Focus on stacker cranes: Four optimization potentials with sensors
Optimization potential 1: Greater design freedom
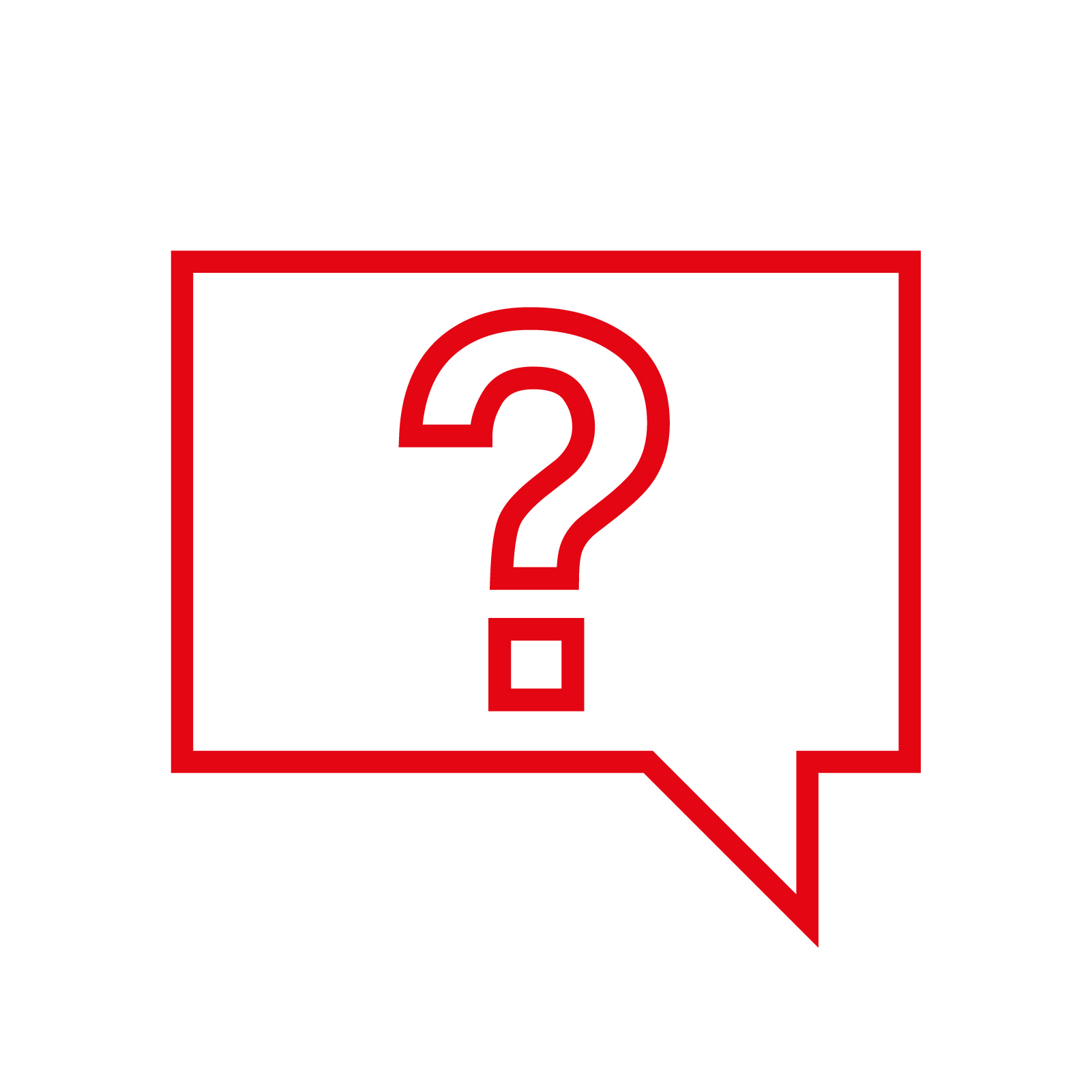
Problem: Design constraints
Is the mounting position, on the stacker crane, of your existing laser positioning system compromised by the size or the specification device?
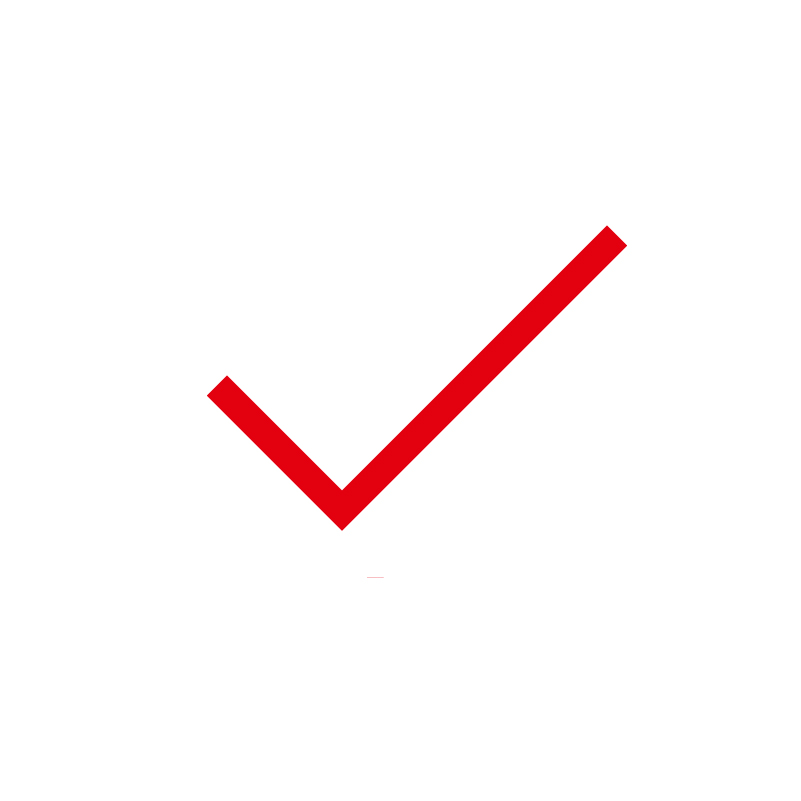
Our optimization for you: the most compact laser positioning system on the market
The small design in combination with the minimal dead zone of just 100 mm makes the new AMS 100i the most compact laser positioning system on the market.
