배터리 셀 생산
배터리 셀은 '기가팩토리'라고 불리는 곳에서 제조됩니다. 개별 기계부터 네트워크화된 생산 시스템에 이르는 생산 단계는 효율적인 프로세스를 갖추도록 최적화되어 있습니다. 이때 공정 안정성과 생산 제품의 품질은 까다로운 기준을 맞춰야 합니다. 따라서, 사용된 센서는 배터리 셀의 추적, 생산 물류, 기계의 안전성과 신뢰성에 의해 결정되는 특정 요구 사항을 충족해야 합니다.
센서 솔루션은 원활한 프로세스와 기계 안전을 보장합니다. 일반적인 어플리케이션은 추적 가능성을 위한 코드 판독, 자동화를 위한 물체 감지, 기계 및 시스템에서의 출입을 보호입니다.
어플리케이션 보고서: e-drive를 위한 정밀한 프로세스
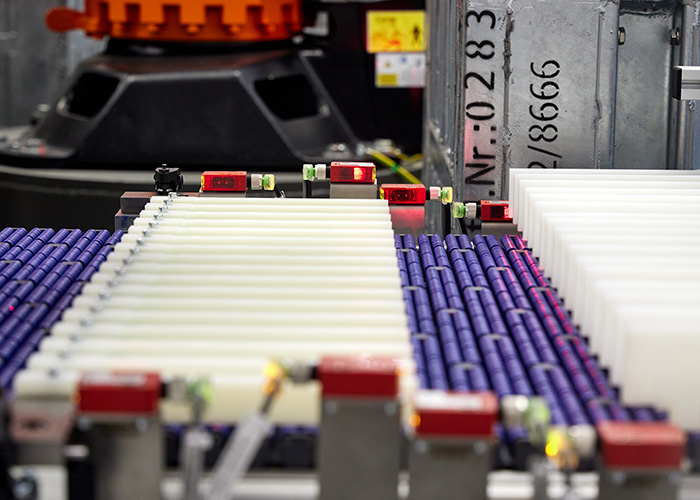
