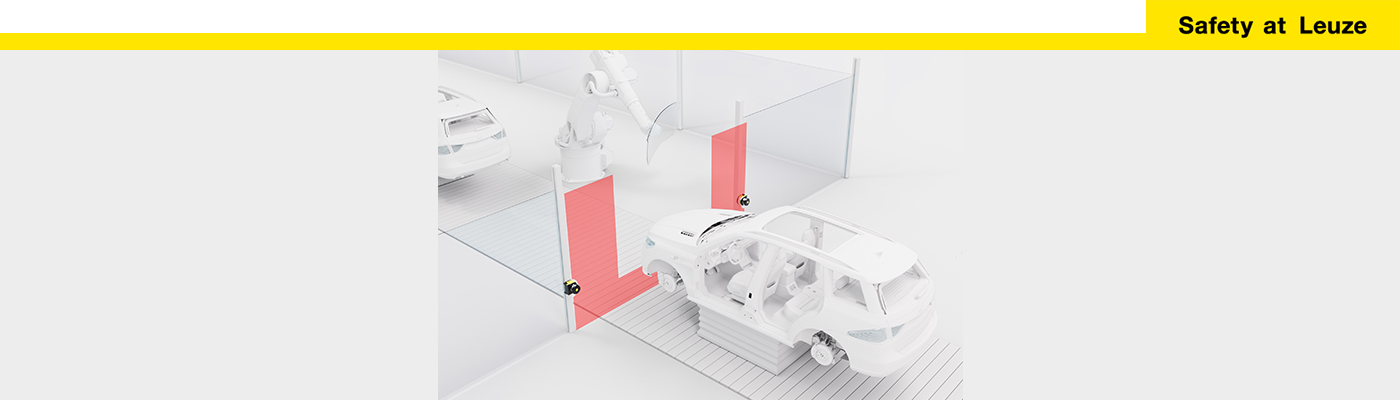
Access guarding at skillet transfer area
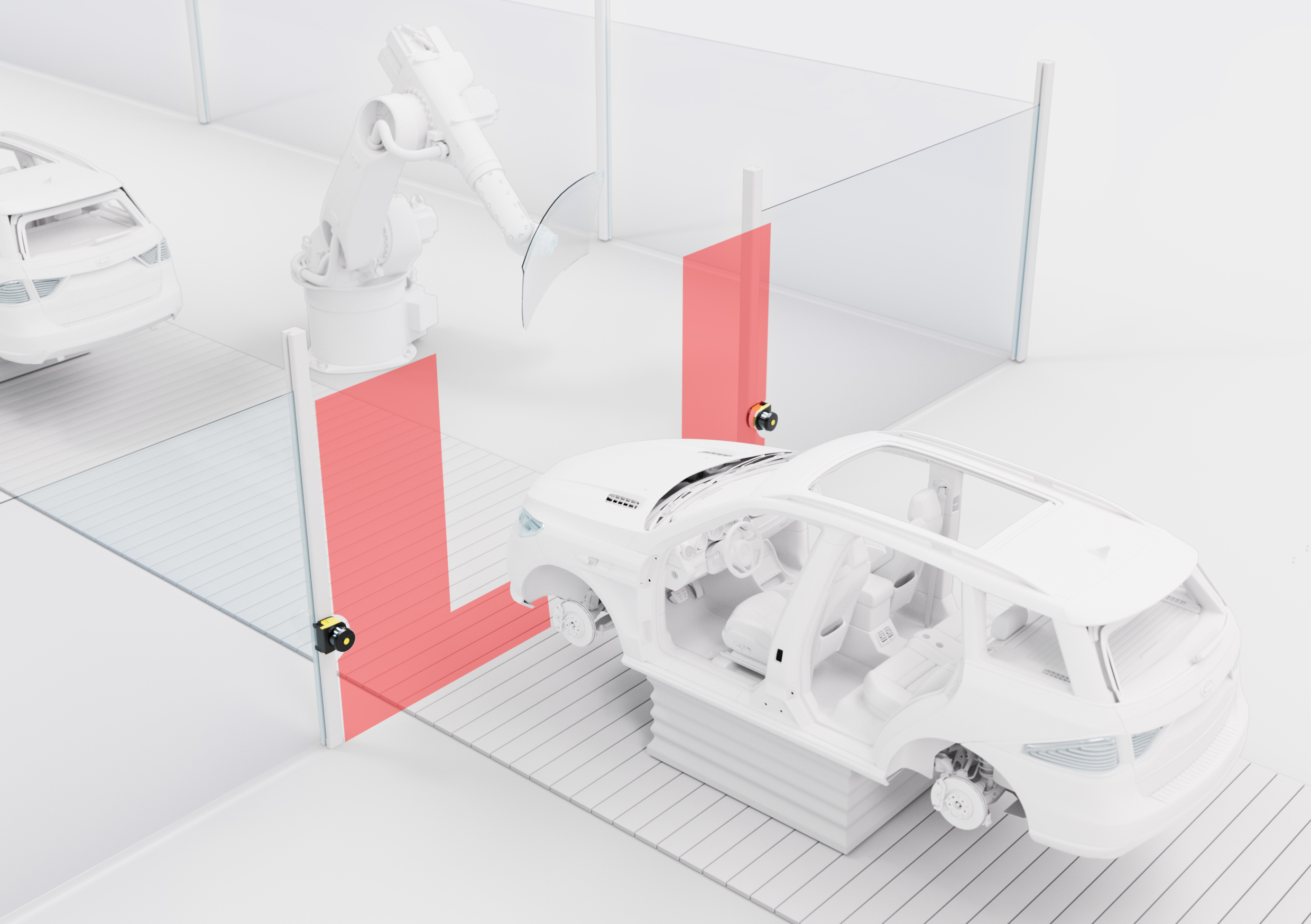
Requirement:
The inward/outward transport interfaces at skillet transfer areas must be guarded against access by persons. The safety concept must allow different body variants to be transported. Persons moving alongside the skillet must also be detected.
Solution:
Two vertically aligned safety laser scanners secure access to the danger zone with their protective field. The system control tells the safety system which body variant will be transported next, and the safety system adapts the protective field accordingly. The entire process is monitored for safety.
Operating principle:
Two safety laser scanners produce a vertical protective field in front of the danger zone. Before the loaded skillet enters the danger zone, the safety system receives information telling it which window needs to be opened in the protective