Más de lo que espera.
Packaging. Sensores. Soluciones.
Las exigencias a los fabricantes de máquinas de embalaje y de bienes de consumo son muy altas y cambiantes: los consumidores desean materiales de embalaje innovadores y sostenibles, la protección de la marca y los consumidores es cada vez más importante y el comercio electrónico es la tendencia determinante en el comercio minorista. Los procesos de embalaje en la industria alimentaria y farmacéutica deben ser cada vez más flexibles, eficientes e inteligentes.
Nuestra amplia gama de productos abarca sensores para todo el proceso de embalaje, siempre adaptados a sus requisitos específicos. Mientras que en los procesos de fabricación de queso y embutidos o de la industria farmacéutica los requisitos de higiene son muy altos, en la industria de bebidas también son de gran importancia la velocidad y la rentabilidad. En el embalaje de productos de confitería, la flexibilidad y la facilidad en el cambio de formato son cruciales. Desde hace más de 60 años desarrollamos junto con nuestros clientes la solución perfecta para cada aplicación. Ya se trate de sensores estándar individuales, sensores especiales o soluciones completas. Nuestro objetivo es lograr la máxima disponibilidad de su instalación y la máxima fiabilidad, seguridad y trazabilidad de sus procesos de producción.
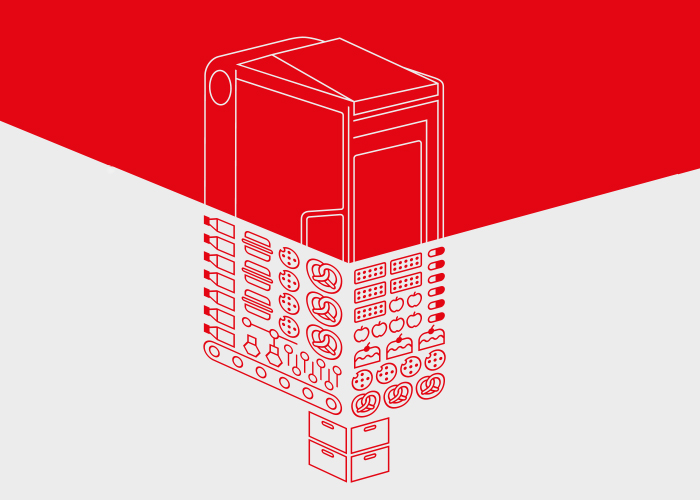
Nuestros productos destacados para los procesos de embalaje en la industria farmacéutica y alimentaria
Sensores Simple Vision: IVS 108 y IVS 1048i / DCR 1048i
Tan fácil de usar como un sensor óptico y con un rendimiento similar al de un sistema de cámaras: así es el exclusivo concepto Simple Vision de Leuze. La nueva gama de productos ofrece un acceso rápido y sencillo al procesamiento de imágenes en la automatización industrial.
Nueva gama de sensores para procesos de producción sensibles a la higiene
Nuestra nueva plataforma de sensores de acero inoxidable con las series 53C en diseño Hygiene y 55C en diseño Wash-Down ha sido especialmente diseñada para aplicaciones con requisitos de higiene elevados.
Fotocélulas reflexivas de alta velocidad para objetos muy transparentes
Los sensores de la serie PRK 18B detectan preformas y botellas de PET o vidrio de manera muy rápida y fiable. Una función especial de seguimiento (tracking) compensa la suciedad y prolonga los intervalos de limpieza.
Las fotocélulas de barrera más potentes para la radiación a través de láminas
Las barreras optoelectrónicas LS25CI han sido desarrolladas como resolución a la radiación a través de láminas. Son tan potentes que incluso transiluminan láminas de embalaje metalizadas de manera fiable.
Sensores de referencia dinámicos para la detección independiente de los objetos
El sensor de referencia dinámico DRT 25C está dotado con una tecnología inteligente "Contrast Adaptive Teach" (tecnología CAT) y es un especialista para la detección de formas o superficies difíciles, sin necesidad de realizar ajustes en el sensor al cambiar de formato.