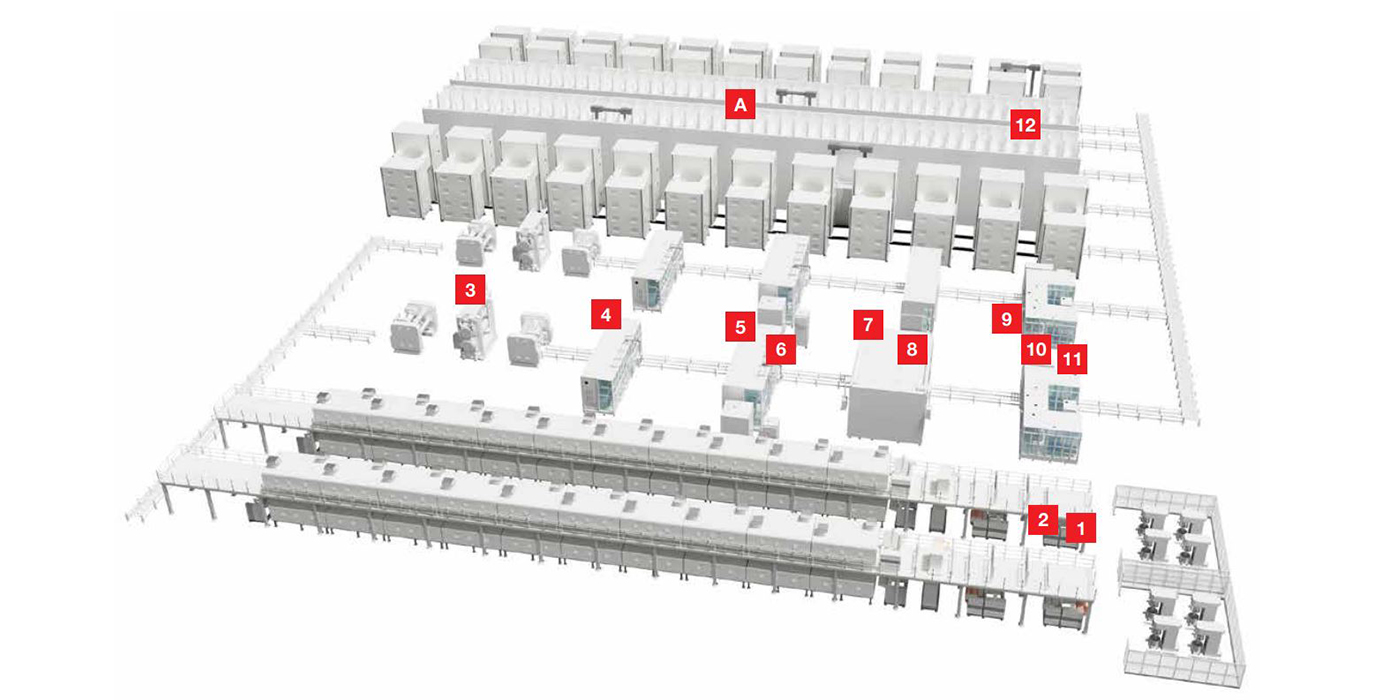
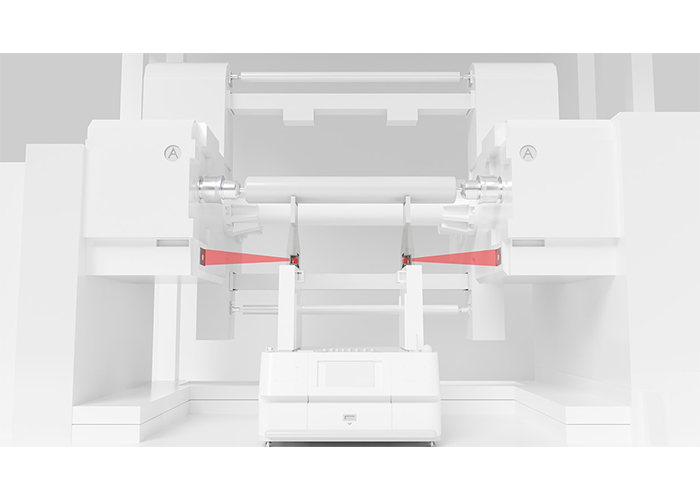
요구 사항:
AGV는 롤을 이송 스테이션으로 운반합니다. 코팅 시스템에 의해 끌어당겨집니다. 안정적으로 이송하려면 AGV의 리프팅 장치를 Y 방향(리프팅 축)으로 정확히 배치해야 합니다.
솔루션:
IPS 200i스마트 카메라는 최대 0.1mm의 정확도로 마커(구멍 또는 반사판)와 관련된 위치를 측정합니다. 최대 거리 600mm까지 감지 가능 Ethernet TCP/IP, PROFINET 또는 EtherNet/IP 인터페이스를 통해 결과가 출력됩니다.
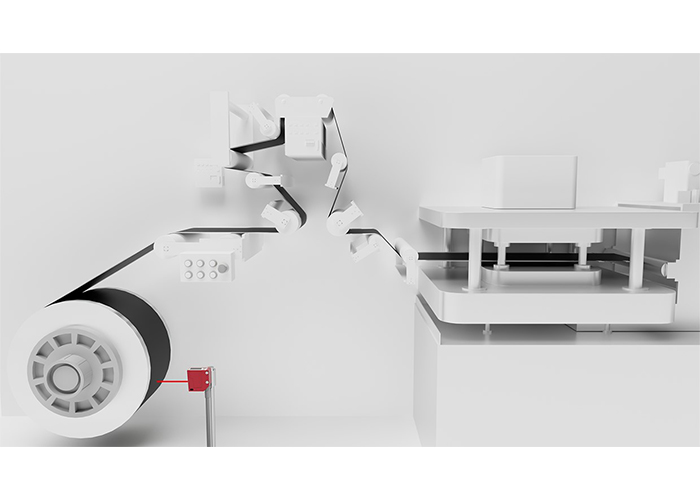
요구 사항:
필름을 감고 푸는 동안 롤러의 직경이 지속적으로 측정되어야 합니다.
