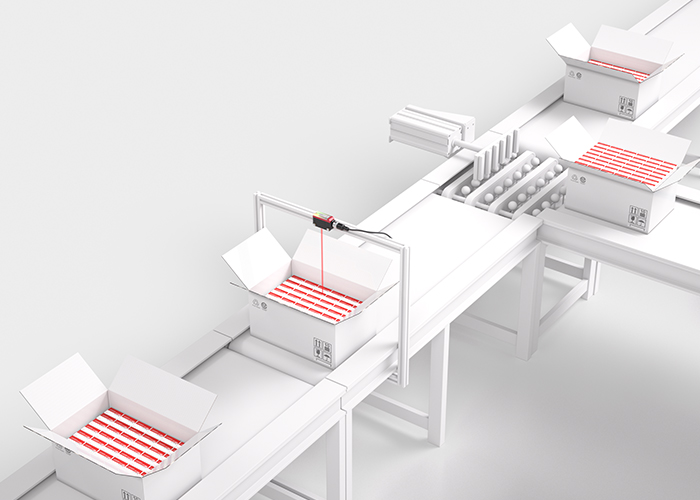
Presence checking in intralogistics with a photoelectric proximity switch
Requirement:
Packages are transported in a distribution system on a conveyor belt. A sensor is to check whether the packages are properly filled. Boxes that are underfilled or overfilled are to be ejected.Solution:
The HT 5B photoelectric proximity switch looks down on the conveyor belt and detects the boxes and their contents with a fast switching behavior of up to 1,000 Hz. Adjustment and fine-tuning are user-friendly and are performed via potentiometers. The background suppression of the sensors ensures that only the object is detected and the conveyor belt is suppressed.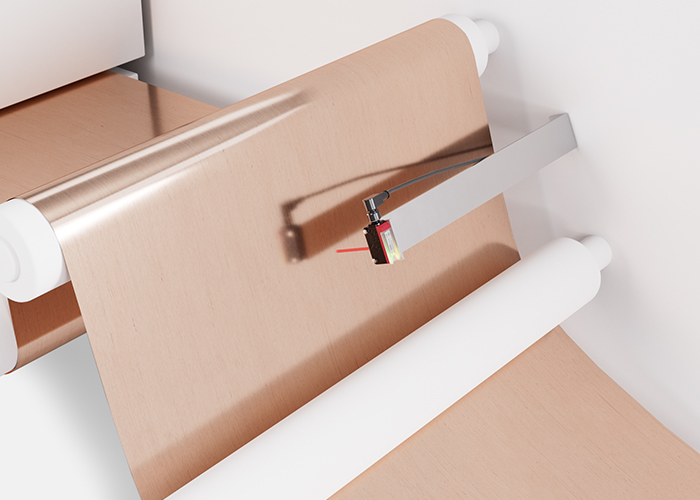
Detection of a film tear in battery cell production with a photoelectric proximity switch
Requirement:
During the production of lithium-ion battery cells, rolled copper or aluminum foils are compressed in a complex process (calendering). High and irregular speeds can cause the foil web to tear. Sensors are used to stop the process immediately to prevent damage to the machine.Solution:
The HT 5B light scanner with background suppression continuously monitors the presence of the film and immediately detects a film tear. The scanner also reliably detects very shiny or dark surfaces and, thanks to its compact design, is also suitable for very cramped installation situations.Technical properties
Parameter | Retro-reflective photoelectric sensors | Throughbeam photoelectric sensors | Diffuse reflection photoelectric sensor |
Switching frequency | 500 Hz | 900 Hz | 1,000 Hz |
Operating range | 6.5 m | 15 m | 400 mm |
Light source | Highly visible red light | Highly visible red light, infrared | Highly visible red light, infrared |
Operational control | Potentiometer | - | Potentiometer |
Housing dimensions (W x H x L) | 11 x 32.4 x 20 mm | 11 x 32.4 x 20 mm | 11 x 32.4 x 20 mm |
Housing material | Plastic | Plastic | Plastic |
Protection class | IP 67 | IP 67 | IP 67 |
Compatibility of materials | ECOLAB | ECOLAB | ECOLAB |
Connection | M8 / cable / Pigtail | M8 / cable / Pigtail | M8 / cable / Pigtail |
53C/ 55C Series
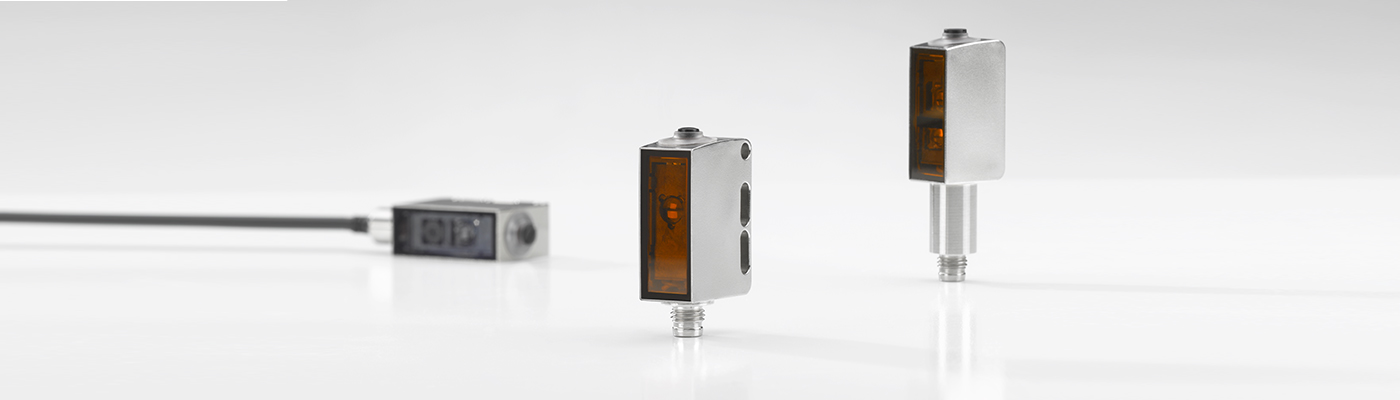
New sensor portfolio for hygiene-sensitive production processes
53C and 55C series: Two new stainless steel series in a miniature housing for detection tasks in production and packaging processes
When processing, filling or packaging food or pharmaceutical products, very strict requirements apply with regard to the hygiene and cleaning of the systems.
