Sensores para sistemas de transporte sin conductor (AGV)
Los sistemas de transporte sin conductor llevan la mercancía de A a B. Los trayectos se pueden adaptar fácilmente. Así, la instalación de producción es muy flexible. Los requerimientos de dinámica y seguridad son muy exigentes. En especial, al usar varios vehículos.
Las soluciones con sensores inteligentes son los prerrequisitos para conseguir un proceso sin contratiempos y evitar colisiones. Los escáneres láser de seguridad protegen los vehículos. Nuestros sensores dinámicos y de alta resolución proporcionan los datos para la navegación precisa de los AGV. El soporte y la transferencia correctos de la mercancía se controlan mediante sensores ópticos e inductivos.
White Paper: Los AGV en el camino hacia el éxito: ¿qué tecnología es la adecuada para usted?
Los sistemas de transporte sin conductor (AGV) han transformado significativamente la intralogística durante los últimos años. La selección de la mejor tecnología de navegación para los AGV desempeña un papel crucial en el éxito de los procesos logísticos en las empresas. Pero, ¿qué tecnología de navegación es adecuada para cada aplicación? ¿Cuáles son las ventajas de las diversas tecnologías? Encontrará las preguntas a estas respuestas en este White Paper.
En este White Paper respondemos a las siguientes preguntas:
- ¿Qué tecnologías de navegación existen para los AGV?
- ¿En qué principios se basan las diferentes tecnologías de navegación?
- ¿Qué tecnología de navegación es adecuada para cada aplicación?
- ¿Qué ventajas e inconvenientes comportan las distintas tecnologías?
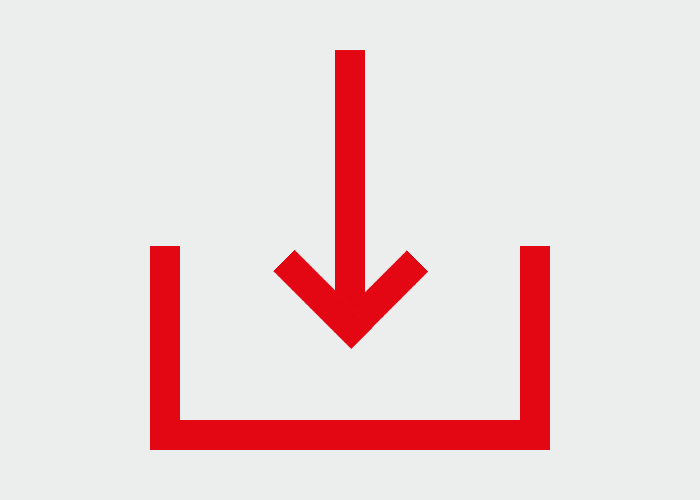
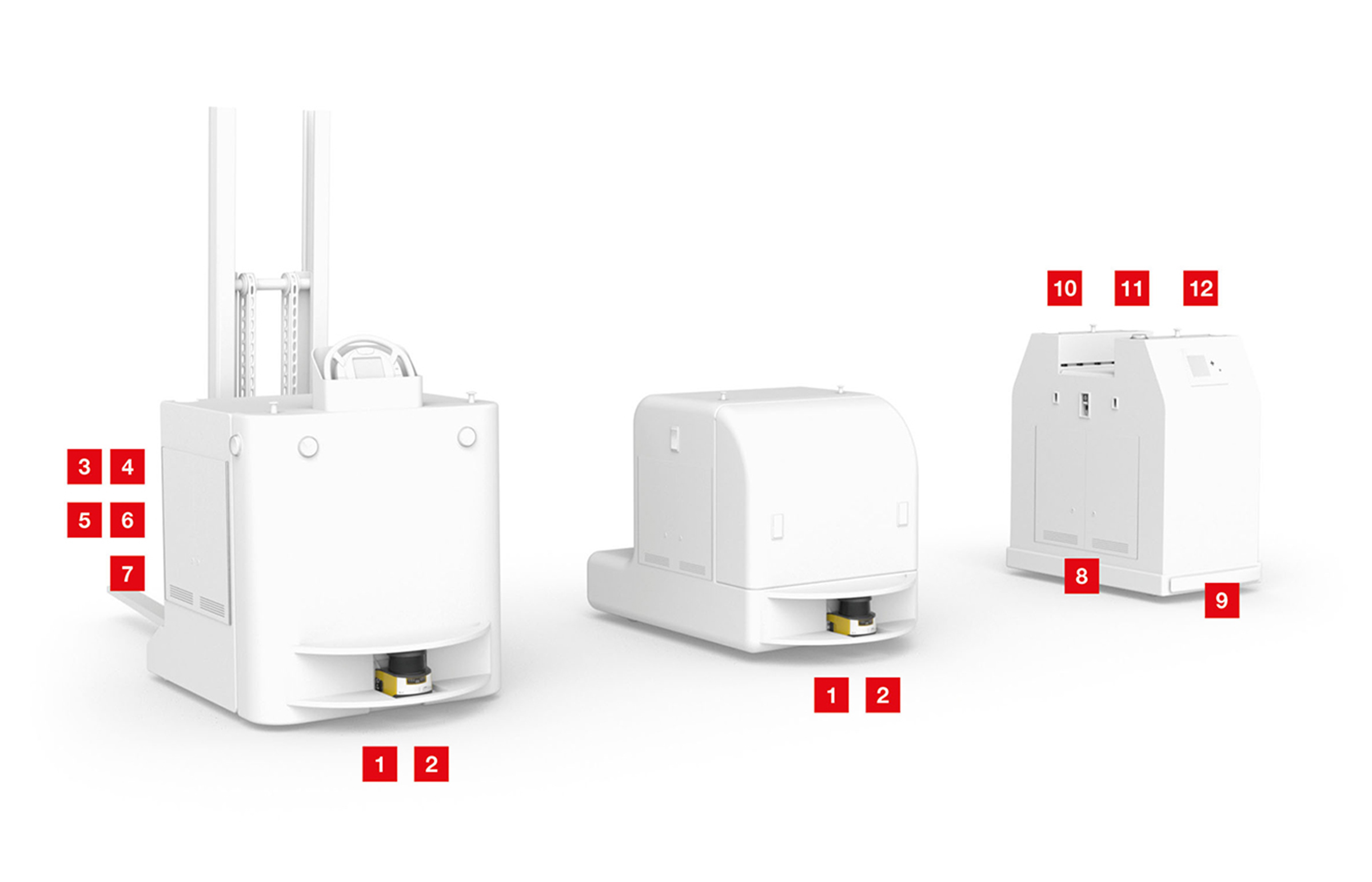
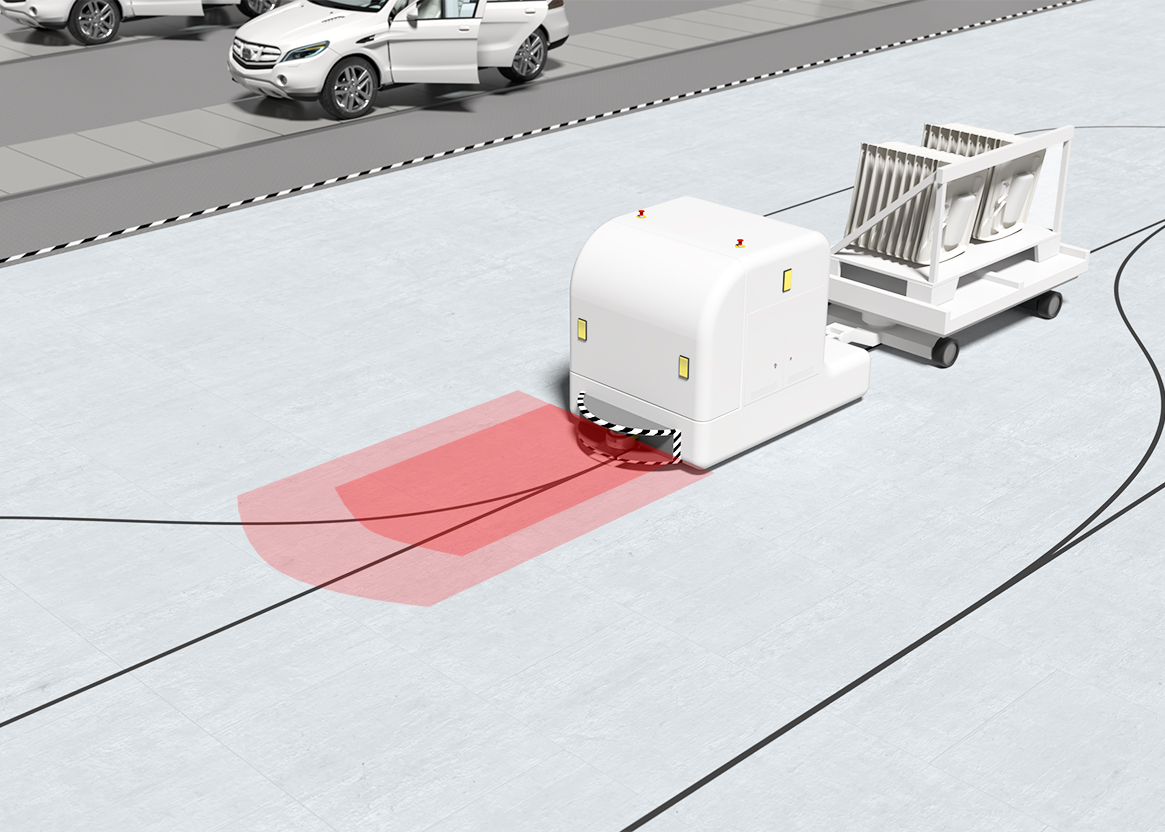
Requisito:
Para poder detener el AGV de forma segura en caso de que haya personas u objetos, debe vigilarse un área definida delante del AGV. Para adaptarse a la velocidad y al recorrido, se debe poder variar el tamaño y la dirección del área.
Solución:
El escáner láser de seguridad RSL 400 dispone de una zona de exploración de 270° y hasta 100 pares de campos conmutables. Esto permite que el campo de protección se adapte de forma óptima a la velocidad y al recorrido del AGV.