솔루션:
광학 거리 센서 ODS 9는 어려운 조건에서도 정확한 측정값을 제공하고 정밀도와 조작 편의성에 대한 표준을 설정합니다. 측정 가치는 통합 디스플레이에서도 확인할 수 있습니다.
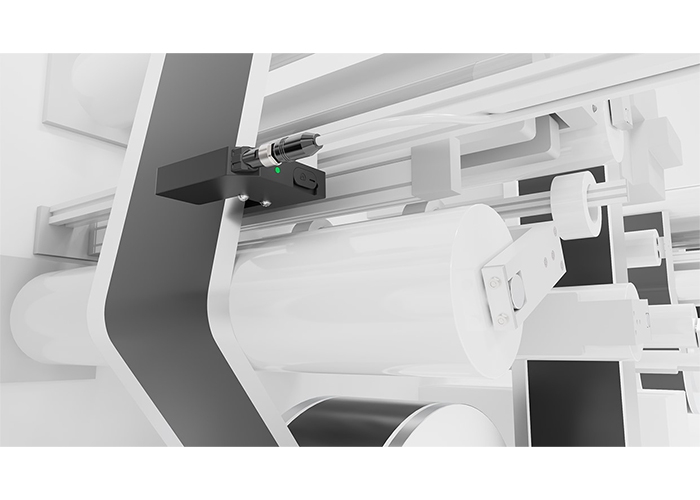
요구 사항:
배터리 셀 생산에 필요한 다양한 프로세스 단계에서는 전극 필름의 위치를 정확히 설정해야 합니다. 와인딩 및 절단 공정에 투입할 때, 필름 가장자리의 위치를 정확하게 감지해야 합니다.
솔루션:
측정식 CCD 포크형 광전 감지기 GS 754B는 전극 필름의 가장자리를 최대 0.014mm의 분해능과
최소 2.5ms의 반응 시간으로 감지합니다. 이 장치는 측정값을 아날로그 형식 또는 RS 232/422 인터페이스를 통한 방식으로 제어장치에 전송합니다.
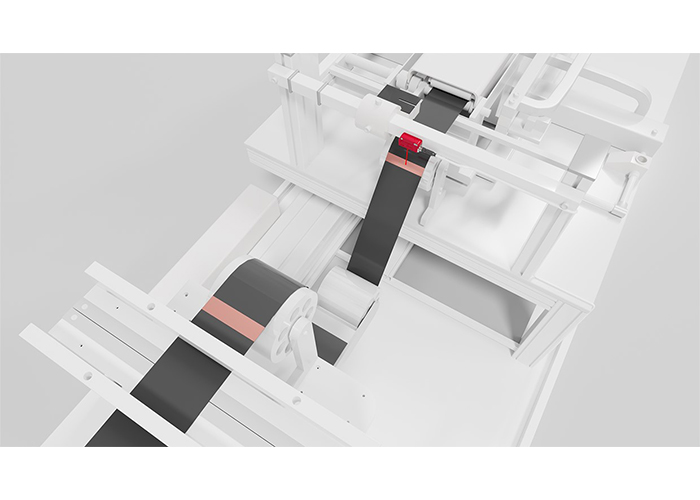
요구 사항:
전극 코팅은 주기적으로 끊어집니다. 따라서, 이 지점에서 구리 또는 알루미늄 백킹 필름이 보이게 됩니다. 코팅 중단부는 공정 제어(예: 절단 공정)를 위한 "표시" 역할을 하며, 센서가 감지해야 하는 부위입니다.
솔루션:
명암센서 KRT 3B는 구리/알루미늄 필름과 전극 코팅을 안정적으로 구분하여 표시부를 감지합니다. 제어장치로 원버튼 티치 기능을 활성화할 수도 있습니다. 60mm ± 20mm의 넓은 작동 범위 덕분에 센서를 기계에 유연하게 통합할 수 있습니다.