Not only the production systems, but also electronic components such as sensors, must withstand regular intensive cleaning and disinfection cycles with sometimes aggressive cleaning agents. In particular, the use of sensors with a hygienic design in accordance with the DIN EN 1672-2 standard (“Food processing machinery - Basic concepts - General design principles”) is recommended for applications involving direct contact with food or for detection tasks above unpackaged products. These sensor solutions are characterized by a special design as well as high resistance to cleaning agents and tightness.
Our new stainless steel sensor platform with the 53C series in hygienic design and the 55C series in wash-down design was specially developed for applications with increased hygiene requirements. To withstand the harsh conditions, the housings of both sensor series are made of high-quality stainless steel V4A (AISI 316L). The smooth stainless steel surfaces (typical value ≤ 0.8 Ra) ensure that cleaning agents drip off immediately, preventing the spread of bacteria in production plants. During the design phase, great importance was placed on making both the glass-free optics cover and the operating elements absolutely tight and gap-free. All housing materials are FDA-compliant and approved for direct contact with food. This ensures additional safety in food processing and packaging.
Advantages for you
- Two full series with all operating principles: Throughbeam photoelectric sensors, retro-reflective photoelectric sensors and scanners for specific areas of application and tasks
- 2 housing designs for use in wet areas (wash-down) and hygienic areas (hygienic design)
- High-quality V4A (AISI 316L) stainless steel housing with smooth surface and glass-free optics cover made of PMMA+ with special scratch-resistant coating to prevent bacterial carryover
- IP69K rating for reliable functionality and absolute tightness of the housing
- Thermal and chemical resistance (tested and certified according to ECOLAB, CleanProof+, JohnsonDiversey)
- FDA-compliant housing materials enable the sensor to be used in applications with direct food contact
- Simple configuration and condition monitoring through IO-Link interface, as well as variants with electronic scanning range adjustment and measured value output via IO-Link
Highlights
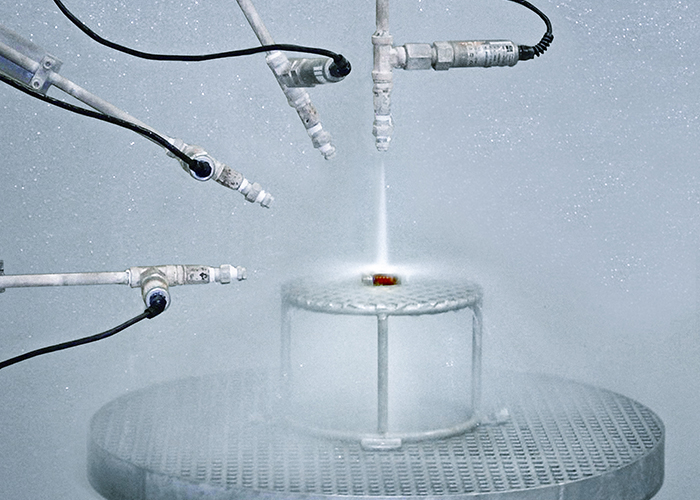
All components of the stainless steel sensors have been specially developed for use in hygiene-sensitive areas. The conditions here are harsh, especially for electronic components. Regular cleaning of the systems with high-pressure cleaners and aggressive cleaning agents plays a significant role. In addition, the change between productive and cleaning shifts results in large temperature fluctuations, which must not affect the functionality of the sensors.
- The stainless steel housings made of V4A (AISI 316L) are absolutely dust- and waterproof and achieve protection ratings of IP67, IP68 and IP69K
- Particularly smooth stainless steel surfaces with around 0.8 Ra prevent bacterial carryover
- The glass-free optical cover (scratch-resistant and diffusion-tight plastic (PMMA+) with an indium protective layer) withstands tough cleaning cycles and ensures reliable operation
- The newly developed control element is completely sealed and gap-free
- All materials are approved for direct food contact (FDA-compliant)
- Chemical and thermal resistance, tested and certified by ECOLAB, CleanProof+ and JohnsonDiversey
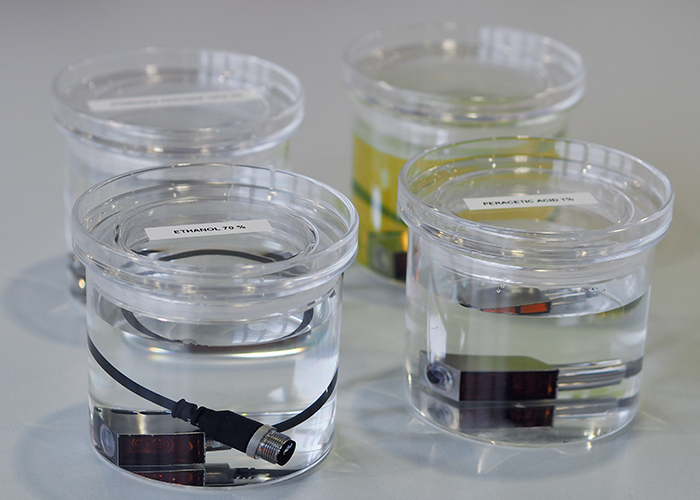
The 55C series in wash-down design is suitable for use in the wet area of production lines. The special design allows the entire system to be thoroughly cleaned with all common agents and methods. The diffusion-tight and chemically resistant materials of the optics and operating elements, in combination with the gap-free construction, prevent bacterial carry-over. The closed housing technology and the extended temperature range guarantee that the systems will function properly for years.