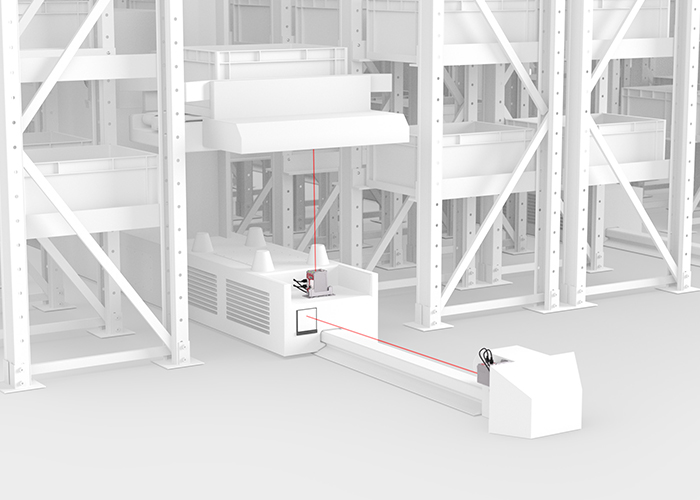
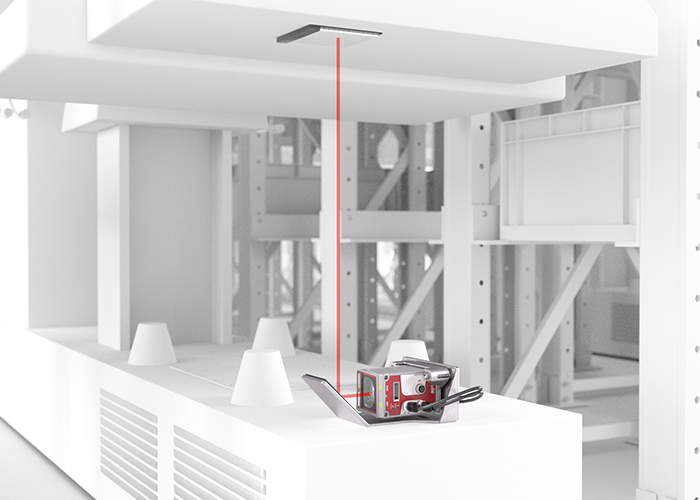
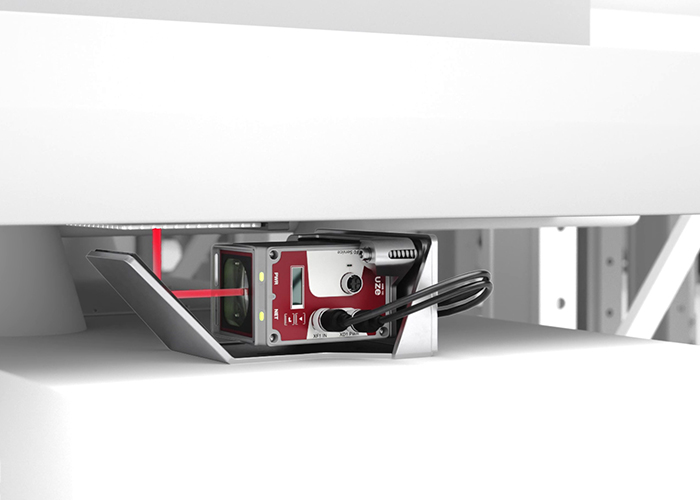
Solving positioning tasks on stacker cranes using the new AMS 100i has the following advantages:
- Maximum design freedom thanks to the small housing (105 x 68 x 75 mm)
- Modular installation options and easy alignment
- Positioning possible up to a close range of 100 mm
- Interference-free mounting directly next to an optical data transceiver
- Attractive price/performance ratio
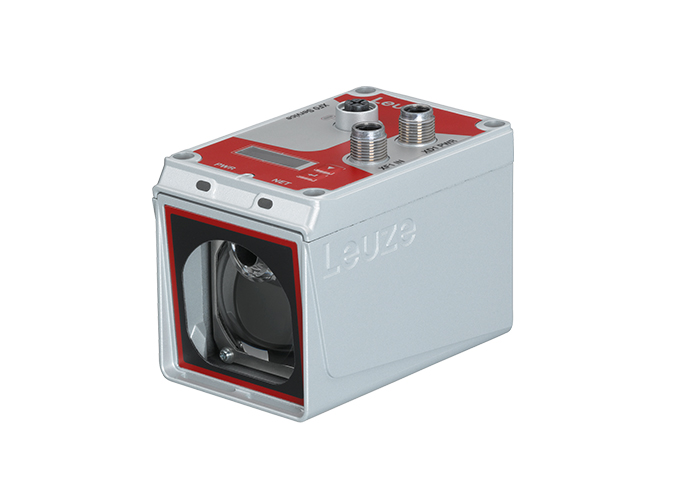
Optimization potential 2: Faster commissioning