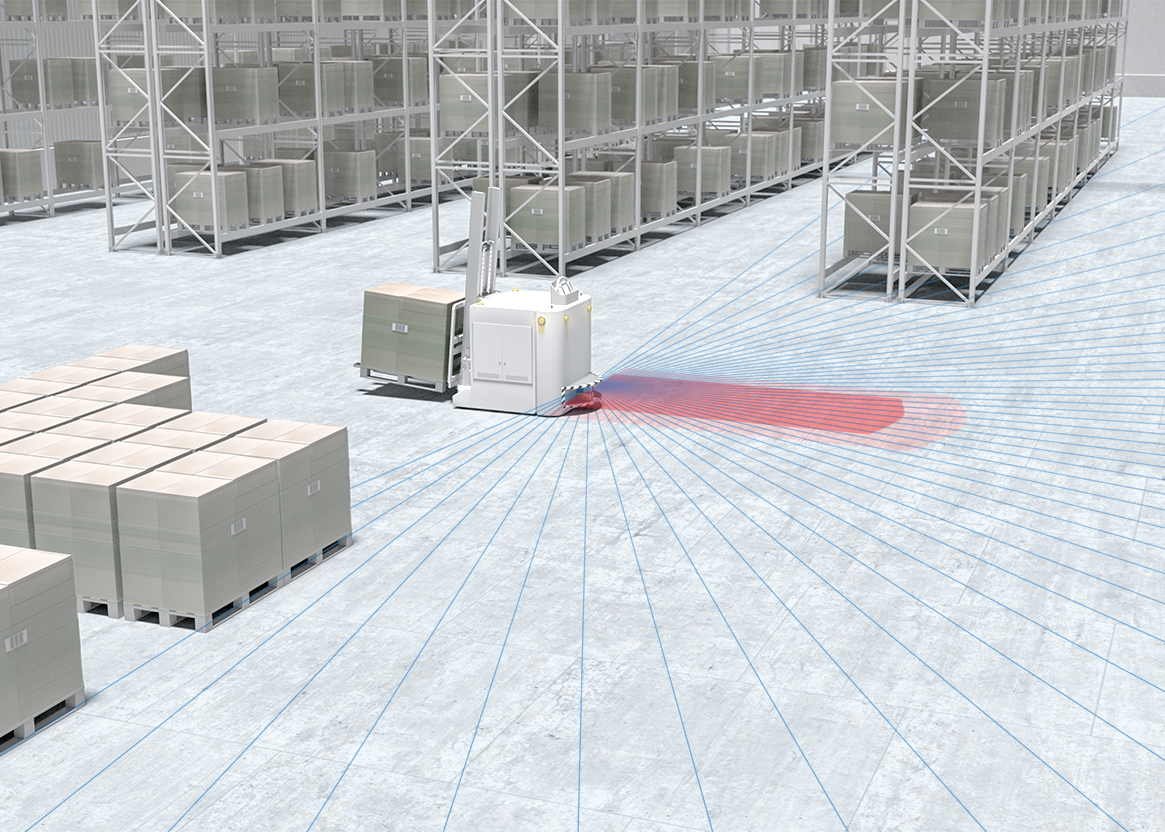
Requisito:
Si se usa el principio de la navegación natural, el sensor de seguridad debe, además de proteger el recorrido en diferentes situaciones de conducción, proporcionar simultáneamente los datos de medición para el software de navegación.
Solución:
El escáner láser de seguridad RSL 400 reúne en un equipo el sistema de seguridad y la emisión de valores medidos de alta calidad. Dispone de hasta 100 pares de campos conmutables. Los datos de medición tienen una alta resolución angular de 0,1°, lo que permite crear un mapa muy preciso del entorno.
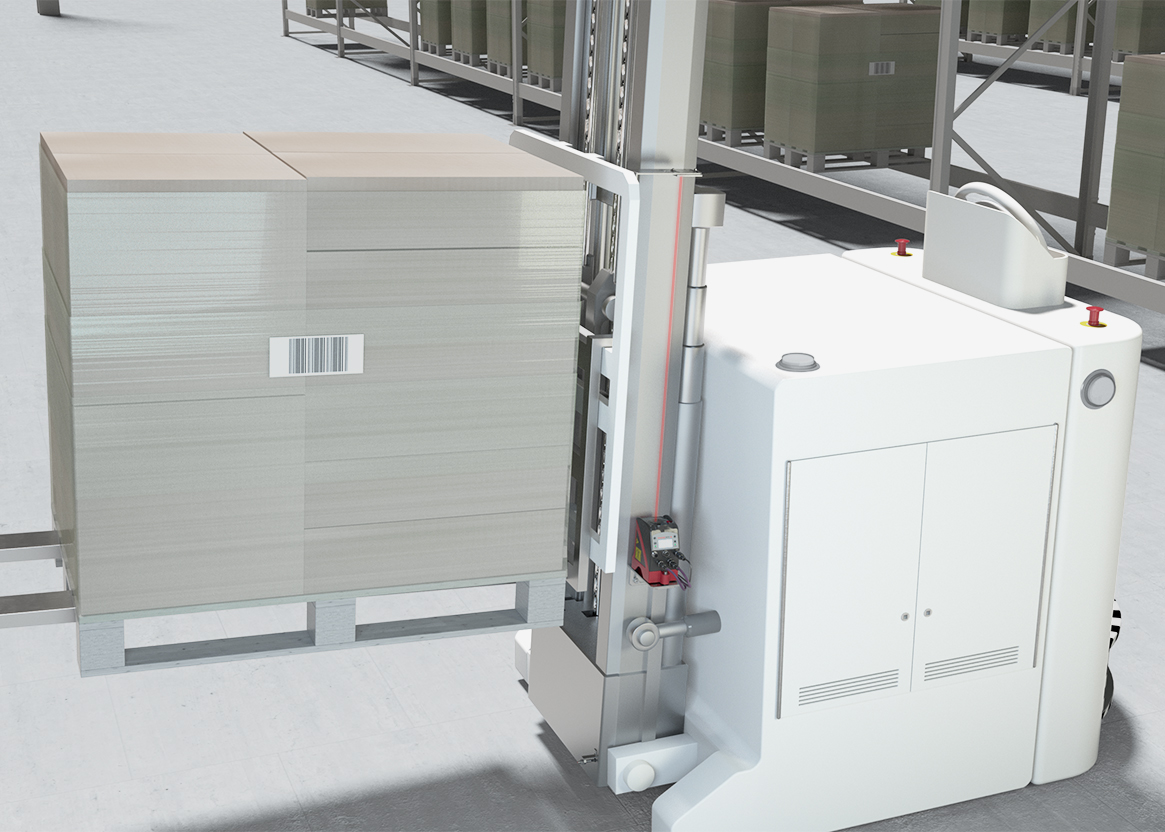
Requisito:
Para extraer y almacenar palets de forma fiable, el manipulador de cargas debe posicionarse a la altura correcta con precisión y repetibilidad.
Solución:
El sistema de posicionamiento láser AMS 300i proporciona datos de medición cada 2 ms con una exactitud absoluta de ± 2 mm. Los datos se pueden transferir al control a través de una gran variedad de interfaces.