The 53C series sensors are designed for use in hygienically sensitive areas, such as the pharmaceutical, cosmetics and food industries.
Based on the 55C series in its basic elements, this special development is even more consistently geared towards preventing bacterial carry-over in its housing design. The smooth housing contours without mounting holes reduce any deposits. The unique mounting concept ensures a gas-tight connection between the sensor and the machine via the mounting spigot.
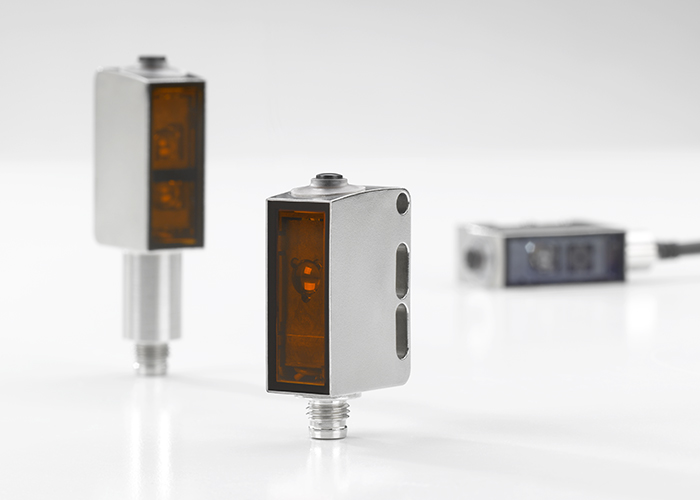
The two sensor series in a miniature stainless steel housing include all operating principles: throughbeam photoelectric sensors, reflective photoelectric sensors and photoelectric proximity sensors. Various models have been developed for special areas of application and solve challenges in production and packaging processes in a customized, reliable and economical way.
Our product highlights for special applications:
- Retro-reflective photoelectric sensors for glass and PET detection or film detection
- Laser retro-reflective photoelectric sensors for small parts detection
- Throughbeam photoelectric sensors for detecting watery liquids and for fill level control
- Scanners with background suppression and small light spot for detecting shiny and color-structured objects
- Scanners with background suppression and elongated line light spot for detecting transparent objects as well as objects with openings, holes and cutouts
- Sensors with background suppression and electronic scanning range adjustment; measured value output via IO-Link
- Sensors with background suppression and special V-optics for detecting transparent, planar, reflective, and high-gloss objects, as well as the top layers of syringe or ampoule trays
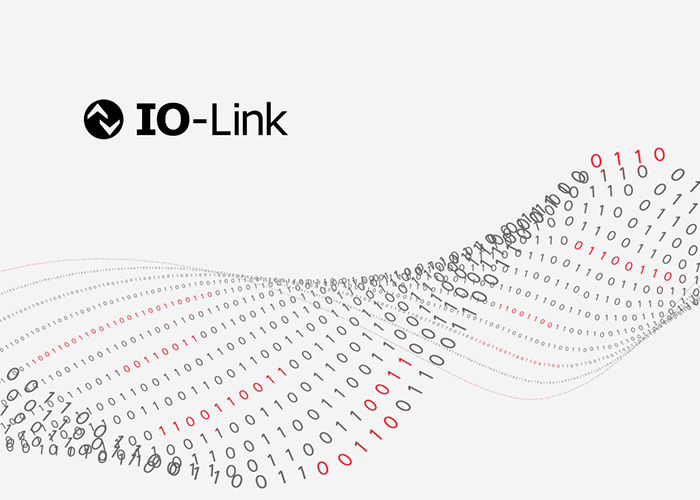
The 55C and 53C series sensors are equipped with an IO-Link interface, which makes it possible to implement innovative machine concepts with remote maintenance, diagnostics or sensor configuration. The sensors can be parameterized, operated and maintained (condition monitoring) via IO-Link. Format changes are also much more flexible and economical with IO-Link.
Special scanner variants are electronically adjustable and equipped with a measured value transmission for monitoring a specific window area. The scanning range can be set numerically via IO-Link (Remote Set Distance). The device calibration enables high accuracy during remote adjustment. When replacing a defective sensor, the default settings can be transferred to the new device via IO-Link without any loss and without having to repeat the teach-in process.
Cables and reflectors for hygienic applications
Our range of 55C and 53C series sensors for applications in the food and pharmaceutical industry is complemented by a range of suitable cable solutions and reflectors.
The special connection cables are made of FDA-compliant materials (thermoplastic elastomers (TPE) and V4A stainless steel) and are therefore approved for direct contact with food.
If the cables are mounted with a tightening torque of 0.4 Nm or 0.6 Nm, they achieve an IP69 rating. This means that the cable solutions prevent the ingress of liquids, dust or steam and can withstand intensive cleaning processes with high-pressure cleaners. ECOLAB certification confirms the cables' resistance to aggressive cleaning agents. The cables can be used in a temperature range from -40°C to +105°C.
The cable portfolio for use in hygienically demanding industrial areas includes M8 and M12 as well as cable lengths of 2, 5 and 10 meters.
Reflectors
Just how reliably retro-reflective photoelectric sensors can detect depends upon the selected reflector, among other things. We offer reflectors with plastic or stainless steel housings as well as reflective tapes for different requirements: Reflectors in the advanced segment are often used in the food and pharmaceutical industry on account of their resistance against cleaning agents. The Solidchem reflectors made of chemically resistant plastic also stand out for their high temperature resistance. The reflectors from the extended segment are suitable for production areas with high air humidity or large differences in temperature.
