Punching machine and laser-cutting machine
Punching machines and laser-cutting machines separate very quickly and precisely smaller parts from large sheet metal plates. When processing sheet metal plates with punch presses or with laser cutting, safety at work plays an important role, as work is performed with high pressure and high-energy laser beams. In addition, the sensor system used must be able to detect very small stamping parts to ensure a fault-free production process.
Our sensor solutions reliably and flexibly safeguard hazardous areas. And do so with maximum protection for people and with minimal influence on the workflows. Moreover, sensors check for tool availability, prevent collisions and monitor the ejection of the sheet metal parts being processed.
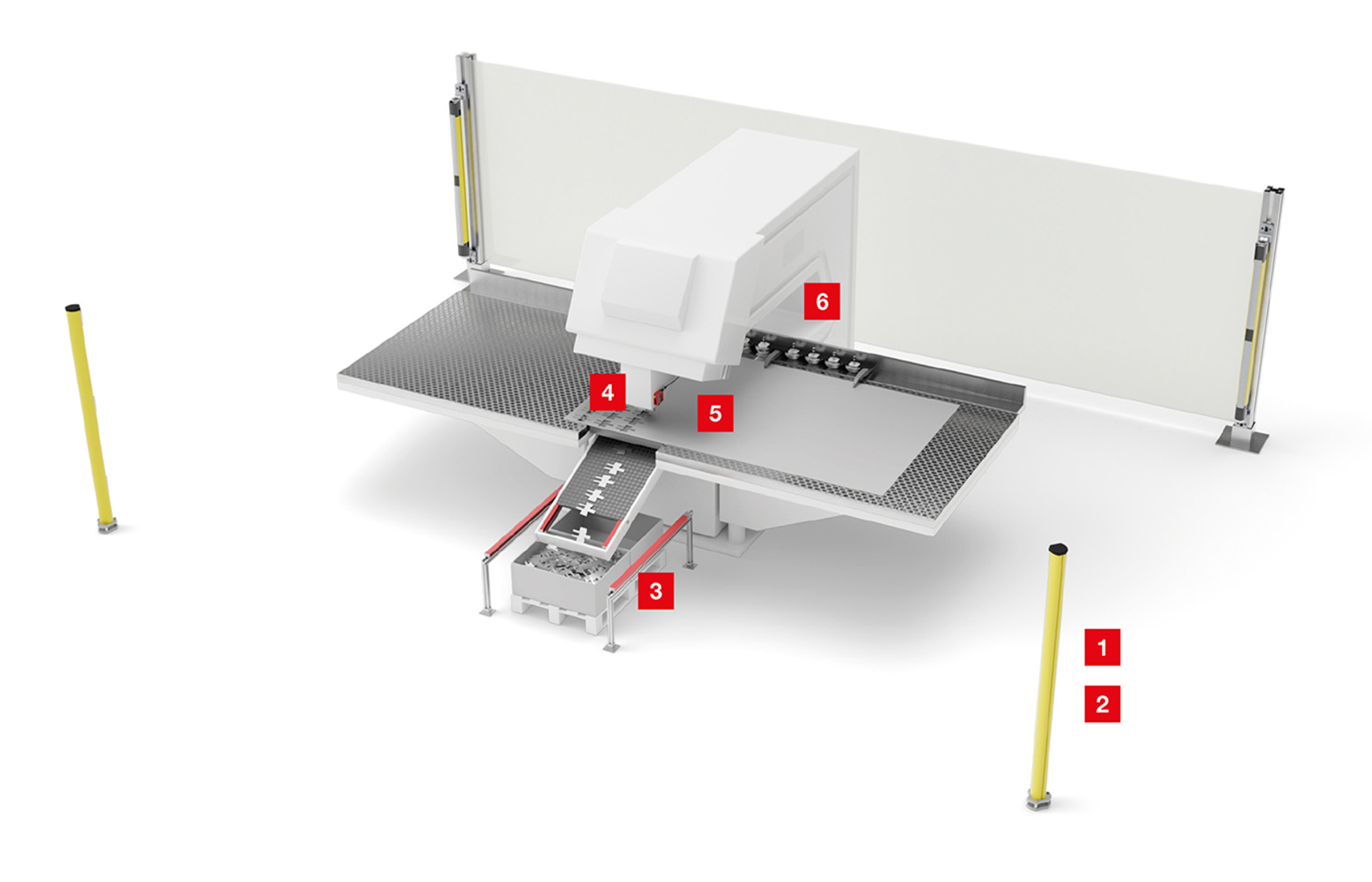