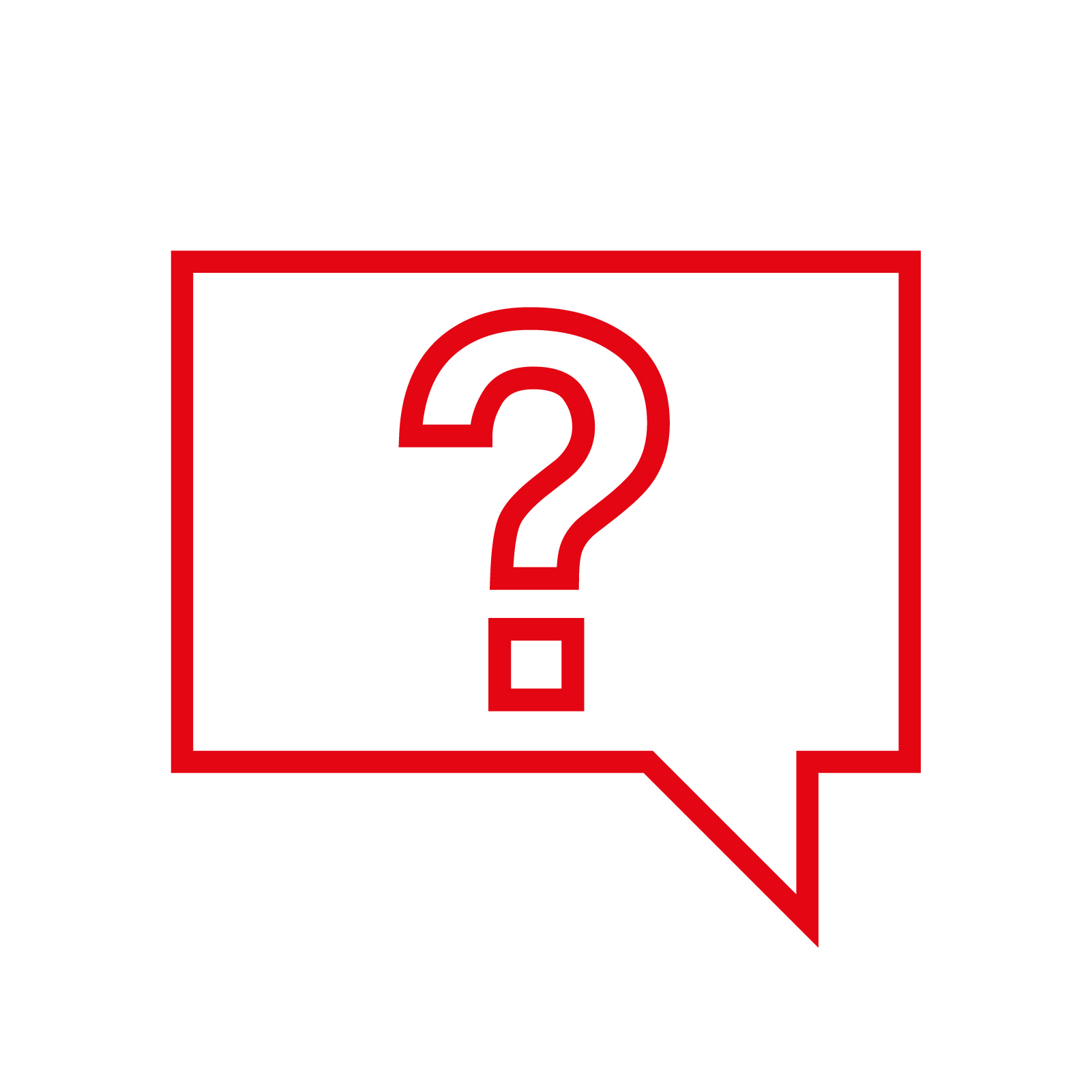
Problem: Wiring, mounting and alignment of multiple sensors
In the compartment fine positioning of stacker cranes, the standard solution involves
the use of multiple sensors, all of which must be mounted, conected and aligned.
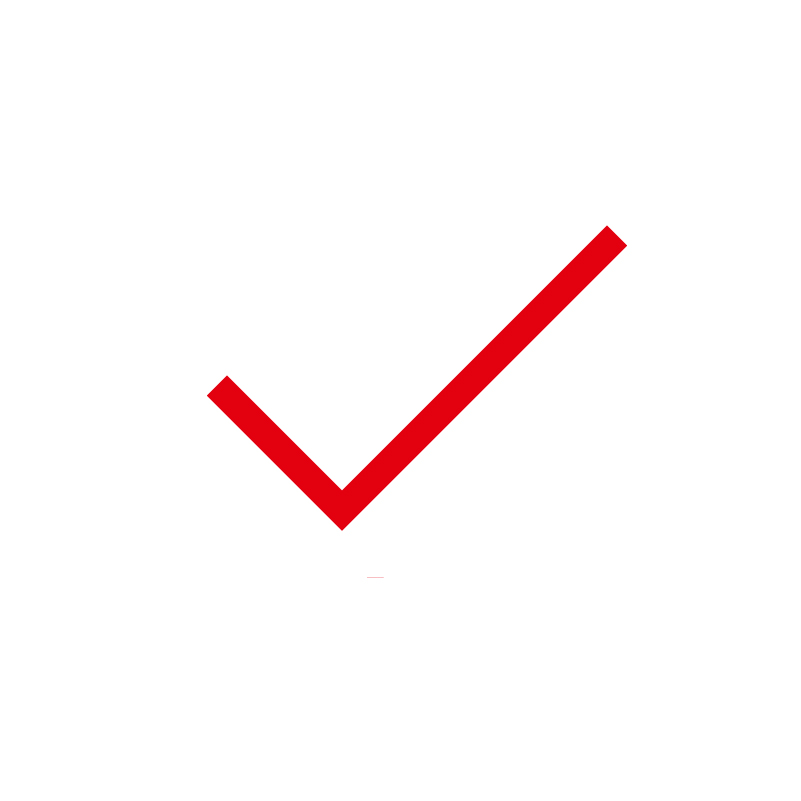
Our optimization for you: one single camera-based sensor is sufficient
A camera detects circular holes and reflectors. It determines the position deviation in the X and Y direction relative to the nominal position and passes the position deviation to the controller via an interface or I/Os.