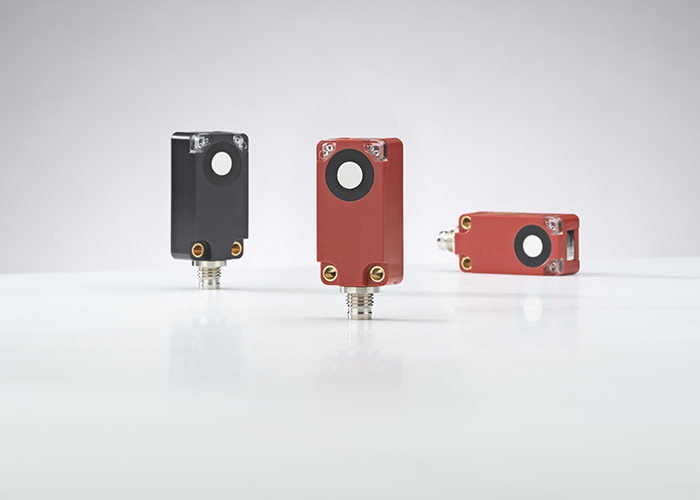
Flexibles y precisos: sensores de ultrasonidos con cono acústico ajustable
Nuevos sensores de ultrasonidos cúbicos con zona ciega pequeña y tres anchos de cono acústico ajustables para resultados de medición y conmutación precisos.
Su tarea: nuestras soluciones
Los requisitos del procesamiento y envasado de alimentos y fármacos son elevados. Prestamos apoyo a los fabricantes de máquinas de embalaje y a los productores de bienes de consumo con sensores y asesoramiento de aplicaciones.
Detección de objetos transparentes