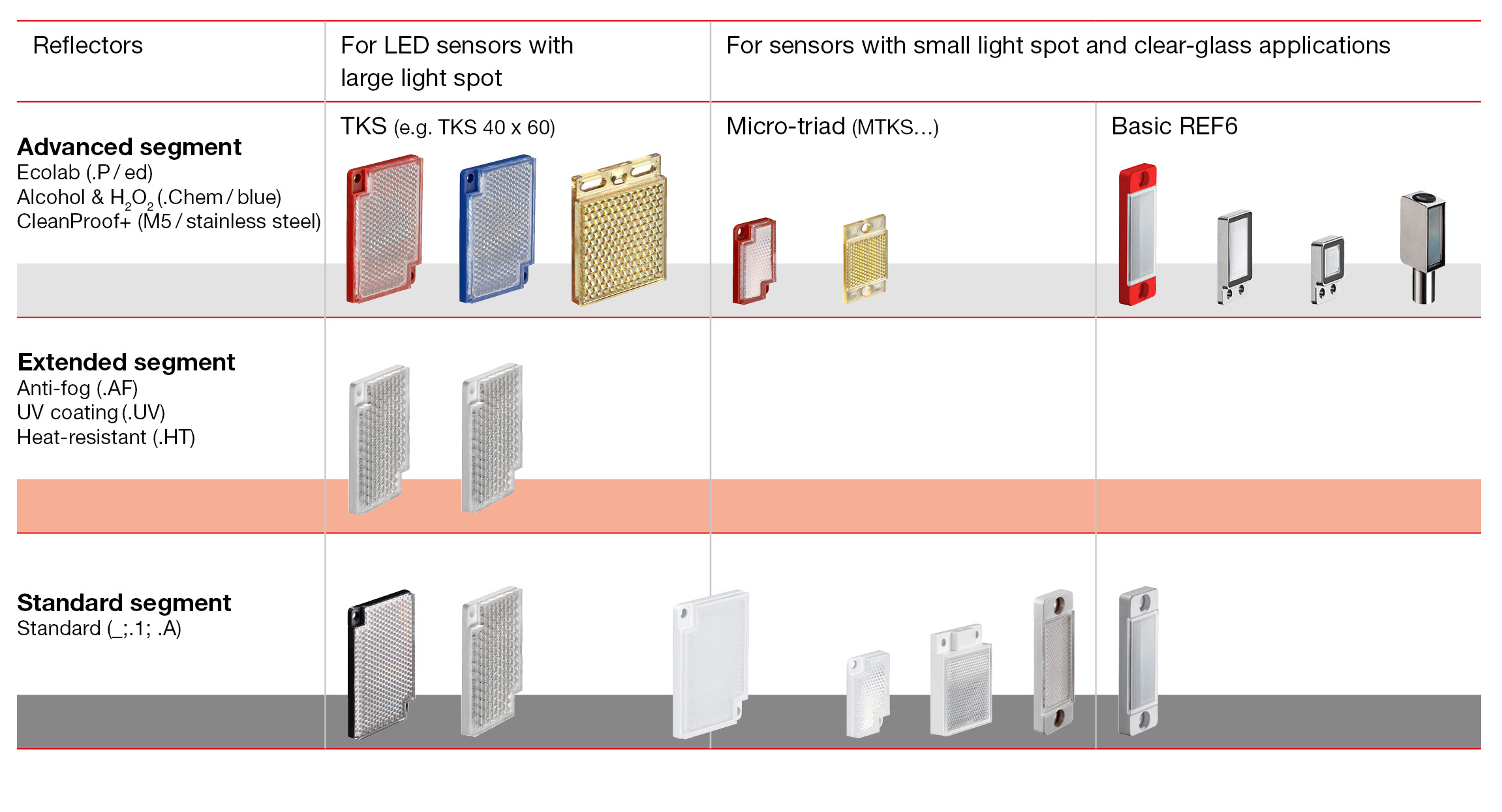
Application
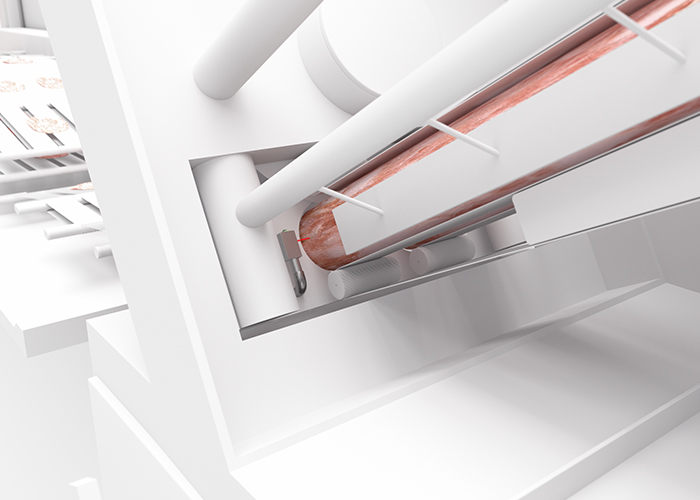
Monitoring the loading of a sausage slicer
Requirement:
In the food industry, sausage is delivered in large bars and sliced into fine slices in a slicing machine. The product in the machine feed must be reliably detected so that the gripper can push the material evenly towards the blade and all the cut slices have the required thickness.
Solution:
Our HT53C.S photoelectric proximity switch in hygienic design reliably monitors the product feed to the sausage cutting machine. If there is enough material for the machine to operate, the system starts up automatically. The particularly small light spot is characterized by excellent performance, especially with objects of different colors, while the sensor's background suppression ensures reliable color-independent product detection.