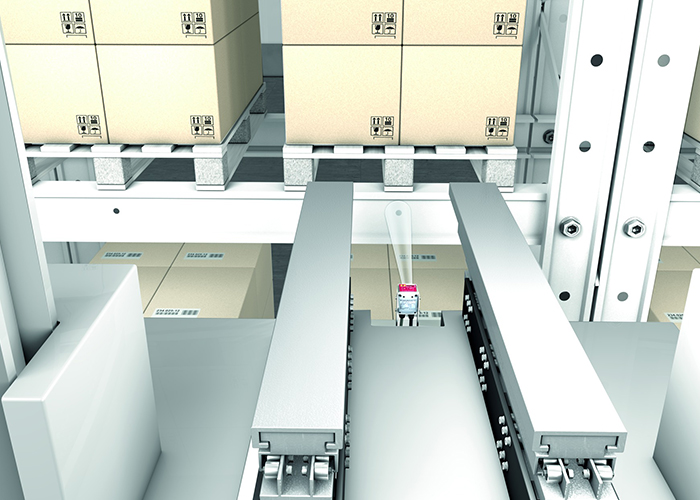
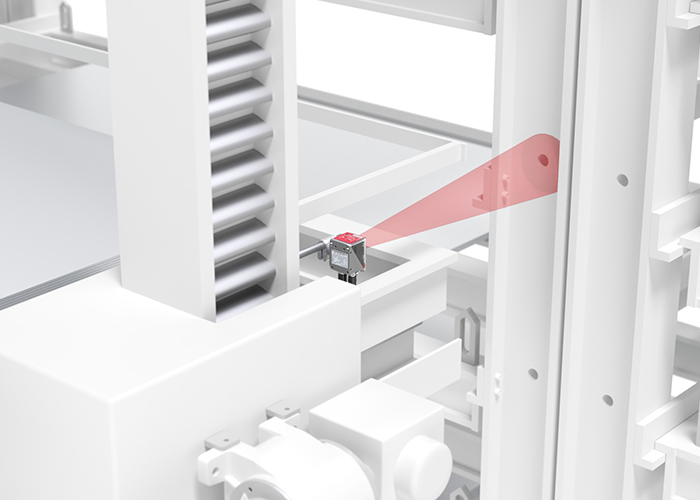
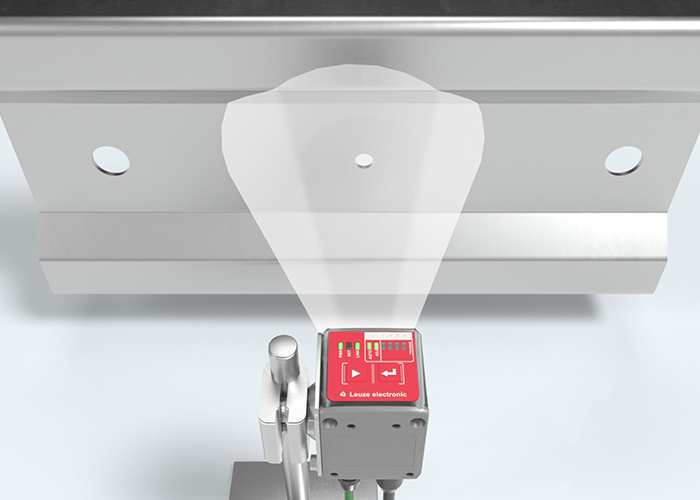
Compartment fine positioning of the stacker crane using a camera-based sensor such as the IPS 200i/400i has the following advantages:
- Wiring of just one sensor
- Mounting and alignment of just one sensor
- Quick and easy setup and configuration
via an integrated setup wizard
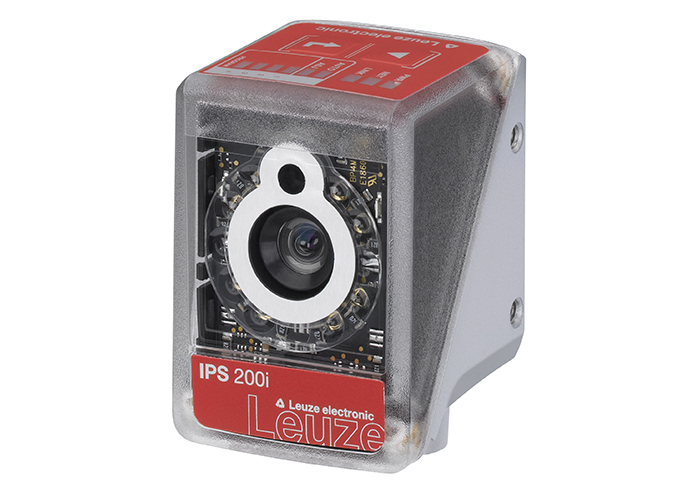
Optimization potential 3: Updated safety requirements
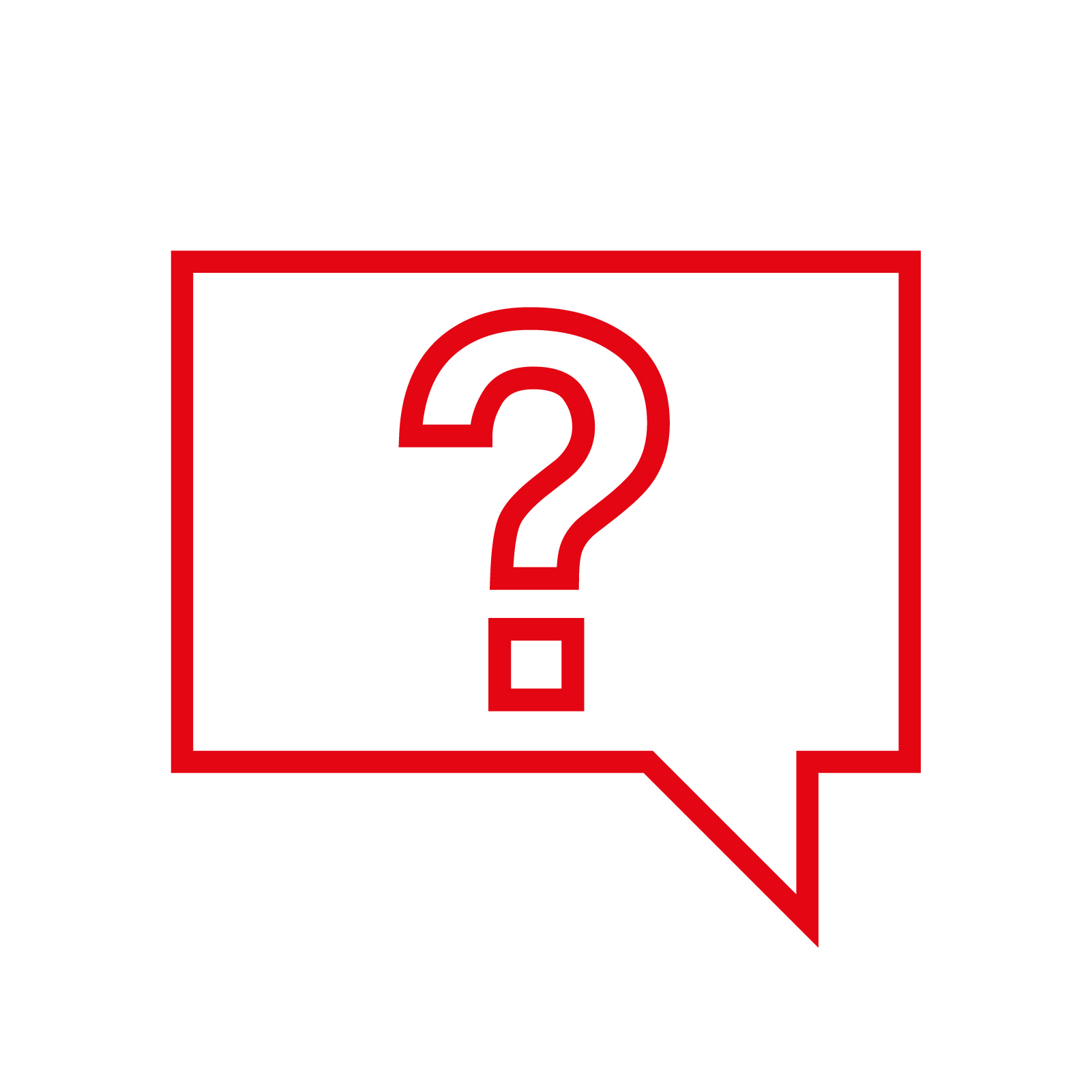
Problem: Adaptation of existing solutions and sensors to meet the safety requirements
The safety standard stipulates safe position detection under certain conditions:
- If a person is on the stacker crane while it needs to be moved – e.g. for maintenance work or for operation (e.g. during commissioning)
- If a person is in the aisle to carry out maintenance work. The stacker crane must safely maintain its position or it must be possible to move the stacker crane at a safe speed.
