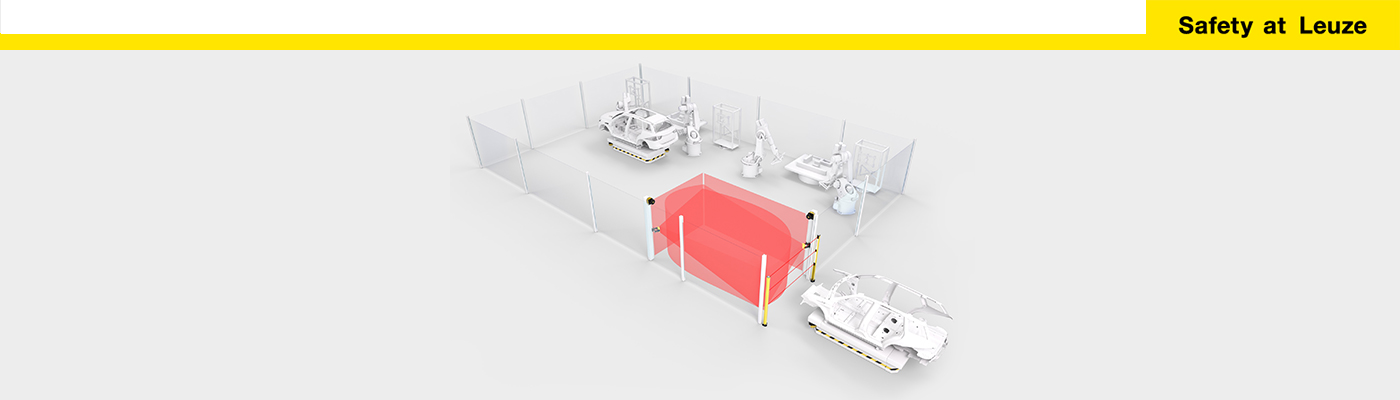
Bidirectional AGV gate for access guarding
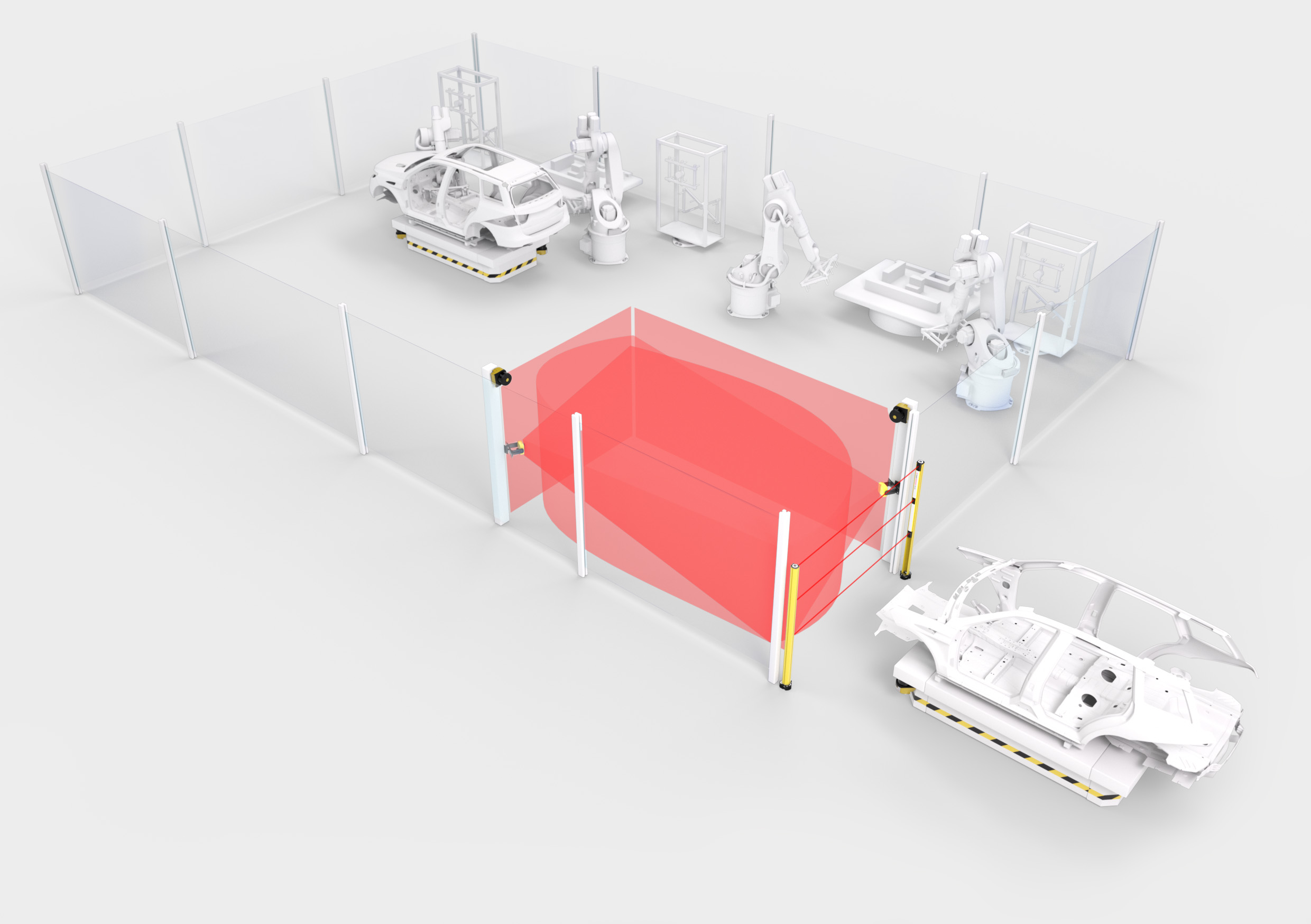
Requirement:
Solution:
A safety gate has optoelectronic safety sensors on three sides. This allows the AGV’s transportation path toward the danger zone to be freely selected. Safety radar sensors check whether persons are present within the gate area. After a corresponding release has been given, the AGV can continue its journey.
Operating principle:
After interruption and subsequent release of the multiple light beam safety device on the access side, radar sensors monitor the gate area for the presence of people. Only when no person has been detected in the interlock area is the release given for the AGV to continue its journey (entry) or to prepare for the next AGV (exit). The system monitors whether the processes are being performed correctly in terms of safety, and also enables a temporary stop in the adjacent protective fields. In addition, release signals for automated movements are also provided.
