Tower storage system
Intelligent solutions for the storage of sheet metal plates and long goods optimize material flow, improve machine utilization and improve work safety and process reliability. Through the compact design of a tower storage system, it is thereby possible, for example, to optimally utilize valuable production space as an intermediate warehouse, buffer storage or for material stockage.
Our components guarantee smooth processes and ensure safety. Typical areas of use are access guarding at dangerous areas of machines and systems. Our inductive and optical sensors check and monitor the presence and position of sheet metal plates or stacks. And they optimize the process flow, thereby ensuring high availability of the machine or system.
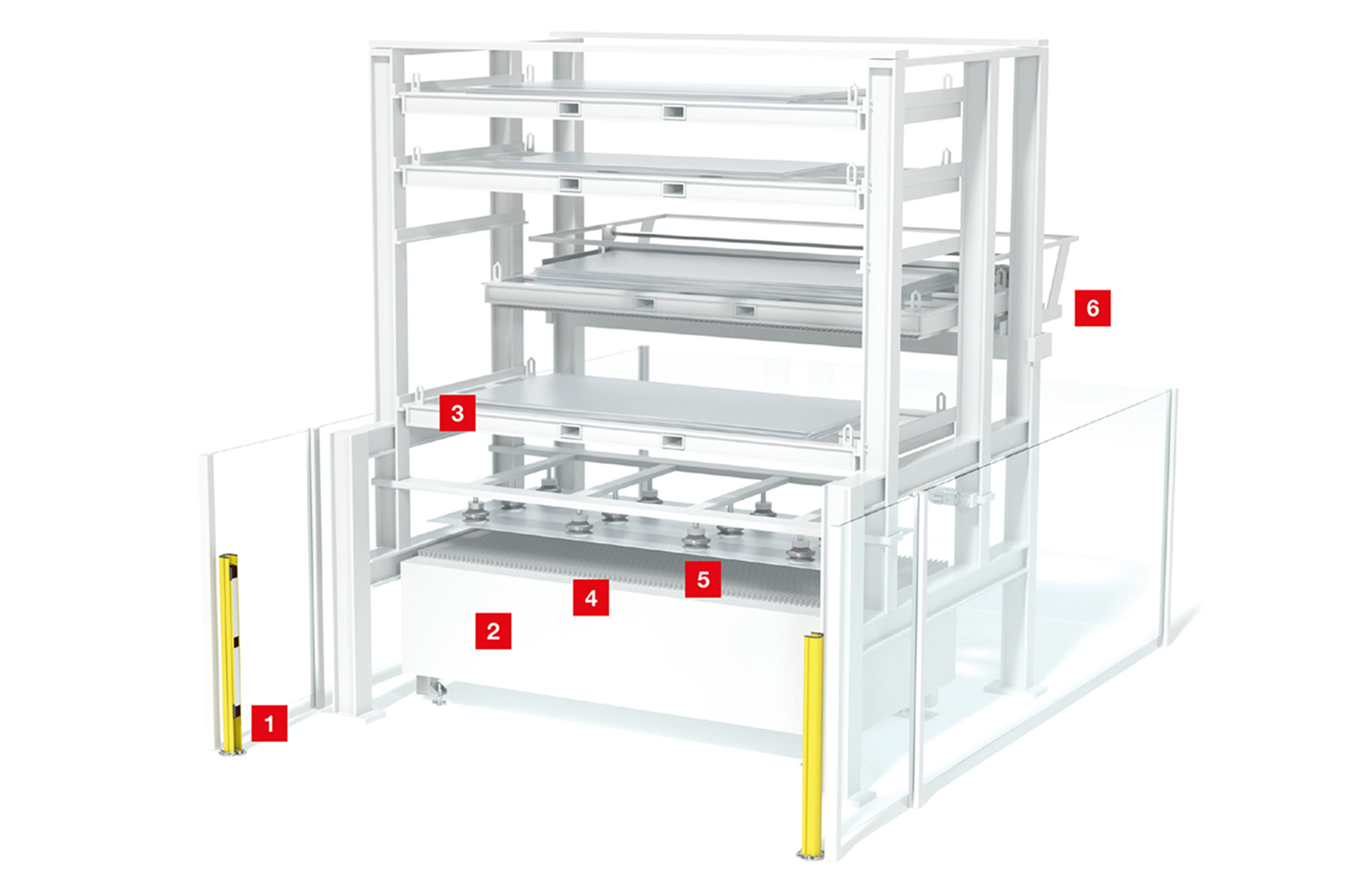