- A safe speed can allow the buffer zone at the end of the aisle to be reduced.
The standard solution is to use two diverse sensors with a maximum achievable performance level of PL d.
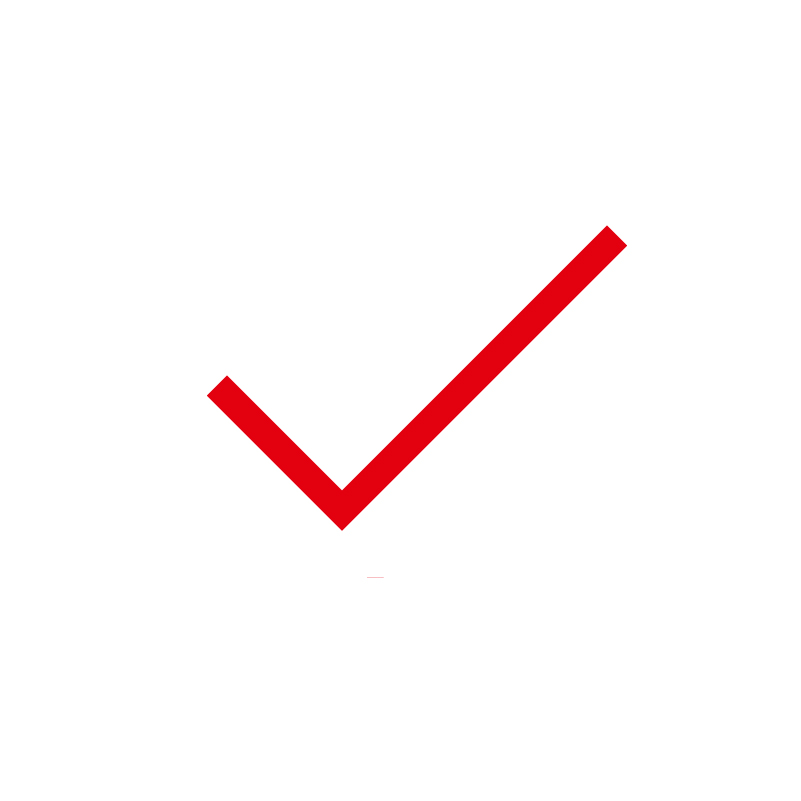
Our optimization for you: the safe bar code positioning system with a maximum achievable performance level of PL e
The world's first safety bar code positioning system, FBPS 600i, requires just one sensor for safe position detection. The device is connected to a safe evaluation unit – e.g. on a frequency inverter – via two SSI interfaces.
More information on the FBPS600i
Safe position detection of the stacker crane using the FBPS600i has the following advantages:
- Safe position detection with just one device
- Meets the requirements for PL e / SIL 3
- Low space requirements and short fault reaction time of 10 ms for use on fast stacker cranes
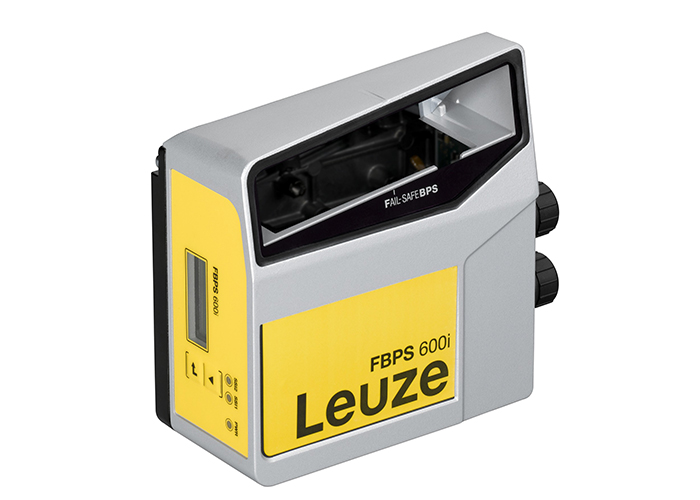
Optimization potential 4: Increase in system availability
Intelligent sensors can help increase the system availability. To achieve this, either additional functions of existing sensors are used or special sensors are implemented.