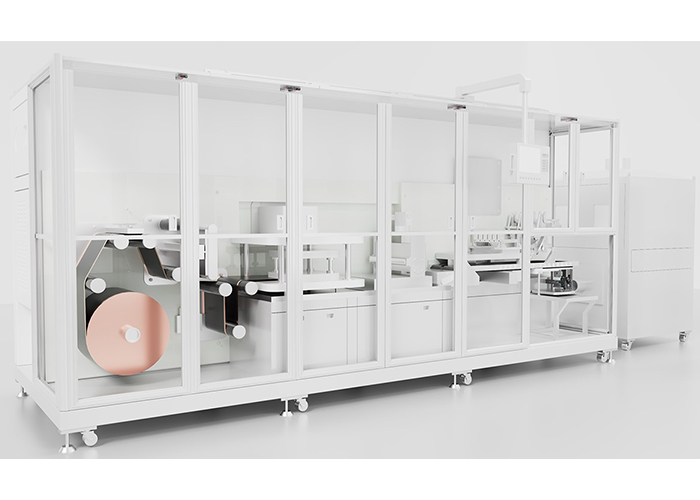
요구 사항:
위험한 움직임이 있는 영역을 유지 보수 목적으로 출입하는 경우, 안전 도어를 통해 들어갈 수 있습니다. 도어를 여는 즉시 동작이 멈추지 않으면 잠금장치가 있는 안전 스위치를 통해 도어를 보호해야 합니다.
솔루션:
잠금 장치를 가진 견고한 L 시리즈 안전 스위치는 전기 신호에 의해 접근이 해제될 때까지 안전 도어를
안전하게 잠긴 상태로 유지합니다. 이 시리즈는 기본형 설계와 최고 수준의 조작 방지 기능을 위한 RFID 코딩 액추에이터 장착형 장치를 포함합니다.
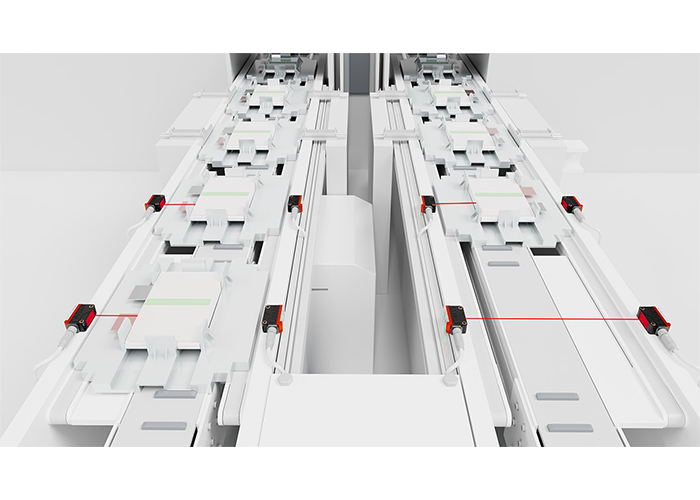
요구 사항:
다음 가공 단계로 넘어가기 전에 운반 캐리어의 배터리 셀의 유무와 위치가 확인되어야 합니다. 콤팩트한 시스템 구조를 위해 센서가 많은 공간을 차지하지 않아야 합니다.
솔루션:
5B 시리즈의 광센서는 매우 작은 설치 공간만 필요합니다. 최적화된 빔 현상 덕분에 장치는 평평한 배터리 셀까지 신뢰성 있게 감지할 수 있어 기계의 높은 가용성을 보장합니다.
