L’officina presse
Dalla bobina di acciaio all’auto.
Da giganti bobine di acciaio vengono realizzati, grazie a diversi passaggi di lavorazione, i pezzi che compongono le carrozzerie dei futuri veicoli.
Che si tratti del taglio delle bobine o della punzonatura, della stampa e della formatura delle lamiere: i sensori accompagnano e proteggono tutte le fasi della produzione, anche in condizioni ambientali critiche.
Le applicazioni sono molteplici tanto quanto la nostra gamma di prodotti creata su misura per loro. Sensori induttivi e ottici verificano e controllano la presenza e la posizione dei pezzi. I sistemi di identificazione registrano i dati per la loro tracciabilità. In impianti di taglio, i nostri sensori comunicano i valori di misura per il sistema di regolazione della curvatura e dei bordi.
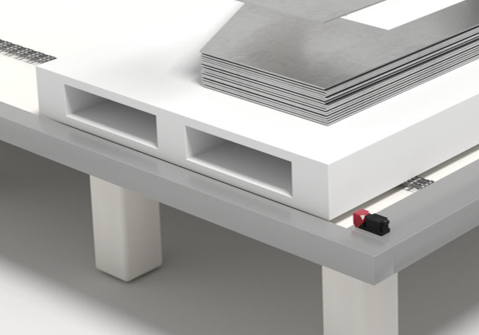
Richiesta:
Le lamiere tranciate (e in parte già punzonate) vengono trasportate alle ulteriori lavorazioni mediante carrelli elevatori o sistemi di trasporto a guida automatica. Prima di prelevare i pezzi occorre verificare che il pallet o il portacarichi abbia raggiunto la posizione di trasferimento. Questo deve avvenire senza contatto.
Soluzione:
I sensori induttivi della serie IS 200 / 244 offrono elevate prestazioni e una grande riserva di funzionamento. A seconda del luogo di installazione e delle portate di tasteggio necessarie, è possibile scegliere tra le forme cilindriche con distanza di commutazione tripla della serie IS 200 e le forme cubiche IS / ISS 244.