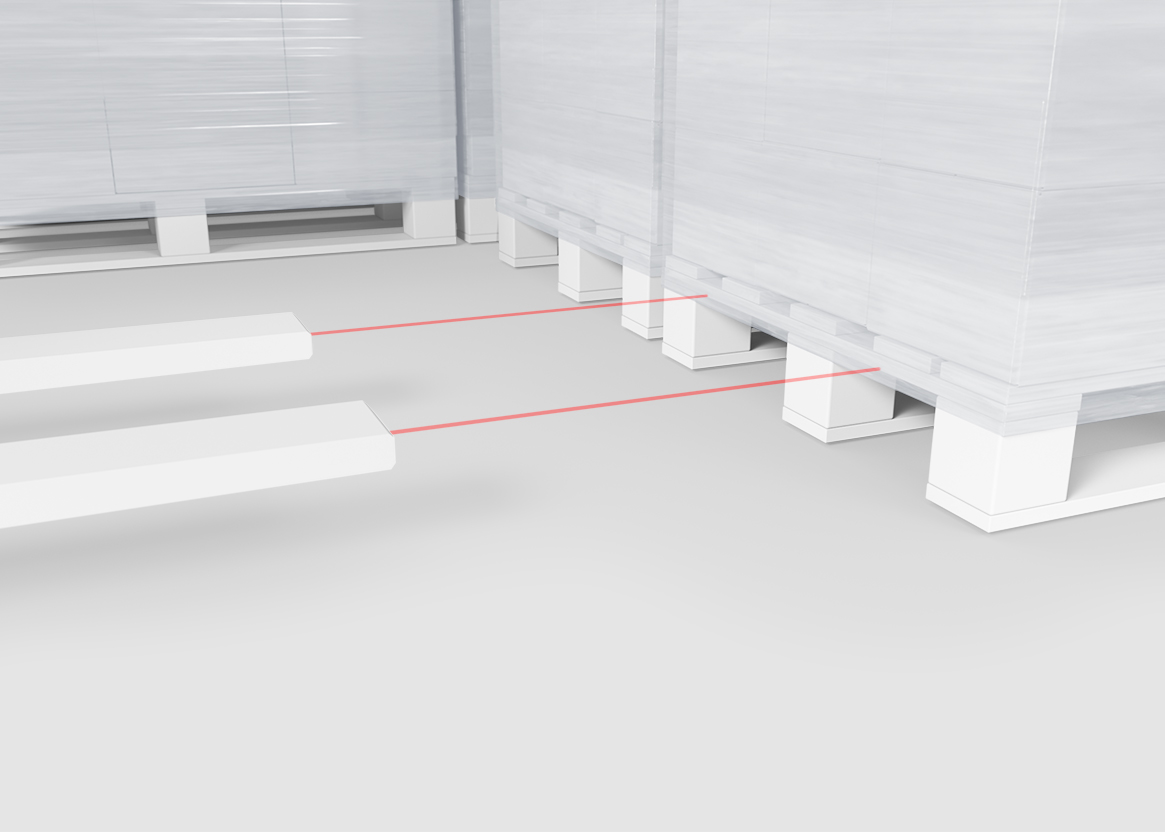
Requisito:
Para detectar el palet con el manipulador de cargas, es necesario reconocer dónde se encuentran los espacios entre las patas del palet y si se puede acceder a ellas.
Solución:
Las fotocélulas autorreflexivas de la serie HT 3C funcionan independientemente del material y tienen puntos de conmutación precisos. Gracias a las dos salidas digitales, los mismos sensores pueden usarse también para el ajuste fino en las ubicaciones.
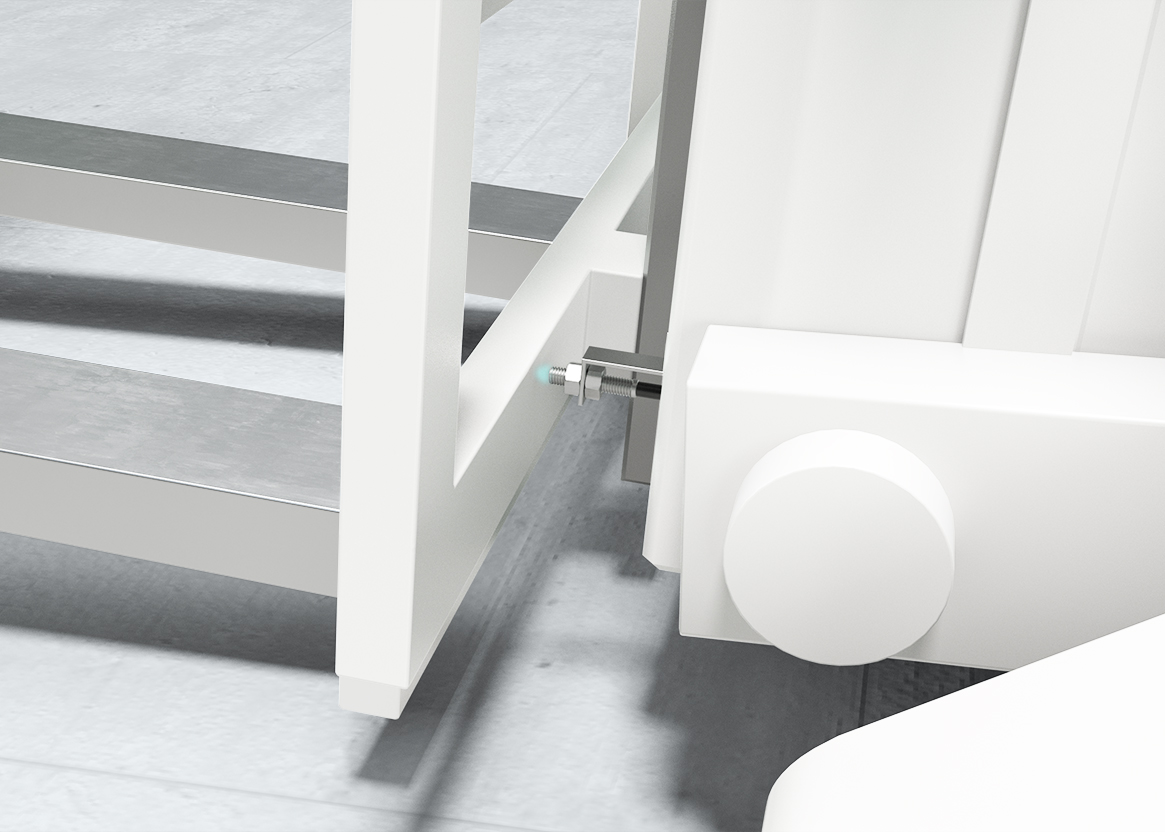
Requisito:
Antes de poder activar ciertas funciones del vehículo como, por ejemplo, pasar de la marcha lenta a la velocidad normal, hay que asegurarse de que el manipulador de cargas está en la posición final.