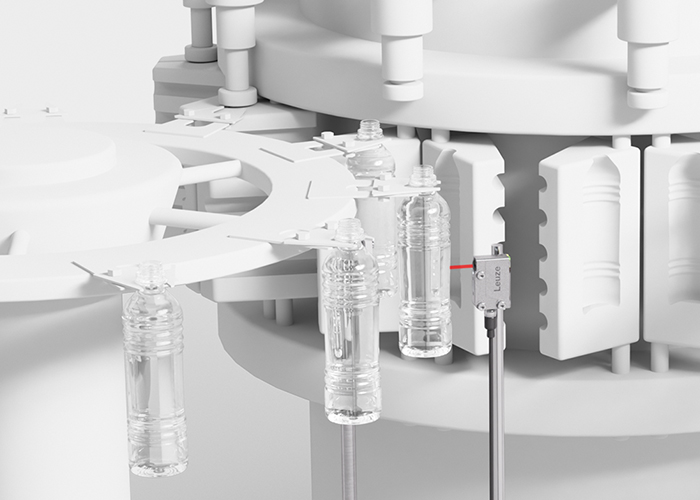
La detección de objetos transparentes suele presentar retos a los sensores. Ofrecemos sensores específicamente diseñados para la detección de preformas, botellas y láminas.
Radiación a través de láminas
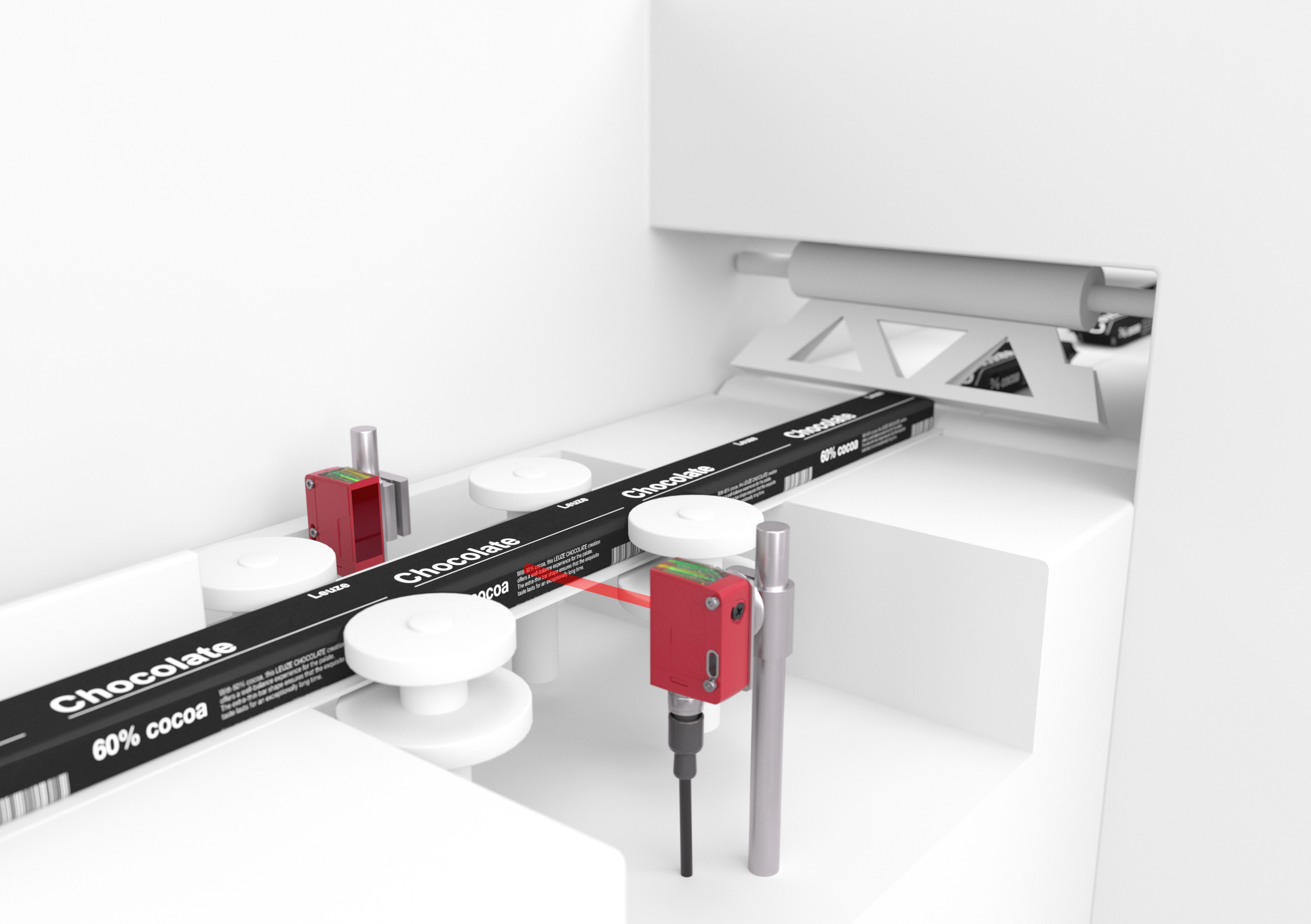
Para el sellado de las láminas y la separación de los productos se debe detectar su posición en la lámina. Las fotocélulas de barrera más potentes detectan el contenido del embalaje a través de la lámina.
Detección de marcas de contraste y de corte
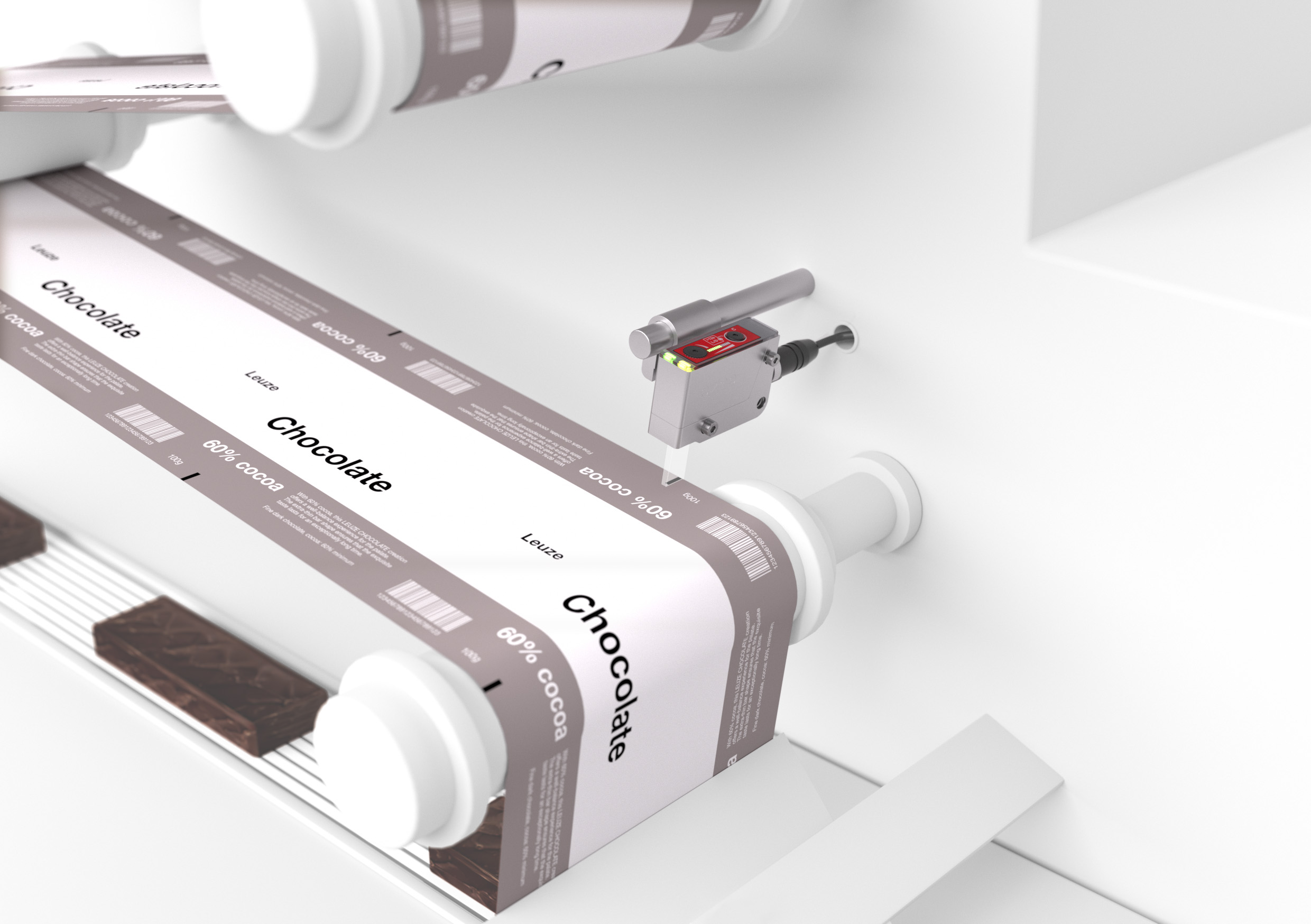