Advantages for you
- Gapless safety during the entire cycle without restricting parts transport (for loads of any shape and size)
- Optimum utilization of the system through interruption-free operation, even when the AGV is entering and exiting
- Free routing of the AGV’s transportation path toward the danger zone because no hard guards are necessary
- No operator action or visual checking of the gate area necessary
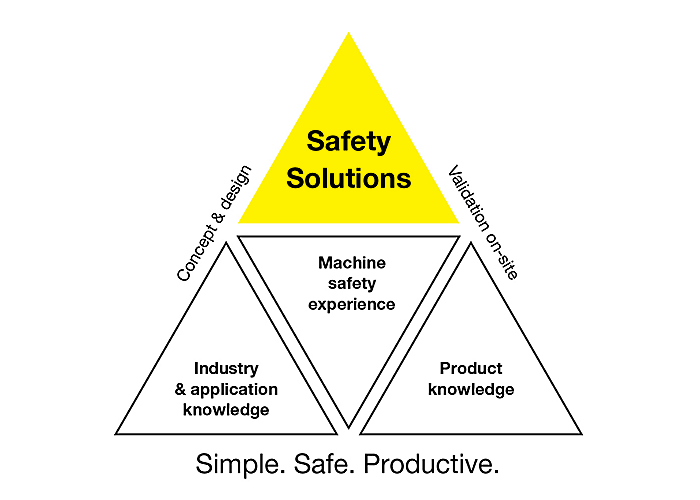
System components and safety parameters
Safety sensors: MLD 500 multiple light beam safety device, RSL 400 safety laser scanner, LBK safety radar system |
|
System control: MSI 400 safety control | |
Leuze safety program | |
PL e in accordance with EN ISO 13849-1, SILCL 3 in accordance with IEC 62061 | |
2-channel safety output |