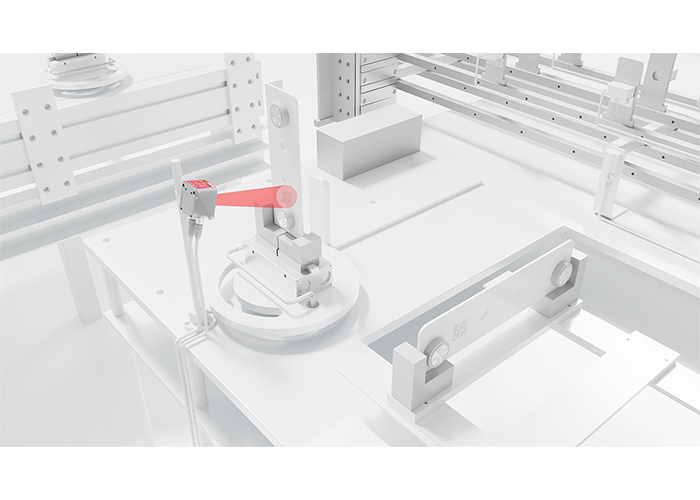
요구 사항:
'Track and Trace' 개념에는 작업 시스템에 있는 각 배터리 셀의 추적 가능성도 포함됩니다. 이 기능을 사용하려면 커버에 레이저 표시된 2D 코드(DPM 코드)를 판독해야 합니다.
솔루션:
2D 코드 리더 DCR 200i는 물체가 빠르게 움직이는 경우에도 금속 표면의 DPM 코드를 안정적으로 판독합니다. 다양한 광학 모델을 사용하여 판독 범위를 어플리케이션에 맞게 조정할 수 있습니다. 이 장치는 PROFINET IO/RT, Ethernet TCP/IP, UDP, RS 232, RS 422 인터페이스를 통해 유연하게 통합할 수 있습니다.
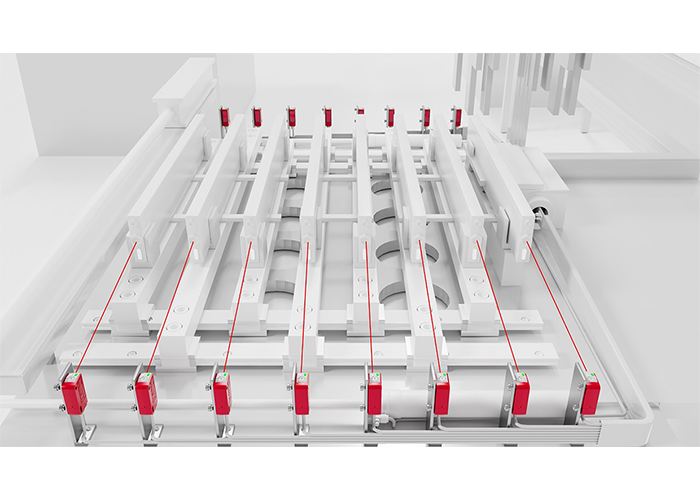
요구 사항:
충전 스테이션에서 액체를 주입하기 전에 배터리 셀이 올바른 위치에 있는지 점검해야 합니다. 이는
배터리 셀을 안정적으로 들어 올리기 위해 필요합니다.
솔루션:
3C 시리즈의 광학 센서는 좁은 공간에서도 레이저 광원으로 배터리 셀을 안정적으로 감지합니다. 또한, 이 센서는 외란광 억제 기능이 탑재되어 LED 홀 조명의 직사광선에도 민감하지 않습니다. 그 결과
스위칭 오류가 방지됩니다.
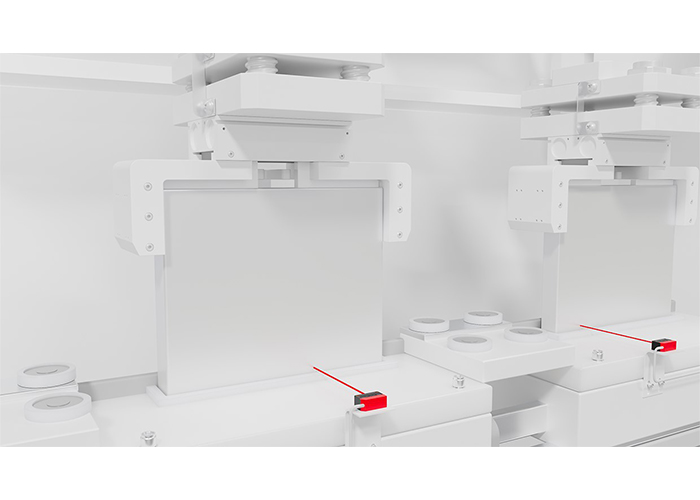
요구 사항:
충전 스테이션에서 액체를 채우기 전에 배터리 셀의 유무가 확인되어야 합니다. 센서는 셀 케이스의 반사되는 알루미늄 재질을 안정적으로 감지해야 합니다.