Los sensores de contraste han sido desarrollados para detectar marcas definidas en objetos en los procesos de embalaje. Estas marcas de contraste se encuentran encima de láminas, bolsas y blísters o incluso etiquetas.
Detección independiente del objeto (DRT)
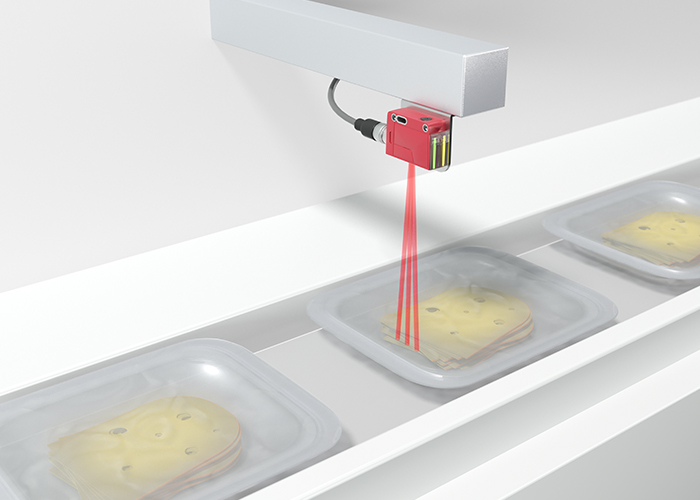
En las cintas transportadoras de las máquinas de embalaje, los sensores deben detectar una gran variedad de productos y láminas. Nuestros sensores de referencia dinámicos detectan incluso objetos con formas y superficie complicadas utilizando la cinta transportadora como referencia.
