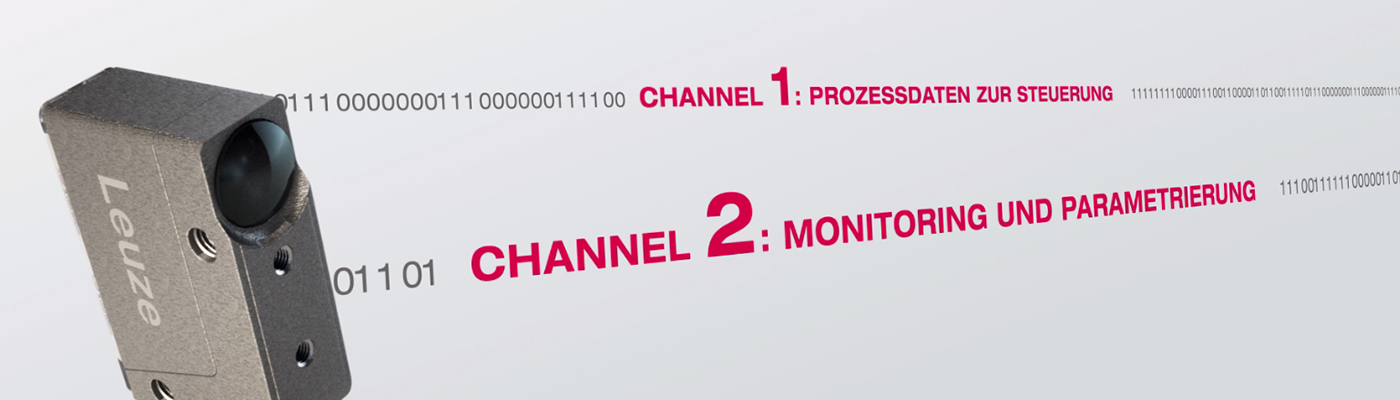
The dual channel principle
The rise of digitization also means that known processes and procedures are subject to change. Standards that have been valid and established thus far are now under examination, done away with entirely, or may need to be adapted. In many regards, there is a sense that the world is becoming increasingly complex, thus requiring a new level of expertise and strategies to successfully master the challenges of the future. For this reason, Leuze electronic is developing smart sensors to optimize the production processes of its customers and increase the productivity of their systems and machines. See exactly what dual channel means in the following video.
What does digitization and Industry 4.0 mean?
The primary idea behind Industry 4.0 and IIoT is to standardize data and the way it is exchanged across all system borders and all the way up to the cloud. Most of this data is generated with the help of sensors. Their job is to capture process variables and transfer these in the form of data to the receiving systems via the interface(s). These process data are basically the original data for solving the actual automation task.
A varying amount of data is available depending on the sensor type. The interfaces used are optimally adapted to the complexity of the data transmission: basic binary switching sensors transfer the process value, status, and diagnostic messages via the IO-Link point-to-point communication interface. More complex sensors with a higher degree of functionality are often integrated in fieldbus networks with real-time capability. They also transfer multiple process and alarm values, as well as status and diagnostic messages and can be fully parameterized via the control system.
Industry 4.0 also puts more focus on other issues, such as recipe and format changeover as well as condition monitoring and predictive maintenance. The data required for this is usually not mandatory for the automation task, but it helps users to increase system availability by scheduling preventative maintenance intervals. The data is collected from a wide variety of sources and gathered in a central location, such as a cloud, for example. Even though the data is updated infrequently, there can still be a significant data volume, thus giving the communication a different character.
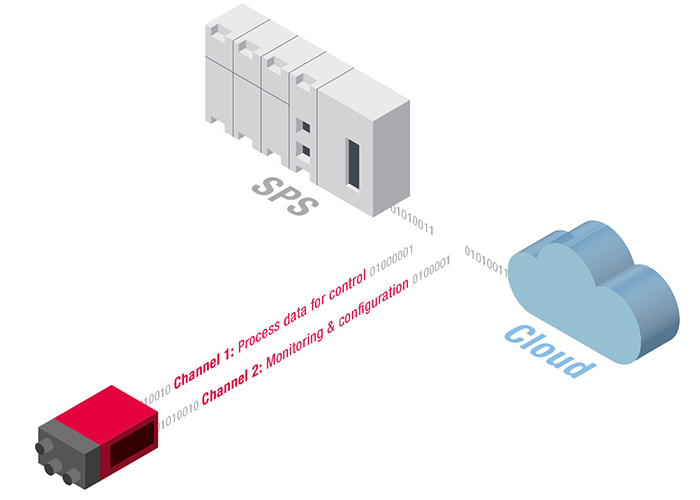
What communication solutions related to IIoT and Industry 4.0 are offered by Leuze?
Leuze optimally supports this different communication characteristic by means of the dual channel principle. While the data for process control is transferred in real time over the first sensor channel, the second sensor channel transmits the information for monitoring and analyzing the machine. The principle is the same for all sensors with an interface(s), regardless of the sensor's complexity.