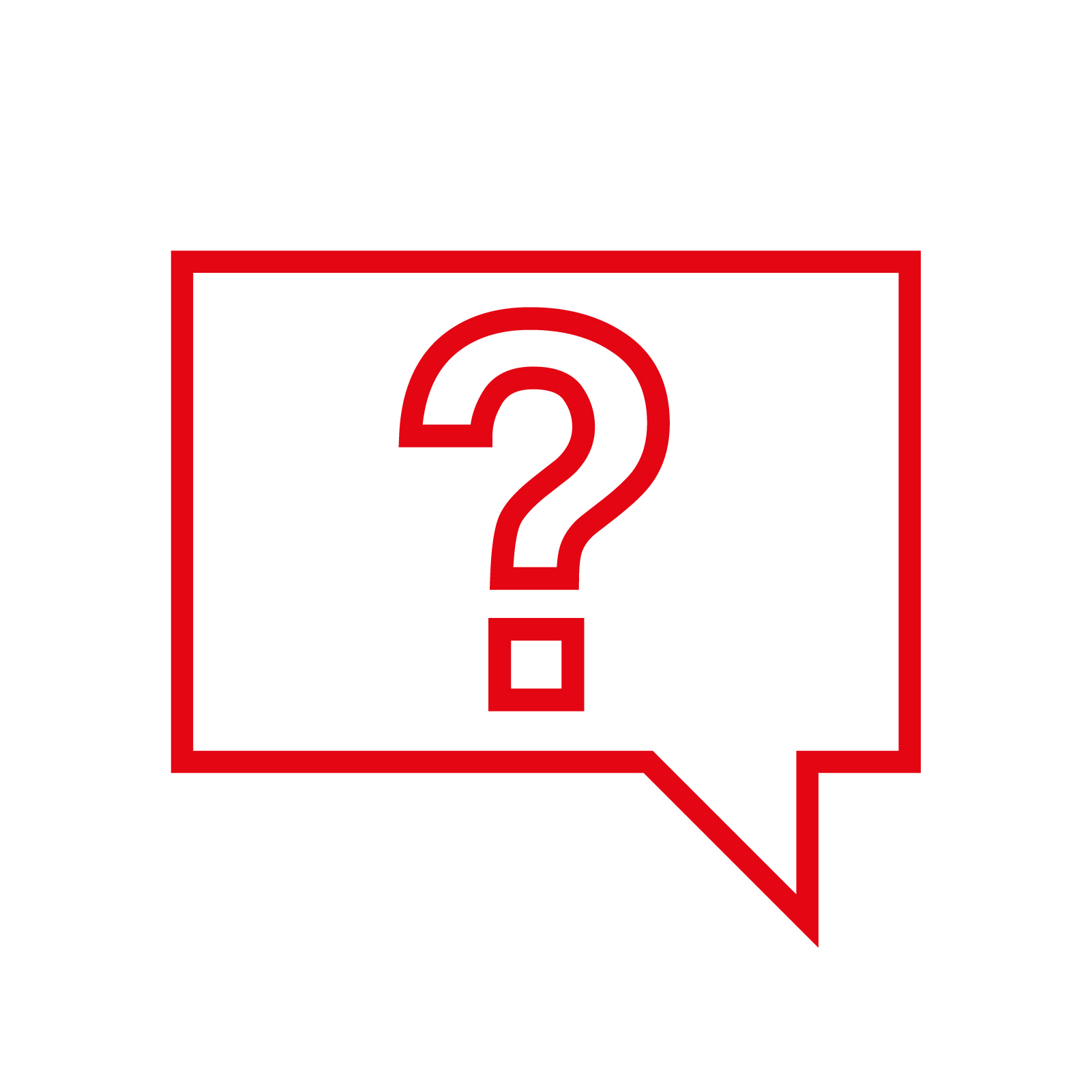
Problem: Faults, downtimes or unscheduled maintenance work
Faults, downtimes or unscheduled maintenance work are the worst-case scenario in intralogistics. Even the failure of just one component in a system reduces efficiency or brings the system to a complete standstill.
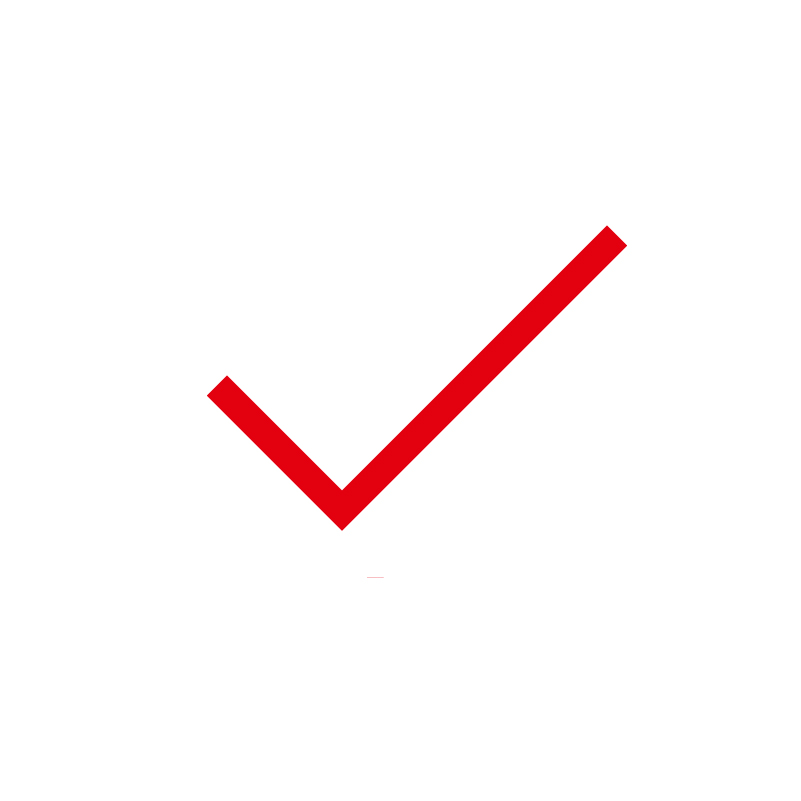
Our optimization for you: condition monitoring and predictive maintenance through contamination control and quality score
The contamination control and the quality score constitute a warning threshold at which the sensor still functions safely but signals that intervention is necessary. In order to ensure that the sensor continues to function properly, its front screen should be cleaned, for example. Or the opening for compartment fine positioning has changed and must be checked.