Determinación del nivel de llenado
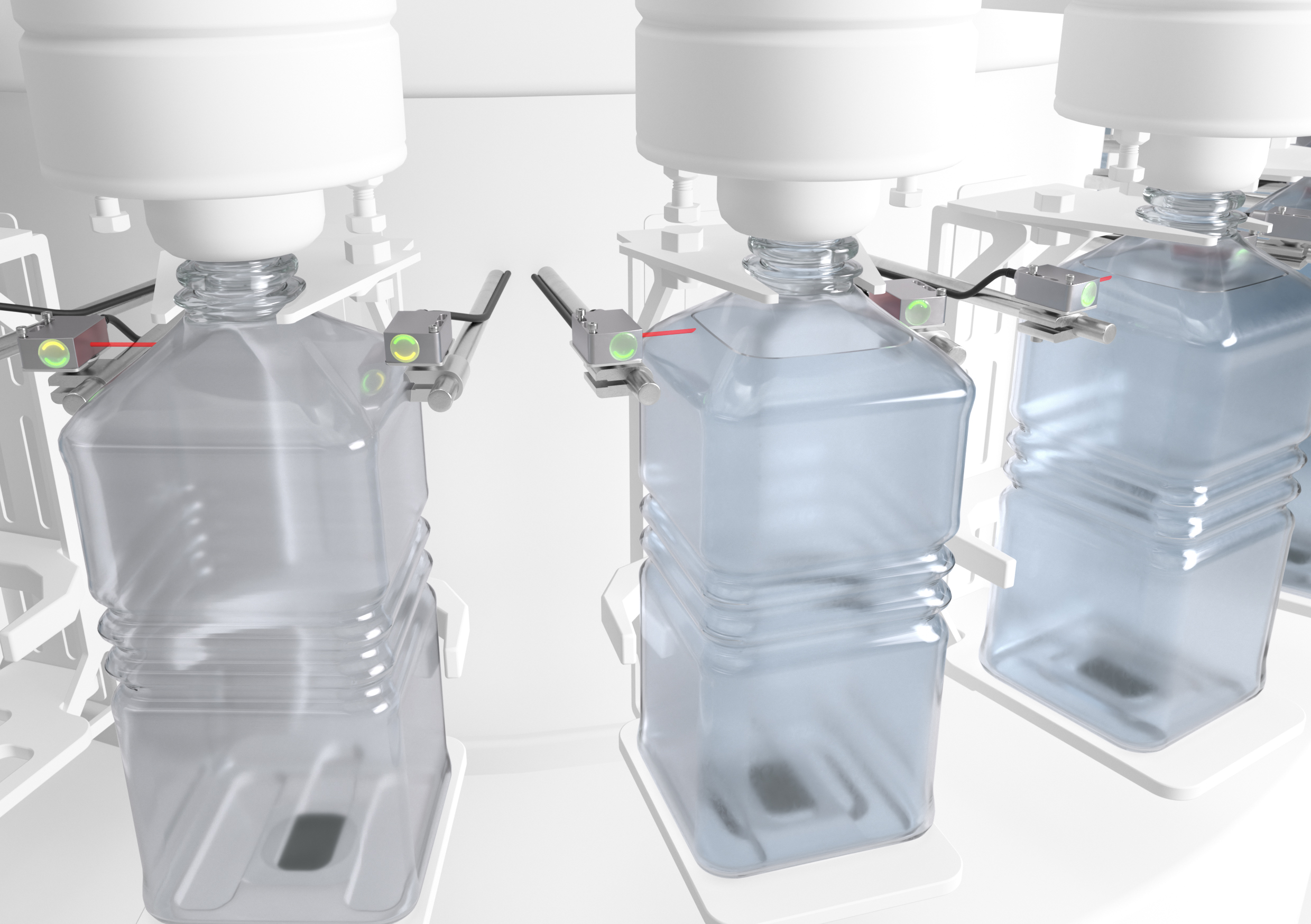
La detección fiable del nivel de líquidos acuosos en cualquier recipiente es una de las tareas de detección más exigentes para los sensores y exige soluciones de sensores especialmente potentes.