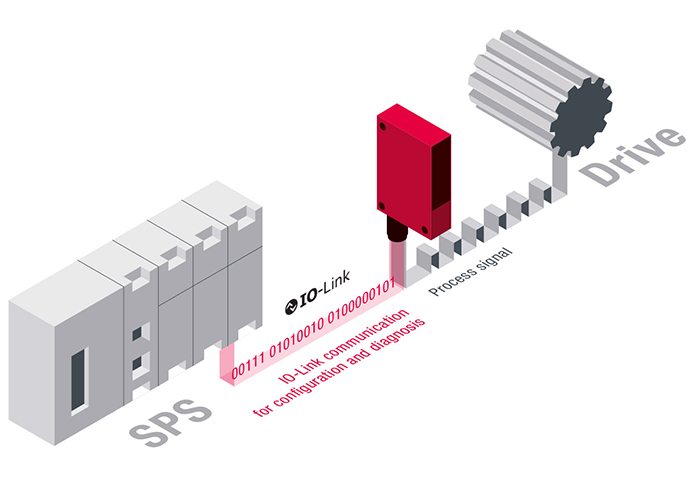
Dual channel with binary-switching sensor
1. Dual channel connected to PLC
With the KRT 18B contrast sensor, for example, which is used in a high-speed packaging machine for determining an exact cut mark position, the packaging quality of the machine depends on the real-time capability of the switching output. For this reason, it is better to not loop the switching output of a contrast sensor via a controller, instead it should be connected directly to an actuator. In order to still allow for monitoring and analysis of the machine, the contrast sensor also features an IO-Link communication interface, in addition to the fast switching output. This interface can be used to monitor the process value, determine the function reserve, and carry out configurations. It also supports customers in changing recipes or switching over formats.
2. Dual channel and IIoT / Industry 4.0
IIoT and Industry 4.0 require data that is as location-independent as possible and available worldwide to other automation participants, for example, for the purpose of monitoring and configuration. This is usually accomplished via cloud solutions. If the same preconditions as described above prevail, then a connection to an IO-Link coupling module with Ethernet interface and OPC UA communication protocol is required, instead of the IO-Link connection to the PLC. The connection to the cloud is then implemented via an IoT Edge Gateway, for example.
Dual channel with sensors with fieldbus interface
Dual channel and IIoT / Industry 4.0
For more complex sensors with an integrated fieldbus interface, Leuze electronic also offers a dual channel solution. The BCL 348i bar code scanner, for example, has a PROFINET fieldbus interface. In principle, process and alarm values, detailed status and diagnostic messages and the complete device parameterization can be carried out from the control via this interface. However, if the data needs to be available location-independent and worldwide, the sensor offers this via its industrial Ethernet interface with the OPC UA communication protocol. It can be transported all the way to a cloud application via an integrated cloud connector or an IoT Edge Gateway.
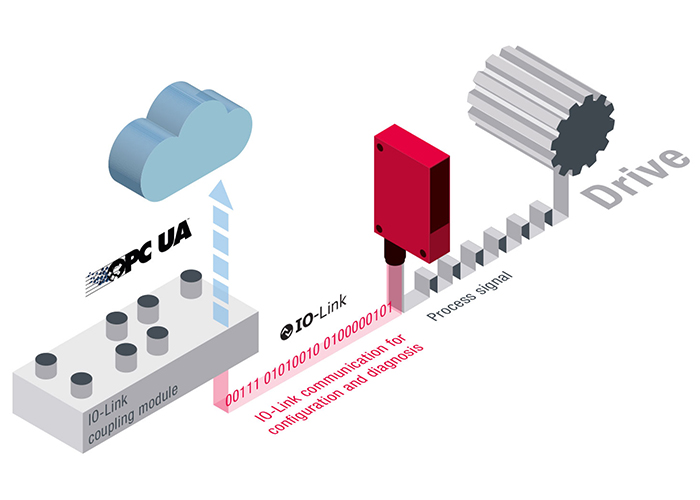
Advantages of the dual channel principle from Leuze
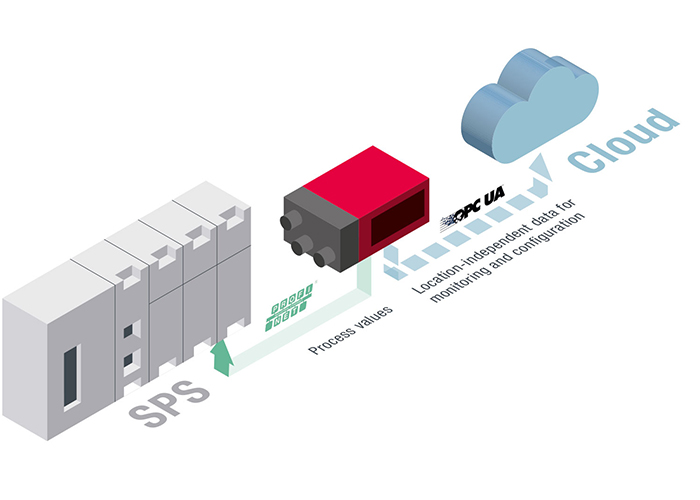
Issues such as condition monitoring or predictive maintenance, which are a big part of IIoT and Industry 4.0, require sensors that are capable of making data available worldwide and in a standardized format. In general, it must be determined what the real-time capability requirements are. The dual channel principle makes it possible for the first time to make data available separately and according to customer requirements. Real-time data is transferred via channel 1, and data for process monitoring and configuration via channel 2.
Traditional IO-Link interfaces for binary-switching sensors that allow either the switching signal or point-to-point communication with the sensor on request in SIO mode (standard IO mode), are not capable of this. This is because both pieces of information are required in parallel for process control. For the customer it must be possible, e.g., to continuously evaluate the process values of a contrast sensor, switching reserves to the threshold values, or the state of contamination in the packing process of a packaging machine online, in order to detect deviations from the target state early on. This is exactly what the dual channel principle helps with.
For sensors with fieldbuses, real-time capability and data for monitoring and configuration is provided, at least for real-time Ethernet interfaces, but only locally and not location-independent and worldwide. And most of the time, the information provided by the sensor for condition monitoring or predictive maintenance is not evaluated. The Leuze dual channel principle also offers the right solution for this.