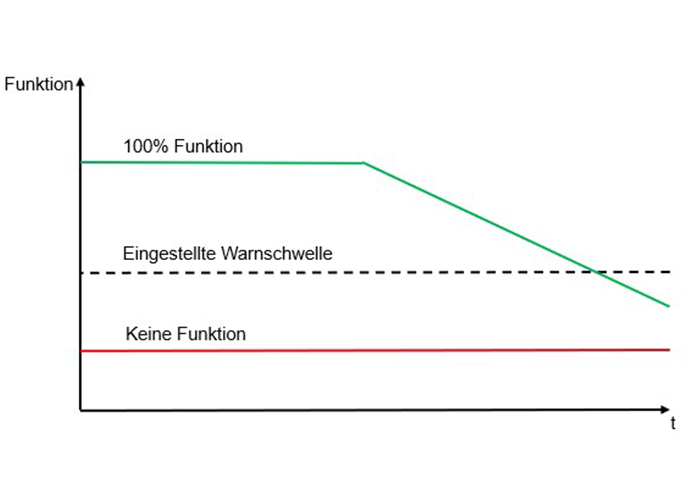
Through additional functions, the devices of series AMS 100i (laser positioning system), DDLS 500 (data transmission photoelectric sensor), BPS 300i (bar code positioning system), FBPS600i (safe bar code positioning system) and IPS 200i/400i (camera-based compartment fine positioning) provide the possibility of condition monitoring and predictive maintenance.
This has the following advantages:
- Maintenance can be planned
- Downtimes can be avoided
- State of the sensor can be evaluated at any time
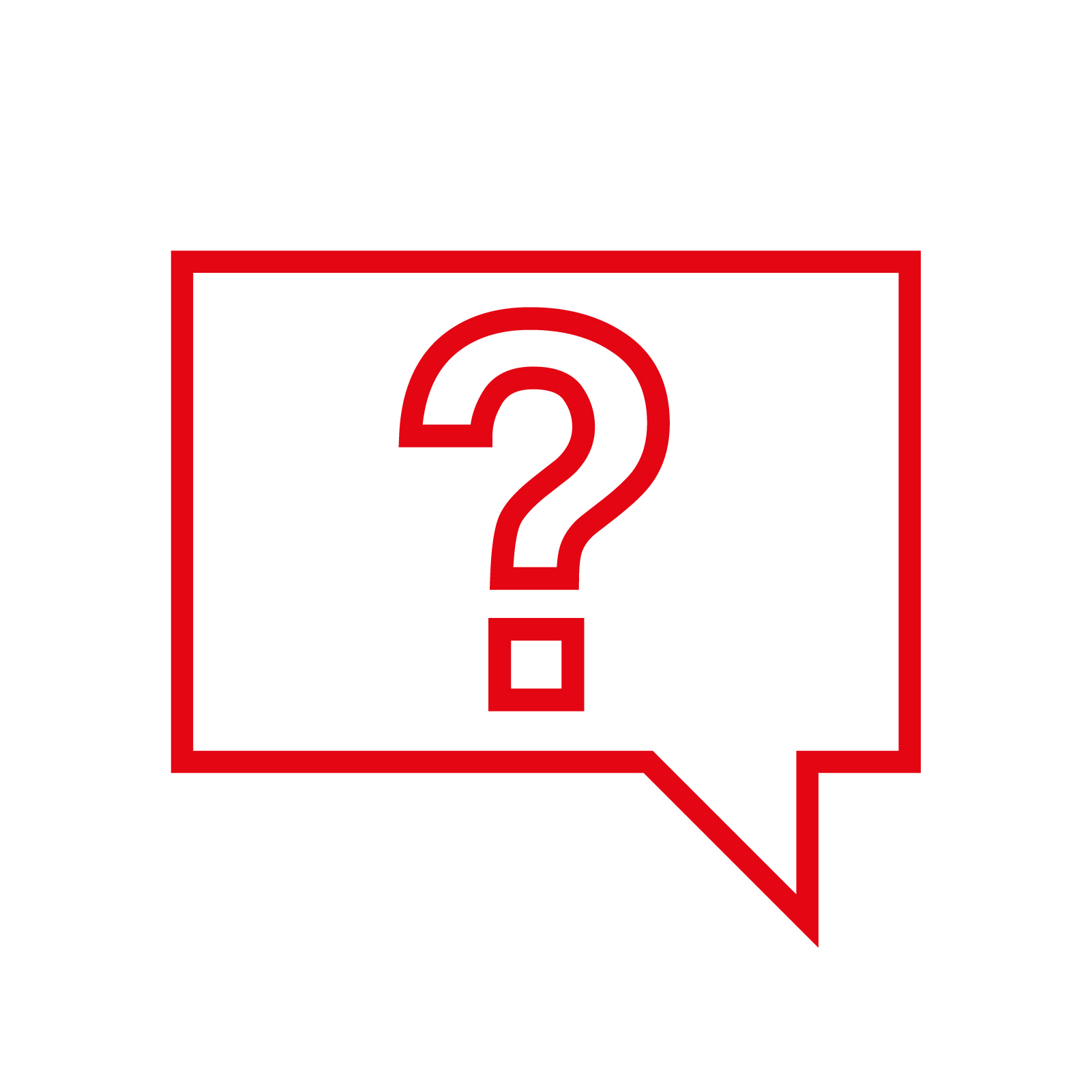
Problem: Fault in the stacker crane
The efficient flow of goods and high system availability are key criteria for the operation of logistics centers. Here, the traceability of events also plays a crucial role in enabling faults to be rectified quickly and efficiently.