field. This allows the loaded skillet to be transported without interruption. The access point to the side of the loaded skillet continues to be guarded. After the loaded skillet has passed through the protective field window, the protective field is reset to its original, closed state. The entire process is monitored for safety.
Advantages for you
- Continuous monitoring of the entire access area
- Gapless safety during the transport cycles
- High reliability and availability
- Low space and service requirements
- Optimum manipulation protection; the protective device cannot be bypassed unconsciously
- Easily retrofittable
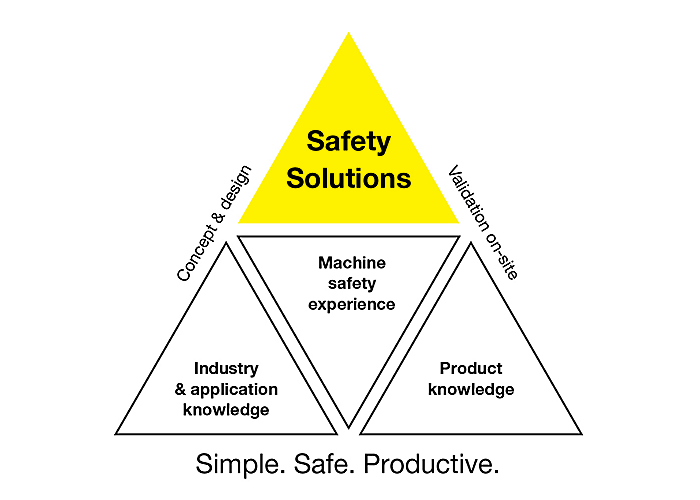
System components and safety parameters
Safety sensors: RSL 400 safety laser scanner | |
System control: MSI 400 safety control or Siemens SIMATIC S7 |
|
Leuze safety program | |
PL d in accordance with EN ISO 13849-1, SILCL 2 in accordance with IEC 62061 | |
2-channel safety output |