Solución:
Los sensores inductivos de la serie IS 212 detectan objetos de metal con una distancia de trabajo máxima de 10 mm. Los equipos están bien protegidos contra las influencias ambientales y los procesos de limpieza gracias a la robusta carcasa de metal.
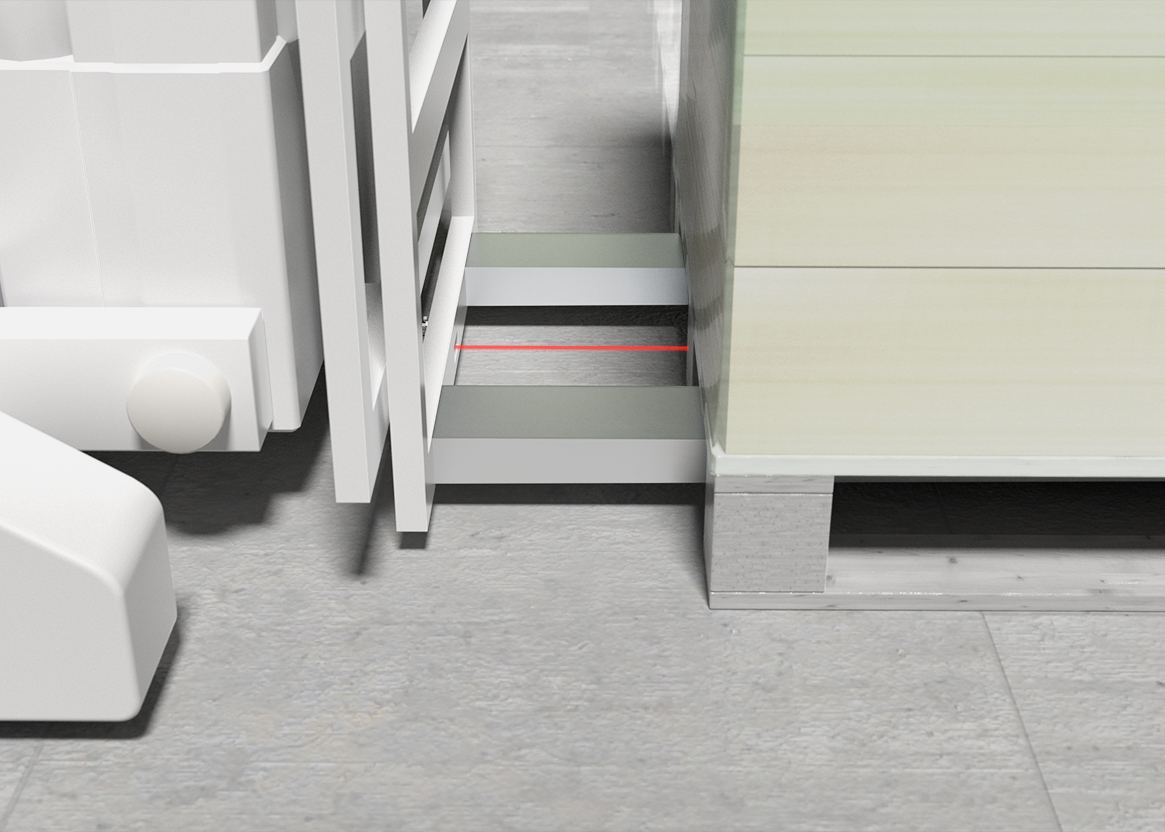
Requisito:
Al recoger el palet, se debe determinar la distancia del palet respecto a la superficie frontal del manipulador de cargas para detener el movimiento de avance a tiempo.
Solución:
Con su gran punto de luz, los sensores de distancia de la serie HRT 25B LR determinan la distancia respecto a objetos con una gran variedad de colores y superficies de forma fiable y con una exactitud repetible. Gracias a la tecnología TOF (tiempo de propagación, time-of-flight), los equipos también disponen de un gran alcance de 2.500 mm y una tolerancia angular elevada.