Etiquetado
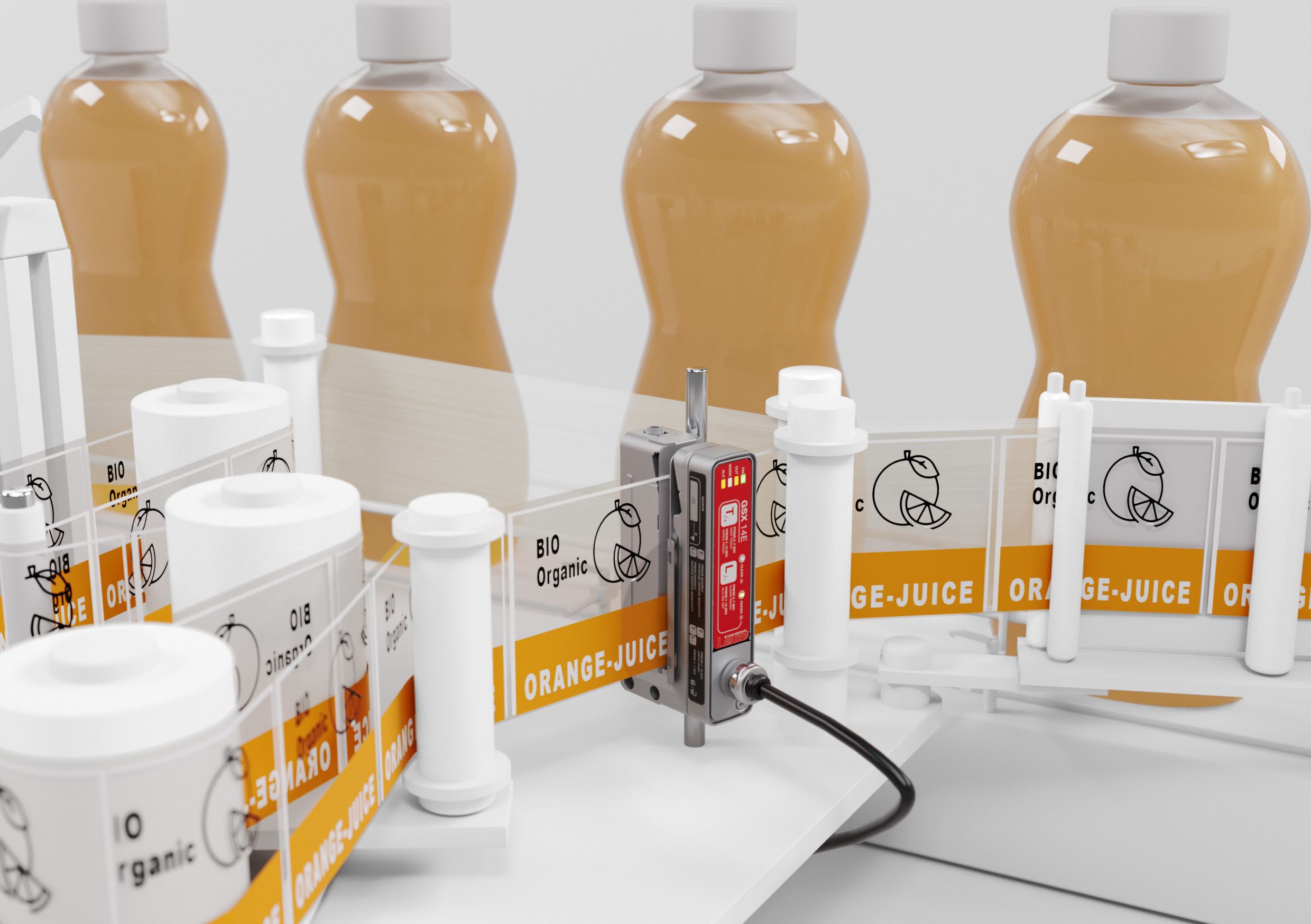
Se colocan en productos y embalajes etiquetas de diferentes formas y tamaños, así como de diferentes materiales y con distintas características, con la ayuda de las etiquetadoras. Sensores de horquilla reconocen las etiquetas con fiabilidad y aseguran la calidad con la que se coloca la etiqueta.