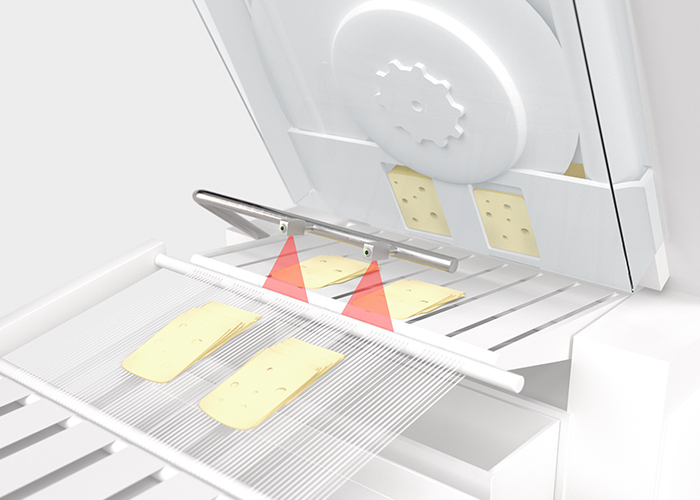
Detecting the front edge of products being cut
Requirement:
In an industrial cutting machine, products are cut into small stacks and pre-portioned into trays for later packaging. The challenge for the sensor system is that the front edge of the sliced goods must be reliably detected at the same switching point, regardless of whether they are on the conveyor belt with a slight lateral offset. The sensors are mounted directly above the conveyor belt. In this application, it must be ensured that no cleaning agent residues drip onto the cheese or the sliced goods.
Solution:
The HT53CL1.X photoelectric proximity switch with background suppression is optimized for detecting the front edges of products with a long laser light spot. Thanks to the line light spot, sliced products are reliably detected at the same switching point even if they are offset to the side on the conveyor belt. This ensures that the cut goods are neatly positioned when loaded into the tray packaging and ensures that the edge of the tray does not come into contact with the food and that traces of grease do not affect the subsequent hygienic welding of the tray. The 53C series housing is designed without drill holes for hygienic applications and is suitable for areas of application with direct food contact.
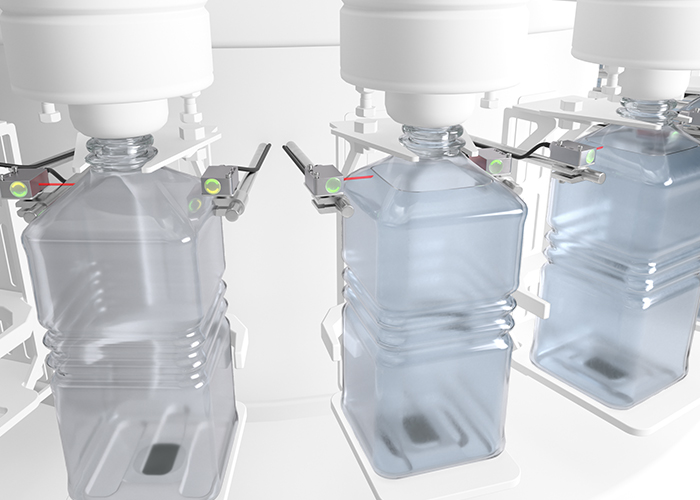
Fill level detection when bottling liquids
Requirement:
In the beverage industry, a filler is used to fill water into 3-liter bottles. The fill level must be exactly the same for all bottles – underfilling must be prevented. Reliably detecting the fill level of aqueous liquids in any container is one of the most challenging detection tasks for sensors and requires particularly powerful sensor solutions.
Solution:
The LS55C.H2O and LE55C.H2O through-beam photoelectric sensors have been developed for detecting aqueous liquids and for fill level control, and reliably stop the filling process. The 55C Series stainless steel transmitter and receiver system in a wash-down design has a high transmission capacity and can also be used with colored containers and containers with plastic labels.
This solution can replace an expensive filling control system, such as a scale or a flow meter, and is easy to set up: No further settings are required via a control element other than the exact alignment of the optical axis.
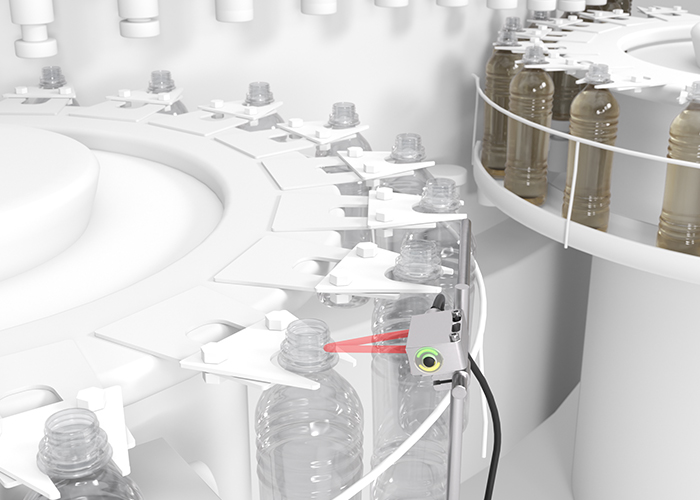
Presence checking in bottle filling in the transfer star
Requirement:
Bottle filling is characterized by very high speeds. To ensure a smooth process, it must be ensured before filling that all positions of the transfer star are occupied by bottles.
Solution:
The HT55C photoelectric proximity switch with background suppression detects containers in the bottle filling reliably and without a reflector. The sensors are designed for wet areas and can withstand intensive cleaning processes. ECOLAB certification and our extended CleanProof+ cleaning agent long-term test ensure the reliable functionality of the sensor even under harsh conditions.
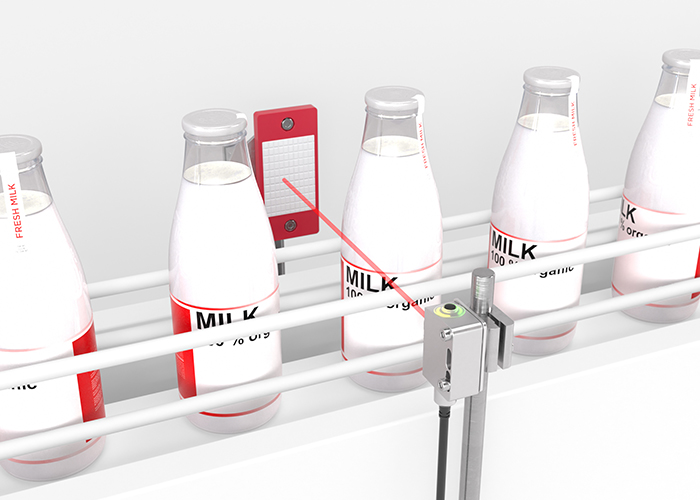
Bottle detection during transport
Requirement:
In a filling plant for milk bottles, the position of the bottles on the conveyor belt must be reliably and precisely detected for the further packaging steps in the plant.