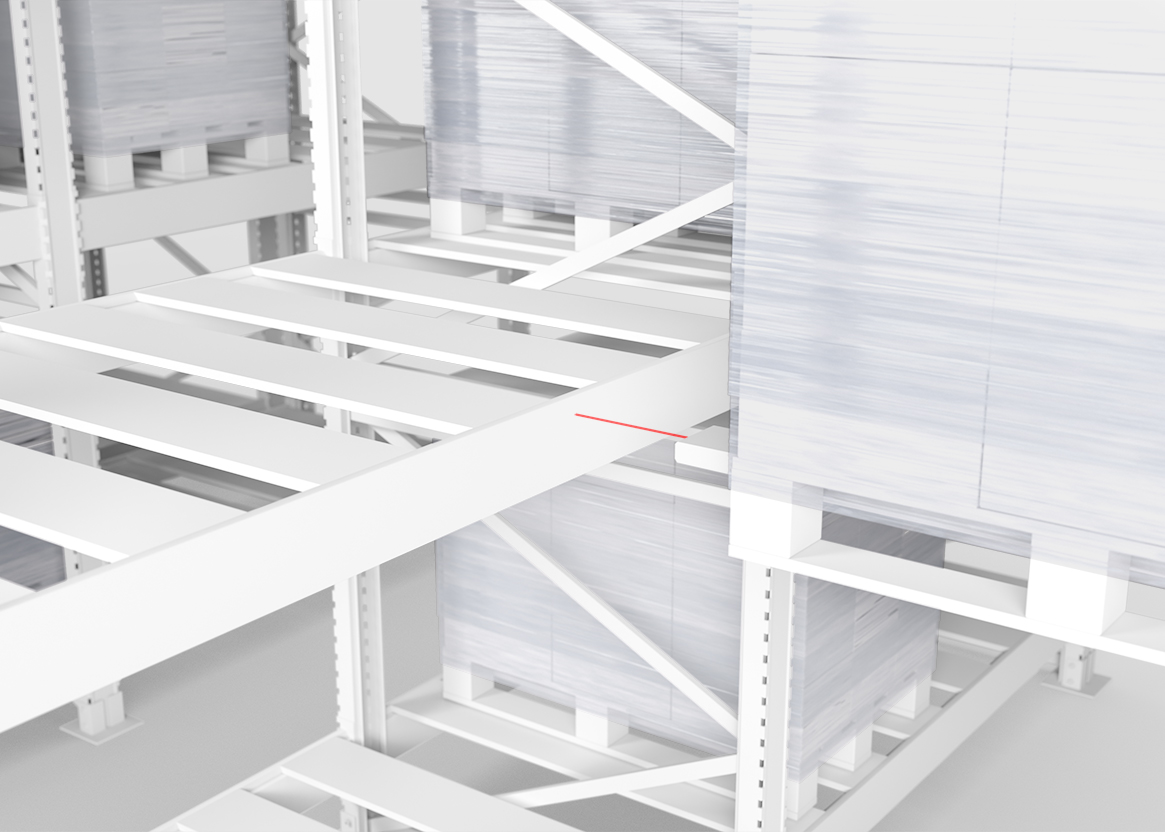
Requisito:
Para poder colocar el palet de forma segura en el almacén, se debe detectar de forma fiable la arista de la estantería en la que se va a colocar el palet.
Solución:
Las fotocélulas autorreflexivas de la serie HT 3C funcionan independientemente del material y tienen puntos de conmutación precisos. Gracias a las dos salidas digitales, los mismos sensores pueden usarse también para el posicionamiento del manipulador de cargas.
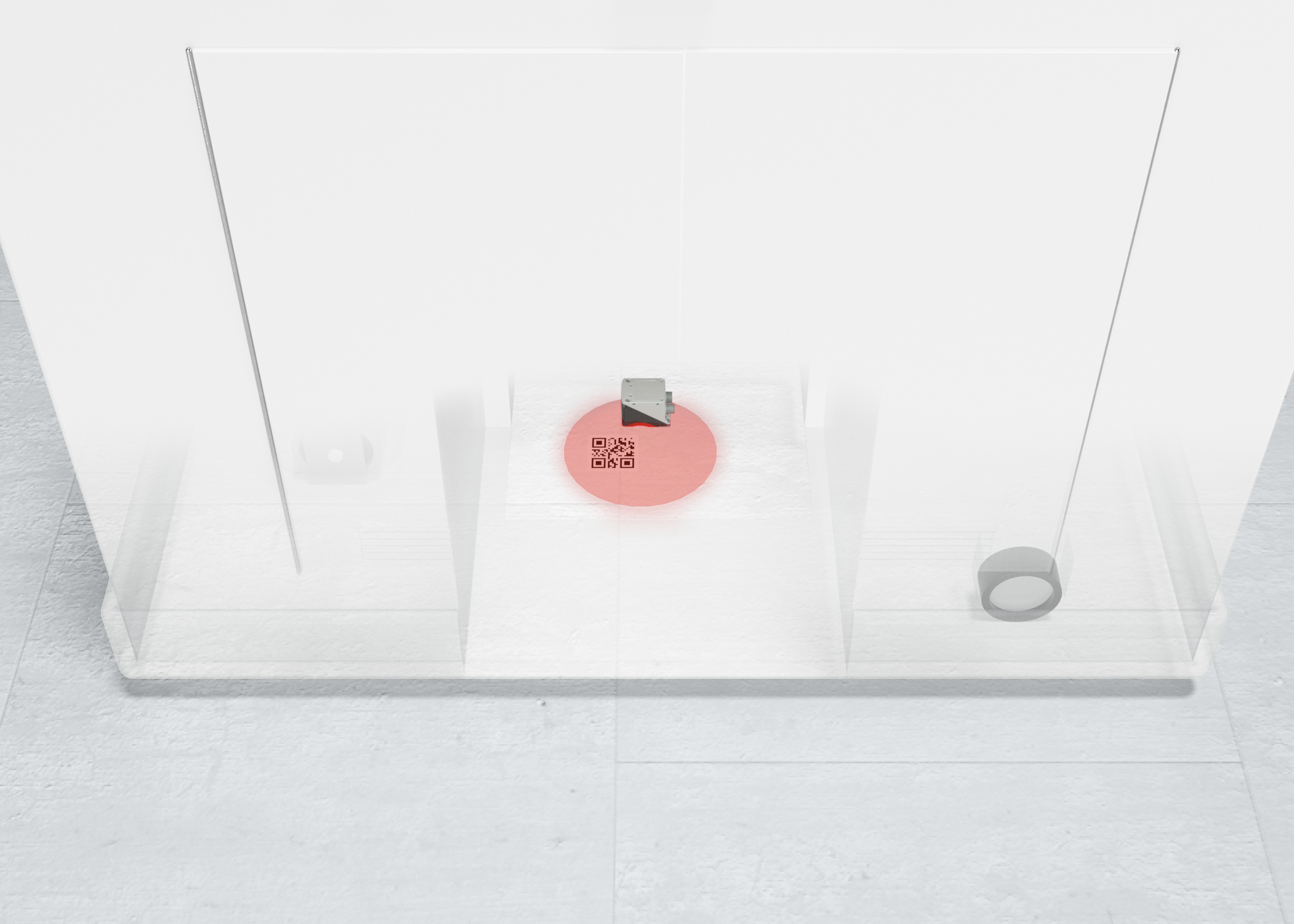
Requisito:
Las etiquetas con códigos 2D se colocan en el suelo en un raster fijo. Mediante la lectura del código y la determinación de la posición angular del código en relación con el sensor, se debe corregir la dirección del movimiento del AGV para poder acercarse al siguiente código 2D.