솔루션:
반사판 포토센서 PRK 5B는 반사 물체도 안정적으로 감지합니다. 이 장치는 균일한 광점으로 안정적인 스위칭 동작을 보장하며 정렬이 간편합니다.
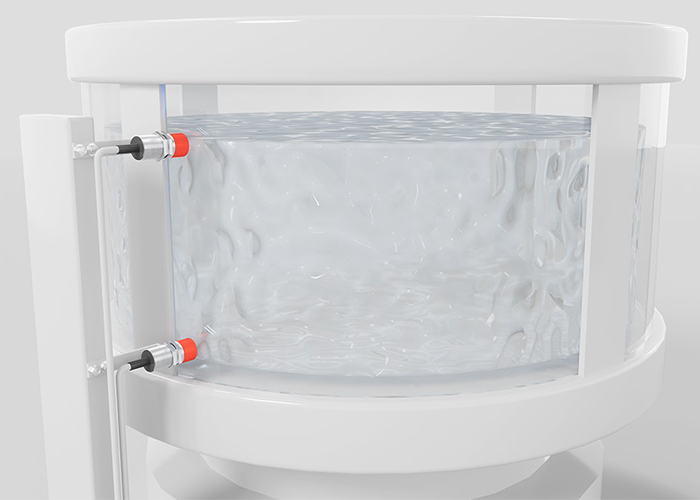
요구 사항:
용기 내 전해질 충전 레벨을 비접촉식으로 외부에서
모니터링해야 합니다.
요구 사항:
LCS-1 정전식 센서는 용기 벽 재료가 달라도 용기의 충전 수위를
감지합니다. 간편한 취급 및 통합을 위해 티치 버튼 및 IO-Link가 포함된 모델이 제공됩니다.
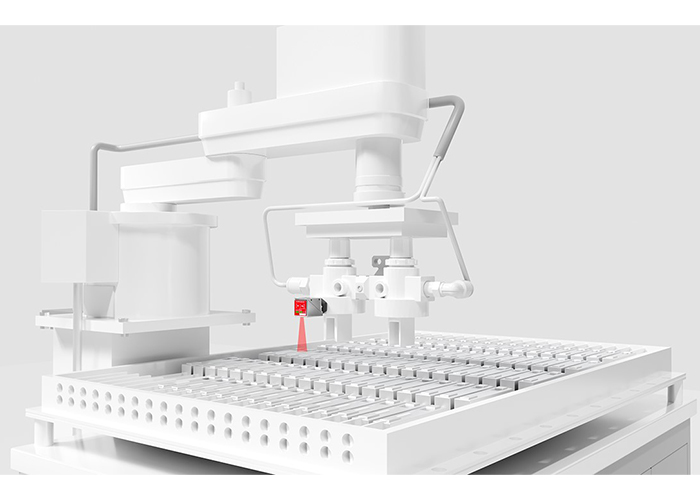
요구 사항:
배터리 셀은 보관하기 전에 코팅이 필요합니다. 관련 정보는 코드화되어 배터리 셀에 표기되어 있습니다. 코팅 기계에 픽업되기 전에, 전체 프로세스 체인의 추적 가능성을 보장하도록 해당 데이터가 감지되어야 합니다.
솔루션:
스캔 속도가 빠른 2D 코드 리더 DCR 200i를 사용하면 빠르게 움직이는 물체의 코드를 판독할 수 있습니다. 판독 범위를 조정할 수 있도록 다양한 광학 모델을 사용할 수 있습니다. 다양한 인터페이스를 사용하여 장치를 필드버스에 쉽게 통합하고 간단한 구성 도구로 빠르게 설치할 수 있습니다.