Solution:
The PRK55C.TT3 retro-reflective photoelectric sensor also reliably detects transparent containers. The sensitivity can be set using the teach button. An integrated tracking function automatically compensates for soiling on the reflector or sensor. This extends the cleaning intervals and reduces system downtime. The stainless steel housing in a wash-down design with the highest degree of protection, IP69K, is very robust. Resistance to the cleaning agents commonly used in the market is confirmed by ECOLAB certification, the Leuze CleanProof+-Test and tests according to JohnsonDiversey.
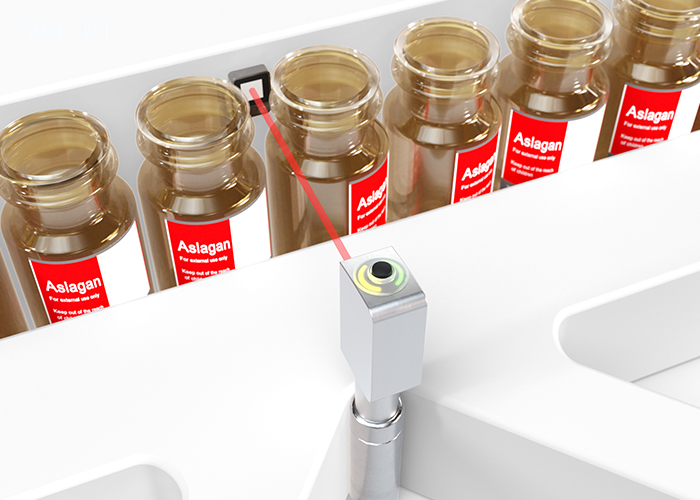
Precise positioning of vials
Requirement:
Vials made of transparent glass must be precisely detected and positioned for the filling of vaccines and other liquids.
Solution:
The retro-reflective photoelectric sensor PRK53CL1.T3 with a small laser light spot, in combination with a small stainless steel reflector, enables highly precise detection and positioning of vials. The sensor in its miniature housing can be easily integrated even in confined spaces. Both the sensor and the reflector are designed for hygienic applications.
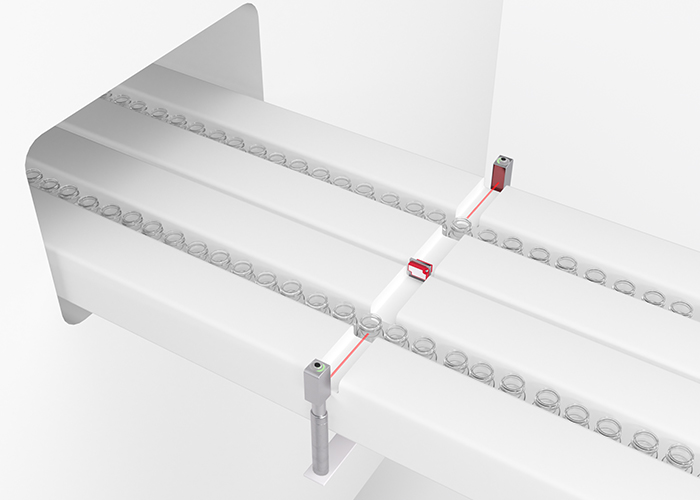
Detection and positioning of transparent vials
Requirement:
In a pharmaceutical packaging plant, vials are filled on multi-track packaging lines. The position of the transparent vials must be precisely detected before filling. One challenge is that the vials are very flat and the photoelectric sensor must aim precisely at the reflector.
Solution:
Our 53C series PRK53C.T3 retro-reflective photoelectric sensors are used in this application with MTKS 14x23.P pharmaceutical micro triple reflectors specially developed for the pharmaceutical industry. The hygienically designed stainless steel sensors precisely target the reflector and ensure reliable detection of the vials.