Detección, inspección e identificación
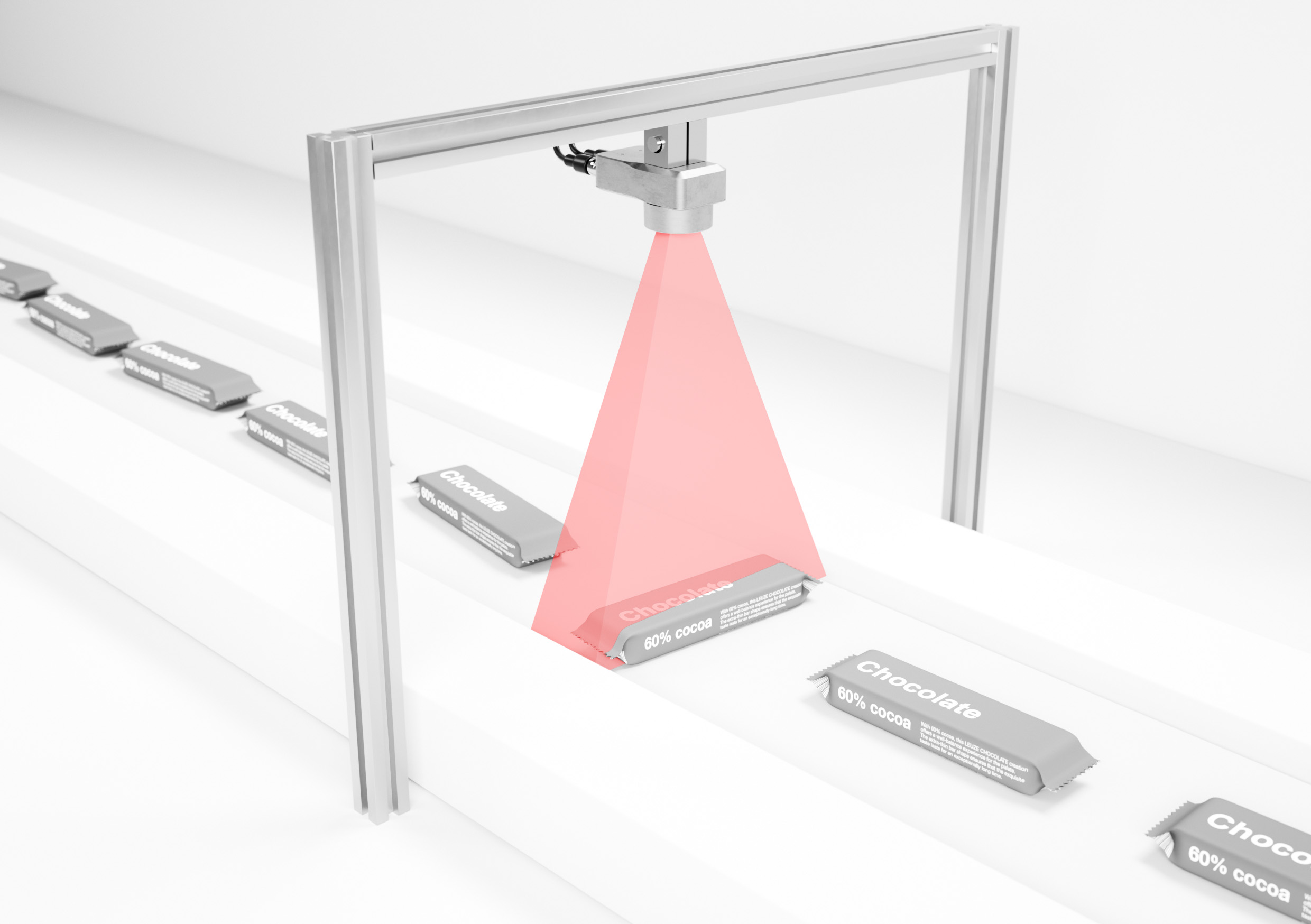
La detección de presencia o ausencia, la detección de piezas, la inspección, la medición y el contaje son tareas que se pueden resolver con la gama de productos Simple Vision, que ofrece un acceso sencillo al procesamiento de imágenes.
Los escáneres 1D/2D basados en cámara leen códigos incluso en movimiento y tienen un amplio ámbito de aplicación.
