L'atelier d'emboutissage
Du rouleau d'acier à la voiture.
De gigantesques rouleaux d'acier, en bobines, sont utilisés lors des différentes étapes de fabrication des pièces de carrosserie destinées à de futurs véhicules.
Qu'il s'agisse de la découpe des bobines ou de l'estampage, du pressage et de la mise en forme des platines, des capteurs accompagnent et sécurisent toutes les étapes de fabrication, même dans des conditions ambiantes difficiles.
Les applications sont aussi diverses que notre gamme qui leur est consacrée. Les interrupteurs inductifs et les capteurs optiques vérifient et surveillent la présence et la position des pièces. Les systèmes d'identification saisissent les données pour leur traçabilité. Sur les installations de massicotage, nos capteurs fournissent des valeurs mesurées pour la régulation de la boucle et le contrôle des arêtes.
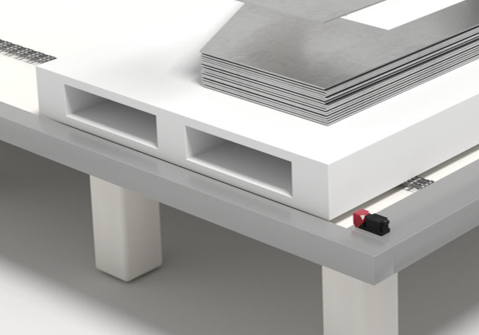
Condition :
Les platines découpées, et en partie déjà estampées, sont acheminées à l'aide de chariots élévateurs ou de systèmes de transport sans conducteur pour la suite du traitement. Avant de pouvoir retirer les pièces, il faut vérifier que la palette ou le support de charge a atteint la position de transfert. Ceci doit se dérouler sans contact.
Solution :
Les interrupteurs inductifs de la série IS 200 / 244 offrent une grande puissance et une haute réserve de fonctionnement. Selon le lieu d'installation et les distances de détection requises, les modèles cylindriques à triple distance de commutation de la série IS 200 tout comme les modèles cubiques IS / ISS 244 s'avèrent appropriés.