Overview of our stainless steel sensors
Parameter |
PRK53C / PRK55C |
LS/LE53C / LS/LE55C |
HT53C / HT55C |
ODT53C /ODT55C |
Function principle |
Retro-reflective photoelectric sensor |
Throughbeam photoelectric sensor |
Diffuse reflection photoelectric sensor with background suppression |
Distance sensor with background suppression |
Housing design and dimensions (W x H x D) |
Series 53C: Hygienic design (14.0 x 35.4 x 20.4 mm) Series 55C: wash-down design (14.0 x 35.4 x 25.0 mm) |
|||
Housing material |
Stainless steel V4A (AISI 316L) |
Stainless steel V4A (AISI 316L) |
Stainless steel V4A (AISI 316L) |
Stainless steel V4A (AISI 316L) |
Light sources |
Red light (645 nm) Laser red (650 nm; laser class 1) |
Red light (645 nm) Infrared (1450 nm) |
Red light (645 nm) Infrared (860 nm) Laser red (650 nm; laser class 1) |
Red light (645 nm) |
Switching frequency |
1,500 Hz (red light) 3,000 Hz (red laser) |
1,000 Hz (red light) 350 Hz (infrared) |
1,000 Hz (red light & infrared) 3,000 Hz (red laser) |
750 Hz (red light) |
Operating range |
0.1 … 5 m (Zweilinser) 0 … 4 m (Autocollimation) 0 … 3 m (Detection of transparent objects) 0 … 2 m (Laser: Autocollimation) 0 … 0.4 m (Laser: Detection of transparent objects) |
0.05 … 8.5 m (Red light) 0 … 64 m (Infrared) |
5... 600 mm (infrared) 5... 450 mm (red light) 5... 200 mm (small light spot) 5... 100 mm (long light spot) 15... 400 mm (laser) |
10... 150 mm 10... 80 mm (small light spot) |
IO-Link |
V1.1 (COM2) |
V1.1 (COM2) |
V1.1 (COM2) |
V1.1 (COM3) |
Operation |
Teach button |
- |
multi-turn spindle |
Teach button |
Temperature range |
-40 … +70°C |
-40 … +70°C |
-40 to +70°C |
-40 to +70°C |
Protection class |
IP 67, IP 68, IP 69K |
IP 67, IP 68, IP 69K |
IP 67, IP 68, IP 69K |
IP 67, IP 68, IP 69K |
Certifications |
CE, UL, ECOLAB, CleanProof+, JohnsonDiversey |
CE, UL, ECOLAB, CleanProof+, JohnsonDiversey |
CE, UL, ECOLAB, CleanProof+, JohnsonDiversey |
CE, UL, ECOLAB, Clean-Proof+, JohnsonDiversey |
Connection |
M8, cable, cable pigtail M12 |
M8, cable, cable pigtail M12 |
M8, cable, cable pigtail M12 |
M8 |
36 Series
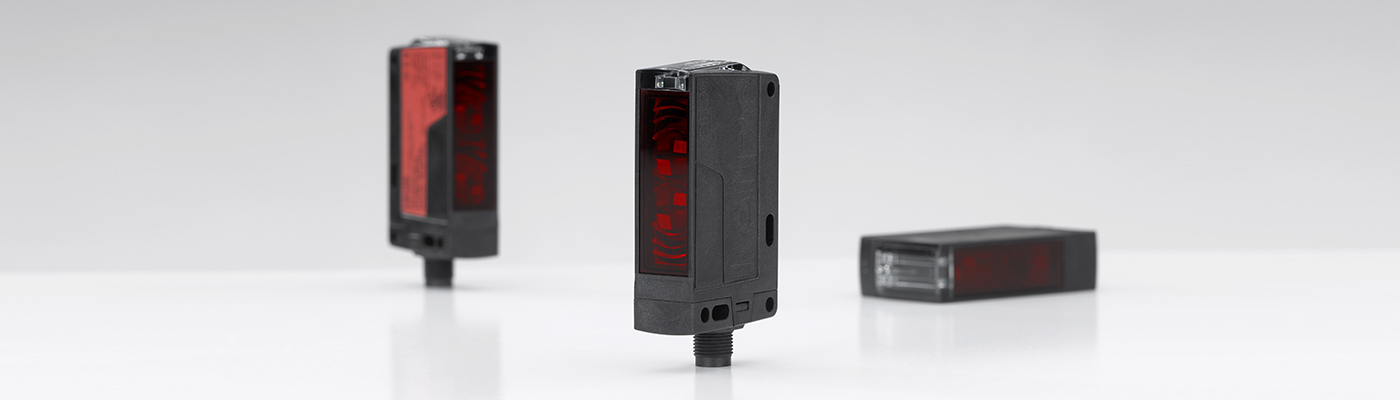
New sensor series for object detection
Perfect performance at the best price. The new 36 series.
Reliable object detection remains the key to a high level of automation and smooth processes in plant engineering. Particularly in intralogistics, packaging technology and the automotive industry, the objects to be detected place the highest demands on sensor technology. Large detection distances, vibration, ambient light and dirt, coupled with objects with a wide range of optical properties, require sensors with a very high detection performance.
At the same time, economic criteria are essential. In many applications, a higher degree of automation is achieved by increasing the sensor quota, which in turn increases the demand for cost-optimized sensors.
The sensors in our new 36 series deliver perfect performance at the best price. Different operating principles combined with superior signal processing lead to outstanding reliability in detecting objects – even in demanding applications. The high performance reserve allows the detection of objects at long distances or the compensation of sources of interference or contamination at shorter distances.
Advantages for you
- Very high ranges lead to a large performance reserve and thus to a reliable detection rate even in critical applications
- Availability with your preferred operating principle:
- Scanners with background suppression with a max. range of 2500 mm
- Retro-reflective photoelectric sensors with max. 17 m range (optionally also for detecting objects with depolarizing properties)
- Throughbeam photoelectric sensors with max. 80 m range
- Excellent price-performance ratio
- Support of all common switching logics: NPN and PNP switching end, light and dark switching
- High connection diversity allows for easy integration (cable, M12 connector or cable with M12 plug)
- Mounting compatibility with 46 series sensors
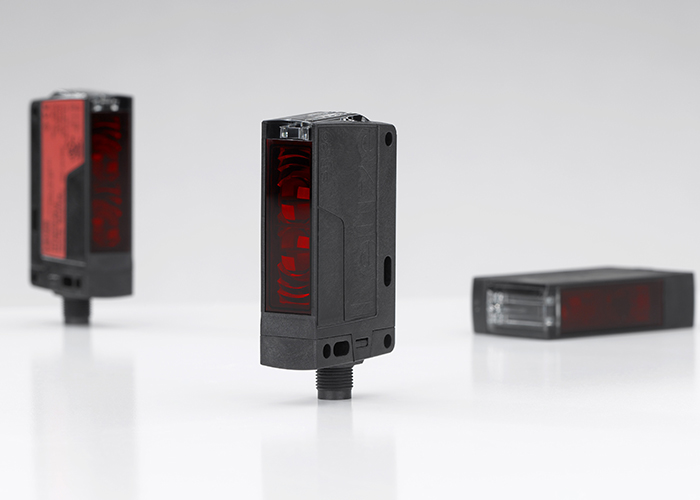
Application
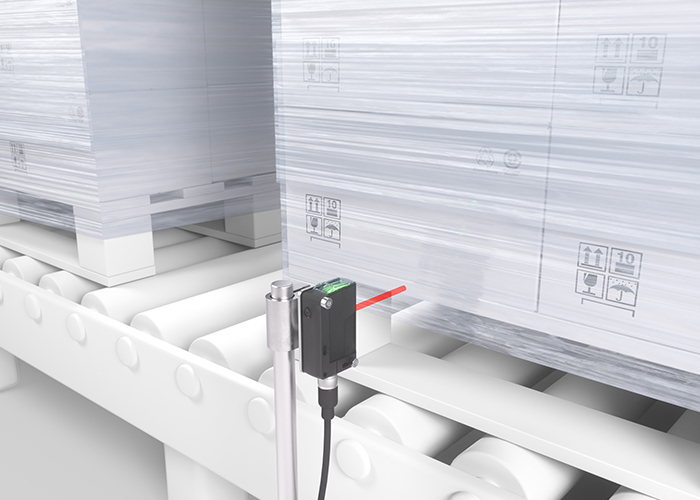
Detection of film-wrapped pallets
Requirement:
Pallets are often wrapped in film for transport security. Conventional photoelectric sensors cannot reliably detect these due to the depolarizing properties of the stretched film. Since this type of transport securing is widespread, the sensor should detect these special objects with absolute reliability. At the same time, an economical sensor solution must be found so that this application can be scaled.