Solución:
El lector de códigos 2D DCR 200i lee los códigos a medida que el AGV pasa por encima. La amplia zona de trabajo de 40 - 360 mm permite una instalación flexible en el AGV y garantiza un funcionamiento estable. El asistente de configuración integrado hace que la puesta en marcha sea rápida y sencilla.
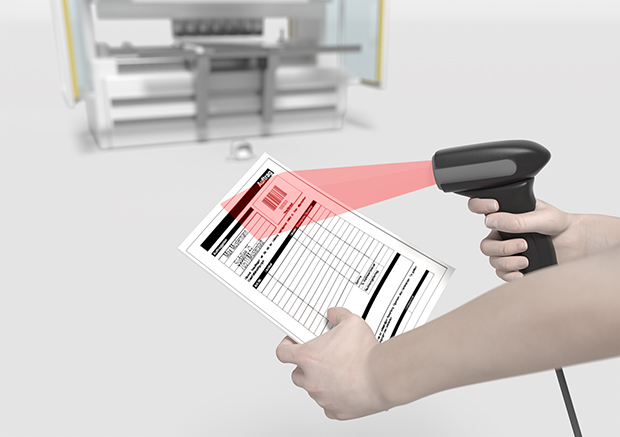
Requisito:
Para un movimiento rápido y eficiente, los AGV deben seguir una trayectoria determinada marcada por una pista colocada en el suelo. Para su uso en vehículos planos, el sensor utilizado solo debería requerir una altura de instalación baja.
Solución:
El sensor de seguimiento óptico OGS 600 detecta la pista mediante la detección de aristas y envía las señales correspondientes al control. Los equipos funcionan de forma especialmente fiable en combinación con nuestras cintas de pista OTB optimizadas. Puesto que la distancia mínima desde el suelo es de solo 10 mm, el OGS 600 se puede integrar en el AGV ahorrando espacio.
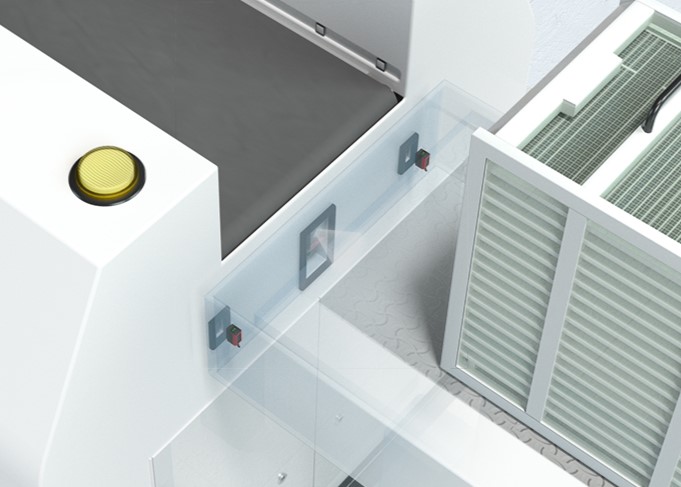
Requisito:
La estación de transferencia debe activar sin contacto la cinta transportadora del AGV en la dirección de movimiento requerida.
Solución:
Las económicas fotocélulas de barrera de la serie 5 transmiten la información de conmutación al AGV. Los equipos son insensibles frente a la luz ambiental y se pueden alinear fácilmente gracias a la luz roja visible.