Supervisión visual
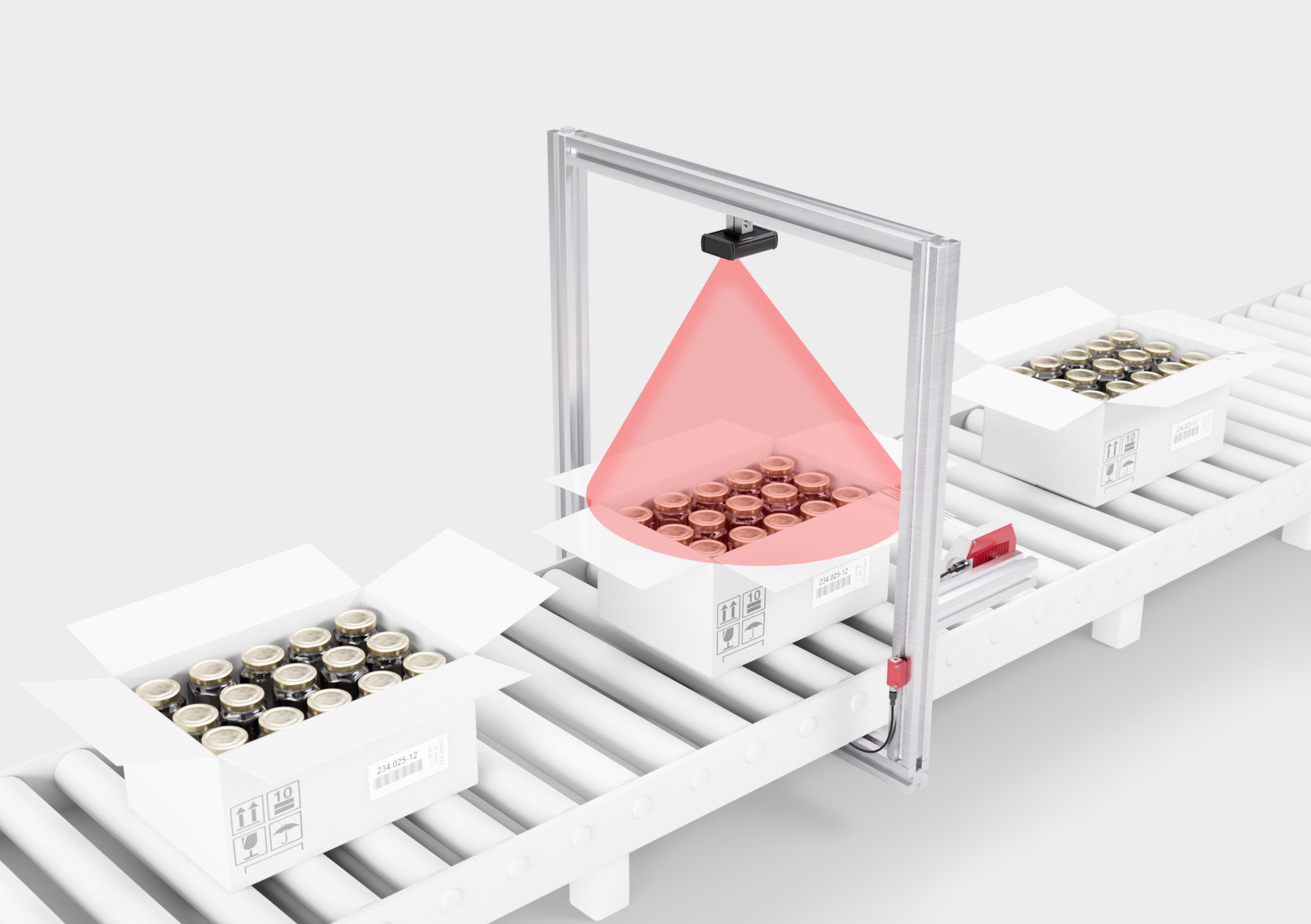
Las soluciones para el procesamiento de imágenes industrial permiten "ver" las máquinas, de modo que las tareas de inspección manual pueden sustituirse o complementarse con el uso de cámaras digitales y funciones de procesamiento de imágenes digitales.
Protección de la máquina
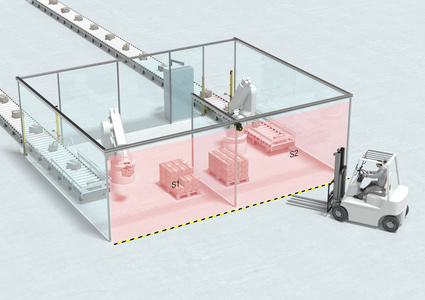
Con un porfolio integral para todos los requisitos de seguridad, le ofrecemos seguridad completa, un flujo de materiales eficiente y la máxima disponibilidad en todo el mundo.
Ámbitos de aplicación
Entrevista: aumento de la eficiencia en el sector del envase y embalaje
Nuestro experto de envase y embalaje Andreas Eberle está a su disposición
Tel.: 07021 / 573 177
E-mail: Andreas.Eberle@leuze.com