Solution:
The new PRK36.D retro-reflective photoelectric sensor has special optics for detecting depolarizing objects with absolute reliability. An improved design offers a cost advantage over sensors currently on the market.
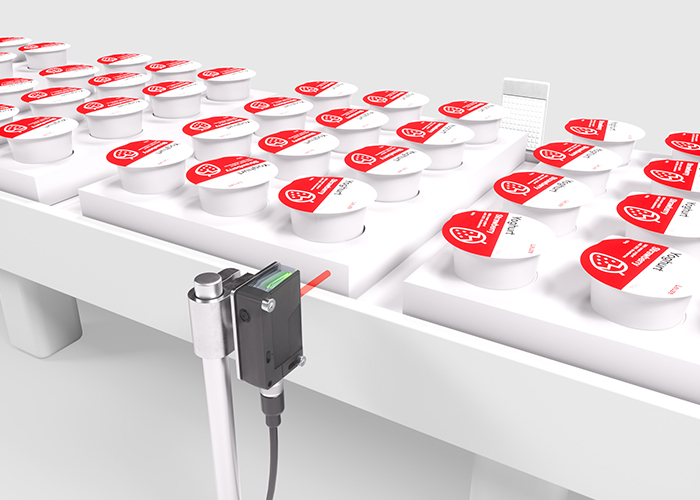
Detection of outer packaging in the food industry
Requirement:
In the food industry, identical products are usually combined into larger packages in order to optimize and automate handling and logistics processes. An important prerequisite for a high degree of automation is the use of high-performance sensors that reliably detect packages, even when the products or outer packaging change. A large number of economically attractive sensors are needed to closely monitor these processes.
Solution:
With our new 36 series, we offer photoelectric retro-reflective sensors that reliably detect different packaging due to their very high function reserve. An improved design offers a cost advantage over sensors currently on the market.
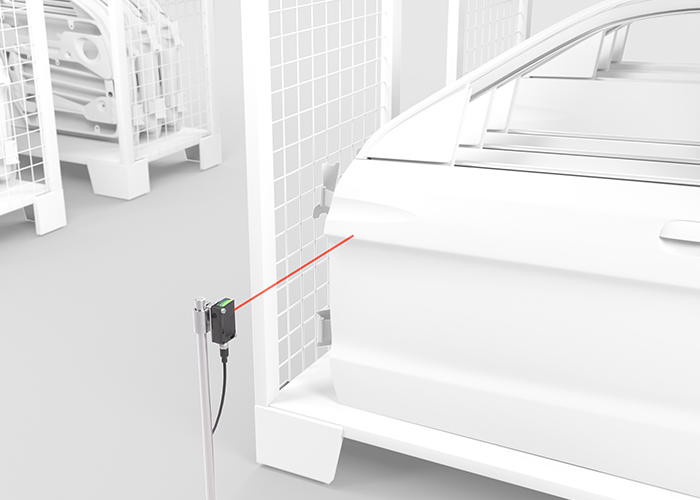
Securing material availability in manufacturing systems
Requirement:
Highly automated manufacturing systems require a high level of process reliability on the one hand, while ensuring material availability and material replenishment are of essential importance on the other. Sensor technology that reliably ensures the presence and thus the stock of different assembly materials is the key component here. At the same time, sensors must be flexibly integrated in different installation situations.
Solution:
Our new 36 series sensor portfolio is particularly well suited for detecting a wide range of objects in production systems and thus for assessing the presence or absence of assembly material due to the different operating principles, the variance in light color and the very high detection rate. A wide range of mounting options and connection variants allow for easy integration. The excellent price-performance ratio enables scaling in large and complex manufacturing systems.
Technical properties
Feature | HT36 |
PRK36 |
PRK36.D | LS/LE36 |
Operating principle | Proximity sensor with background suppression | Retro-reflective photoelectric sensor | Polarized retro-reflective photoelectric sensor | Throughbeam photoelectric sensor |
Operating range | 2500 mm | 17 m | 11 m | 80 m |
Light source | Red light, infrared | Red light | Red light | Red light |
Switching frequency | 250 Hz | 300 Hz | 300 Hz | 300 Hz |
Switching output | PNP, NPN for light and dark switching |
PNP, NPN for light and dark switching |
PNP, NPN for light and dark switching |
PNP, NPN for light and dark switching |
Operation | spindle | - | - | potentiometer |
Protection class | IP 67 | IP 67 | IP 67 | IP 67 |
Certifications | CE, UL, ECOLAB | CE, UL, ECOLAB | CE, UL, ECOLAB | CE, UL, ECOLAB |
Connection | M12 and cable variants | M12 and cable variants | M12 and cable variants | M12 and cable variants |