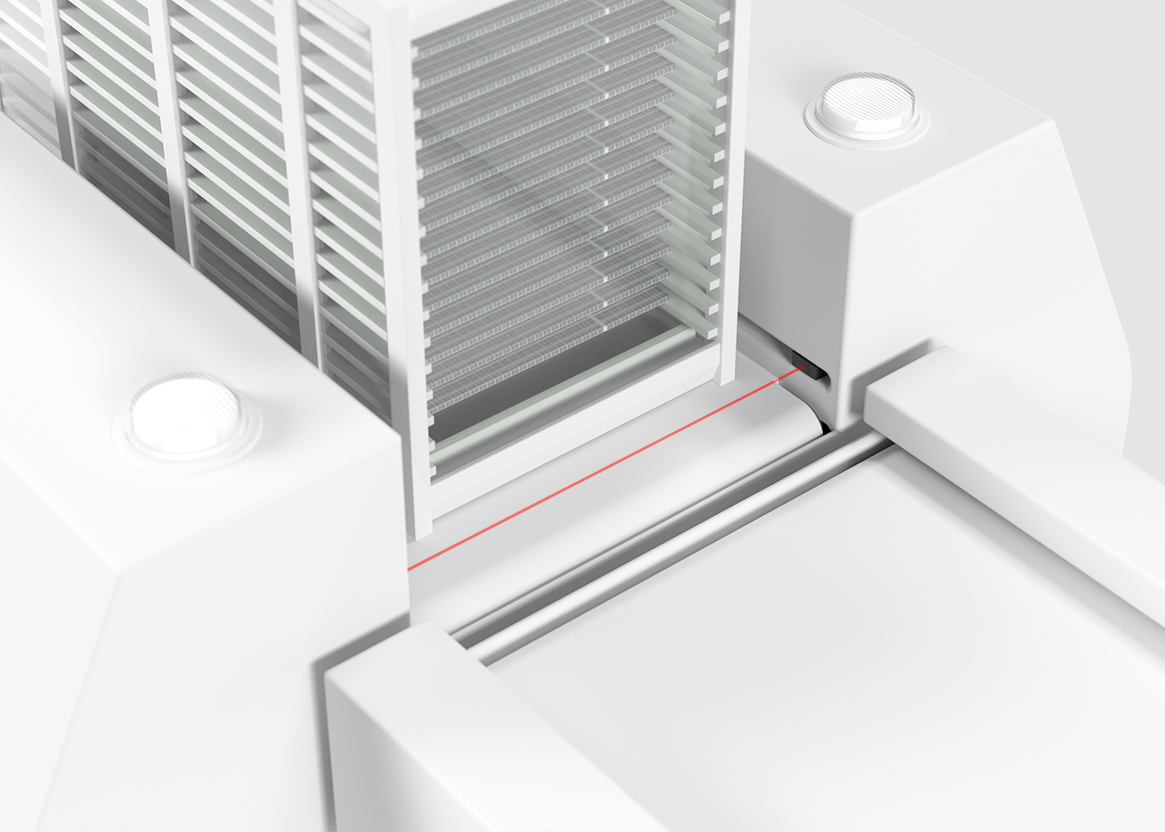
Requisito:
Se debe comprobar si la mercancía transportada se ha transferido íntegra al AGV y sin salientes.
Solución:
Las fotocélulas reflexivas económicas de la serie 5 pueden integrarse fácilmente gracias a su diseño compacto. Mediante la supresión activa de luz ambiental, los equipos funcionan de forma especialmente fiable.
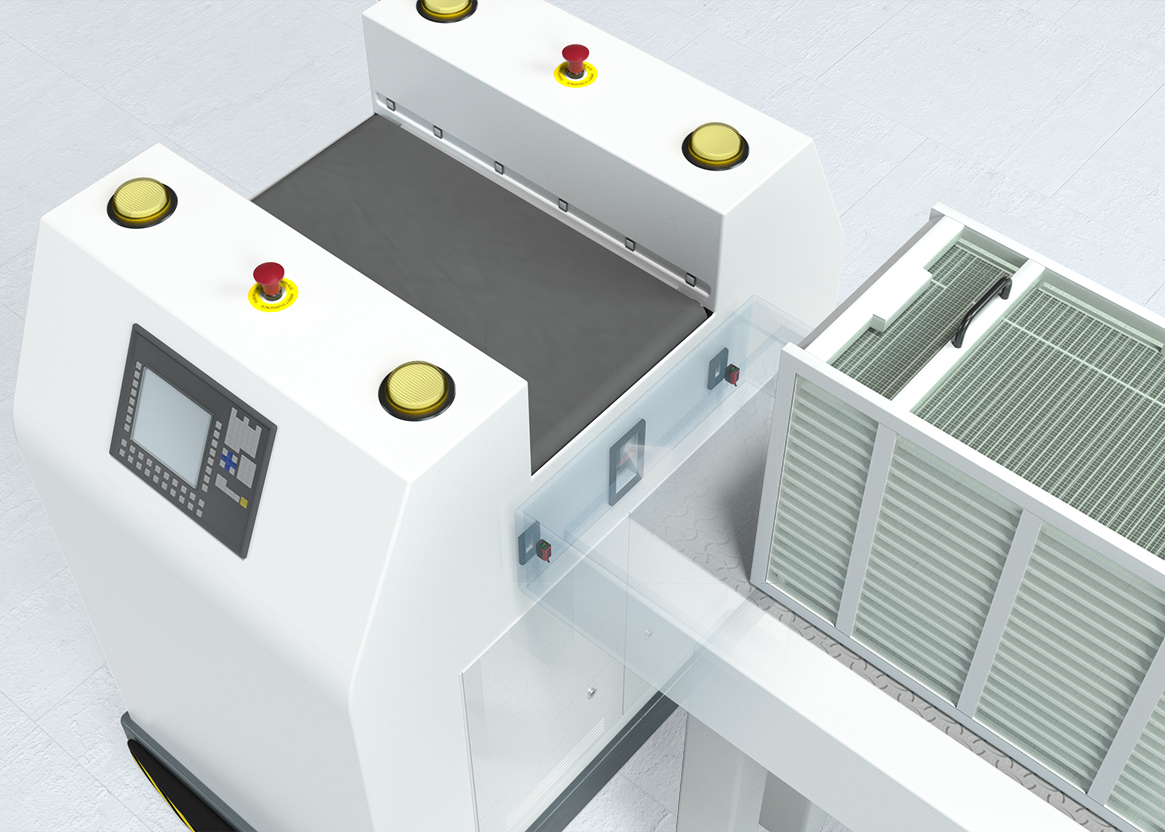
Requisito:
En la estación de transferencia, las mercancías transportadas se deben transferir sin vibraciones. Para ello, el AGV o el manipulador de cargas se deben posicionar con precisión milimétrica.
Solución:
La Smart Cámara IPS 200i determina su posición en relación con una referencia (agujero o reflector) con una exactitud de hasta 0,1 mm. La distancia puede ser de hasta 600 mm. Los resultados se emiten a través de una interfaz Ethernet TCP/IP, PROFINET o EtherNet /IP.