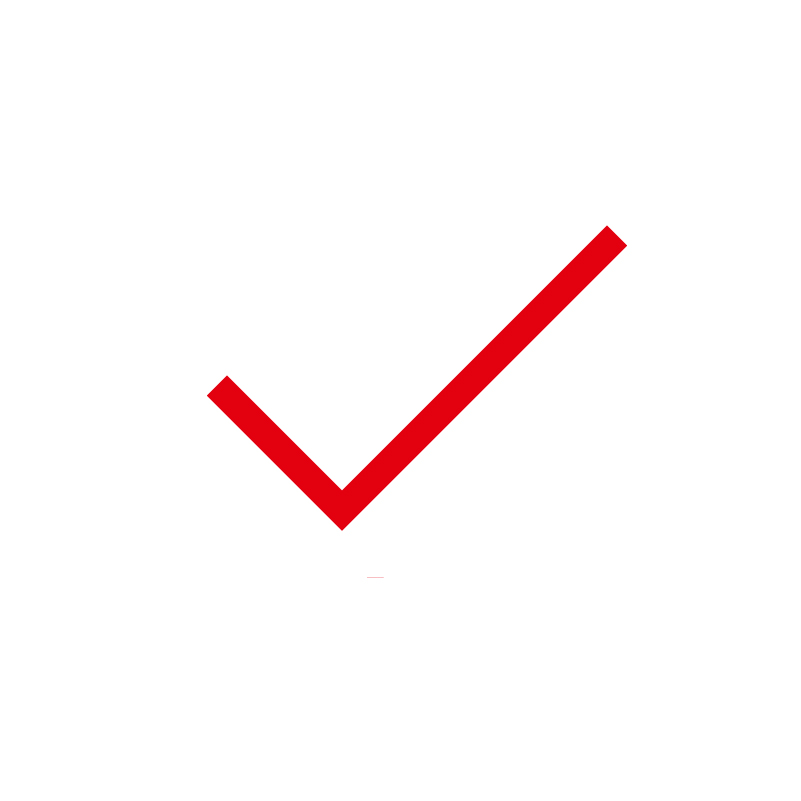
Our optimization for you: visual checking of non-visible areas on the stacker crane using an industrial IP camera
Using the new industry-standard LCAM308 IP camera, visual checks can be performed on an stacker crane in the event of a fault. Moreover, a snapshot mode is also available to capture a single image, e.g. for documenting the content of a carton.
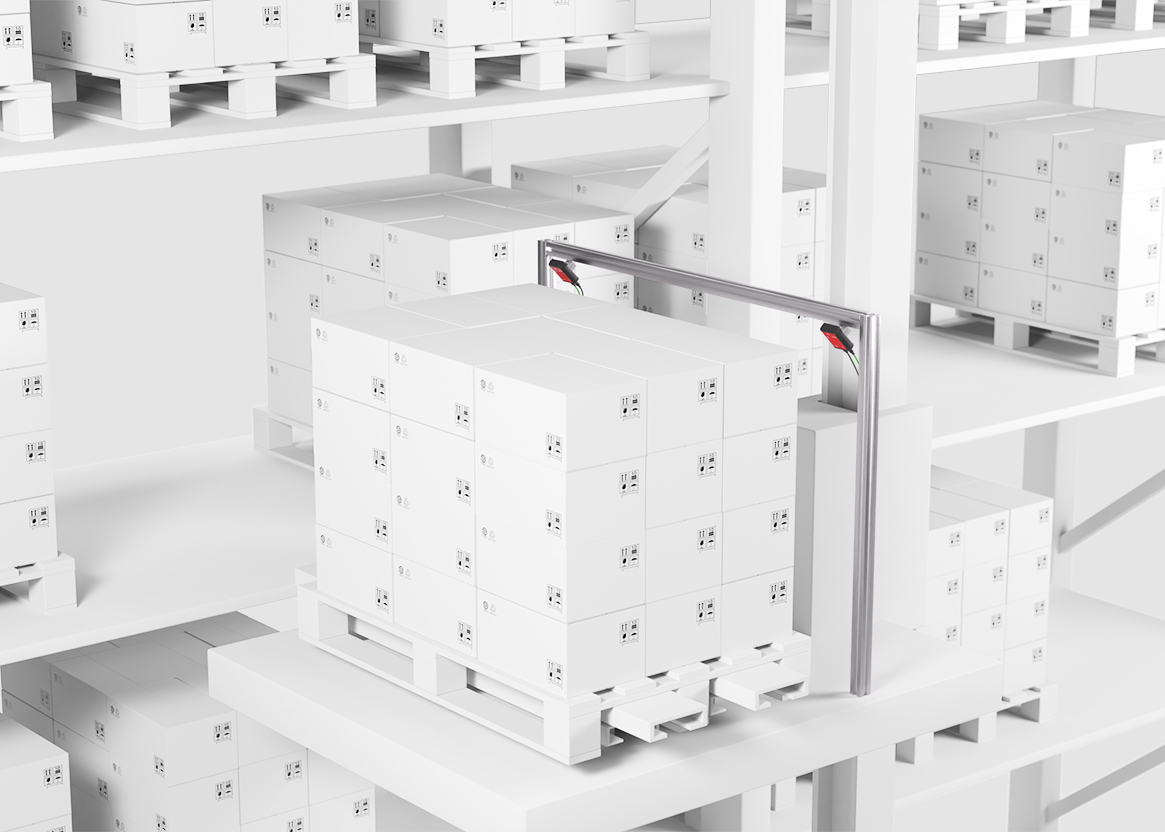
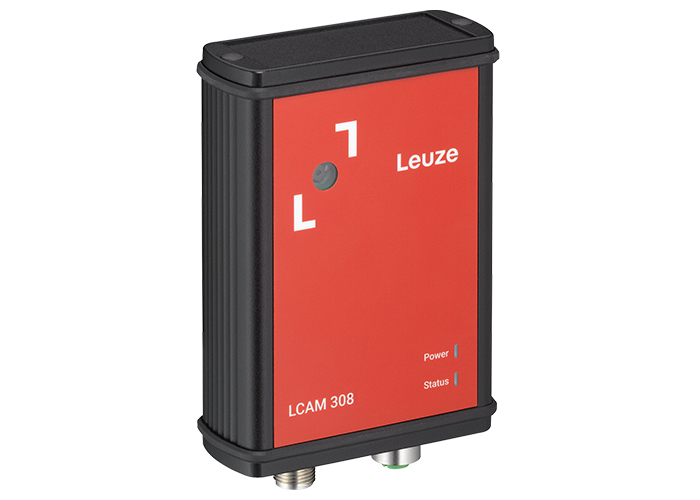
Visual checking in the event of faults on the stacker crane using the LCAM 308 has the following advantages:
- The stacker crane can be checked externally – a manual check is no longer necessary
- A live stream of the current situation on the stacker crane can be transmitted
- Once the ring memory has stopped recording, the last 60 seconds can be checked